Introduction: R/C LEGO® Car Redux
After I built R/C Lego Car, that used hacked motors and motor housings from the toy Car and toy R/C cars. I realized most of the parts from that toy R/C car that I took the motor out of became wasted.
This way was not very practical or not so "green" at all.
So I decided to design a 3D printed motor housing (See details in Step1) that is generic to all of my Lego car designs (details in Step 1).
This instructable, R/C Lego Car Redux, shows you how to use the 3D printed motor housing with my very first built R/C Lego Car.
Most of the parts from my original R/C Lego Car were still in used in this version. There were also some new Lego parts added, but only a few.
Eventhough this instructable is a "Redux" of the R/C Lego Car, I am going to show you how to build this car step by step from scratch, just like we tear the model apart and rebuild it again.
One good thing, neither the programming the Arduino, nor the UI to control the car in Processing needed to be changed.
Note: See more photos of "Redux" version of R/C Lego Car and video in Step 12.
Enjoy!
Disclaimer:
LEGO®, TECHNIC, are property of The LEGO Group of Companies (http://www.lego.com), which does not sponsor, own, authorize or endorse this creation.
Step 1: 3D Printed Motor Housing
Why 3D Printed Motor Housing?
I was not very happy and was tired of using hacked motor and motor housing from toy car or toy R/C car, because each time I want to build a different design Lego Cars. Most of the time the new design Lego car that I plan to make was not able to use the previous hacked motor and motor housing.
Now that I created my own 3D printed motor housing. My motor housing for custom LEGO® car can be used over and over, and I do not have to buy toy R/C car to hack for motor housing from it and mod it to fit with my new design Lego car anymore.
This 3D motor housing was designed to have studs (4x6 studs) that compatibles with LEGO® modular system.
printed motor housing fits most of DC gear motors (130-Size), standard toy DC motors, with the approximate size of 15x20x25mm (height x width x length) with 2mm shaft diameter.
Photo 1 Screen grabbed from the 123D Design of the finished 3D model of motor housing.
Photo 2, 3 The 3D printed motor housing used in this project was first created in 123D Beta 9, and then migrated to 123D Design, both have the similar functionalities. The 3D printed motor housing was first printed from The Free 3D Printing offer from instructables.com (now closed).
Photo 4, 5, 6 Show the installation of the motor housing on my Wireless Lego Race Car.
Here are the steps I made to create 3D printable motor housing in 123D Design,
Photo 7 Before I migrated from 123D Beta 9 to 123D Design I tried out the 123D Design app. by created 130-Size motor in the 123D Design first.
Photo 8 Then I created 1x4 LEGO Brick.
Photo 9 And then added Primitives, and used Combine tools to form the housing.
Photo 10 And 3D Printing ready model.
Photo 11 I hided the motor model and ready to send to fabricator.
Attached is the STL file, you also can view the model and download the file from Shapeways here.
Attachments
Step 2: Parts & Tools
Lego Bricks
Following is the list of Lego parts that I used for building this car.
Most of the parts are from my previous built R/C Lego Car. Some addition parts were from ebay.
If you want to do this R/C Lego Car with the different color, please feel free to do so.
Note: The number in the bracket is the Lego's Design ID.
2 no. - 1x12 Technic brick (#3895)
6 nos. - 1x8 Technic Brick (#3702)
7 nos. - 1x6 Technic Brick (#3894)
15 nos. - 1x4 Technic Brick (#3701)
10 nos. - 1x2 Technic Brick (#32000)
4 nos. - 1x2 Technic Brick with hole (#3700)
1 no. - 1x2 Brick with Horizontal Snap (#2458)
4 nos. - 2x8 Technic Plates (#3738)
1 no. - 2x6 Technic Plate (#32001)
4 nos. - 2x4 Technic Plate (#3709)
2 nos. - 2x3 Standard Plate (#3021)
2 nos. - 2x2 Standard Plate (#3022)
3 nos. - 1x8 Plate (#3460)
2 nos. - 1x6 Plate (#3666)
11 nos. - 1x4 Plate (#3710)
5 nos. - 1x2 Plate (#3023)
1 no. - 1x4 Flat Tile (#2431)
1 no. - Bush for Cross Axle (#6590)
2 nos. - Bush 1/2 Toothed Type II (#4265b)
1 no. - Bush for Cross Axle (#6590)
1 no. - 1/2 Bush (#32123)
3 nos. - Connector Peg/Cross Axle (#6562)
14 nos. - Connector Peg (#3673)
8 nos. - Connector Peg With Friction (#2780)
4 nos. - Connector Peg 3M (#32556)
1 no. - Cross Axle 12M (#3708)
1 no. - Cross Axle 6M (#3706)
1 no. - Cross Axle 3M (#4519)
2 nos. - Axle Joiner Perpendicular (#6536)
Steering Kit
1 no. - 1x 8 Steering Rack Bracket Plate (#4262)
1 no. - Steering Gear Holder (#2790)
1 no. - Steering Rack Top (#2792)
1 no. - Steering Rack (#2791)
2 nos. - Steering Arm Drop Link (#4261)
3 no. - 8-Tooth Gear (#3647)
24-Tooth Crown Gear Type III (#3650)
Servo horn glued to Axle 3L with Stud (#6587)
Wheels and Rims
Front
2 no. - Tire size 30.4 x 14 VR (#6578)
2 no. - Wheel size 30.4 x 14 VR (#2994)
Rear
2 no. - Tire size 43.2 x 22 ZR (#44309)
2 no. - Reinforced Rim with no pin holes 30.4mm D x 20 mm (#56145)
2 nos. - Lift Arm Triangles Thin (#2905)
2 nos. - 1x2x2 Corner Plate (#2420)
1 no. - Panel Fairing #5 (#32527) Red
1 no. - Panel Fairing #6 (#32528) Red
1 no. - Panel Fairing #7 (#32534) Red
1 no. - Panel Fairing #8 (#32535) Red
Servo
9g Micro Servo (T Pro SG90)
Motor
4.5V - 9V, 130-Size Motor
3D Printed Motor Housing
2mm Shaft Adapter for Lego Wheels (Pololu part #1001)
(or Modified Connector Peg/Cross Axle (#6562) to fit the shaft of DC toy motor.)
Arduino and Motors Driver
Arduino or Arduino compatible (I used DIY Arduino in this project.)
L293D (or SN754410) motors driver IC
XBee module
Xbee breakout board (I used XB-Buddy Basic Kit, Jameco's Part no. 2163680)
PCB (approximately 2"x3")
Hook up Wire
Tools
Sugru
X-ACTO Knife
Sand paper
Files
Step 3: Steering System & Front Bumper
Following are the photos show how to assemble parts:
Photo 1 One 2x4 Technic Plate (#3709)
Photo 2,3 Two 1x8 Technic Bricks (#3702)
Photo 4,5 One 1x4 Flat Tile (#2431)
Photo 6,7 Steering Gear Holder (#2790) and Steering Rack Top (#2792)
Photo 8 Steering Rack (#2791)
Photo 9,10 Two Connector Peg/Cross Axles (#6562) and Two Steering Arm Drop Link (#4261)
Photo 12 8-Tooth Gear (#3647)
Photo 13 Servo horn glued to Axle 3L with Stud (#6587).
(See details of how to make the servo axle in Step 4 of R/C Lego Car )
Photo 14,15 One 1/2 Bush (#32123)
Photo 16,17,18 Connector Peg/Cross Axle (#6562) and Two Tire (Balloon) size 30.4 x 14 VR with rims (#2994)
Photo 19,20,21 One 1x 8 Steering Rack Bracket Plate (#4262) and 1x2 Brick with Horizontal Snap (#2458)
Photo 22,23 One 1x6 Technic Brick (#3894) and Two 1x2 Plates (#3023)
Photo 24,25 Two 1x2 Plates (#3023)
Photo 26 One 1x4 Technic Brick (#3701)
Photo 27,28 1x2 Plate (#3023)
Photo 29 Two 3M Connector Peg (#32556)
Photo 30,31,32 Cross Axle 6M (#3706) and Two Axle Joiner Perpendicular (#6536)
Step 4: Car Front Frame
Following are the photos show how to assemble parts:
Photo 1 One 1x12 Technic brick (#3895)
Photo 2,3 Connector Peg 3M (#32556), one grey, one black
Photo 4,5,6 One 1x6 Technic Brick (#3894) and Two Connector Peg with Friction (#3673)
Photo 7,8,9 Repeat of photos 1 to 6
Photo 10 Add parts to Steering System from Step 3
Photo 11 One 2x4 Technic Plate (#3709) and 2x8 Technic Plate (#3738)
Turn the finished part upside down. Attach both parts to the Steering system as shown.
Photo 12 Two 1x4 Technic Brick (#3701)
Photo 13 Two 1x2 Technic Bricks (#32000)
Photo 14,15 Two 1x2 Technic Bricks (#32000)
Photo 16,17,18 Modified Technic plate for Servo support.
For servo support pieces, see how to make them in Step 4 of R/C Lego Car:
Photo 19 Now, we have the front frame done.
Step 5: Battery Compartment
This step we're continuing on to build the battery compartment.
Following are the photos show how to assemble parts:
Photo 1,2,3 Two 1x8 Technic Bricks (#3702) and Two Connector Peg with Friction (#3673)
Photo 4,5 Three 2x8 Technic Plates (#3738)
Photo 6 Two 2x3 Standard Plates (#3021)
Photo 7,8,9 Four Connector Pegs with Friction (#3673) and Two Lift Arm Triangles Thin (#2905)
Photo 10,11,12 Two 1x4 Plate (#3710) and two 1x4 Technic Brick (#3701)
Photo 13,14 Two 1x2x2 Corner Plate (#2420)
Photo 15,16,17 Two 1X2 Technic Brick with 2 holes Ø4,87 (#32000)
Step 6: Motor Housing
Following are the photos show how to assemble parts:
Photo 1 2mm Shaft Adapter for Lego Wheels
Photo 2 Install shaft adapter (Pololu #1001) or Modified Connector Peg/Cross Axle (#6562) to motor.
Photo 3.4 Insert the motor with shaft adapter to the 3D printed motor housing.
Photo 5,6 Fit the 8-Tooth Gear (#3647) to the shaft adapter.
Photo 7 Continue on from last step (Step 5)
Photo 8, 9 Install 2x6 Technic Plate (#32001)
Photo 10,11 Place the motor housing (that we just finish in this step) to the car frame.
Photo 12,13 Two 1x4 Technic Bricks (#3701)
Photo 14,15 Two 1x4 Technic Bricks (#3701)
Photo 16,17,18 Two 1x4 Technic Bricks (#3701) and Four Connector Pegs with Friction (#3673)
Step 7: Gear Box
New parts:
24-Tooth Crown Gear Type III (#3650)
Cross Axle 12M (#3708)
Following are the photos show how to assemble parts:
Photo 1,2 Cross Axle 12M (#3708) and Bush for Cross Axle (#6590)
Photo 3 24-Tooth Crown Gear Type III (#3650)
Photo 4, 5, 6 Two Bush 1/2 Toothed Type II (#4265b)
Photo 7,8 Two 1x6 Technic Bricks (#3894)
Photo 9, 10 Two tires (Balloon) size 43.2 x 22 ZR with rims (#56145)
Photo 9, 10 Two 1x6 Technic Bricks (#3894), Cross Axle 3M (#4519), 8-Tooth Gear (#3647), and Bush for Cross Axle (#6590)
Photo 11,12 1x6 Plates (#3666)
Photo 13,14 Connect the Gear Box to the finished part from previous Step
Step 8: Frame Construction (Cont.)
Following are the photos show how to assemble parts:
Photo 1 Finished parts from last Step.
Photo 2, 3, 4, 5 Four 1x4 Technic Brick (#3701) and Four Connector Peg With Friction (#2780)
Photo 6, 7, 8 1x6 Plate (#3666) and Two 1x8 Technic Bricks (#3702)
Photo 9, 10 Two 1x4 Plate (#3710) and two 2x4 Technic Plate (#3709)
Photo 11, 12, 13 Four 1x4 Plate (#3710)
Photo 14, 15 Two 2x2 Standard Plates (#3022)
Photo 16, 17 Four 1x2 Technic Brick with Ø4.9 hole (#3700)
Photo 18, 19 Two 1x8 Plate (#3460)
Photo 20, 21 Two 1x4 Plate (#3710)
Photo 22, 23 Installed the DIY Arduino and Motors Driver PCB that we are already built from the previous version.
Step 9: Additional Decorative Panels
New parts:
1 no. - Panel Fairing #5 (#32527) Red
1 no. - Panel Fairing #6 (#32528) Red
1 no. - Panel Fairing #7 (#32534) Red
1 no. - Panel Fairing #8 (#32535) Red
Following are the photos show how to assemble parts:
Photo 1, 2, 3, 4 Panel Fairing #7 (#32534), Panel Fairing #8 (#32535), four Connector Peg With Friction (#2780), and Two 1X2 Technic Brick with 2 holes Ø4,87 (#32000)
Photo 5, 6, 7, 8 1x2 Technic Brick (#32000), 1x4 Plate (#3710), and 1x8 Plate (#3460)
Photo 9, 10, 11 Panel Fairing #5 (#32527), and Panel Fairing #6 (#32528)
Photo 12, 13 The Battery Compartment could accommodates 4x1.5V AA type battery with holder, or 7.5V 500mAh rechargeable LiPo battery, or 9V battery.
Step 10: Arduino, Motor Driver & Wireless Module (XBee)
This Step is similar to Step 8 of R/C Lego Car: Arduino, Motor Control and XBee. I needed to modified the PCB by added two 1x2 Lego plates(#3023) to the PCB (as shown below).
Following are the photos show how to assemble parts:
Photo 5 Remove the assembled Panel Fairings nos. 7 and 8 from both sides before installing the Arduino & Motor driver PCB.
Photo 6 Prepare two 1x2 Plate (#3023) (I picked the old or rarely used plates).
Photo 7 Put 1x2 Plates at the end of 1x8 Bricks on both side.
Photo 8 Prepare Sugru and add them on top of both 1x2 Plates.
Photo 9 Place the Arduino and motor driver PCB on top of Sugru. Wait 24 hours allow Sugru to dry.
Photo 10,11 Completed!
Step 11: Processing UI & Arduino Sketch
This Step is exactly the same as previous version of R/C Lego Car, Step 9: Processing UI & Arduino Sketch. Please follows the link for details. I also added the source codes for both Processing Sketch and Arduino Sketch here in this step.
Step 12: Conclusion
Right way to solve the problem. More "green" than hacking toy R/C Motor housing.
Lego Bricks or parts are already recyclable products. This motor housing is designed to be compatible with the Lego's parts, so it could be reused with Lego's brick as long as you want to create something new with them. And it could be passed on to the next generation just like all the Lego parts do.
What works well?
Software (3D Modeling for 3D Printing)
Free available software to use as the designing tool e.g 123D Apps, SketchUp etc.
Note: I used 123D Design to model this Motor housing, as shown in Step 1)
What doesn’t?
The motor housing can only be used with DC gear motors (130-Size), standard toy DC motors, with the approximate size of 15x20x25mm (height x width x length) only.
Could not used with the Lego car design that is larger than 10" long. Motor does not have enough power to push/pull such a car.
What next?
If the Lego compatible motor housing is the success, and is going to be in production, the material of choice is going to be use plant-based PLA plastic.
Gallery of photos of the finished R/C Lego Car.
Photo 2 R/C Lego Car before the "Redux", Photo 3 R/C Lego Car after the "Redux".
Photo 4,5,6,7 Different view angles of New R/C Lego Car.
This video demonstrated test of GUI control of the R/C Lego via XBee.
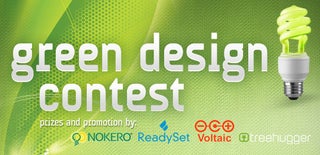
Third Prize in the
Instructables Green Design Contest
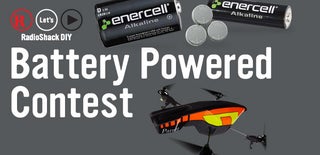
Participated in the
Battery Powered Contest
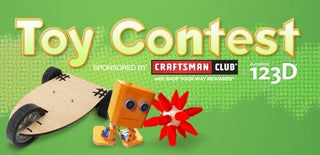
Participated in the
Toy Contest
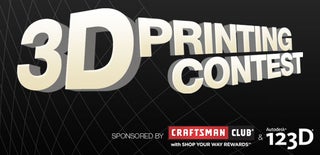
Participated in the
3D Printing Contest
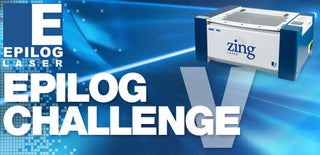
Participated in the
Epilog Challenge V