Introduction: Portable Bicycle Repair Station
In this instructable, I will show you how to build an awesome portable bike repair station. Imagine having an entire bike shop on the rear rack of your bicycle! You can take this portable repair station to festivals, on bike paths or wherever your bike will go, using it for business or hobby purposes. I got this idea from a mechanic who lugs around a trailer full of bike tools. I think this design is an easier and more functional alternative to bringing tools in a toolbox and then having to find a work surface. This is my first wood working project so please give me feedback :)
I would like to thank the membership of The Recyclery (http://wptest.therecyclery.org/) and Pumping Station One (http://pumpingstationone.org/). The Recyclery is my favorite not-for-profit in Chicago because it does bicycle education and community outreach through the power of bicycles. Thanks Jesse for your input on tools and Tomaz for loaning me tools. Pumping Station One is an amazing resource for makers and hackers who want to build anything. I had to learn many new skills to build this project. I want to thank JP for his design consultation, Greg for his help with drafting, Josh for his help with parts, Jason for his help with the second iteration of the tool wall and everyone else who contributed. Building stuff is always a learning experience and these amazing people helped me understand and realize my vision for this project.
I hope you enjoy this instructable :D Please vote for me if you like my Instructable.
Step 1: Tools and Materials
Tools:
*Important* Use safety goggles, noise dampeners and other proper safety equipment; some of these tools can be very dangerous.
- A planer and jointer - used on all the wood.
- A table top drill press - used for small wood work holes.
- Larger freestanding drill press - used for countersinking and metal holes.
- Multiple bit sizes - for holes, bit size based on the size of my bolts (see below).
- Spade bit - countersinks, size based on my washer size.
- Safety stop table saw - to cut down the wood to size, also use a chop saw. All wood pieces were checked for metal with a metal detector to avoid damage the tools or myself.
- An angle grinder - for quick small cuts.
- Metal chop saw- was used to resize aluminum extrusion channel stock.
- A belt sander and grinder wheel - were used to get rid of sharp edges and to create grooves in some pieces (for hinges).
- Various small hand tools- like flat and screw drivers.
- A square and pencil- used quite a bit.
The most important tool is your mind. Use it when design decisions need to be made. If you are in doubt, think it out.
Materials:
I mostly used scavenged materials (approximately 70% of project. Available materials determined a lot of design choices.
- 15/16ths bolts throughout - since I had an abundance of them. I used two sizes of washers and the corresponding nuts for these.
- Single size U clamp- used throughout (pictured).
- All wood was found wood - these look nice because of planing and jointing.
- Hinges and L brackets - were bought at Ace and a small local hardware store (pictured).
- Peg board - was found.
- Aluminum channel stock - was found (80/20 is supposedly a popular brand though).
- Small metric bolts and nuts - were gifted (see pictured).
*Important* I used a heavy duty weight rated old man of the mountain rear bicycle rack. I don't think my project is that heavy but do consider if your rack can handle this sort of project. Most racks have a weight rating. Check yours before proceeding.
Step 2: Drafting and Secure Mounting Points
While I can provide the measurements and design choices specific to my bike I think a general discussion of the design will be more useful in reproducing this project. My bike is highly customized and its geometry is unconventional (I don't know any other long wheel base recumbent riders). That said, this project will work similarly on a standard frame geometry that accommodates a rear rack.
I started by measuring my rear rack size then set my length limit as no more than 1.5 rack lengths. I did the same for width. This limit was based off past experiences carrying oversized loads on my rack. I taped up a chair to model the dimensions. I created a scrap-wood board alpha version to test placement of the holes and figure out alignment. I drafted with Greg from the PS1 sub group Biking Station One a template for mounting the U clamps to the straight cross points so they would ideally distribute load in a level way while being completely secured (see U clamp on rack at cross points and template pictures). A template is a nice intermediate step if you are not confident about the alignment.
I based the 3 layer design off of a swinging arm design (middle layer was to house swinging arms) pictured in paper cut outs from a discussion I had with JP from the PS1 sub group Bridgeport Social. In theory you could do a two or even one layer design but 3 layers gives you more flexibility in my mind to layer and secure parts together.
Measuring throughout was critical for mounting the clamps to the baseboard and rack. Make sure to mark and drill all of the hole locations precisely. This mounting is essential to a safe project. You do not want your project falling or coming loose in traffic. Shake the bike and take it for a test ride once you have mounted the base board. You should not be able to hear any rattling or tell that it is there if it is properly secured.
Step 3: Wood Working
My philosophy on wood working is still nascent. That said, always measure twice. Find center line and cross point. Use a straight edge, a square and a level if you can. The time spent measuring and marking will easily save you from the much greater and more frustrating time you will have to spend correcting poor drafting and alignment mistakes.
1. Mark (pencil so you can erase) with a straight edge. I like to give space away from the edges of a piece or where a knot in the wood lies. I also off set (zig-zag stagger) my holes that are immediately adjacent so I avoid splitting the wood along a grain line.
2.Cut down (saw stop, chop saw, band saw, scroll saw, or alternatively hand blade). Since I am using salvaged wood this means cutting off splits in the wood while trying to retain as much area as possible.
3. Square. Use a Jointer to create straight edges. This makes it easier to cut pieces down further and allows pieces to site flush next to each other. Use a Planer to create flat level surfaces. Be careful not to remove too much wood at one time so the machine does not jam. If you are matching multiple pieces to create a large surface plane that is level, use calipers to make sure the pieces are the same height when mounted.
4. Create Mountings. Drill press holes. Measure the center line and the cross point. Do this twice. Drill pressing holes close together when you are off by a little bit is no fun!!!! Securely clamp the piece and make sure your bit is properly mounted and centered (don't drill press the drill press table ;) . Locking down with a clamp or other securing device prevents the piece from either spinning out when the press punches through the bottom of the piece or wandering off alignment when it is starting the hole.
5. Counter Sink. Sunk bolts both look better and allow for a level plane without protruding washers and bolt heads. Doing this also gives you access to extra threading on the bolt in case you need it. I measured bolt head and washer with electronic calipers then used the throw indicator on the drill press to determine depth of my spade bit (spade bit size was chosen to match washer size. If you want, you can use bicycle handlebar end-caps to cover sunk holes and create a fun look.
Step 4: Hinges, Spacer Planks, and Work Surface
I have never worked with hinges so I decided beefy was the best. My hinges would probably comfortably accommodate a hundred pound door.
Earlier in the process, I mocked-up the design on my taped-up chair by laying out how I imagined the pieces would sit, using hinges on opposite sides. At this point, I simplified my design from hinges on opposite sides to two parallel hinges. I measured and marked the cross points and drill press each hinge. I ground two grooves into the rear hinge to allow the U clamp arms to lie snuggly adjacent to the hinge. The hinges act as load spreader plates for the U clamps. Drill pressing metal is an iterative process where you move through 2 or 3 (or more) bits starting small and working towards your desired size. This process also allows you to check the alignment of the first iteration before the hole is very large. Make sure to use cutting fluid! This will ease the strain on your bit. Also secure your piece and strongly secure your bit. Any wobble here will be bad for your project and your tools and may pose a risk to you. Drill pressing metal poses more risk than wood. It is a more difficult material to pass through and the kick when a job goes wrong is significantly worse. Be careful! Wear eye and hearing protection and a work bib. Ask for help or look online if you are unsure about how to properly use the drill press. You can with relative ease create a negative situation. That said with a little knowledge this step is a piece of cake, especially if your markings are spot on.
I created the spacer plank to support the top surface using the same techniques mentioned in the wood working section. I leave all pieces long unless shorting is necessary so I have some fudge factor if something needs to be modified. I used dado cuts (http://en.wikipedia.org/wiki/Dado_(joinery)) to allow the spacer plank to lay level over the hinges and L brackets. I sunk nuts in the spacer board to pull up the bolt for the top plane surface. I also used needle nose pliers to get the threading to catch on very tight bolts (see picture). I then tested to make sure the alignment of the hinged work surface and the rack surface were flush. I did some minor sanding to make the flush perfect. Flat surfaces pose some interesting challenges. If you pay attention to the details, the surfaces will align without any problems :D
Step 5: L Brackets
I struggled with the L brackets. I was nervous about not having a direct mount to the rack like the hinges do from the U bolt pass through. This is why on the bottom side I used over sized washers to increase the surface area of the load distribution. The L brackets also posed the most challenges in terms of getting the alignment right for each bracket to be perfectly in parallel with the other (slides require high precision alignment). If you get very close to the alignment you want there is sometimes flex in the L bracket. Use this method as a last resort as it can weaken/fatigue the metal.
Step 6: Tool Wall Version 0
The tool wall idea was definitely a case of my eyes being bigger than my stomach. I wasted a lot of time on my initial design that did not foresee the fundamental flaws of my material choices. Do not use standard drawer slides!!!! They are not robust enough. They do not tolerate lateral forces. They don't work. I could elaborate further. Just take my word for this, and don't use drawer slides.
All of that said, I learned a lot building the initial tool wall. I used the bottom of my pedal stroke and the bottom of my rear derailleur as a guideline for how low hanging my lowest hanging piece could be. I had some issues mounting my seat with long upper wooden guide rails so for me there was a top limit as well. The prototype pictured in this step was very heavy and suffered a lot of lateral forces. It unevenly loaded the bike and made riding difficult.
Step 7: Tool Wall Version 1
I modeled my tool wall on a Recyclery workstation. I used some superstrut and zip ties to model the glide action. With a better understanding of how I wanted the tool wall slide to function I took the aluminum extruded channel stock and cut it to length. I dado cut channels for each piece to sit in. All of these lengths were based on the model 0. I drill pressed the bolt holes that interfaced with the L brackets keeping in mind the up position of the board and the riding board position. I then drilled the series of holes for the connection between the aluminum stock and the wood channel housing. Once these were bound together with the small screws they were then bolted to the L bracket. At the resting position at the bottom of the channel, I mounted a small stop on each channel to support the resting position. This is not needed if you are willing to tighten the sliding bolts' nuts when you want to use or put away.
Step 8: Support Leg
I constructed two versions of the support leg. This is the first and much less complicated design. I took a old outdoor rake handle measure and cut it to length. I then used a belt sander to do a graduated round at the top end. I then raised the drill press and drilled the top using a bit one size smaller than my bolt. Since wood is soft you can sometimes use a bolt to tap your threading. I tapped threading into the leg using this method. I then used a series of spade bits sunk to progressively deeper depths until I passed through the other side of the table surface from bottom up. I used a rotating barrel sander to even out the layer depths. I then added an over-sized washer and threaded the bolt through the hole and into the leg. This style of leg has some play for different angles of ground while also providing robust support for your table top.
Step 9: Extras
This is my first major woodworking project so there were alot of things I was hoping to add that did not make it into this iteration. Perhaps you will add these in your build:
- A counter sunk magnet bowl - in the fold-up table surface
- A clamp - on the rear end. Very useful.
- A home-built bicycle stand- I have a bike stand bungeed to the rear rack, but I want to build a custom stand.
- Portable chair- I wanted to fabricate a fold-up chair using used bicycle inner tubes and used rims.
- A pump mounting - on the underside of the fold up.
- Truing stand- There are some fun instructables on making your own.
- Roof awning- For rainy days
- Sign - To show off your shop name.
- Engraved - I wish I had time to cnc or laser etch the table surface.
Fun Reach Projects:
- A welder- add on tool mount to build bikes on the go.
- Lean to/shelter - For the touring mechanic. It could convert to this structure using a canvas shell
- Electricity heating,a fan, and lighting - would require a battery or a powerful dynamo. To accommodate all weather conditions.
- Hammock- would require improved kickstand design
Step 10: Conclusion
I took the portable repair station to a Recyclery bike drive event. I do not have a picture of the portable station at the event but these are the bicycles we collected. At the event, I received a very positive response to my portable workstation, and it was very useful to have there.
Doing this project taught me a lot about woodworking, prototyping, the effects of small mistakes in margins, and accounting for design errors. I hope to fix many bikes with this project and use it to help my community and my fellow cyclists. Happy riding!
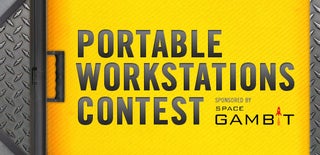
Participated in the
Portable Workstations Contest
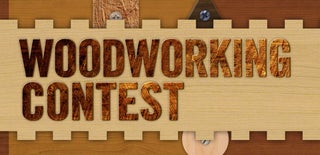
Participated in the
Woodworking Contest
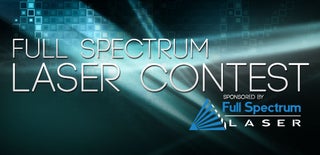
Participated in the
Full Spectrum Laser Contest