Introduction: Practical, Prototyping, and Plastic
[ Warning: Obligatory Backstory ]
I remember, as if it were yesterday, walking past our local hardware store on my way home; Ace Hardware right next to Green's Grocery. Ah, yes... that store had everything from tools to toys!
Gasp! ... look there in the window - do you see it?
Step 1: Measure Your Treasures
Artfully displayed in the store-front window ... a giant plastic robot called Mazinger Z. Deals were made, money was saved, and the glorious treasure was mine!
(photo: Dynamic Collection, 2013)
Step 2: Modelling Madness
Now that I'm all grown-up... scratch that.
Now that I'm... Uh. Anyway!
I've decided to make a animatronic Mazinger Z torso - and it's taking considerably longer than the original 1970's $14 purchase. Much longer.
So... I've turned to 3D printing to accelerate things - and I've discovered some wonderful stuff along the way that I would like to share with you.
First tidbit, is the translation gap between 3D printed plastic parts and just about everything else. Can you 3D print a ball caster?
Yes... yes you can.
Step 3: Datasheets Are Your Friend
You know that feeling you get when you stumble onto a website that has exactly what you need to finish your semi-sentient bioloid?
Before you raid your piggy-bank... use datasheets and technical drawings to create facsimiles of the parts in your shopping cart. Large and small, make them all!
"Measure seven times, 3D-print as much as necessary, and buy your final supplies once." - Me
Step 4: Standardize... Everything!
McMaster-Carr has thousands of fasteners, bearings, nuts, bolts, and wibble-wobbles. Gaps in their smaller fastener offerings can easily be filled by Micro Fasteners.
Is there a particular thread / size that can get you through 80% or more of your project? And, while you're at-it, pick a 'system' (metric or standard) and stick with it as much as possible.
Unless you have unlimited time and finances that is... in that case, go nuts!
(photos: M3 tapered tap and self-tapping screws)
Step 5: Proofing Is Priceless
Cold steel... is what my final robo-product will be made of; mid-grade aluminium to keep costs reasonable. Else, things could get crazy expensive crazy fast.
"Here's one quirky tip to shed additional pounds off your project budget!"
Companies are starting to release mechanical models of their products - that can be used in modelling software or even printed for use in lite-duty proofs / prototypes.
I used the guts provided by Servo City to make Mazinger Z's shoulder joint... take a look!
Step 6: Have Fun and Get Things Done!
Warming the plastic a bit and dry-threading a screw into place can help form threads in delicate parts when a tap is too aggressive (e.g. removing too much material). If you need a little more grip, consider using threaded inserts; recycling them back into your parts bin when the printed part has served its purpose.
Bearings can be printed solid - just leave enough clearance for interlocking or rotating parts (sand as needed).
Bamboo skewers, toothpicks, dowels, and screws can be used as a substitute for rods and shafts - checking alignment is important!.
Firm but gentle is the rule with fasteners... material strength, layer adhesion, and print resolution can all lead to RUD (Rapid Unscheduled Disassembly) when using the Force.
Delicate parts are... well... delicate! Paint them with a thin coat of epoxy resin to toughen them up a bit.
What are you waiting for? It's time to make, make, make!
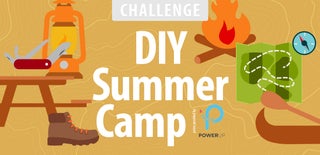
Participated in the
DIY Summer Camp Challenge
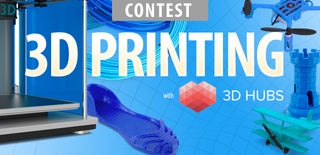
Participated in the
3D Printing Contest 2016