Introduction: Soft Robots: Make an Artificial Muscle Arm and Gripper
Using artificial air muscles, a very flexible robot arm and gripper can be made.
This soft robot is powered by compressed air and each one of the 11 muscles can be controlled by a standard infrared universal remote control or an infrared LED connected to a micro controller that can output Sony code.
This is a hack of silicone caulk. It is in fact mostly made of silicone caulk.
This robot was a test of hand cast, silicone based air muscles which I plan to use in an inexpensive prosthetic robot hand that I am working on. A laser cutter would be very useful to make the precision sheet plastic molds necessary to cast the hand muscles. The cutter could also be used to create the "bone" structure of the hand out of plastic or plywood.
The very short video shows the robot picking up an egg and moving it.
Step 1: How It Works
I am convinced that soft robots are the way to finally create inexpensive and flexible robots that can work well with humans. They may make possible the first really practical robots for everyday use. Soft robots use flexible materials to create the frame and actuators of the robot.
The artificial air muscles for the hand and arm are made from Oogoo, an inexpensive mix of silicone caulk and corn starch that can be cast into many shapes. For this robot, the Oogoo was cast into layers to create stacked air bladders that can be expanded or contracted with pressure or vacuum.
A standard infrared universal remote can control individual muscles or pre-programmed sequences. It does this by sending signals to an air muscle controller that is controlled by robot neurons. The air muscle controller can control up to 11 air muscles using solenoid valves and a 12 volt air compressor that provides pressure or vacuum.
This is a tethered robot that has 11 air lines connected that power the air muscles. Eventually it should be possible to fit the valves and compressor on board. A less noisy compressor could also be made.
Step 2: Materials
Materials For The Robot Arm And Gripper
Plastic grocery bag
Corn starch from grocery store
Nitrile gloves
100% silicone caulk, the type that smells like vinegar. Available from Walmart, Dollar Store, or hardware store.
1/16" sheet plastic for forms and base plate. Can be phenolic, acrylic, or any smooth sheet plastic. A good source for plastics of all kinds is usplastic: http://www.usplastic.com/
1/16" and 1/8" ID silicone hose and fittings, available from usplastic
Materials for the air controller
The air muscle controller requires various 12 volt solenoids, silicone tubing and fittings, and an air compressor. A detailed list and sources can be found here: https://www.instructables.com/id/Air-Muscles-Make-an-Artificial-Muscle-Robot-Contr/
Materials for the Robot Neurons
The robot neurons that control the solenoids that control the muscles are made using Picaxe micro controllers. A detailed list of parts and schematics and code can be found here: https://www.instructables.com/id/Tinkertrons-Make-Artificial-Neurons-For-Robots/
Step 3: Making the Artificial Air Muscles
The step 3 pic shows the 11 segments of the upper arm. The silicone tubing goes to an air chamber that constitutes one muscle. This creates four muscles that can counterbalance each other to move the arm in four directions. This was later glued to a 1/16" plastic base plate that was bolted to a large blue sheet of expanded PVC.
The second pic shows two muscle segments, top and bottom. The segments are cast in two layers with a thin sheet of polyethylene creating an air chamber that can be filled with air. A hole in the middle of each muscle chamber brings air to the chamber when all the segments are stacked and glued together.
Pic 3 shows all twenty segments of the upper arm and forearm stacked and glued and the air power lines. A 1/16" plastic plate was later glued on top with bolts protruding that allow different grippers to be bolted on.
The next step shows how the muscle segments are cast.
Other Shapes
There are probably hundreds of useful shapes of air muscles that can be cast. Here are a couple of others I have tried:
https://www.instructables.com/id/Soft-Robots-Making-Robot-Air-Muscles/
Step 4: Casting the Artificial Air Muscles
Mixing the Oogoo
A 2 to 1 mix of Silicone caulk to corn starch is mixed BY VOLUME. It sets up quickly, so it is best mixed in small batches. Typically, I would mix up 2 tablespoons of silicone to 1 tablespoon of corn starch. You can add a small dab of artists oil paint to the mix if you want colors. For more details and safety info on mixing Oogoo, see here: https://www.instructables.com/id/How-To-Make-Your-Own-Sugru-Substitute/
Casting The Artificial Muscle Segment
The second pic shows the first form which was made from two pieces of 1/16" phenolic sheet, but any sheet plastic can be used. Plywood can also be used if it is coated first with spray lacquer as a release for the Oogoo. The two pieces of phenolic have 4 bolts holding them to a plywood base.
Screeding The Segment
Pic 3 shows the screeding (smoothing and leveling) with a metal straight edge after the form was filled with white Oogoo. Filling the form must be done carefully to avoid bubbles that will leave weaknesses that can blowout under pressure.
Pic 4 shows the four polyethylene plastic pieces from a grocery bag that are used as separators to create the chambers for each muscle segment. Under pressure, the Oogoo will not stick to the polyethylene leaving a chamber to be filled with air.
Pic 5 shows the final blue layer of Oogoo that after screeding completes the cast of one muscle segment.
After the segment has set up, it is removed from the mold and a hole drilled or punched in the middle of each chamber created by the polyethylene. The center square is then cut out. This allows a space for the silicone air tubing. The segments are then glued together in a stack. Oogoo is applied carefully to the white washer around the holes. Fresh Oogoo glues old Oogoo remarkably well and fuses the silicone pieces together as if they had been cast as one piece.
Step 5: Making the Soft Robot Gripper
The first two pics show the gripper closed and open.
Pic 3 shows the 3/4" piece of plywood scrap that was cut out to create the form. Next to it is a 1/16" thick piece of plastic that was embedded in the cast to add stiffness.
Pic 4 shows the gripper finger after Oogoo casting.
pic 5 shows the bottom and top of the gripper muscle segments after the center square has been cut out and the air chambers punched out.
The finished gripper is bolted on to the plastic plate that is glued to the forearm. This gripper is far from an optimum configuration and so I made it to be easy to remove and replace with a better version.
Step 6: Artificial Muscle Air Controller
The robot air controller consists of 14 solenoid valves that can control 11 air muscles by pressure or vacuum. I originally tried using cheapo 3/16" silicone aquarium tubing for the tubes that go from the controller to the robot. Unfortunately they collapsed when under a vacuum and had to be replaced with more expensive, flexible silicone tubing. This type of tubing is translucent white and almost sticky to the touch. It has the advantage that it very flexible and it glues extremely well to Oogoo.
I have written a detailed instructable on how to make the artificial muscle controller: https://www.instructables.com/id/Air-Muscles-Make-an-Artificial-Muscle-Robot-Contr/
The solenoids are controlled by Tinkertrons which are artificial robot neurons. I have posted the details of making the neurons and the Picaxe code for this robot here: https://www.instructables.com/id/Tinkertrons-Make-Artificial-Neurons-For-Robots/
Step 7: Other Possibilities
Tether-less Autonomous Robots
This soft robot is tethered with eleven tubes to a fairly heavy controller. I am working on making much smaller and lighter valves out of Oogoo to replace the solenoids. I am also working to create a quiet air compressor that will be powered by a twelve volt gear motor. This should make possible fairly small, tether-less soft robots that are autonomous.
There are several robotic researchers who are using compressed air tanks or working to create gas generators that could be used instead of a compressor.
Adding Sensors
At this point the robot arm has no sensors for position, touch or object detection. They will be required for more precise movement. I am working on conductive silicone sensors that can be embedded in or around the artificial muscles. Here is one of my earlier experiments: https://www.instructables.com/id/Conductive-Rubber-Make-Touch-Sensitive-Robot-Skin/
"Bone" Structure
This was an experiment in an almost boneless artificial muscle structure. While it could be used to create a robot worm or snake or underwater eel, it has its limitations. In some positions, the arm is wibbly-wobbly and very difficult to control. Some kind of internal bone structure and maybe support tendons could be added to aid in achieving more precise control.
3D Printing Of Robot Muscles
The ultimate method would be to 3D print the whole soft robot structure. I am working on making a 3D printer that will print Oogoo. Until then, casting is the easiest way to go.
Future Of Soft Robots
I am convinced that soft robots are the way to go to create inexpensive and flexible robots that can work well with humans. Perhaps a combination of motors and air muscles will create affordable robots that can be more easily produced.
Spiders, snakes, squid, fish, flowers, amoebas, and never before seen forms of soft robots can be made. It is a fresh, new frontier in the field of robotics.
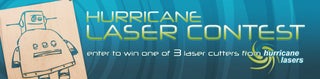
Grand Prize in the
Hurricane Lasers Contest
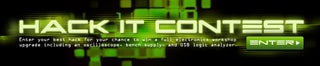
Participated in the
Hack It! Contest