Introduction: Razor Blade Cutter
Several years ago, I had a few small projects in which I needed to cut hundreds of small wires to a specific length and also hundreds of small plastic tubes to specific length. Typically the plastic tube would be crushed on the ends if using side cutters, but for my purpose, the plastic tube needed to retain the general shape. I was inserting something inside, so I needed to be sure the inner diameter was not greatly altered.
My solution is the device shown in this Instructable.
This design could be scaled up or down depending on your needs, so I
won't really give specific dimensions, but if you have a question about some part, let me know and I will measure.
Bill of Materials
- 2x4 pieces
- 2 long bolts with straight shanks (metal rods could be used also)
- 2 small springs for lifting the razor blade assembly (not too strong, but enough to hold it up)
- 8 sheet metal screws (for holding the metal pieces to the wood razor blade slider assembly, other screws could be used, this is just what I had)
- 1 short bolt, washer and nut for lever arm middle pivot
- 1 longer bolt, washer, nut for pivot arm end pivot
- 2 spring for the short and long bolt just to give some tension, so you don't need to over tighten the nuts. These are stronger than the first two springs
- 1 long thin metal piece for the lever arm (other designs could be achieved, depending on your needs or preference)
- one square or rectangular piece for the main plate for pinching the razor blade in place
- 1 small angle iron for lever arm pivot on top of the razor blade slider assembly
- 1 larger angle iron for the bottom of the razor blade slider assembly
- other small angle brackets for the lever's end pivot piece and for mounting the whole cutter assembly to a work surface (I have 4 total, but more could be used)
- other wood screws to mount the angle brackets as shown. I used deck screws because I have many of them
- assorted washers for spacers as needed (see pictures for reference)
- 2 short pieces of brass rod (could be other metal, this is just what I had)
- razor blades
- powered graphite for lubricant if desired
Warning: Use caution when placing fingers near a razor blade, especially with this much leverage. You could easily lose the tip of a finger. Also be sure to use proper eye protection in case the blade were to suddenly shatter from whatever you are cutting (maybe too large or too hard).
Step 1: Making the Base
I chose a piece of 2x4 for the base. I drilled a couple of holes in which I could insert some partial threaded bolts. I wanted a very tight fit, so I drilled to the exact size of the shank, then pressed them in. Be sure to make these holes as straight (perpendicular) as possible to the 2x4 for smoothest operation.
I then attached another piece of wood for the lever arm pivot (seen in step 4). This can be fastened with angle brackets, or just screwed directly to the 2x4 base, but this was sufficient for what I needed. This piece has a hole drilled in for the lever's pivot. I would wait until you have the full unit assembled. This way, you can position it at the appropriate spot to give you the best range of motion and leverage.
Step 2: Razor Blade Holder Assembly
The next step was to make a robust assembly to hold the razor blade in place. The design had to ensure proper alignment of the blade, so it was perfectly parallel to the base's cutting surface, yet be easy to replace the blade as needed.
You can see several pieces attached to this slider block, which was trimmed to match the angle iron depth. It could also be taller or shorter based on your needs. For mine, I made it as tall as the main metal plate holding the razor blade.
So, we will start with the main metal place which has the 4 screws to hold the razor blade. I notched out the corners to allow a deeper contact toward the edge of the blade (you can see next to the small brass rods). I added spacer washers under the top screws to help provide good leverage when the two lower screws were tightened to really allow the metal plate to pinch the razor blade at the bottom against the piece of angle iron that is mounted on the bottom and back of this assembly. The brass rods are there to align the razor blade to be parallel to the cutting surface as well as provide a hard stop so the blade doesn't slip vertically up into the assembly when pressing it down during the cutting.
Next, I drilled holes to match the spacing of the bolts on the base. Since this assembly will be sliding up and down on the bolts' shanks, I made these holes slightly larger, to ensure they could glide smoothly. Later I added some graphite powder for lubrication. These holes must go through the angle iron on the bottom. If you plan it out, you might just be able to drill through the angle iron pre-spaced holes, otherwise, you just need to create your own holes.
The angle iron was held in place with two more of the same screws used on the razor blade's metal plate. Washers were added to allow proper spacing. The bolt heads actually touch the 2x4 base. This prevents the razor blade from going too deep and breaking when pressing hard on the lever. The blade cuts slightly into the base like approximately 1/16", to ensure it severs the wires and tubing completely.
For this assembly, a short angle iron piece was added to the top, held in place with two more screws. A hole was drilled in the center for the lever arm pivot (seen in step 4).
Finally, attach the razor blade, and be sure you have aligned the guide pins to hold the razor blade vertically. It is a good idea to measure the distance from the bottom angle iron to the edge of the blade on both ends, to ensure it is equidistant. This will give a good, flat cut. Be careful not to cut yourself on the razor blade.
Step 3: Attaching the Razor Blade Slide Assembly to the Base
Place the two smaller, weaker springs on the vertical bolts, then add the razor blade slider assembly on top. It should "hover" but be easy enough to push down. Of course, the lever will help add much torque for pushing down on the assembly, so be sure to account for the weight of the lever as well. The nice thing about this design is you can experiment with various springs to get the desired operation feeling.
Step 4: Lever Arm and Pivot Bolts
Next, you will need to drill holes into the lever arm.
The middle pivot hole should be circular, like a typical drill bit, and larger than the bolt's shank dimension.
For the end pivot on the lever arm, I actually made a slot shape. Mine is very rough and ugly, but it's functional. This slot shape is critical because if you only have circle holes, the lever might not be able to go through the full range of motion smoothly. The slot along with the pivot bolts and springs will ensure smooth motion.
I also used a long bolt which I cut off for the end pivot (rather than just a threaded bolt and nut), then drilled a hole in the end of it (correct hole location should ensure the spring has some tension and not too tight or too loose) and used a brass rod bent to prevent it from falling out (see step 5). Since this is rotating constantly, I didn't want it to gradually un-thread, if I had used a nut. Of course, lock washers, etc could be used.
Step 5: Attaching the Lever Arm
Middle pivot bolt and spring would be attached first, then maneuver the lever arm to where you think you would want it to be at rest. Pinch the end of the arm to the vertical wood piece attached in step 1, then push down on the lever until the razor blade touches the base. If this position feels good, then mark it and drill the end pivot hole here. Be sure it is just slightly larger than the bolt diameter, so it does not bind during operation.
Attach the bolt as shown with the spring, washer and pin (or nut if you prefer). Don't over tighten if you use a nut. The spring is there to hold a nice tension.
Step 6: The Final Assembly and Operating Positions
Examine the final assembly to ensure there is no parts that will interfere or bind improperly and prevent smooth operation.
Then screw it or clamp it down to your work bench or other flat surface or mount it in a vice and cut away!
Warning: Use caution when placing fingers near a razor blade, especially with this much leverage. You could easily lose the tip of a finger. Also be sure to use proper eye protection in case the blade were to suddenly shatter from whatever you are cutting (maybe too large or too hard).
I typically feed the wire or tubing from the rear, and have markings on the 2x4 base to guide me if I need consistent lengths. Sometimes, I need wires that are a few inches long, so I use another piece of 2x4 against the base, and have markings on it.
Step 7: Basic Cutting Motion
A simple video just to show the cutting motion.
(Let me know if the videos don't work. I just converted them to a different format because the previous ones weren't playing properly on my computer)
Attachments
Step 8: Cutting a Wire
A video to show cutting a wire. I typically don't cut heavy gauge wires, so I can't really attest to the max size. This was designed for smaller gauges like 12AWG or smaller. If you build one and find it works well on other sizes, let us know in the comments section.
Attachments
Step 9: Cutting a Small PVC Tube
A video to show cutting a tube. I typically don't cut thick tubes, so I can't really attest to the max size. This was designed for smaller plastic tubes. If you build one and find it works well on other sizes, let us know in the comments section.
It's not likely that this design would cut metal tubes. I've never tried. It might do OK on very thin copper tubing or other soft metals.
Attachments
Step 10: Final Thoughts and Ideas
Some final thoughts and ideas:
A hole at the output side to allow the cut pieces to fall into a collection bin (see first image)
Finger guard (see second image)
Eventually, I want to add a motor and gear box and touch switches. I think it would be cool to make it powered. Although, there is inherent danger of a moving blade powered by a motor, so I would have two separate switches externally mounted, so you would be required to keep your hands clear of the blade, and press the switches for each operation. For sure would need a finger guard.
Let me know if you build one or if you have already built something similar. I know I've seen an automatic wire cutter and stripper on youtube in the past: http://www.youtube.com/watch?v=F2O7kGE34EA
http://www.thingiverse.com/thing:268
Step 11: Videos of Cutting Other Stuff
Here are some more videos of cutting other stuff. You might need to click the video link, then click the Play button in the lower left corner.
Mine seemed to cut them just fine. I could tell they are a harder plastic than the PVC tubing I show in the other video, but didn't seem to be an issue.
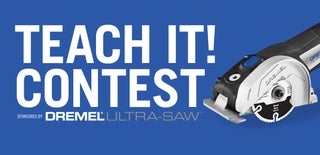
Participated in the
Teach It! Contest Sponsored by Dremel