Introduction: Powder Coat Your Hand Tools
Powder coating is cool.
It's a tough finish that is stronger than paint and looks great. It's a "Green" process since there are no solvents to spray, and the over spray can be swept or vacuumed up.
I thought it would be cool to powder coat my trusty old wrenches for personalization and good looks.
They were getting dirty and the finish was starting to show signs of wear, so I brought them with me to the Tech Shop to get the treatment.
Now is a good time to preheat the oven and think about where to hang your tools in oven before it gets hot.
My powder needed to be baked at 375 degrees.
Step 1: Clean Your Tool
First step is to clean your tool.
Wipe off any grease or other grimy residues and then put them in the sand blaster to prep the surface.
Use the sand blaster to roughen up the surface, clean the metal and give the powders a good surface to adhere to.
Warning - the sand will get inside the mechanism and will need to be worked out afterwards. I just wiggled the parts back and forth for a few minutes and the sand started to work it's way out.
A quick spray with de-greaser or TSP and a final water rinse will be sure the powders adhere everywhere.
Dry thoroughly with compressed air.
Step 2: Powder Your Tool
Once your tool is cleaned up and blasted, you will want to make a hanger to support it in the spray booth and in the oven. A simple wire with a hook on each ends works great.
You connect your powder coating gun's ground lead to the wire hanger, set your pressure according to the manufacturers recommendation, and apply the powder. The gun I used was set at about 7-10 psi.
The process works with static cling - just like rubbing a balloon in your hair and sticking it to a wall. In this case, your piece is charged up negatively and the powder wants to stick to it after it shoots past the charged electrode in the spray gun.
Step 3: Bake Your Tool
Once the powder is on and it looks even, it's time to bake!
Make sure the oven is set to appropriate temperature and quickly hang your tools so the heat doesn't all escape.
BE CAREFUL not to bump the powder!
Set your timer according to powder type - mine was for 15 minutes at 375 degrees Fahrenheit.
Step 4: Remove, Cool, & Enjoy Your Tool
Ding!
your timer is done, so be sure to wear your gloves and carefully remove your tools from the oven. The coating is still soft now so don't bump it - you will be sorry.
It's still HOT, so be smart now and don't touch it!
Hang the tools somewhere to cool slowly.
Be Patient, metal holds heat longer than fresh baked cookies.
Sit back and enjoy your pretty new tools.
Remember, don't try this at home! Do not bake powders in an oven used for food.
I did it at Tech Shop!
http://www.techshop.ws
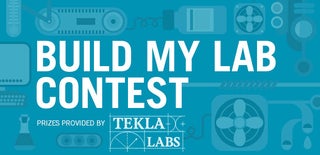
Participated in the
Build My Lab Contest