Introduction: Restoring Corroded Battery Contacts
Ok, before anyone else says it, this took more effort than it probably should have. These RCX bricks are pretty common on eBay and go for pretty cheap, so I could have bought another one rather than going to all this effort, but that's not how I do things. Once I got started I just couldn't help myself and I kept experimenting with different things to remove the corrosion and bring these battery contacts back to the way they were originally. All of these processes are new for me, but I can already see that they will be useful for other projects so I view this as a learning exercise as well. I have considered using electrolysis to remove rust on tools, but I never got to the point when it seemed necessary.
I am currently moving to a new house and I only have a few tools left unpacked, so for this project I only had basic tools to use. I started out using only regular household products that everyone should have laying around, combined with some bits and pieces scrounged from salvaged electronics parts. I ended up spending just $10 for one specialized item online, a piece of pure nickel for use as an electrode for electroplating. Other than that, I had everything else on hand.
Step 1: Cleaning Battery Corrosion
I bought this Lego Mindstorms RCX brick on eBay for cheap because it said it didn't work. I actually just wanted the IR remote that it came with so this piece was just a bonus. Once I saw the Alkaline crystals and corrosion on the battery contacts, I tried cleaning them off and eventually wound up restoring them back to their original nickel plated form.
The corrosion on these battery contacts was from Alkaline batteries. These batteries often leak their electrolyte all over the battery compartments if you leave them inside a remote or toy for too long. These white crystals of dried electrolyte are mostly Potassium Hydroxide also called caustic Potash, which is a strong base and will need to be dissolved and neutralized. For this, I started pulling the contacts out of the plastic housing and putting them in a plastic cup so I could soak them in household vinegar. Three of the contact bars were so corroded they would not come out of the housing, so I had to immerse the whole thing in vinegar.
The vinegar and the potash bubbled and the crystals eventually dissolved leaving behind cleaner contacts that now showed spots where some weird copper plating had been deposited and other spots where the underlying steel had rusted. I could have left it like this, but I like experimenting and I have a shortage of projects these days so I decided to take it a little further.
Step 2: Cleaning Rust
A friend of mine finds a lot of rusted artifacts with his metal detector, and he has a lot of luck with this electrolysis method for removing rust. Since I am not going to scrub these tiny pieces of metal with steel wool, I decided to give this a shot.
I took another plastic cup and filled it with hot water and a little baking soda (some people say baking soda doesn't work, but it definitely does). I wrapped a little thin UTP wire around the end of a cheap screwdriver bit and stuck it in the cup to be my steel/iron electrode.
I took the most rusted piece first, hung it from another piece of UTP wire and attached it to the negative lead on a 9 volt battery. I dropped the rusty terminal piece into the water electrolyte and waited. You can tell something is happening after about 5 or 10 minutes, but to get the heavy rust off I had to wait over an hour.
After the first piece, I switched the 9 volt battery to a 12 volt AC adapter which worked much better. Once the water turned rusty, I dumped it out and started fresh. It seemed to me that the fresh water and baking soda worked better at removing the rust.
Unfortunately, this process also took the nice nickel plating off the otherwise dull stamped steel contacts. By this point I wanted perfection for my final result, so I started looking for a way to shine and protect the newly cleaned parts.
Step 3: Nickel Plating Part 1: Electrolyte
I found this great Instructable about how to do nickel electroplating at home and I decided I would give it a shot.
I bought one electrode for $10 and I was able to cut it into 2 long strips with my tin snips. I bent the ends of my electrodes so they would hang on the edge of a spaghetti sauce jar. I filled the jar with household vinegar and added a pinch of salt.
I don't have any alligator clips handy at the moment so I twisted some more UTP wire over the top of the electrodes. I hooked my barrel jack connector up to the 2 nickel electrodes. I tried a few different AC adapters, but eventually settled on the 12v one I used for the electrolysis. After about an hour the vinegar turned a pale green and the positive electrode's (cathode's) sharp corners became rounded off and the surface was pitted. The negative electrode (anode) had long streaks where bubbles had deposited fresh layers of nickel.
Step 4: Nickel Plating Part 2: Plating
According to the plating Instructable, you should use a low voltage power source and plan to make multiple coats of nickel to get a nice, even finish. I made about four passes of about an hour with 2 AA batteries (3 volts) and saw very small improvements each time. I decided to go back to my 9 volt AC adapter and although it seemed to make bubbles about the same size and speed, after only a few minutes I saw much better results. I left each piece in the bath for about 10 minutes, adjusting and rotating the pieces until the bubbles can touch each part and the plating shines all over.
Step 5: Polish, Plate, Repeat...
I didn't polish the steel before I plated it (big mistake), so I don't have a good example of what they looked like without the plating. They probably would have ended up with a nicer finish if I had polished then first. Once I stepped up the plating voltage I only had to polish them one more time.
Step 6: Entire Process
I am very satisfied with these results. Now the contacts are clean and make good electrical connection with the batteries. The plating ensures that they will remain clean and conductive for a long time.
Lessons Learned
The thing that took the most time was experimenting to find what worked best. Next time I would skip the batteries altogether and use the AC adapters instead. For the electrolysis, 12v seemed to work best, but for the plating process a 9v adapter worked best. Before you start plating anything, polish the metal with some Cameo or other general metal polish. I think I could have gotten a better end finish if I had spent some more time prepping the raw metal.
The nickel plating can be very delicate in some places, especially at the edges. If you have ever gotten a cheap tool from a flea market or dollar store that had shiny metal flaking off immediately after you bought it, that was probably the result of a poor plating job. I think that I am missing a necessary step to make a tougher finish, but it is probably not something that can be done at home.
Step 7: More Corroded Terminals
I keep finding more toys and devices with exploded batteries inside of them. In the future, I expect that this process will come in handy again.
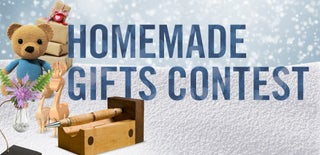
Participated in the
Homemade Gifts Contest
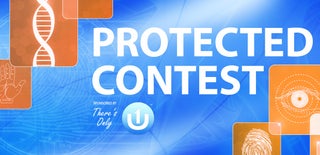
Participated in the
Protected Contest
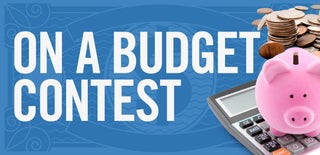
Participated in the
On a Budget Contest