Introduction: Palletwood Beer Carrier
This instructable is intended to help you make a hip, attractive six-pack carrier out of wood from an old pallet. Carriers like this are rather common, this one stands out due to its integrated bottle opener and tidy cap catcher. I also include instructions for internal dividers to reduce rattling.
Pallets are generally free and an excellent source of wood but often full of nails. This project can be built with the short length of board that result from sawing along next to the upright members holding them together, thus solving the problems caused by nails or screws left in the wood breaking your tools. Use a hand-held circular saw for this. Once you have a pile of boards, double check them for nails, staples, screws, etc.(Tools are expensive)
Step 1: Materials
You will need-
Six boards (these will vary, but these particular ones are from a heavy duty pallet, so they are 5.5 inches wide, 3/8 inch thick and about 16 inches long) Pallet wood is very rough and often dirty and/or stained, if you want a smooth finish on your carrier now is the time to plane or sand the boards. Also choose boards that are not split or too severely warped.
About a foot of 1 inch dowel
some brads or finishing nails and 2 short (1 inch)drywall screws
The internal dividers are made from 1x1/4 inch furring strips or similar scrap.
To make the integral bottle opener you will need 2 heavy washers, a 1.25 and a 1.5 inch.
Those of you out in metric land will have to do your own math.
Step 2: Tools
The main tools used are saws and a drill. While any power drill will do it is probably best to have a drill press as well as a hand drill. The hand drill can make pilot holes quickly at any angle, but the drill press is better for making the one inch hole and/or pockets for the handle. The best tool for this is called a Forstner bit. It makes a clean flat bottom hole with very little work. If you don't have access to one you can use a Spade or twist drill or even a hole saw but all of these make holes with messier bottoms that require more fiddling.
For saws I used a full set, a Table saw for straight cuts, a chopsaw for angle cuts, a band saw for non-through cuts, and a Japanese style pullsaw with a miter box for miscellaneous cuts.
You will also need a ruler, a marking square, a pencil or pen, a pair of foot long bar clamps, a quarter-inch chisel for the separator notches and a way to drive nails, a hammer works fine, but a pneumatic brad driver turns an hour long job into a 2 minute one.
Step 3: Getting Started
The plans provide a good overview of the build, the critical dimensions are in the drawing (5x8.5 inches internally, center of dowel hole is 1.75 inches from top of boards). Most of the other dimensions will be varied to suit your wood thickness or personal taste. The dots in the drawing represent nail heads. Not shown is the left end piece which has three nails going into the bottom board as shown on the drawing of the right end. The far right drawing shows inside of a side board with the spacing for the separator notches.
The first thing I did was to cut all the ends off square using the table saw and miter gauge. This prevents me from messing up later by measuring from crooked ends. Also I used the rip fence to rip all the boards to 5 inches as the 3 critical boards are 5 inches wide and the side boards can be any height. Select the three best boards to be the ends and bottom.
Step 4: Cut the Bottom and Ends
Be careful to cut these absolutely square. In this case the bottom is 11 inches long (8.5+2.5), The left end is 13 inches and the right is 12 and 5/8's. This is because the right board sits on the bottom board, but the left goes all the way to the floor. If you are not including the cap catcher make both end boards the same length. The bottom board will also be shorter.
Find the center of the top edge of the end board and mark it, then mark 1 and 1/8th on either side. I used a miter/chop saw so I just set the blade to 15 degrees and carried on. Note, in the picture, the bottom board is clamped to the table of the chopsaw. When I lined up my first cut I clamped the bottom board snug against it. Since the boards are all the same width and the part is symmetrical all I have to do is shove the end board into place, cut, flip it, cut and done. If you don't have a chopsaw you will need to get out your protractor and draw a line 15 degrees from perpendicular to the end starting at the marks 1 and 1/8th off center and going until it reaches the side, then the cut along that line. Watch your fingers.
This is a good time to test fit your pieces and make sure your math is right. Also this is when I label the pieces with things like "top of bottom" and "inside of left end" or "top of right end". These act as assembly instructions and guides to make sure you cut things on the right end.
Step 5: Drill Holes
Clamp the end boards together. Be sure the insides are together and the TOPS and sides match up perfectly. Measure 1.75 inches straight down from the center and mark. Drill a pilot hole slightly smaller than the shaft of your drywall screw through both boards. Now separate the boards and use the pilot hole to center the bit for the 1 inch hole in the right end board. When that is drilled through prepare to drill the pocket in the left board. Be sure you are drilling into the inside face of the board and line up carefully with the pilot hole. Carefully advance the bit until you are halfway through the board. If your drill press does not have a gauge stop frequently to measure. If necessary clean out the bottom of the hole so the dowel can seat well. It helps assembly if you sand inside the hole in the right end so that it is fractionally larger than the dowel. A sharp Forstner bit will leave a hole EXACTLY the size of the dowel and it will be nearly impossible to push it through. The fit should be tight but not require brute force.
If you are not including the opener in your carrier just drill two pockets rather than a pocket and a through hole.
Step 6: Cut the Sides
First cut to length, (in this case 11 and 3/8's) then test fit, if correct then mark a rectangle 3 by 2 inches in the top right hand corner and cut it out. With a bandsaw you can mark one piece, stack the sides and make one pair of cuts. Just make sure you have the pieces facing properly before you cut. Test fit everything one last time. If you have done a good job it should just stand there.
Step 7: Clamp and Nail
Assemble your carrier and clamp lightly as shown, then use your square and your fingertips to make sure everything is flush and straight. Now tighten down the clamps firmly and start nailing. If you are using a hammer check frequently for slippage.
Step 8: Final Assembly
Measure and cut the end piece for the cap catcher (in this case 2x6.25 inches), nail into place. Measure and cut the dowel so that it projects 1/2 inch past the outside face of the right hand end board. Push the dowel through the right end hole and into the left end pocket. Trim to fit if needed. Run a drywall screw through the left end pilot hole and into the dowel rod. Drill a pilot hole into the center of the dowel on the right end.
Step 9: The Opener
Stack the washers as shown and attach the to the dowel with a drywall screw driven into the pilot hole as shown. The washers should be centered. You may want to drive a nail into the top of the right end board and into the dowel, but if the dowel is properly fit it shouldn't be necessary.
Step 10: Separators and Finishing
If you want you can measure the placement of the separator notches when you are cutting the side boards and dado them in on the table saw. I prefer to assemble the whole carrier, measure for the notches and then cut the edges with the pullsaw and clean them out with a 1/4 inch chisel. The actual separators are just thin scrap or furring strips cut to length. They are not glued or nailed.
I like the rustic look of pallet wood, but if you have access to a laser engraver you could obviously customize the side boards before nailing them in place. Paint and varnish are also possibilities if you prepare the wood before assembly. I am working on a version for larger bottles with a 7.5 x10.5 inch internal area, but I'm not sure that pallet wood is large enough. Have Fun!
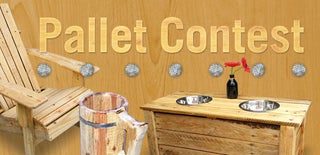
Participated in the
Pallet Contest