Introduction: Simple 10w Bluetooth Portable Speaker
Hey everyone! Today I'm going to show you how I built this super simple 10 watt bluetooth speaker - an excellent companion for these summer months! I've been designing, refining, and tweaking this speaker design over the past few months, and I'm happy to say that it's now as simple, affordable, good looking and good sounding as it can possibly be! This speaker is based around a 1 cell battery, all wrapped up in a multi-layer plywood enclosure.
Specs:
- 5W output per Channel
- Bluetooth 4.0 with Qualcomm aptX codec
- Micro USB Charging
- 10 hour battery life on high volume
- (Optional) function buttons
- Dual 50mm drivers, single passive radiator design
Here's a buildlog video for the speaker. However, I go into much more detail here on Instructables than in the video.
Also, here's a sound demonstration:
Step 1: Parts List:
To make things easier, I have put together kits of the speaker parts needed, however, all the parts can also be found separately. All the parts linked are shipped internationally from Central and Western Europe so shipping times are a lot faster compared to China. Alternatively you can even just use this Instructable as inspiration/guidance if you're a more experienced builder, and find your own parts.
or
Speaker Kit with HEX Pattern Panels
and
High Quality 18650 battery (with protection) or alternatively, an old phone battery (more on this later!)
If you decide to follow the same enclosure design as I did, you will also need good quality 18mm plywood.
If you want to buy parts separately, you can get them here:
High Quality 18650 battery (with protection)
10v 1600uF capacitor (or similar)
Slide Switch
Step 2: Power! (Batteries)
Since this is a battery powered project, we're going to need a high capacity battery. Lithium ion batteries are ideal for this. We have 2 options though, since we'll only be using 1 cell. We can either...
- Use a high capacity 18650 battery
- Recycle an old phone battery, that already has a built in protection board
Both options work great, provided that we keep a few things in mind: If we're using a phone battery, we have to use one from a relatively high end/new phone, as it needs to have quite a large capacity. 1500mAh or even higher is ideal. All phone batteries from the past 10 years have a battery protection board built in to them, so we don't have to worry about adding one. Most phone batteries have 3 contact points. The positive and negative are usually marked. The middle contact is usually for transferring data, so we only have to worry about soldering wires on to the positive and negative contacts. (I would recommend using flux as the solder will stick a lot more easily, and it can be damaging to batteries if you hold a soldering iron against it for too long).
If you're using an 18650 battery (which I would recommend), try and go for a genuine cell. You can get decent genuine batteries for as little as 4 dollars per cell, or batteries with a built in protection circuit for a few dollars more. Check out the link I gave in the previous step. These cells have protection built in, so you don't have to worry about soldering on an extra battery protection board. If you're using the battery I just mentioned, or a phone battery, you can skip the 'battery protection board' step, on the schematic (in step 2). When soldering 18650 batteries, I would recommend:
- Get some sandpaper, and lightly scratch the contacts on both sides of the battery.
- Wipe down the contacts with a dry cloth (don't use your finger, as solder doesn't like finger oils!)
- Add a drop of acid based flux to the contacts
- Add solder on to the battery (try not to hold the soldering iron against the battery for too long)
- Add solder to your wire, then solder it on to your battery.
- Wipe down the contact with a damp soapy cloth to wash off the remaining flux as its mildly corrosive (be very careful not to short your battery when doing this!)
Step 3: Charging, Switch, and Stepped Up Voltage:
Charging is going to take place through a 5v micro USB charging board. You've more than likely seen these boards before. They're great. We're going to connect the wires from the protection board to the charging board (refer to the schematic in step 2). Our output wires from the charging board will also branch off to the step up module. But before they go there, we will need to add a switch so that we can turn on and off the speaker. We will solder on a slide switch on the positive cable.
The purpose of the step up module is in its name, it's used to step the voltage of the battery up, so that its the ideal voltage for the Bluetooth and amplifier board. The BT and Amp board requires 6.5 volts, so before connecting it, we will step the voltage up. This is done by twisting the blue potentiometer anti clockwise until we get the reading we are after. At this time, we will also add the capacitor to the output of the step up module. The capacitor will go across the positive and negative contacts, with the longer leg of the capacitor going to the positive contact.
Step 4: Bluetooth, Amplifier, and Speakers!
The final part of the electronics is connecting the amplifier and Bluetooth module. To start, we will connect the power to VCC (+) and GND (-) (make sure that your switch is off while soldering on wires!). Then we just need to solder on 4 wires for the speakers, 2 for each channel. [LP (+) and LN (-), RP (+) and RN (-)]. If you would like, you can also solder on function buttons to control music and volume. There are 6 contacts for these, vol+, vol-, NEXT, PREV, PLY (play/pause), and COM (common). To wire them up, you need push to make switches (included in the kits if you decide to buy them), all 5 of the other contacts connect back to COM, so that you have: wire from VOL +, goes into push to make switch), then back to COM, and repeated for the other 5. Personally I prefer having less buttons on my speaker, but it's all to do with personal preference.
Lastly we can wire up the speakers. And test it out!
Step 5: Building the Enclosure
Now that we're done with the electronics, it's time to built the enclosure! My enclosure is built 100% out of plywood. If you would like to build a similar looking enclosure, then follow these steps. Alternatively, you can skip this part of the enclosure if you have different ideas for an enclosure.
If you'd like to follow exactly how I did it, I would recommend buying a kit with the laser cut panels included. They have designs engraved into them, purely for aesthetics. These of course could also be made by hand, using a hole saw bit and a jigsaw. Alternatively, if you have access to a laser cutter yourself, you can cut my panels yourself, using these files.
The panels are 3mm thick plywood. There are 2 of them for the front and the back of the speaker. The layers that you see in between are actually the side profile of 2 sheets of 18 mm plywood, rather than layers upon layers of stacked 3mm wood. Assuming that you have the laser cut panels, or have cut the panels by hand yourself, we will move on to making the 2 ring layers that stack to make the body of the enclosure.
Step 6: Cutting the Rings
To start off, we will get a piece of 18mm plywood. It's important to use a good quality piece plywood for extra rigidity. Make sure that the plywood is straight and square on 2 sides. We will now use our 3mm plywood panels to trace out 2 shapes. Using a ruler we will retrace the shape 4mm inside of the original. The material left inside the inner line drawn will need to be taken out. Using a 16mm drill bit we will drill a hole in the corner of each traced shape (this is to match the inside radius). We can then get a jigsaw (or coping saw), and join the dots! Since I traced both shapes next to each other, I now need to separate them. I will do this using a table saw, in order to get the most accurate line possible.
Once cut out, we will have 2 rectangular shapes (with the insides cut hallowed out). We now just need to round off the sides. We can again do this using our jigsaw/coping saw. Give all the corners a very light sanding to remove any splinters.
Step 7: Glueing and Sealing the Enclosure
So now it's time to glue together the enclosure! We can just use normal wood glue for this. We'll start by glueing together the 2 rings, and then quickly move on to the back panel. We're going to leave the front open for now, as we'll need to get into the enclosure later on.. After glueing we'll then clamp it down to dry (with some paper protecting the back panel, so that we don't get glue or other contaminants on it. Since the 3 mm wood is quite flexible we'll also add some thicker sheets of ply on top of it within our clamping solution.
Wipe off any excess glue with a damp cloth, and leave it to dry for several hours.
After a few hours, we'll remove the clamps. In this next step, we're going to make sure that our glued part of our enclosure is 100% air tight. We'll do this by painting on a thick layer of glue on the inside of the enclosure. Add extra glue around the join line of the two 18mm panels, and also in any spots where the plywood might have chipped during cutting. This step is crucial as it's important to have a fully air tight enclosure when the speaker is complete. Once glued, we will leave the whole enclosure to dry overnight.
Step 8: Sanding and Finishes
Now that our enclosure is dry, its time to clean it up! We will start off by thoroughly sanding down the whole enclosure. We want our sides to be completely flush. Be sure to round the edges accurately too for best results. Once we're happy with the enclosure, we will take our front panel, and line it up with the enclosure. It's likely that our front panel will be too large to rest flush against the enclosure, so we will have to sand it down separately until its exactly the right size. It's important to get it exactly to size now, as we wont be able to sand it down later. Before we continue, we will sand the whole enclosure in very fine sand paper.
After sanding, it's time to add a finish. If you would like to paint/draw patterns on to your enclosure like I did, now is the time! I decided to colour in the laser engraved patterns using water colours. I applied a thick coat, without using too much water, which left a result where I couldn't see the wood grain through the paint. What's great about painting on laser engraved wood is that the engraved lines act like boundaries, which prevent the paint from spreading over the line, which makes painting a lot easier. I repeated on the front and back panels.
Finally it's time to apply a protective coat. I went for a polyurethane clear coat. I applied 5 layers successively to the enclosure as well as the separate front panel, and left it to try for 24 hours before lightly sanding it. Keep in mind that the procedure for applying your clear coat completely depends on the can of clear coat that you use. Following the instructions on the back of the can is always best.
Step 9: Mounting the Electronics
Now it's time to mount the electronics! We'll start with the battery. Add plenty of hot glue to the enclosure, and then stick it in place. We will then move on to glueing down the switch and charging board - probably the most difficult part of the project! It's very important to make sure that no air can escape through the either of these parts. Be clever with how you apply your hot glue, to ensure that it gets in every gap!Don't rely on your slide switch to be internally air tight. Completely glue over the whole switch and surrounding wires to make sure that absolutely no air can escape!!
Next we'll glue down the step up module and bluetooth and amp board. I decided to mount the bluetooth and amp board to the roof of the speaker, so that there would be less obstacles between the bluetooth board's antenna and the connected phone. Avoid glueing the board right next to your battery as it decreases signal strength.
Step 10: Mounting the Drivers
Last of all, we're going to mount the drivers and passive radiator. We'll start by adding a thin bead of super glue gel around the perimeter of the speaker hole. I recommend super glue gel over super glue as it stays on the surface as a semi solid substance, rather than getting absorbed into the wood straight away. Once we add our bead of glue, we'll flip over the panel, position it, and rest it on top of our driver, and hold it in place for several minutes. We'll then repeat for the other driver. After doing so, we'll use the same method to secure the passive radiator. Next we'll add a thin bead of hot glue around both the drivers and passive radiator to ensure that they are 100% sealed. Be sure not to make the bead too wide, as we need to leave room for closing the enclosure.
Before gluing down the front panel, we'll turn on the speaker to make sure that it's 100% working. Once we're sure, we'll add a thin bead of wood glue around the outer perimeter of the front panel, and then press it down on to the rest of the enclosure, followed by clamps. Make sure to remove excess glue!
Once it's sealed, it's almost finished! If we ever need to open it up again, using a scalpel, we can cut into the enclosure in between the front 18mm panel ring and front panel. Once we actually puncture the speaker with the knife, the knife will easily slide through the glue. For resealing the enclosure, firstly clean off the old glue, and then repeat the gluing process mentioned above.
Last of all, we will add 4 rubber feet to the bottom of the speaker to reduce vibrations.
Step 11: Finishing Ideas..
If you'd like to have more control over your speaker, for example add treble/bass or reduce mids, I would recommend installing an equaliser app on your phone. It works wonders! Personally I use this app. Although I'm sure that there are similar apps available on iOS.
If you think that this speaker isn't going to be big/bassy enough for your tastes, I also have a bigger speaker kit available over here, which is actually based of the speaker in my last Instructable.
Step 12: The Finished Product!
We can't end this Instructable without some end-result photos, can we? ;)
Step 13: Would You Like to See What Other Designs I Create?
Making an Instructable is a lot of work, and requires a lot of commitment to make one that is comprehensive, not misleading and engaging. Therefore I can't make Instructables for all my designs, so if you'd like to see my other speaker projects, I'd recommend giving me a follow on Facebook:
www.facebook.com/barryllewellyndesign
or on Instagram if you'd like to see lots of fun photos!
www.instagram.com/baudio_design
And of course, most importantly, if you'd like to see more of my projects explained, be sure to follow me here on Instructables!
Thanks a lot for reading, I hope you learnt something new/got some new ideas. If you've ever built a speaker, I'd love to see it! Feel free to post it down below for everyone to see! I also have a 'community speaker album' on Facebook where you can share your designs and expertise with others, and make new friends from around the world. Have a brilliant day, and I'll see you on social media/in the next Instructable! :)
If you think this Instructable is worthy of your vote in the competitions it's entered in, I would really appreciate it. Thanks! :)
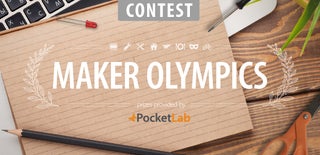
Third Prize in the
Maker Olympics Contest 2016
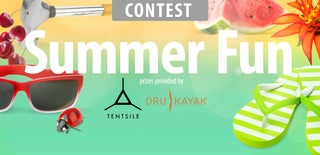
Runner Up in the
Summer Fun Contest 2016
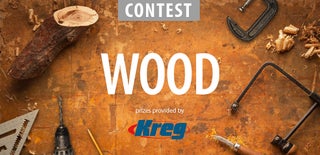
Participated in the
Wood Contest 2016