Introduction: Steadycam
I've been looking at steadycams for awhile now but haven't been very keen on the price of the brand name ones. There are a few that go for a fraction of the brand name rigs but they look simple enough to make, so here we are...
Step 1: Materials List
MATERIALS:
-1 - 36" L, 1" W, 1/8" T aluminum flat stock
-gimbal handle ( I used a 1" aluminum outboard motor shaft but later found a much lighter jump rope handle with bearings already attached )
-2" L piece of 1" x 1" square aluminum tube
-1/4" drive universal/swivel socket adapter
-bearing to fit inside the gimbal handle or just find the afore mentioned jump rope handle.
-1/4" drive socket that fits tightly in gimbal bearing
-1 - 1/4"-20 x 5/16" T-nut
-1 - 1/4"-20 x 1/2" ss* carriage bolt
-3 - 1/4"-20 x 1" ss* bolts ( I used button heads but use what you have / prefer )
-3 - 1/4"-20 ss* or plastic wing nuts
-1 - 1/4"-20 ss* bolt for mounting screw ( I used a phillips pan head but suggest a thumb screw )
-2 - #10-24 x 2" ss* bolts with 2 lock washers, 2 flat nuts & 2 wing nuts each
-assortment of #10 & 1/4" ss* fender washers ( weights )
-throw away level with at least 1 good bubble vial that's between 7/8" & 1" long
* - ss = stainless steel
TOOLS:
-measuring / marking tools
-drill driver ( I recommend using a drill press for the level vial mounting holes )
-hacksaw
-files
-drill bits: 5/32, 3/16, 1/4, 5/16, 3/8 & 1/2"
-super glue
-6" diameter wheel
Step 2: Frame Construction
The first thing is to cut two sections off the flat stock, one at 5" & one at 6". Now round off both ends of the 6" bar and only one side on the 5" and the 25" bars. Drill a 1/4" hole centered, 1/2" in, on both ends of the 6" bar and on the rounded end of the 5" and 25" bars.
The next step is to cut the slots on the main frame and the gimbal mount.
For the gimbal mount you'll want to extend the hole on the rounded end to 2" long. To do this, measure in 2 3/8" from the rounded end and drill another 1/4" hole centered on the bar. Scribe a line across the center of the two holes and drill out as much material as possible with a 3/16" bit in the same fashion pictured for the main frame slot. Next, file out the remaining aluminum while testing with the carriage bolt until the bolt slides smoothly back and forth on its square shoulder. Finish it off by squaring off the two ends of the slot.
For the main frame slot, measure out 2 5/8" from the square end of the 25" bar and drill 1/4" hole centered. Then measure out 5 5/16" centered from the same end and drill a 3/16" hole. Use the same method used for cutting the gimbal slot except instead of using a 3/16" bit for the bulk removal, use a 5/32" drill bit. The end result for this slot should be a 3/16" slot, 3" long, ending with a 1/4" hole to insert the mounting screw on the back end.
To bend the main frame, place the bar flat on the 6" wheel and start the bend about an inch from the slot. Pull the bottom of the frame around the wheel past 45 degrees to allow for spring back.
Finally, after bending the frame, place the frame in a square as pictured in the final pic and mark the crest of the bend. Center your mark and drill a 1/4" hole for the front weight bolt.
Step 3: Building the Gimbal Mount Level Block
This part is simple if you have a drill press. All you're doing is drilling a through hole on the 2" long 1" x 1" square tubing. You just measure 1/2" in from one end and center your mark from top to bottom, then center punch your mark and drill through both sides of the tube. Match a drill bit to fit the vial, I don't recall the size bit I used but you can easily check by drilling a scrap piece and checking the fit. The vial should go in easily with no play in the holes.
Dry fit your vial and check it for level by placing it flat on a checked and leveled surface. If your drill press is trued, the vial should read level. If all checks fine, just add a bit of super glue to both ends of the vial from the outside of the tube and you're done with this step.
You don't have to install the level on this part and just eyeball it when adjusting the rig, but I had the throw away level and the drill press handy so I went with it.
Step 4: The Homemade Camera Mounting Screw
For the mounting screw, I modified a 2 1/2" long 1/4-20 pan head from my stainless bin.
The first thing i did was chuck the screw onto my drill. I started by filing about an 1/8" of the screw down to a 3/16" diameter against the head. To do this evenly, I slowly spun the drill while filing the screw. This is the only other way I know of turning metal outside of a proper lathe, which I don't have.
To cut it down to size, I cut half the threads of the screw off so that I could re-chuck the screw on my drill deep enough to get my desired length of four threads. I chucked the shortened screw so that the fifth thread of the screw was just on the jaws of the chuck. Again, I spun the drill slowly while this time using a hacksaw to cut along the fifth thread using the jaws as a guide.
Disclaimer: This method is not intended to be instructional. It is an improvised method that could prove dangerous. I am merely showing how I did it. I take no responsibility for your actions.
Step 5: The Gimbal
Unfortunately, for this step I'm revisiting my first attempt at making this rig so this is just a recap of a finished piece. I have since found a jump rope from "everlast" called a speed rope that would eliminate the need to source out a bearing and fit it to the handle material.
The first thing I did here was to make the swivel/Universal piece. For this I drilled out the female end of the adapter to 5/16". Next, I flattened out the barbs on a 1/4-20 x 5/16" t-nut and pushed, hammered and beat it into the hole. ( If you find an easier alternative please post it in the comments.) Finally, grind or file the edges of the t-nut flush with the adapter and that's it, really!
For the handle, I suggest finding the previously mentioned speed rope at a discount retailer or a thrift shop if you're lucky. The handle on mine is from a motor guide outboard motor shaft ( 1" -thick wall pipe ), the end cap, also 1", is from a discarded lap bar on an amusement ride and I believe the bearing is a 6202, not sure. I had to hone out one end of the pipe to fit the bearing and pressed it in with a bit of bearing retaining compound. To connect the handle to the adapter simply find a 1/4" drive socket that fits snugly into the inner race of the bearing and carefully glue it in. In my case, it was a 7mm socket that I had to grind down slightly to fit the bearing.
Once done, you end up with an easily removable handle that can be adapted to fit other mounts where the rig might come in handy.
Step 6: Assembly
To start assembly you'll want to clamp the main frame, level block and the gimbal bracket together in that order with the block and bracket towards the bend side of the main frame. Make sure that everything is flush, straight and well clamped. Mark two hole locations about 1" apart and centered on the main frame making sure to avoid the bubble vial. Lightly center punch them and drill them out to 3/16" all the way through the three pieces on your drill press. Install and tighten the #10-24 bolts with a locknut or a flat nut with a lock washer but do not cut off the excess threads, they will be used to add weights for balancing the rig.
Next install the 6" bar to the bottom of the main frame with the 1" bolt and wing nut with two more 1/4-20 bolts and flat nuts or wing nuts for the counter weights on the crest of the bend and the bottom hole on the 6" bar. Don't worry too much about reducing the weight of the bar at this point. It is easily removed and just as easily replaceable if damaged.
Finally you install the gimbal. insert the carriage bolt down into the gimbal bracket slot, add a 1/4" lock washer to the opposite side of the bracket and screw on the t-nut side of the swivel/universal adapter hand tight.
The camera mounting screw just goes into the 1/4" hole of the main frame slot and is slid forward. Read my notes on the pics for a revision on the slot.
Step 7: Finished
It's not 100% but as far as construction it's done. I'll clean and paint once time permits and post a video of it in action soon. To learn how to balance the rig I suggest going to YouTube and searching the topic. This is my first experience with a finished steadycam so I'm not fully versed on properly balancing it. If there's anything you think I can improve please comment, this build was done with no plans or measurements and almost no knowledge of the rig itself. I hope you enjoyed it.
Winning the Shop Bot would mean I would have more time for documenting my instructables.
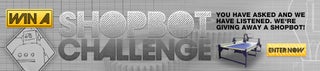
Participated in the
ShopBot Challenge