Introduction: Radio Wave
Introducing the new Radio Wave. This new Product will revolutionize how sailors and water sport enthusiasts will listen to the radio, or just put music to your ears in the shower. The radio wave is the result of a 12 week product design project at Dundee University. The task was to use the workings from an existing radio and redesign it completely. I loosely based my radio on a character card that i made but i deviated from it along the way. This rugged and impact resistant radio will withstand the hardest knocks and can be taken anywhere and stuck to almost any surface. have a go at building one for yourself. I will take you through exactly what you need to build it and the way i found best to make it.
Step 1: Materials List
This is a list of the materials that you will need to build the radio wave
. 1 working radio chip and speaker
. arox 1sq M of fiberglass matting
. arox 500ml of fiberglass resin
. arox 10 ml of fiberglass hardener
. 1 new bathroom plunger
. 1 tub of car body filler and hardener
. 3 small pieces of wood
. 2 small pieces of 3 mm pvc plastic
. 1 old bike inner tube
. 3 small nuts and bolts ( size is optional)
. 1 hot melt glue stick
. 1 can of gloss spray paint
These are the materials i use but many can be substituted with alternate build methods.
Step 2: Exploded Diagram
This is an exploded Diagram of my final radio. This should make putting the radio together easier once you have made all the parts.
Attachments
Step 3: Dismantelling the Radio
I started by dimanteling the radio we had been given. There were only a few screws to take off the outer casing to get to the circuit board. It is a simple FM/AM radio from Amazon and there is a link below. For my radio i discarded the outer casing ( apart from the battery holder which i chopped down as small as possible) and just kept the circuit boar and the speaker. I took the volume control and the tuning control off the circuit board and re-wired them with longer wires. this will give me room to put these controls in different places.
http://www.amazon.co.uk/Sony-ICFS22-Personal-Radio/dp/B0007YQNSW/ref=pd_cp_ce_1
Step 4: Building the Outer Casing
Step 2
Step one is the making of the impact resistant and waterproof outer shell. The things you will need are
1. A well ventilated space either outside or in a large room. This stuff smells pretty bad and the smell will hang around for a few days if you do it in your house. I did it in my new shed hence the reason for all the electrical wiring that is exposed in many of the photos.
2. A piece of cardboard.
3. A cone shaped mould.
4. A flat surface
5. Cling-film
6. Resin
7. Hardener
8. Matting
9. An old brush
10. A pair of scissors.
11. An old container.
12. A dust mask
13. latex gloves ( i was already wearing mine)
Once you have gathered up all these materials you are ready to get started. Start off by putting on your gloves and dust mask. Next put down your cardboard so prevent any spillage that may happen wrecking the work top. Take the cones mould and line it with two layers of cling-film. This will stop the resin sticking to your mould. Next cut up the fiberglass matting into a manageable size. Place one layer of the the matting into the mould. I found if you cut up the middle of the square it made it easier to place the matting in to the mould. Once the whole mould is covered it is time for the resin. Get a flat bottomed container that is disposable and mix in 1 part hardener to 50 parts resin. So I found about 2 ml of hardener with 100 ml of resin was about enough for this project. mix it well as if it is not mixed properly the reaction can not happen and the resin will not cure. With the old paint brush begin applying the resin to the matting. Apply generously and make sure the matting is soaked through. There should be no dry spots. Repeat this process another 2 times so you end up with 3 layers of matting completely covering the mould. The resin will begin to set after about 15 minutes so you have to work relatively quickly. With the left over resin and matting on a flat surface make a disk shape. that is bigger than the base of the cone. make this about 3 layers thick also. After around 20 minutes the resin should be almost set and because of the chemical reaction it should become hot. Just before the resin sets completely take the cone out of the mould and peal off the cling-film then allow it to set completely. You should end up with a perfect cone and a rough disk shape. Both can be trimmed roughly at this stage with a pair of scissors. I should add that if you are working with fiberglass at colder temperatures then you may need to apply heat or add more hardener to make the resin harden. You have completed stage 2!
Here is a link to where i got my fiberglass. It is available in many places online.
http://www.allscotltd.co.uk/
Step 5: Fitting the Suction Pad
Step 3
I moved from my shed at home into the University workshop for the next stage. Many may not have some of the tools or these kind of facilities available to them but you should be able to make do.
I cut out the disk into a perfect circle using the ban saw and a disk sander. I had made a paper template to see what size of disk i would need to still be able to fit in all my electronics. Next i had to fit the plunger to the bottom of the disk. I bought this plunger from B&Q for £3. It has a thread on the base which made it ideal. I drilled a whole large enough for the thread to fit through so i could screw on the plunger from the other side and it would sandwich the fiberglass disk. I then cut off the excess handle and gave it a quick sand for neatness.
Step 6: Trimming the Shell to the Correct Size
Step 4
Next I marked where the disk would sit on the inside of the cone. This allowed me to cut off the excess around the bottom. I cut it with a hack saw on top of an extraction bench because the dust is very toxic. Wear a dust mask for this stage. I cut the bottom in a wavy pattern to make it look more shell like and gave it a sand to get rid of any splinters.
Step 7: Making Fixings to Hold the Case Together
Step 5
Next i made this fixing that will hold the bottom disk onto the cone. To do this i cut out 4 pieces of wood that had one face that is at the same angle as the slope of the cone and one face that can sit on the bottom face. This took some fiddling about to get the correct angle and to get them lined up properly. I used more fiberglass and resin to fix the three pieces of wood to the cone. the fiberglass sticks really well to the wood so it gives a nice strong fixing. In the drilled hole i counter sunk bolts that were a tight fit. this meant that the bolt could be tightened from the bottom plate. I drilled 3 holes on the bottom plate for the bolts to pas through.
Step 8: Making the Seal
Next I got an old bike inner tube to make a seal around the disk. I cut a piece much smaller than the disk and sewed it together with a needle and thread. This gave me a very strong fixing between the rubber. All i had to do then was stretch it over the disk and my waterproof seal was complete.
Step 9: Creating the Shell Like Texture
The next step in the process was to create the correct shape on the outside of the fiberglass cone. To make my desired pattern to make it look like a shell i used car body filler. I mixed up the filler and hardener (comes as a set from Halfords). I also used a trick i had seen online which is to mix in some fiberglass resin as this makes the filler a better consistency to work with and is easier to create the shell texture i wanted. I used the card provided to apply the filler and i would suggest wearing gloves for this process as it can get quite messy. The filler took a lot longer to dry than in the test i did beforehand but i can only assume this was because it was colder and i had mixed in less hardener. Once the filler is completely dry i spent quite a long time sanding out all the bits of filler i didn't want. You can make it any shape you want and it would be fun to experiment with different shapes. By now your shell should be very strong and if it is like mine you would struggle to break it!
Step 10: Adding the Contolls
To make the dials to control the volume and tuning i used the universities laser cutter. I made the shape in adobe illustrator and sent it to the cutter. This was a very easy and accurate process. I decided to make them out of 3 mm black PVC as this will stand out against the colour of the shell. any people will not have access to a laser cutter so the same shape could probably be made using a coping saw and a file. Next i used my dremel to drill a very small hole through the centre of the plastic shape. This allowed me to screw the dial on using the existing screws that previously held the dial on. Next i used the dremel again to cut two holes through the shell to create slots for the dials to come through. I marked a line from the centre down to the base to line up where i was going to cut the hole. I used a very small grinding blade that my dremel had as it was perfect for the job and it cut through relatively quickly. I then carefully sanded the hole to the correct size for the dial so the dial is not sicking out all the way but is out enough so it is easy to turn. I have fitted a piece of rubber under the shell to seal it better.
Step 11: Painting
I sprayed both parts of the casing with an off white gloss. I had to do two coats to give a good finish. this will really make it stand out and give it the natural look I really want. I Used an old piece of cloth to spray against and i hung up the parts to dry. It is important to spray in quite a warm room so that the paint can dry properly.
Step 12:
Ok. by this step you should have finished building all the parts you need to start putting the radio together. I have drawn an exploded diagram labeling all the components and the way in which they should be assembled. This is what my Radio Wave looked like when it was finish all put together.
Thanks very much for looking at my Instrucable and I hope you will have as much fun making it as i had designing and building it.
any comments or feedback would be much appreciated and if you have any alternate ways you built the radio wave then let me know
thanks
Francis Munnoch
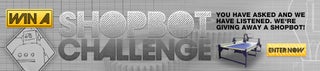
Participated in the
ShopBot Challenge
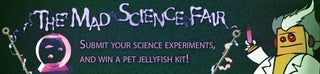
Participated in the
The Mad Science Fair
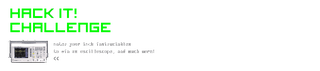
Participated in the
Hack It! Challenge