Introduction: S.A.M. Spring Aided Machining (CNC With Adhesive Remover)
S.A.M. Spring Aided Machining (CNC with solvent) is a school project designed by three architecture students at CCA, San Francisco: Matt Boeddiker, Abelino Robles, and Tim Henshaw-Plath. (www.cca.edu) The machine is capable of rapidly prototyping and creating subtractive formwork that can be used to cast material. The machine was designed with the instruction of Jason Kelly Johnson, and Michael Shiloh in the Creative Architecture Machine class Fall 2013. Tecnically this is a transformative process where by material mass is maintained while volume is reduced ie a global increase in density.
Step 1: ASSEMBLE BODY
First step is to laser cut 1/4 inch acrylic frame. This should include a rigid stable truss to span width of desired length. Our width is two feet and height is about five feet.
Second step is to build basic 1/2 inch plywood frame as foundation for acrylic frame.
Third step is to attach 3/8 inch threaded rod through plywood foundation and connect to acrylic frame using laser cut acrylic pieces or simple zip ties.
Step 2: CREATE SPRING
Model a 3D spring that can be printed with PLA.
Make sure that you design a central hole that is wide enough to allow a tube that caries adhesive remover liquid to pass through.
The spring should have 4 small holes that form a square shape, north, east, and south that are used to allow threaded wire to connect spring to motor.
If access to a 3D printer is difficult, a file can be sent to the online ordering company Shapeways to print your spring. (www.shapeways.com)
Step 3: ATTACH DELIVERY SYSTEM
First step is to attach two, motors to the acrylic frame. These motors should be horizontal, and symmetrical to each other.
Second step is to attach a set of knobs to the end of each stepper motoro with a set screw. These hold the wire that pulls the spring.
The third step is to attach a DC motor peristaltic pump to the top of the acrylic frame.
The fourth step is to thread a stainless steal of plastic threaded wire from motor knob to bottom of spring. Tie and close this connection with a jewelry brad.
Fifth step it to insert 1/2 inch fuel line from pump all the way through center of spring to end tip.
Attachments
Step 4: WIRE ELECTRONICS
We use an Arduino Uno (www.ardunio.cc) and a quadstepper sheid that can be purchased from www.sparkfun.com
Step 5: WHEEL ASSEMBLY
The first step is to create a rod that can attached two beefy wheels to a motor. We used a steel 1/2 rod.
Second step is to screw a hole a the end of the rod to allow the motor to go inside the hollowed shaft. drill a hole for a set screw on the outer side of this rod to pin it to the motor.
Third step is to attach a set of metal side that pin the wheels to the rod using additional set screws.
Step 6: LIQUID CONTAINER
First step is to get a standard glass mason jar with removable screw lid.
Second step is to drill and attach a brass hose fitting to the lid.
Third step is to connect the fuel line to the brass fitting.
Step 7: UPLOAD INTELLIGENCE
First step is to upload Firefly Firmata "Quadstepper" script to Arduino Uno through USB computer connection (www.fireflyexperiments.com)
Second step is to create and load a grasshopper script through Rhino 3D. (www.rhino3d.com, www.grasshopper3d.com) This is simple to create using an evauluate curve command. Start by drawing the curve, which becomes the tool-path for the end of the spring. The change in X, and Y coordinates are translated into number of steps for each stepper motor (left stepper, right stepper, and wheel stepper motor. Use the Firefly Quadstepper Component)
Third step is to calibrate grasshopper controls with number slider to adjust how many steps are ncesessary to move in X, Y, direction. On a flat piece of paper about 16x16 inches draw out a basis grid square, and put under the spring. Slide the left x motor, see how many steps translate to 1 inch, 5 inches, and 10 inches. Then calibrate your grasshopper script by comparing how well the machine draws compared to the curve drawn in grasshopper. Draw a basic line in grasshopper to evaluate, and adjust the number of steps until the curve printed matches the curve drawn on the computer.
Step 8: LOAD MATERIALS
First step is to load rigid foam insulation board onto platform between two wheels that squeeze material to machine.
Second step is to fill mason glass container on top of machine with adhesive remover liquid. We use "Citrus Strip" Low VOC, Adhesive Remover. It can be purchased from Amazon www.amazon.com, and often found at local hardware stores.
Third step is to initiate the grasshopper firefly script to begin the milling process.
Step 9: CAST INTO MOLD
First step is to set up a working area to pour plaster.
Second step is to place a reinforcing steel rod into the center of subtracted area to be used for reinforcing purposes.
Third step is to mix plaster and water together until ready to pour, and then pour into the mold.
Fourth step is to wait until plaster has cured and can be removed from mold.
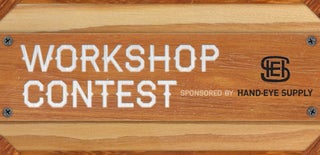
Participated in the
Workshop Contest