Introduction: Signet Ring From Nut
Late one night I had a crazy idea to make a signet ring. I had been thinking about the possibilities of making a ring from a nut, and this seemed to be the logical thing to do with it. Well, I couldn't sleep after that and I lay awake musing about how to accomplish it. I wanted to get up and go to the store and buy myself a suitable nut and get started, but alas, most stores aren't open at 2 am. Therefore, I was relegated to waiting until morning.
Since then I have collected the items necessary to make the ingenious project brewed up in the sleepless hours of the night. And I must be honest, it turned out just as cool as I imagined it late at night a couple weeks ago. My wife has taken to calling me "The Scarlet Pimpernel" because I wear it all the time now. It is comfortable and yields some great conversation.
There are a couple other instructables that have made rings from nuts that I tried to glean information from to make the project go as smoothly as possible. Those are listed below:
Daddy Daughter D6 Ring
by donedirtcheap
Remix: Metacarpal Armor
by FlatCatRussellandtheTennesseeTwo
Step 1: Materials
This was a relatively simple project.
- 3/4 nut (the size that best fit the target finger)
- Angle grinder (purchased at a friends garage sale for $25)
- Dremel (my trusty friend... seriously, if you don't have one, now is the time to invest)
- File
- Sandpaper (220, 600)
- Masking tape
- Xacto blade
- Trickle Down Charger
- Salt Water
- Q-tips
- Polyurethane
Step 2: Round Edges
This is where the sparks really fly! I started by picking what flat edge I wanted to keep. This was simple, since all 6 sides were the same, I couldn't really mess it up. Then, holding the nut with some pliers, I started the process of rounding out all the other edges with the angle grinder.
I had to prop the nut up against my work bench to do this. I would then simply use the grinder perpendicular to the nut and shape it slowly. I would periodically check the shape to make sure it was uniform. This took about 10 - 15 min.
Step 3: Angle/Shape Ring
This is where a cutting blade came in really handy. On each side of the nut I cut a gradual incline to make the band smaller at the back of the ring. Once the cut was complete I put the grinder disc back on.
I then shaped down the side to have as smooth of a bevel as possible. Then I rounded the edges to create an aesthetic and ergonomic appeal. I was cautious not to carve this down too much at this point as I still needed to shave out the threads of the nut to size it to my finger.
Step 4: Fit Ring (grind Out Threads)
Now comes the time to bust out my friend Mr. Dremel. I can't even begin to count how many projects I have used a dremel for. Using an old, duller tool I began shaving out the threads. I was surprised by how this didn't heat up the nut that much... it did, but never to the point where I couldn't hold it with my bare hands. This process took another 10 - 15 min.
I also was cautious to not shave off too much here as I would still need to sand it down. I got it to the point were it just fit tightly on my finger.
I also used the dremel to do a little more fine shaping of the ring. Particularly I focused on rounding the edges for the comfort in wearing the ring.
Step 5: Sand Smooth
While I don't have a picture of it, I started the smoothing process with a metal file. This knocked down all the rough edges left over from the grinder and the dremel that would have taken forever with just sand paper. Once that was achieved I started at it with the 220 grit sandpaper. Do as much as you can with this as the 600 grit won't get out any of the scratches. Then, using the 600 grit paper, sand it to as shiny of a polish as you can get.
I don't like my rings to be mirror smooth so I stopped here. You could get a smoother and more reflective surface if you wanted, but I was satisfied.
Step 6: Design for Imprint
I wanted the stamp of my signet to be a design of my initials. So, using the shape of the flat surface of the ring I began designing what I wanted. Once I figured out one that I liked I turned the paper over and traced the design in reverse. This is what I would then need to trace onto the ring for etching.
Step 7: Prep for Etching
With electrolysis (how I do the etching), anything that you do not want etched needs to be well covered. This can be done with nail polish, tape or any other thing that will seal off the metal. I used masking tape for this.
Placing a strip of tape onto the ring surface, I drew the reversed design onto the flat surface. Then, using and Xacto blade I carefully (and I mean carefully) cut out the design from the tape. Anywhere that metal is showing will be etched, so make sure only what you want is carved out of the tape.
Step 8: Etch Imprint
This is a fun process. I have done it a few times now, and I learn more each time. It takes some patience and caution. I think it looks more dangerous than it actually is. The fumes are probably not very good to breathe, so I usually find something to cover up my mouth.
I use a 12V trickle down charger to do this. Start by clipping the positive end to the metal to be etched. Then, dip a Q-tip into the salt water solution. Make sure it is nice and wet. Then, clip the negative end of the charger to the Q-tip making sure it is touching some of the wet part. Then touch and hold the Q-tip to the metal. The longer you hold it to the surface the deeper it will etch. Since the plan was for this to be a signet, I wanted the etching to be rather deep. I did the etching for about 5 min. in each spot going through both sides of 7 Q-tips.
Then comes that magical moment (its actually a bit nerve racking) part where you take the tape off and see if it did what you hoped it would. In my case, it did... mostly. The tape had shifted a bit in one spot, but it still looked pretty good.
Step 9: Clear Coat
To prevent any corrosion on the metal while wearing it (I woke up with a reddish brown finger after wearing it the first night) I applied a thin coat of polyurethane over the inside and outside of the ring. This should keep my finger staying the same color and the etching to stay nice and clean looking.
Step 10: Put It on and Look Awesome
This turned out just as I had imagined it late at night. It ended up working really well too.
I hope you enjoyed this and I would love to see others try it too.
If you liked it, please vote for it in the Guerrilla Design contest too.
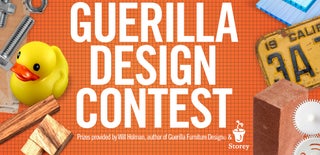
Third Prize in the
Guerilla Design Contest
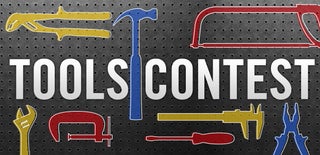
Participated in the
Tools Contest