Introduction: RS-01 Ayrton Senna’s 1993 McLaren MP4/8 Formula 1 3D Printed RC Car
About the car
A tribute to Ayrton Senna, 22 years since he died May 1st, 1994.
By Brett Turnage
@3dprintRaceTech
Simplify3d
https://www.simplify3d.com/3d-printed-tribute-to-f...
3ders.com
http://www.3ders.org/articles/20160502-3d-printed-...
3dprint.com
https://3dprint.com/132295/formula-one-ayrton-senn...
This car honors arguably the greatest Formula One driver ever, three-time world champion Ayrton Senna, and his iconic 1993 McLaren MP-4/8 which he drove under both the McLaren/Marlboro red and white livery. If you have never heard of Ayrton Senna I highly recommend watching the documentary Senna (also check out the movie Amy by the same director)–it’s an amazing story of an amazing man who inspired the nation of Brazil and the world with his amazing driving. You can also watch the quick clip that Top Gear did a few years ago about Senna, which I have linked.
I have always loved this car. This is the first unique car to emerge from the RS-01 chassis family and the first to be released… Being that it’s Senna’s car, I’m sure it will be outstanding in the rain, and do unworldly pole qualifying laps. :)
This car is an evolution of the RS-01 chassis with a highly detailed body that is very accurate to the original car, updated RS-01 suspension parts, rims, and tires that can all be 3D printed. The chassis uses the running gear (carbon fiber rear shaft, differential, front uprights, motor mounts, carbon reinforced links) from a Tamiya F104-ver. 2 Pro F1 RC race car—parts that are readily available, and can use either foam tires, 3D printed tires, or rubber tires on either 3D printed rims or with the original F104 plastic rims. I loved making this car; I hope that you enjoy printing and building it just as much.
What I learned by building this car
This car was my first attempt at building a 3d printed car. I learned two CAD programs doing the build. First Blender, which is what I used to build the originally RS-01 chassis, and then Autodesk's Fusion360, which is what I build the car on. Building RC cars has quickly allowed me to master these programs, and I use the things that I have learned in my composites company. Building these cars has enriched my life, and I am now mastering CAD.
-Brett Turnage
Step 1: RS-01 3d Printed F1 Chassis Intro
Introducing the RS-01 3d printed chassis. I originally designed this chassis for the Open RC F1 Remote Control Car to turn that car into a fully tunable RC car. The Senna RS-01 chassis is the ultimate iteration, a car designed from the ground up to take advantage of this full suspension chassis.
I’ve named this chassis the RS-01. The “RS” stands for Riverside Speedway. The Riverside Speedway was a historic track, located on the border of Moreno Valley and Riverside, California, that hosted all of the greats from Carol Shelby to Mario Andretti. It even hosted many Formula 1 races. I grew up in Moreno Valley, less than a mile away hearing the sounds of engines filling the air, so I hold that track and it’s historic history as part of my heritage. As a homage to this great track I’ve named my chassis after it.
About Me: I’m a car guy who learned Computer Aided Design (CAD) 5 days ago (since I posted this March 16, 2016)… This is the first design that I’ve made. No lie!
GOALS: The RS-01 Chassis is designed to make a 3d printed competition race car. This car is a 3d printed version of competition RC cars like the Tamiya F104 Pro Ver. 2 and 3Racing FGX F1—cars that cost around $600.
It features tunable front pushrods, adjustable rear suspension with an anti roll dampener. The front suspension translates the movement through rocker arms that then compress the shocks. The rear suspension moves independently of the main body. It is basically a Live Axle with a Panhard Bar. It not only compresses, but can also move torsionally, so if one wheel hits a rock, only that wheel will move up.
Modular Design:
I designed this chassis to be modular. You can run 3d printed wheels, or actual plastic wheels from the store—just by changing the axles. Different motor mounts will also be easily swapped in by printing out a different rear chassis which has the correct holes for that particular setup. If you are focused on building the fastest remote control car that you can have, with the most powerful motor and stickiest rubber tires that you can find—cars that can run 80 mph, then this chassis will also work for you. In its race form it is designed to use Tamiya F104 rear motor mounts and rear axle. With these additions, the sky is the limit. Go to the track and show people how fast a 3d printed car can go!
Front Suspension:
I chose a pushrod double wishbone suspension over a typical Macpherson strut suspension for two reasons: (1) I wanted the shocks to fit within the Formula F1 Body, and (2) believability—a pushrod suspension is the exact type of suspension that real Formula 1 cars use, so it was fitting.
Rear Suspension:
Rear suspension needs to move not only laterally, but also torsionally for greater control. The shock is mounted inside the car and attaches to a mount on the rear chassis. The damper controls the roll of the live axle. It will prevent the rear wheels from reacting too fast, so you can adjust the rear of the car for your particular settings and environments. Lower control arms allow the hinging action ,and the upper control arms are nearby with springs attached to keep everything level. You can swap out these damper springs for further adjustment of the car. All these parts work together to create a suspension setup that allows you to adjust the stiffness of the rear suspension by adjusting the shock settings, damper springs and even how strong the damper works through use of particular thicker fluids.
Servo:
To be a real F1 RC car, you have to use rear and powerful servos. However, with the size restrictions of RC car bodies you need to use a low profile servo. The servo that I am using is a low profile servo from Hitech. Hitec RCD 31077S HS-77BB Low Profile BB ServoSpeed (4.8V/6.0V): 0.18/0.14 sec @ 60 degree Torque oz./in. (4.8V/6.0V): 61/76, Torque kg./cm. (4.8V/6.0V): 4.4/5.5 It has great specs and even better—a great price. It retails for $25, so it is the perfect servo to use in the Open F1 Rc car because it is powerful, and is designed for use in F1 projects like this. Servo mounts are included.
Battery: The battery is mounted lengthwise in the car for better weight distribution by keeping the center mass in the center of the car. The battery cage can fit any battery up to the size of the Turing nano-tech Shorty 4200mah 2S2P Hardcore Lipo Pack (96x46.4x25mm). Shocks: The RS-01 chassis uses 55mm shocks. Any shocks can work. The front shocks were modified to use longer 110mm shafts with carbon fiber tubes acting as shaft covers. The spring rate is currently 19 lbs/ft, but the great thing is that you can use any 55mm shock and spring rate that you want—it’s all tunable. Screws and taps: To keep weight low, I used metric taps to screw the bolts into the plastic. M3-1.0 screw taps, and bolts. I’m very proud of this chassis that I designed and built. I will be developing this suspension setup until it reaches all of its design goals.
This instructable comes with detailed manuals that show detailed pictures and walkthrough. Use it along with this insturctable.
Step 2: 3d Printing Tips for Success
3d printing tips for Success
The RS-01 Ayrton Senna's 1993 McLaren MP4/8 consists of over 54 3d printed parts.
Optimized for standard 3d printer build areas of 200x200x177mm (7.87”x7.87”x7”).
When designing a 3d printed car, I had to be aware of what many people’s 3d printed build areas were. All parts are made to be able to be printed on a standard bed size of 200x200x177mm.
If your build area is smaller than 200x200x177mm (7.87x7.87x7"), you will want to slice the parts that do not fit your bed size. A great program for this is Autodesk’s Netfabb Basic https://www.netfabb.com/products/netfabb-basic.
1. Simply import the STL file that you want to cut
2. Go to the “cut” panel on the right, and select which axis you want to make your cut on (either the x, y, or z)
3. Select “Execute Cut”
4. then select “cut” at the bottom of the screen
5. Now you have two cut pieces. If the new cut pieces show up in any color other than green, run the Repair tool at the top (red cross icon), and repair the part.
I’ve included a link to a good how to slice video.
Bed adhesion and bed surface material:
For successful printing, you want to make sure that you have good bed adhesion, but that you are still able to remove your print easily without breaking the part.
Select a good bed material, whether that is PEI sheet or Printinz Bed. I used both of these materials when printing this model. PEI is good for items that are below 2” in height. Many of the large items would become dislodged before the print was finished, so I would only use the PEI for the chassis pieces, and small piece of the body. I used the Printinz bed for all of the body parts because it gave good adhesion, and because I could easily remove the item by flexing the bed.
If you are still using Blue Tape and Glue, determine which is the best method for your printer for the optimal around of bed adhesion.
Printer settings:
I printed my prints at .2mm layer thickness. My machines resolution is 1/128 micro stepping. Any layer height or micro stepping will work, this is all based on your preference and your machines specs.
Supports:
A majority of the parts require supports for successful printing. Make sure that your slicer’s generated support material is very easy to remove, so that supports just break off easily and are not something that you have to fight to get off. I highly recommend good slicers like Cura and Simplify3d. Any slicer works, just make sure you have your settings correct so that it will be easier to work with.
Slicer Settings and Speed:
The parts are already orientated in the way that I printed them. Many parts like the rear wing print vertically, this is to reduce any imprints that support material might have left. Simplify3d has very intricate tool paths which allow the machine to slow down on intricate parts. If your machine does not slow down on intricate parts, you can either adjust your slicer setting speed, or re-orientate the part.
Material:
I printed all of the parts with PLA. I have a heated bed to prevent warping set at 60C for the first layer and 43C for all remaining layers. You can print this item on printers without a heated bed, but you may have some slight warpage on larger parts.
You can print this car in any material the you like, but ABS may be hard because of the warpage that you may encounter on larger parts.
Step 3: Tools That You Need
Required tools
2.30mm drill bit
m3 drill bit
m3x1.0mm tap (for open holes)
m8 drill bit (can use 5/16 if you do not have a m8)
m10 drill bit Tap wrench
Metric Allen wrenches
hobby knife (for cleaning up any parts and removing support material)
Needle nose pliers (for removing supports in small areas)
Adjustable Pliers
Adjustable Pump Pliers
May need if your electronics do not come already soldered.
Wire Cutters
Wire Stripper
Soldering Iron
Wire Crimper
TAPPING
The RS-LM kit requires tapping screws to keep weight down, and because that what all modern RC cars require. Tapping is how we can put screw/bolt threads into the plastic, so that you can screw it in, instead of using a nut to fasten to parts together. If you have never used a tap before, tapping plastic is easy! Insert the tap end into the hole and slowly apply pressure while turning. Plastic taps very fast, so try to move slowly, with constant pressure. Once you have the tap through the hole or once you have reached appropriated depth, slowly reverse the turn—keeping the tap straight—backing the tap out of the hole. You want to avoid yanking it out or you will destroy any threads that you made. Once you have the tap out, check to see if there are well defined threads, and you are done.
Step 4: RS-01 Chassis Layout
Chassis Layout for the two Renderings
Servo Holder (green)
ESC (blue)
Battery Cage (white)
Rear Shock Mount (Red)
Rear Shock Tower (blue)
Right & Left Lower Control Arm (blue)
Left and Right Rear Damper Mount (Yellow)
Step 5: Rear Differenital
Mechanical Parts needed:
Tamiya F104 C Parts 51379 (motor mounts and rear diffuser)
Tamiya F104 54158 (Aluminum Diff Housing set)
F104 rear shaft--- they come in aluminum, steel, and carbon [iber
I choose carbon [iber Tamiya 54162 Tamiya wheel stopper 58431
Motor bearing holders--- multiple options
I purchased 3Racing F109-01 ... it had multiple sizes and a spacer for the left side wheel that is needed.
Tamiya Front uprights--- again there are many choices I choose the Carbon Reinforced Uprights 54154
(4) 1050 Ball bearings for front wheels Gears— many different choices and brands
I choose F1 Machined spur gear 93T 64 Pitch
Robinson Racing Pinion 64P 23T Differential Balls... many choices
Cheapest one is 3racing 3RB-B30
F104 wheels and tires--- multiple choices and rubber compounds
I choose Taimya F104 Mesh Wheels for Rubber tires 51398 51400 F104 Rubber Tires Rear
54198 F104 Rubber Front tires Hard compound
all of my parts were purchased from TQRCracing www.tqrcracing.com
The F104 rear differential kit comes with a manual to assemble. Please follow the Tamiya instructions for this step.
Step 6: Chassis Deck
Printed Parts
chassis bottom (front)
chassis bottom (mid)
chassis bottom (rear)
chassis bottom (for large printers)
rear diffuser
1. Print out the chassis deck pieces.
Print out chassis bottom (front), chassis bottom (mid), and chassis bottom (rear).
If you have a large printer (350mm bed), you can print out the one piece chassis front section for large printers.
2. Bolt the sections together with m3 x 6 flat screws and washers.
3. The rear diffuser will be attached when you attach the motor mounts in the later section. The diffuser sits on the chassis bottom (rear), and is sandwiched between the chassis bottom rear, and the motor mounts.
Step 7: Front Pushrod Suspension
I. RS-01 FRONT SUSPENSION ASSEMBLY
A. Front Assembly Parts
Printed Parts
Center Bottom
Center Top
Left and Right Lower A-arms
Left and Right upper A-arms
Left and Right Rocker Arms
Metal/Plastic Parts
F104 front uprights (if using building the F104 version) (3) printed spacers
(10) m3x10 set screws
(3) Aluminum Unthreaded Spacers 6mm OD, 5mm Length, for M4 screw size
(2) countersunk washers for m3 https://www.tqrcracing.com/shop/product_view.asp?... (4) 5x8x2.5mm bearings
(2) m3x14 flat screws
(3) m3x30 flat screws
(3) m3 nuts
(2) m3 nylock nuts
(2) m3x30 bolts
(2 packages of 12) Team Associated 6271 Short Ball End Set [will use 16]
(1 package of 6) Traxxas 2742X Short Rod Ends Ball Connector [will use 4] (2) spacers m3x3.2 ID x4.5 od http://www.mcmaster.com/#92871A171
(2) M3 treaded rod cut to desired length of the shocks that yo are using
B. Assembly parts
A-Arm Assembly
1. Take the all of the arms for the front suspicions, Upper and Lower A-arms, and drill the holes on the ends with the 2.3mm drill bit.
2. Tap all the holes with the m3x1.0 tap.
3. screw in m3x10 set screws into the holes.
(an prototype version of the front suspension, but is used to illustrate the assembly and how the set screws must be placed into the lower and upper a-arms).
4. Insert a tap screw into the single hole on the end the arm which will support the ball end that holds the front spindles or uprights.
Rockers Assembly
5. Drill and tap the holes on the rockers.
6. Grab (4) 6271 Short Ball sockets and balls, and insert the balls into the sockets. *** This is extremely hard unless if you use pressure. Take the wood and drill and tap it so that you can screw the ball screw into the wood. The place the ball socket above, holding the hex end with pliers. Then place another piece of wood onto of it all and press down. On most occasions you will hear an audible pop as the ball and socket are joined. Unscrew the now joined ball and socket from the wood and then you are done. ****
7. Screw these 4 ball and sockets into the rocker arms. You may need to use the pliers. Get them snug, do not try to over tighten or you may break the plastic or ruin the threads in the hole and you will have to remake the printed part.
8. Assemble the Rocker Arms. Take the printed Rocker Arm parts and, if needed, clean out the bearing hole (large hole) with an m8 or 5/16 drill bit. Place it on a piece of wood and grab it with a set of pliers so that it does not spin, and with the drill set on slow (or going slow), slowly drill out the hold so it is perfectly 8mm.
9. Insert the 5x8x2.5mm bearings into the rockers. Each rocker requires two bearings.
Center Assembly
10. Take the Center Top and Center Bottom and place (8) Team Associated 6271 Short ball nuts.
11. Drill and Tap the holes on the center top, These holes will be the holes that are on the perimeter of the part.
12. Drill and Tap the holes on the center bottom.
13. Install the ball screws into the holes that you just created on both the top and Bottom centers.
14. Screw (8) Team Associated 6271 Short ball sockets onto the the A-arm ends. 2 per each A- arm.
****IT IS A GOOD IDEA TO TAP ALL BALL SOCKET/ROD ENDS WITH THE M3 TAP FOR EASILY INSTALLATION******
15. Attach the A-arm ball socket ends on to the associating ball nut that are on both the top and bottom center sections.
16. Take (4) Traxxas 2742X Short Rod Ends and their centers and attach them by snapping them in.
17. Once attached screw these (4) short rod ends into the ends of the A-arms.
18. Place (2) m3x30 screw through the Traxxas rod ends and bolt them together with a m3 nut. this will make sure everything is aligned for the next step.
19. take (4) Team Associated 6271 Short ball sockets ends and (2) m3x10 set screws and screw in them into the rod ends. Screw them 30% in.
20. Install the remains two ball socket ends onto the opposite end of the m3 set screw. You now have a short, yet adjustable rod end for the push rod.
21. Install (2) Team Associated 6271 ball sockets into the ball sockets on the rod end that you just made, leaving the other side open.
22. Taking these newly formed rod ends and the rocker arms snap the rod end onto the one side of the rocker arm. NOTE THE ANGLE OF THE ROCKER ABOVE FOR REFERENCE! IT MUST BE ON THE APPROPRIATE SIDE.
23. Install an open ball socket on the other end of the rocker arm.
24. Drill and tap the screw holes in the upper center that hold the rocker arms.
25. Take the m3x3.2 ID x4.5 od spacers and sliced one into the bearings from the bottom. 26. Install the rockers on to center top.
27. Attach the rod end that is located onto push rod that is attached to the rocker, and install the screw nut into the hole on the lower A-arm. If the you cannot screw it you can drill the hole with the m3 drill bit and then 5 minute epoxy the nut screw into the hole.
CHECK THAT EVERYTHING MOVES SMOOTHY BEFORE CONTINUING
28. Drill the Three holes that are in a diamond shape on both the top center section and lower center section with the m3 drill bit to clean out the holes.
29. With the upper and lower centers, rocker arms and push rods installed. Grab the (3) Aluminum Unthreaded Spacers 6mm OD, 5mm Length, for M4 screw size.
30. Drill the Three holes that are in a diamond shape with the m3 drill bit to clean out the holes.
29. Insert the 3 unthreaded spacers placing them between the center top and center bottom, aligning them with the 3 diamond bolt holes.
30. Insert (3) m3x30 screws from the bottom chassis pointing upwards. 31. Place the printed spacers onto the screws.
32. Holding the assembly, slowly guide the assembly onto the screws. Through the bottom center, then then unthreaded spacers, and then the top.
33. Bolt with a nuts.
34. Install the threaded rod into the rod ends.
33. flip the car over and drill and tap the two feet of the bottom center.
34. Install (2) set screws. These set screws allow you to adjust the ride height of the front suspension. Set it accordingly.
35. Install printed spindles or Carbon Reinforced Uprights into the ball joints. Reinstall the m3x30 bolts and screw on the two nylocks.
[it is a good idea to use use epoxy on set screws on the lower A-arms that connect to the carbon uprights to prevent them from backing out from vibration.]
Front Suspension is completed.
C. ADJUST THE CAMBER OF THE FRONT WHEELS
Camber or the tilt of the front wheels, which allows for better cornering can be adjusted by either screwing out the m3 set screw on the lower A-arm or by using a shorter rod ends for the upper A-arms.
Step 8: REAR SUSPENSION
PARTS
Printed Parts
Battery Box Front
Battery Box Middle
Battery Box Rear
Damper mount
Left Damper Spring Mount
Right Damper Spring Mount
Triple Shock Mount
Rear Shock Tower (Right)
Rear Shock Tower (Left)
Metal or Printed Parts
(2) 55mm shocks
(1 pack) of Yokomo Rear side roll springs (YOKR12-21SH) * can use different brand if you choose
(2) Yokomo Roll Spring Holder (YOKR12-21) *
(6) Team Associated Ball and socket nuts
(1) Tamiya RM-01 Carbon rein L Parts- Links 2pc RM01 / F104 V2
(10) m3x25 screws
(2) m3x30 bolt
Steps
I’m going to skip writing drilling and tapping and assume that you understand that is required for install screws.
1. Install Battery Cage on to the center chassis (chassis B). Placing an m3 screw into each leg of the box.
2. Install two ball socket screw (Team Associated) on the the holes on the center section. These particular holes are for the front of the rear lower control arms which are illustrated in the pictures above with blue socket nuts.
3. Install the shock on to the center hole of the battery cage with the rear ball socket facing the rear of the car.
4. Install a ball nut into the damper holder located on the far left side of the center chassis battery box cage. (it is the last section of the cage, towards the rear).
5. Install rod ends on to the m3x35 turnbuckles, and install the turnbuckle onto the center chassis.
6. take the Rear chassis bottom and install the rear shock mount and rear shock tower, install with (4) m3x25mm screws.
7. Install team Associated ball socket screw in the center rear hole on the rear shock mount. (if your shocks came with a ball and socket and a particular screw then use that screw instead for this step.
8. Install the rear damper. Damper is the the same shock with the spring removed.
9. Scew in two team associated screws nuts on to the back chassis section.
10. Join two chassis sections by attaching snapping the rear damper to the rear chassis piece and by attacking the lower control arms (m3x35 turnbuckles) by snapping them into the the ball screws.
11. Attach the rear shock to the bottom rear section by snapping it into the ball screw on the rear shock mount.
12. Take the left and right spring damper mount and attach the a Roll Spring Holder to each mount.
13. Install the Roll Spring onto the holder.
14. Instal the spring damper mounts by screwing them in with a m3x30 bolt, and placing a m3 nut on the end.
Make sure everything moves smoothly. And adjust your spring tension. The rear droop can be adjusted by adjusting the strength the spring in the shock and it’s settings. Roll of the damper can be adjusted with different fluids.
Rear Assembly is now completed.
Attachments
Step 9: Front Shock Assembly
(2) 55mm Shocks
(2) m3 female to female unions (2) m3x45mm turnbuckles
I used 2 55mm shocks with 110m shock shafts. This is not necessary. You can use the 55mm shocks as is, with longer m3 turnbuckle to reach. You can cover the shafts with carbon fiber tubing 4mm id, 6mm od to make it look nice.
(2) m3 female to female adapters. You can also make these by using nylon standoffs for a computer and cutting off the male side.
Steps:
1. Prepare the shocks and mount them to the battery box with 2 m3x35mm bolts and bolt them to the battery box.
2. Slip the m3 union onto the m3 threaded rod and connect the threaded rod to the shock.
3. This is easier if the threaded rod is already installed into the ball socket end that is attached to the rocker arms.
4. Join the rod and the shock shaft together.
ENSURE THAT THE THREADED ROD AND THE SHAFT ARE TOUCHING INSIDE THE UNION SO THAT THE ASSEMBLY DOES NOT BEND WITH THE SHOCK IS COMPRESSED.
Step 10: Steering
printed servo mount
(2) m3x30 screws
18 gauge steel wire or Turnbuckles (m3x32) [TT02B Full Turnbuckle set) servo arm (I used Hitec RCD 55701 Standard Aluminum Servo Arm)
if using linkage
[TT02B Full Turnbuckle set http:// www.tqrcracing.com/shop/ product_view.asp?p_id=7734] (Hitec HS-77BB servo)
Hitter Servo arm like Racers Edge RCE10384B http://www.tqrcracing.com/shop/product_view.asp?p...
1. cut the bolt mounts on the backside of the servo along the red line in the picture.
2. Install Servo Arm onto the Servo and screw it in
3. Install the servo into the servo mount and bolt it to the servo mount.
If using Steering Linkage kit
1. If using turnbuckle install the ball studs so that they face up when the servo is mounted to the car.
2. Attach another ball stud to the axle.
3. Depending on whether you are using printed axle or carbon reinforced F104 axles, the turn buckles you may need will vary.
4. Measure the distance between the servo arm when it is pointed straight towards from the from top the car, and measure to the axle where the wheels are pointed straight.
5. After determine the length, in step 3 choose your turnbuckles that you require and screw in one side into the ball socket. Remember these are turnbuckles so the opposite side will screw in the reverse.
6. Attach one side of the turnbuckle to the ball screw, and the other side to a ball screw on the axle.
If using 18 gauge wire
1. If using 18 gauge: install the 18 gauge steel wire into the car and then attach it to the bell crank’s arm the tis at a 90 degree angle
2. Cut two pieces of wire and install them into the bell crank. Stretch them out to the wheels.
3. Align the wheels so they are at their farthest angle from the bell crank, or furthest lock to lock.
4. Take a maker and mark where the point is.
5. Cut the wire with wire cutters.
6. Bend the wire at a 90 degree angel with
the needle nose pliers.
7. Insert that end into the hole on the
uprights.
8. Check that that tire can move freely without jamming and then repeat not the other side.
9. Once done with both fronts ensure the they move freely, and point forwards. Readjust and redo as needed.
NOTES
Use wire ties to hold keep all of your wires tight and compact. After the body has been on the car for a day or two the wires will stay compact so taking the body on and off will be easier.
Location of parts in the car.
Battery Wires, ESC charger and ESC capacitor, and on/off switch may need to be lengthened via cutting and splicing the wires.
A Battery Lipo Battery charger extension wire can be used to allow you to charge the battery without having to remove the body.
Attachments
Step 11: Rims and Tires
PARTS
If using Printed Rims with printed tires:
Printed Parts:
(2) Front Rims for Printed Tires
(2) Front Rims for Printed Tires
(2) Front Tire
(2) Rear Tire
(For Printed Tires, use a Flexible filament like Ninja Flex.)
Note* Printed tires do not have the same grip as rubber tires. Newer flexible filaments may have better grip.
If using Printed Rims with Rubber Tires:
Printed Parts:
(2) Front Rim
(2) Rear Rim
If using Plastic Rims and Rubber Tires:
Taimya F104 Mesh Wheels for Rubber tires 51398 51400
Rubber Tires:
Tamiya F104 rubber tires come in many different tire compounds, so there are a variety of choices.
I used:
51400 F104 Rubber Tires Rear
54198 F104 Rubber Front tires Hard compound
Note: Rubber tires require CA Tire glue (smells just like super glue... I believe it is just that—high priced super glue.)
Prepare the tires
1. Slide the tires and foam onto the rims.
2. Readjust the tire foam with your hand to make sure that the tire sets squarely on the rim.
3. work the bead of tire on the rim so that it sits on the rim’s edge (the rim has grooves, the tire bead should sit on the outside of the outer groove).
4. Take the CA glue or superglue (with gloves), pull the tire back lightly and insert the tip into the gap.
5. Let the glue pour out. It will travel down along 1/3 of the rim. Go around the rim repeating this method until the tire is glued to the rim.
6. Repeat on the opposite side of the rim, working in thirds.
7. Once all rims are glued, attach them to the chassis, affixing a 4mm lock nut on each side.
Step 12: Body Assembly
Printed Parts:
front wing (white)
front wing spacer (white)
nose (white)
front (red)
mid body front (white)
rear (red)
turning vane support (right) [white]
turning vane support (left) [white]
turing vane right (white)
turning vane left (white)
turning vane red (left)
turning vane red (right)
rain light for working light (black) or standard rain light
rear wing (red)
rear wing (white)-- smaller white wing accent
driver body (if using helmet)
Decorations:
Stickers: http://www.rc-expert.com/110-1984-1985-1988-1991-... mclaren-senna-mp42b-4-5b-6-7-8-decal-sticker-rc-body-sr036-p-5062.html
better adhesion decals: http://www.tqrcracing.com/shop/product_view.asp?p_id=4471
tire Goodyear decals http://www.tqrcracing.com/shop/product_view.asp?p_id=2741
Helmet (if using body): http://www.ebay.com/itm/1-10-Prepainted-F1-Driver... Helmet-fr-RC-Car-Ayrton-Senna-Mclaren-Honda-Mp4-4-5-6-/361495660967
Rainlight: 5mm Flash LED light – Red (F1 Tail Light) http://www.ebay.com/itm/1-10-Prepainted-F1-Driver... shop/product_view.asp?p_id=1800
You will need:
Superglue
5-minute epoxy
toothpicks (for mixing and applying epoxy) hobby knife
sandpaper (180-220 grit)
Body parts need to be glued together.
Driver Helmet can be found on eBay from seller “0.01shop”, or by searching “1/10 repainted F1
helmet.”
Attachments
driver.stl
front wing spacer.stl
front wing.stl
front.stl
mid body front.stl
midbody rear.stl
nose.stl
rain light for working light.stl
rear diffuser.stl
rear wing (red).stl
rear wing (white).stl
rear.stl
turning vane left.stl
standard rain light.stl
turnign vane red (right).stl
turning vane red (left).stl
turning vane right.stl
turning vane support left.stl
turning vane support right .stl
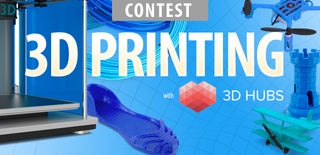
Runner Up in the
3D Printing Contest 2016