Introduction: RS-LM 2014 Audi R18 E-Tron Quattro 3d Printed RC Car
By: Brett Turnage
twitter: @3dprintracetech
ARTICLES
3ders.com
3printr.com
https://www.3printr.com/40501-4740501/
Competitionx.com
http://www.competitionx.com/news-feed/3d-printed-r...
RC Car Action Magazine (rccaraction.com)
RS-LM 2014 Audi R18 E-Tron Quattro “The Ali"
This car is about inspiration. I first planned on nicknaming this car “the Edwin” after one of my best friends. The R18 LMP1 race car and Audi’s commercials featuring it have always inspired me. One in particular, that beautifully imagined what it would be like if people drove an R18 as an every day car as a brilliant way to show how Audi’s racing technology makes it into their production cars. That commercial has always stuck with me as the ultimate in imagination and dreams for a car fan. However, that nickname had to change because recently my hero died, so it has a new nickname “The Ali.” So, this car is about inspiration, and about inspiring others in the way that those commercials and Muhammad Ali inspired me. So this car, is my tribute to The Greatest of all time: Muhammad Ali and to Audi’s amazing R18 race car. A fitting tribute because Audi called this black R18 “black beauty” and Ali always said he was the prettiest.
Enjoy it, Be inspired by it. Rest in peace Champ! Let’s Go Audi!
“I’ve done wrestled with alligators, I’ve tussled with a whale. I done handcuffed lightning—throw thunder in jail.”
-Muhammad ali
Enjoy it, Be inspired by it.
About the car
Love and watching the 24 hours of Lemans
I love watching the 24 hours of Leman! I’ve been staying up and watching it for years nows, and this weekend I will be sitting up at my computer watching the laps go by as the race turns from light to dark to back to light again. I’ve always rooted for the former champs Audi, who dominated the LMP1 class until Porsche’s re-emergence in the sport last year. I’ve seen their cars evolve from the R-10 to the R15, to the cockpited R18. This particular version, the 2014 Audi R18, was to me, the most beautiful iteration. It was beautiful with a hint of ugly—almost like perfection need a flaw. When I decided to do a Lemans car, there was no other car that I wanted more than this one.
”I’m so Mean”
“I murdered a Rock, injured a stone—Hospitalized a brick! I’m so mean I make medicine sick.” -Muhammad Ali
This is the prototype version of the 2014 Audi R18. I choose the pre-race version rather than the racing version because it consists of my favorite colors: black and red, and it is also easier to print versus the white version that has a variety of many color patches. This car varied from the racing version in some areas: the front fenders have openings, the wing endplates hang over the rear of the car, and other crucial difference, but wow is it strikingly mean! There is something magical that happens when a car is completely black. It just looks sinister and evil. Like it is Darth Vader’s car or the batmobile. The black on this car is Real Black from Solutech 3D filament. The red accents are Real Red as well as the grey which is Real Grey are also from Solutech 3D.
”I’m Pretty”
“I’m handsome, I’m pretty, and cannot possibly be beat.” -Muhammad Ali
I designed the car and chassis in Fusion360 in the last month. I try to be as close to the original car that I can possibly be so that you see the R18 when you look at it, and not a representation of it. Some changes had to be made, mainly a box for the rear suspension because real car’s differentials are not 1/2 the height of the car, but I’m proud of the finished product, and it looks incredibly gorgeous. (if anyone would like to just make a model I have the correct rear without the suspension box). I printed it at 1/128 micro stepping at .2 layer height. I also have to give credit to Simplify3d and it’s amazing tool paths, and Bondtech extruder-I believe these two products helped make the car look beautiful.
”Too much Speed for him, I’m Fast! Too Fast!”
“I’m so fast that last night I turned off the light switch, and was in bed before the room was dark.” -Muhammad Ali
This car is build to be fast. No only does this car look fast, but it was actually meant to be fast! The RS-LM chassis that I developed was designed to fit the largest and fastest motors that you can stick in an RC car. I am running the car with a 13.5T motor, a much faster motor than the 21.5T motor in my F1 car. It has a long wheel base (320mm wheel base) for stability, all wheel drive with the capability to run two differentials or a one way gear in the front. The RS-LM’s extra room also makes it so that it can fit standard size lipo batteries (148mm long). The car’s 3d printed rims use F1 front tires, but the car can also fit touring car rims and tires. This car is low! The RS-LM fits all of these features into an extremely low profile package—the highest point of the car is 56mm, all to keep the weight down low for better cornering and speed, and to allow for an extremely realistic LMP1 body.
RS-LM Lemans RC chassis features:
*Long wheel base 320mm
*Belt driven drivetrain
*All wheel drive
*two differentials
*Larger battery capacity
*Built for speed—high powered motors
*Adjustable ride height
*Adjustable camber
*F1 front tires
*Low— fit all the mechanics of a touring car body into a low profile.
Enjoy this car..
“Float like a butterfly and sting like a bee. Rumble young man, Rumble.” -Muhammad Ali.
Goodbye Champ.
Step 1: RS-LM 3D Printed RC Chassis Build Intro
The RS-LM is a 3d printed Lemans RC car chassis that uses off the shelf RC parts for its drivetrain. The reason why I choose to use RC gears, is because they are readily available, and they are manufactured to better specifications than your printer can make printed gears. To make this car capable of competing and running with professional RC cars, it has to have drivetrain parts that are made to the same specifications as it's store bought counterparts. This increases the reliability of the car, as well as the overall top speed. This choice allows anyone to build the car, where its overall performance is not based on how well you calibrated your machine.
The chassis has many 3d printed parts that can be interchanged with plastic parts that can be ordered in either plastic or metal, so it makes this chassis upgradable so you can modify the chassis as you see fit—just like real RC car racing kits.
Professional RC cars require an investment in electronics, because of this investment I have worked hard to ensure that your car will be reliable, durable, and can perform to the highest standards. Reliability is key!
THIS KIT CONSISTS OF OVER 98 INDIVIDUAL 3D PRINTED PARTS
The 3d printed parts are the car. Without them you would just have:
(4) double joint universal shafts (2) differentials (2) belts (4) tires (4) shocks, and a assortment of bearings, nuts, and screws.
I have optimized the .stl files to be able to be printed on machines that have the standard bedside of 200x200x200.
THERE ARE 3 MANUALS INCLUDED IN PDF FORM: (PLEASE USE THEM AS THEY ARE FILLED WITH PART NUMBERS AND DETAILED PICTURES OF EVERY STEP)
*R18 BODY ASSEMBLY MANUAL (located in "Build the Audi R18 body"
*RS-LM AUDI MANUAL
*RS-LM PARTS LIST
Step 2: 3D PRINTING TIPS FOR SUCCESSFUL PRINTS
3d printing tips for Success
The RS-LM R18 Audi E-Tron Quattro “The Ali” consists of over 98 3d printed parts.
Optimized for standard 3d printer build areas of 200x200x177mm (7.87”x7.87”x7”):
When designing a 3d printed car, I had to be aware of what many people’s 3d printed build areas were. All parts are made to be able to be printed on a standard bed size of 200x200x177mm.
If you're printed bed is smaller than the standard size you will want to slice the parts that do not fit your bed size. A great program for this is Autodesk’s Netfabb Basic https://www.netfabb.com/products/netfabb-basic.
1. Simply import the STL file that you want to cut
2. Go to the “cut” panel on the right, and select which axis you want to make your cut on (either the x, y, or z)
3. Select “Execute Cut”
4. then select “cut” at the bottom of the screen
5. Now you have two cut pieces. If the new cut pieces show up in any color other than green, run the Repair tool at the top (red cross icon), and repair the part.
I’ve included a link to a good how to slice video.
Bed adhesion and bed surface material:
For successful printing, you want to make sure that you have good bed adhesion, but that you are still able to remove your print easily without breaking the part.
Select a good bed material, whether that is PEI sheet or Printinz Bed. I used both of these materials when printing this model. PEI is good for items that are below 2” in height. Many of the large items would become dislodged before the print was finished, so I would only use the PEI for the chassis pieces, and small piece of the body. I used the Printinz bed for all of the body parts because it gave good adhesion, and because I could easily remove the item by flexing the bed.
If you are still using Blue Tape and Glue, determine which is the best method for your printer for the optimal around of bed adhesion.
Printer settings:
I printed my prints at .2mm layer thickness. My machines resolution is 1/128 micro stepping. Any layer height or micro stepping will work, this is all based on your preference and your machines specs.
Supports:
A majority of the parts require supports for successful printing. Make sure that your slicer’s generated support material is very easy to remove, so that supports just break off easily and are not something that you have to fight to get off. I highly recommend good slicers like Cura and Simplify3d. Any slicer works, just make sure you have your settings correct so that it will be easier to work with.
Slicer Settings and Speed:
The parts are already orientated in the way that I printed them. Many parts like the rear wing print vertically, this is to reduce any imprints that support material might have left. Simplify3d has very intricate tool paths which allow the machine to slow down on intricate parts. If your machine does not slow down on intricate parts, you can either adjust your slicer setting speed, or re-orientate the part.
Material:
I printed all of the parts with PLA. I have a heated bed to prevent warping set at 60C for the first layer and 43C for all remaining layers. You can print this item on printers without a heated bed, but you may have some slight warpage on larger parts.
You can print this car in any material the you like, but ABS may be hard because of the warpage that you may encounter on larger parts.
Step 3: Tools That You Need
Required tools
2.30mm drill bit
m3 drill bit
m3x1.0mm tap (for open holes)
m8 drill bit (can use 5/16 if you do not have a m8)
m10 drill bit
Tap wrench
Metric Allen wrenches
hobby knife (for cleaning up any parts and removing support material)
Needle nose pliers (for removing supports in small areas)
Adjustable Pliers
Adjustable Pump Pliers
May need if your electronics do not come already soldered.
Wire Cutters
Wire Stripper
Soldering Iron
Wire Crimper
TAPPING
The RS-LM kit requires tapping screws to keep weight down, and because that what all modern RC cars require. Tapping is how we can put screw/bolt threads into the plastic, so that you can screw it in, instead of using a nut to fasten to parts together.
If you have never used a tap before, tapping plastic is easy! Insert the tap end into the hole and slowly apply pressure while turning. Plastic taps very fast, so try to move slowly, with constant pressure. Once you have the tap through the hole or once you have reached appropriated depth, slowly reverse the turn—keeping the tap straight—backing the tap out of the hole. You want to avoid yanking it out or you will destroy any threads that you made. Once you have the tap out, check to see if there are well defined threads, and you are done.
Step 4: Differential/Solid Axle
1. GEAR DIFFERENTIAL/SOLID FRONT AXLE
The car can use either 2 differentials, front and rear or Solid Axle in the front.
Other differentials may work with the car. I used 3racing differentials from the Sakura XI Touring car kit.
Printed
Bearing holders
PARTS NEEDED
Differential
Differential: 3Racing (SAK-XS110) (2 if not using solid front axle)
for solid front axle
Solid Axle: 3Racing (SAK-D134)
38T Pulley: 3Racing (SAK-D135)
Bearing Holder
(4 total) 3racing Bearing Housing for Sakura D4 XI Ultimate CS Sport Advance 2016 (SAK-X07)
Differential manual comes with the differential that you buy. I will include a link to the Sakura XI touring car kit if you do not have the manual for how to assemble your differential.
http://www.tqrcracing.com/forum/files/manual/xispo...
The car can use either 2 differentials, front and rear or Solid Axle in the front.
Other differentials may work with the car. I used 3racing differentials from the Sakura XI Touring car kit.
After differentials are assembled set them aside.
Step 5: ASSEMBLE CHASSIS DECK
Printed Parts:
Front deck
Center deck (part 2)
Center deck (part 1)
Rear deck
Chassis deck motor brace
Metal Parts:
M3 x 5 flat screws
M3 x 1.0 x .5 flat nuts
(4) M3 x 8 flat screws
Steps:
1. Remove any support material from the printed parts.
2. Drill the joining holes with 2.4 mm drill bit.
3. Press in M3 x 1.0 x .5 flat nuts into he nut holders screw in m3 x 5 flat screws repeat until all sections of the deck are attached.
4. Position Chassis deck motor brace. screw it in with m3 x 8 flat nuts and tighten with m3 flat nuts.
Step 6: 3. SUSPENSION
Printed Parts:
Front
suspension front mount (+10mm)
suspension rear mount (left)
suspension rear mount (right)
front suspension arm (left)
front suspension arm (right)
C-hub (left)
C-hub (right)
Front Knuckle (2)
Rear
suspension rear mount
suspension rear mount (+8.4)(right)
suspension rear mount (+8.4)(left)
rear suspension arm (left)
rear suspension arm (right)
Rear Knuckle (left)
Rear Knuckle (right)
*** Print Rear Knuckles at 100% infill (the Upper Control Arm mount needs to be solid) ***
Metal parts:
outer pin m3 x 22.9 pin 3Racing SAK-28
inner pin m3 x 46 pin (4) 3Racing SAK-27
m3 x 6 x 1.0 spacer (4) 3RAC-WF305/PK
m3 x 6 x 2.0 spacer (4) 3RAC-WF320/PK
m3 x 8 flat screw (8)
m3 x10 set screw (10)
(2) 3Racing FGX F1 4mm ball stud M3 x 5 4 pcs (FGX-123)
(2) Yokomo 39.1mm Front Double Joint Universal Driveshaft [YOKBD-010RW] *any 39.1mm double joint shaft can work
(2) Kokomo 40.6mm Front Double Joint Universal Driveshaft [YOKB7-010FW] *any 40.6mm double joint shaft can work
(4) M2 x 10 pin (M2 x 10 shaft B-02-VBC-0020)
King Pin Post for 3racing Sakura Zero (3Racing SAK-42)
Aluminum M3 Countersink Washers (3Racing 3RAC-WC3/PK)
Plastic parts:
Hex adaptor SAK-D123
Bearings:
(4) 5x8x2.5 bearings
(4) 10x5x4 bearings
Shocks:
(2) Associated FT Front Aluminum Shock Kit Blue RC18R / FGX 2pcs
with
(2) Rear Damper Spring Set for Sakura FGX 3Racing FGX-303
Shock oil 30 weight (Team associated 5422)
other shocks can work as long as they have a 2mm shaft.
Assemble the shocks with the manual appropriate to the shocks that you bought.
Steps:
For all holes, tap the hole with a m3 x 1.0 tap before installing bolt.
1. Clean out the front suspension mounts holes that are on the perimeter of the plastic parts with an m3 drill.
2. Tap the bolt holes on the mounts with an m3 x 1.0 tap.
3. Install 10mm front suspension mount onto chassis. (Front of the chassis has two holes at the end, rear has one hole).
4. Install the rear suspension mount onto the rear with two m3 x 8 bolts.
5. Chassis with Front and rear mounts installed.
6. Prepare Front and Rear Suspension arms by drilling out the m3 holes with a m3 x 1.0 drill bit.
7. Tap the suspension mount holes that are on the top of the suspension arm with a m3 x 1.0 tap.
8. Remove the supports from the front and rear knuckles
9. Clean out the m3 holes on both the front knuckles and the rear knuckles with an m3 x 1.0 drill bit.
10. Clean out the bearing holes on the knuckles with an m10 drill bit for the rear and an m8 drill bit for the front. PLACE THE DRILL IN REVERSE MODE. The points to clean out the holes of any printed debris, not to cut.
11. For the rear knuckle, tap the hole on the side with an m3 x10 tap. The hole that is farthest from the bottom m3 hole.
Front Suspension
12. Tap the holes on the top of the front knuckles with the m3 x 1.0 tap.
13. Press the (4) 5x8x2.5 bearings into the front knuckles. You may need to use pliers to get them set. For the rear bearing push in with either a large allen wrench or some other flat tool to get the rear bearing set correctly into the knuckle.
13. Insert two front universal joints into the front knuckles
14. Clean the C-hubs m3 hole with the m3 x 1.0 drill bit.
15. Not the direction of the C-hubs in the pictures The extended side of the C-hub should face towards the front of the car.
16. Install the C-hubs into the front arms by using the m3 x 22.9 pin outer pin. Use oil and pliers to press the pins in , if they are snug. Repeat on the other side.
17. Install a 4mm ball stud on each arm, and install the shock with the piston body at the top.
18. Press the inner pin (m3 x 46) into the front suspension arms.
19. Install the long King Pin Post into the bottom of the c-hub and the shorter King Pin Post into the upper hole in the C-post. Slide the Front Knuckles into the C-post, with the Knuckle arm aimed toward the shock.
20. Install a 3Racing FGX F1 4mm ball stud M3 x 5 4 pcs (FGX-123) on the C-hub in the circle housing on the top of the C-hub, with the 4mm ball stud facing the front of the assembly.
21. Screw in the Front knuckle with an m3 x 12 screw on the bottom, and an m3 x 8 screw with a m3 countersink washer on the top.
Repeat on the other side.
Rear Suspension
20. Clean out the Rear Knuckle bearing holder with a m10 drill. Remember to run the drill in reverse. The point is to clean, not to cut.
21. Press the 10x5x4 bearings into the rear knuckles. Make sure that they are seated into the holders.
22. screw in a m3 x 12 into the upper a-arm holder on the rear knuckle. Slide on a m3 x 6 x 2.0 spacer, and install a 4. (spacer is not shown in the picture below)
23. Install the Rear Knuckles into the rear suspension arms with the horizontal panel aiming towards the front of the car.
24. Press in the m3 x 22.9 pins, to join the knuckles to the assembly.
25. Install the 4mm ball stud into the shock mount hole.
26. Install the m3 x 44 outer pin into the rear suspension arm.
27. Install the rear shock.
28. Install the universal joint.
30. Place an m3 x 6 x 2.0 spacer on the outer pin on the front arm assembly facing the front of the car and a m3 x 6 x 1.0 spacer on the rear (towards the rear of the car).
31. Install the front arm assembly onto the chassis by pressing the pin into the front suspension mount.
32. Place the suspension rear mount (left)
suspension rear mount (right) on the end of the outer pin, and press it onto the outer pin.
33. Bolt the rear mounts to the chassis with an m3x10 flat screw.
34. Switch to the rear suspension arm. Place an m3 x 6 x 2.0 on to side facing the front of chassis, and a m3 x 6 x 1.0 spacer on the side facing the rear of the chassis.
35. Install the suspension rear mount (+8.4)(right)
suspension rear mount (+8.4)(left) on to the outer pin and press on.
36. Affix the suspension rear mount (+8.4)(right)
suspension rear mount (+8.4)(left) to the chassis with m3x10 flat screws.
37. Both arms assembly installed in the car.
Upper Suspension Arms
Plastic / Metal Parts:
m3 x 16 set screw
(4) ball sockets
(8) 4.8mm ball studs (3Racing 3RAC-BS48H5/PK)
*rear upper arms can use 4.8mm ball studs or ball nuts… front could use 4-4.8mm ball studs.
TO SNAP UPPER SUSPENSION ARMS ONTO BALL STUDS, USE PLIERS TO AVOID BREAKING ANY PARTS.
1.Insert (2) 4.8mm ball studs into the front base plate, so that they are pointing towards the front of the car.
2. Insert (2) 4.8mm ball studs into the rear base plate so that they are also aiming towards the front of the car.
3. Create your front Upper Suspension Arms by screwing in two ball cups onto a m3 x 16 set screw.
4. Attach the arm to the front suspension assembly by snapping it on to the ball nuts on the C-hub and the front base plate.
5. Assembly the rear upper suspension arms by repeating the step with the m3 x 32mm turnbuckle. Remember it is a turnbuckle, so one with screw on by reversing the rotation.
6. Attach the rear upper suspension arm onto the rear assembly by snapping it on the ball studs on the rear knuckle and rear base plate.
7. Adjust the lengths until you have the desired camber (wheel tilt) that you desire. If you need to take an arm off wedge it off with an allen wrench, by positioning it on the base plates and levering the ball cup off of the ball stud.
Attachments
front suspension arm (right).stl
rear shock tower.stl
suspension rear mount (new) (right).stl
suspension rear mount (new) (left).stl
suspension rear mount (new) (left)(+8.4) .stl
rear suspension arm (right).stl
suspension front mount (+10mm).stl
rear suspension arm (left).stl
rear knuckle (right).stl
front suspension arm (left).stl
c-hub (right) .stl
rear knuckle (left).stl
front knuckle.stl
c-hub (left).stl
suspension rear mount (new) (right)(+8.4) .stl
suspension rear mount.stl
Step 7: Drivetrain
Printed Parts:
(4 total) Bulk heads (Left and Right)
Base Plate (Front)
Base Plate (Rear)
Rear shock tower
(2) Bearing Holder
Plastic Parts:
Bearing Holder
Assembled Differential(s) or One Way Axle
Metal parts:
(8) M3 x 8 flat screw
(4) m1.6 x 5 Socket Screw
(2 Aluminum M3 Countersink Washers (3Racing 3RAC-WC3/PK)
Bearing:
(4) M10 x 15 x 4
Belts:
Small belt :
3Racing Low Friction Rear Belt 177 (Bando Belt) [SAK-X09]
Long belt:
3mm pitch (GT2), 210 teeth, 6mm wide Single Sided Neoprene Belt with Fiberglass Cords.
(A 6R53M21060 from sdp-si.com)
Front Differneital
1. Slide an M10 x 15 x 4 bearing onto either side of the differential outer joint.
2. Slide the bearing holder onto the bearing.
3. Place the long belt on the differential (or solid axle)
4. Place the Differential into the bulkhead. The front axle or differential should have the gear on the righthand side of the car. The bulkhead should have the recessed area pointing inwards towards the differential or straight axle.
5. Turn the bearing holder so that arrow points toward the top hole on the bulkhead.
6. Screw in the differential into the bulkheads with the m1.6 x 5 socket screw.
7. Place the base plate (front) on top of the front bulkhead assembly and screw it in with four m3 x 8 flat screws.
8. Screw the front bulkhead assembly onto the chassis using four m3 x8 flat screws. The bulkhead assembly should be positioned with the base plate bar aiming towards the front of the chassis.
9. Insert the universal shafts into the differential.
Rear Differential
1. Slide an M10 x 15 x 4 bearing onto either side of the differential outer joint.
2. Slide the bearing holder onto the bearing.
3. Place the short belt on the differential
4. Place the Differential into the bulkhead. The front axle or differential should have the gear on the righthand side of the car. The bulkhead should have the recessed area pointing inwards towards the differential or straight axle.
5. Turn the bearing holder so that arrow points toward the top hole on the bulkhead.
6. Screw in the differential into the bulkheads with the m1.6 x 5 socket screw.
7. Place the base plate (rear) on top of the front bulkhead assembly and screw it in with four m3 x 8 flat screws.
8. Screw the front bulkhead assembly onto the chassis using four m3 x8 flat screws. The bulkhead assembly should be positioned with the base plate bar aiming towards the front of the chassis.
9. Place two 3Racing FGX F1 4mm ball studs into the rear shock tower. One on either slanted side.
10. Screw the rear shock tower into the rear bolt head with two m3 x 8 flat screws with (2) m3 countersink washers.
11. Attach the rear bulkhead to the chassis with four m3 x 8 flat screws.
12. Insert the universal shafts into the differential.
13. Attach the rear shocks upper ball socket to the 3mm ball studs on the rear shock tower.
Step 8: Steering System
Printed Parts:
Steering Arm (right)
Steering Arm (Left)
Steering link holder
Steering link
Plastic / Metal Parts:
(m8 x 10.5) Steering Post for Sakura XI Sport [3Racing (SAK-XS111)
m3 x 0.2 shim spacer
m5 x 0.2 shim spacer
m3 x 6 x 1.0 spacer (3Racing-WF310/PK)
(3) 4.8mm ball stud
m3 x 8 Flat Screw
m3 x 6 button screw
The steering system can be purchased if you want a metal or plastic alternative.
7075 Aluminum Steering System for 3Racing Sakura Ultimate/ XI Sport (SAK-U113/PK)
or
Aluminum Steering System for 3Racing Sakura Ultimate/ XI Sport (SAK-U113/P_V2)
or
Plastic Motor Mount and Steering System for Sakura XI Sport (SAK-XS101)
Bearings:
(4) m5 x 8 x2.5
(2) m3 x 6 x 2.5
Steps:
1. Insert (2) m5 x 8 x2.5 bearings into the Steering Arms, one on the top and one on the bottom.
2. Place the m8 x 10.5 steering post into the bottom of the steering arm.
3. Place a m5 x 0.2 shim spacer on top of the bearing on the top steering arms.
4. Place the Steering Link Holder on top and screw it in with (2) m3x6 button screw.
5. Switch to the Steering Link and insert two m3 x 6 x 2.5 bearings into the bearing mounts.
6. Screw in two 4.8mm Ball Studs into the Steering Link with (2) m3 x 6 x1.0 spacers.
7. Install one 4.8mm ball stud on the horizontal hole on top of the Steering Link.
8. Place a m3 x 6 x 0.2 shim spacer on the front holes on both of the Steering Arms.
9. Screw the Steering Linkage to the Steering Arms with (2) m3 x 8 Flat Screws.
10. Attach two 4.8mm hex Ball Studs into the Front Knuckles, screwing them in with an m3 x8 flat screw. The Ball studs should be aimed down.
Once assembled, Place the Steering System into the chassis with the long held traveling UNDER the Steering System.
Step 9: Center Gear Adaptor
Plastic or Metal Parts:
Spur Gear 48 Pitch - 85T
(2) M5 x 8 x 2.5
19T / Plastic Gear Adaptor (3Racing SAK-XS103)
or
7075 Aluminum Gear Adaptor With 19T Aluminum Pulley and Shaft (3Racing SAK-XS304)
(4) M2 x 5 Flat Screw
Steps:
1. Assemble by pressing in an m2 x 5 bearing into each of the Center Pulley/Gear Adaptors.
2. Place both Gear adaptor on either side of the Spur Gear.
3. Place the Gear Adaptors on either side of the Spur Gear, line up the holes and then screw in (2) M2 x 5 Flat
4. Fasten screws on either side.
Step 10: Motor Mounts
Printed Parts:
Motor Mount
Motor Mount Arm
Gear Mount (Right)
Gear Mount (Left)
(2) Spur Gear Holder
Plastic / Metal Parts:
(2) M3 x 6 Button Screw
M5 x 25 Post
(2) M5 x 0.2 Shim Spacer
(2) M1.6 x 5 Socket Screw
Alternative parts:
Plastic Motor Mount and Steering System for Sakura XI Sport (SAK-XS101)
Aluminum Motor Plate For Sakura XI Sport (SAK-XS109 / PK)
or
7075 Aluminum Motor Mount (SAK-XS303 / PK)
Battery Holder Plastic Replacement (for Spur Gear Holders) [SAK-U106]
Steps:
1. Slide the M5 x 25 post into the Spur Gear.
2. Attach a M5 x 0.2 shim on either side of the shaft.
3. Attach a Spur Gear Holder to either side of the shaft and attach it by screwing in an m3 x 6 screw on either side of the shaft.
4.Attach the Gear Mounts to the chassis with m3 x 8 flat screws.
5. Attach the motor mount to the Left Gear Mount and to the Motor Mount Arm. Screw them in with m3 x 6 set screws, and attach it to the chassis with m3 x 8 flat screws.
6. Slide the long belt over the 19T gear mount on one side and the short belt on the other 19T gear mount.
7. Slide the Spur Gear Assembly down into the Gear Mounts.
8. Screw the Assembly into the Gear Mount with two M1.6 x 5 Socket Screws.
Step 11: Upper Deck
Printed Parts:
Upper Deck (front)
Upper Deck (rear)
Metal Parts:
(10) M3 x 8 Flat Screw
(2) M3 flat nuts
3Racing FGX F1 4mm ball stud M3 x 5 4 pcs (FGX-123)
Steps:
1. Connect both the Upper Deck sections together with two m3 x 8 Flat screws, and tightening them with a nut on each screw.
2. Slide the Upper Deck into the long belt so that the belt with pass over the Upper Deck, and set it on the bulkheads.
3. Attach the Upper Deck to the chassis by attaching the front to the bulkhead and screwing it in with (4) m3 x 8 flat screws, and (4) screws attaching the upper deck to the rear bulkhead.
4. Screw in 4mm ball stud into the shock tower mounts on the front Upper Deck.
5. Attach the Front Shocks top mount to those 4mm ball studs.
Step 12: Belt Tensioner
Parts:
Belt Tensioner 3Racing SAK-58/BL
there are many different Belt Tensioners that can work.
Assemble the Belt tensioner as per the instructions, and install it into the chassis on the bottom. It should be located where the center chassis sections meet.
Step 13: Servo and Servo Mount
Printed Parts:
Servo Mount
Servo Mount Top
Plastic / Metal Parts:
Hitec HS-77BB Low Profile Servo
Servo Arm (you can use a long servo 1.5-2” arm I used a servo arm and then made an extension with a piece of carbon)
(2) M3 x 16 flat screws
(10) M3 x 8 flat screw
(2) 2.0mm Aluminum M3 Flat Washer
[3RAC-WF320/PK]
(4) 4.8mm ball stud (3RAC-SD48H5/pk)
m3 x 12 bolt m3 x 3 aluminum washer [3RAC-WF330/PK] 4.8mm plastic ball cups
(1) m3 x 16 set screw
Steps:
1. Cut off the rear servo bolt mounts on the rear of the servo. The mounts opposite to the wire, and servo arm.
2. Screw the m3 x 12 bolt down through the top of the servo arm so that it pokes out the bottom. (remember, the servo will be mound upside down)
3. Slide on the m3 x 3 aluminum washer, and screw on the 4.8mm ball stud.
4. Install the servo arm onto the servo
5. Slide the servo assembly into the servo mount.
6. Screw the servo into the mount with (2) m3 x 8 flat screws.
7. Attach the Servo top onto the servo mount and screw in with (6) m3 x 8 flat screws. Two screws go though the servo mount and attach it to the upper deck.
8. tap the 4.8mm plastic ball cups with an m3 x 1.0 tap, and screw in the m3 x 16 set screw into one ball cup.
9. attach one ball cup on to the 4.8mm ball stud on the servo, and the other onto the ball stud that is on the steering system.
10. Plug the servo wire into the first slot of your receiver, and plug in the esc. Turn it on and adjust the servo arm making sure that it is aimed straight. Adjust the servo arm if it is not. Adjust the steering linkage so that the wheels are aimed straight in the neutral position by unscrewing one side of the plastic ball cups to lengthen or tighten to shorten. Once you have the position correct, attach the steering linkage to the servo arm so that the steering linkage connects the servo arm to the steering system.
Step 14: 3D Printed Rims and Rubber Tires
Printed Parts:
(4) Rims
Plastic or Metal Parts:
This car uses Tamiya F104 Front Rubber Tires. There are many compounds from different makers. I used Tamiya 51399 Rubber Tires.
CA Tire glue (smells just like super glue… I believe it is just that—high priced super glue.)
(2)M2 x 10 shaft Pin (VBC Racing B-02-VBC-0020)
(4) Wheel adaptor ( 3Racing 3RAC-WX124/PK)
(4) 4mm Aluminum Locknut (Tuning Haus TUH1066)
Wheel Adaptors
1. Slip in M2 x 10 shaft pin into the universal joint.
2. Slide a wheel adaptor over the pin. Make sure the pin slides into the grooves of the wheel adaptor.
3. Repeat on every universal joint.
Prepare the tires
1. Slide the tires and foam onto the rims.
2. Readjust the tire foam with your hand to make sure that the tire sets squarely on the rim.
3. work the bead of tire on the rim so that it sits on the rim’s edge (the rim has grooves, the tire bead should sit on the outside of the outer groove).
4. Take the CA glue or superglue (with gloves), pull the tire back lightly and insert the tip into the gap.
5. Let the glue pour out. It will travel down along 1/3 of the rim. Go around the rim repeating this method until the tire is glued to the rim.
6. Repeat on the opposite side of the rim, working in thirds.
7. Once all rims are glued, attach them to the chassis, affixing a 4mm lock nut on each side.
Attachments
Step 15: Motor and Electronics
Battery:
This chassis has a lot of room for a variety of batteries types. I use two 2000mah batteries that are run in parallel with an adaptor. It can run batteries up to 158mm long.
Motor and ESC:
Any size can be used.
48 Pitch Pinion Gear 23T
Step 16: Building the Audi R18 Body
You will need:
Superglue
5-minute epoxy
toothpicks (for mixing and applying epoxy) hobby knife
sandpaper (180-220 grit)
binder clips
(2) m3 x 12 flat screws
(2) m3 x 8 flat screws
For windshield, source the lexan from a lexan rc body. I used the windshield from a car. Bolt it to the windshield frame. Side windows can be glued in.
Driver Helmet can be found on eBay from seller “0.01shop”, or by searching “1/10 repainted F1 helmet.”
Stickers http://www.the-border.com/A.-Racing-R18-Quattro-f...
(they do not have the best adhesive on the back so add place the stickers on a sheet of 3m adhesive—-something strong like 3M 468MP)
If using lights... make sure you drill the holes to make sure that the lights fit perfectly before starting to assemble the body
Start at the front...
Glue the pieces together. Try to get the sections to line up as best as you can.
Fenders bolt in with an m3 x 12 screw at the rear hole and a m3 x8 screw at the front.
Lights: any 1/10 light kit works with 4 white lights and 2 red. You need two sets, one for each side. I used Yeah Racing LK-0001WT
Red pieces and stripes: you will need to use sandpaper to sand them down until they fit perfectly. Use a flat surfaces to lay the sandpaper on, and run the stripes over them.
Use superglue to glue them in. Be careful with the superglue because it can stain the printed part with a white residue, so be careful.
Attachments
antenna.stl
inner red stripe (right).stl
midbody front (left).stl
left outer red stripe.stl
left front red stripe.stl
front wheel well connection panel.stl
front splitter.stl
cockpit (right).stl
body base.stl
r18 body assembly guide.pdf
body front (left) .stl
cockpit (left).stl
body front (right) .stl
body rear mid (left).stl
body rear mid (right).stl
midbody front (right) .stl
mirror (left).stl
mirror (right).stl
number plate (left).stl
number plate (right).stl
rear body diffuser (left).stl
outer red stripe (left).stl
rear wing endplate (left) (1).stl
outer red stripe (right).stl
rear body diffuser (right).stl
rim.stl
rear fender (right).stl
rear diffuser mount.stl
side skirt (left).stl
side skirt (right).stl
rear fender (left).stl
windshield wiper base.stl
silver cockpit top.stl
windshield (for lexan).stl
turning vane (right) .stl
rear fender nose ( left).stl
rear fender nose (right).stl
rear fender red stripe (left).stl
rear fender red stripe (right).stl
rear wing (208mm).stl
rear wing endplate (right) (1).stl
red hood number plate.stl
red small righthand side.stl
scoop (black).stl
scoop (red).stl
side bracket.stl
side window (left).stl
side window (right).stl
turning vane (left) .stl
winshield (solid).stl
winshield wiper.stl
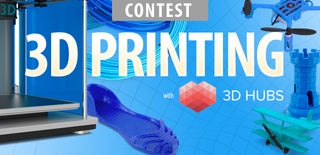
Participated in the
3D Printing Contest 2016