Introduction: Steel and 2x4 Full Dining Table Set
Welcome to my first Instructable, and thank you for taking a look!
This dining table set was made primarily of steel square tubing, some left over steel flat stock I had on hand, and dimensional pine lumber. It has been serving me well for the last 6 months and has made a great addition to my home.
Even better, I saved a ton of money by spending a few days to make it myself. Enjoy!
Step 1: Buy the Lumber First!
To make the table, chairs, and bench tops, I purchased dimensional lumber from a local big box store.
17 - 2"x4"x8'
Take time to choose the straightest pieces with the least amount of knots, bring the lumber home, and WAIT.
Dimensional lumber from big box stores has a tremendous amount of moisture still locked inside of it. Lumber needs to acclimate to the moisture levels of your home or workshop. I recommend 1 week minimum, and the longer the better.
Step 2: Prepare the Steel
7pcs - 2"x2"x8' .063" steel square tube
1pc - 2"x1/8" steel flat stock
1pc - 1"x1/8" steel flat stock
The steel can be bought at home supply centers, but it is substantially cheaper at local metal supply depots. I look out for the pieces with rust. It does require a bit of clean up but my local metal supply gives a discount for buying rusty metal. Cleaning the rust was done with a 4.5" grinder and flap discs and sanding discs. I find that grinding the steel before cutting is easier.
Cut List:
Using a grinder with a cut off wheel, a band saw, chop saw, or even a metal cutting hand saw, make the following cuts on the square tube.
Table Legs:
4 vertical legs @ 26.5"
4 horizontal cross members @ 20"
2 truss-like pieces going towards center of table @ 22"
Bench Legs:
4 vertical legs @ 16"
4 horizontal cross members @ 10"
2 truss-like pieces going towards center of bench @ 12"
Chairs:
4 front legs @ 16"
4 rear legs @ 30"
2" Flat Stock End Caps:
20 - 2"x2" Squares, 16 of which will be drilled in the center with a 1/2" bit
1" Flat Stock Chair Tabs:
16 - 1"x2" rectangles with two 3/16" holes drilled into their center line
(Take a look at the 3rd photo here to see what I mean)
Step 3: Adding an Angle to the Back of the Chairs
I cut a "V" onto the rear chair legs to give it a slight angle so that I can lean back comfortably as I sit.
I measured 18" up from the bottom, marked a line perpendicular to the pipe, and then marked a line 10° from that.
Use an angle grinder to cut a wedge out on 3 sides of the square tube.
As you can see in the photo, I clamped the long end of the leg to my work table, and used some scraps to prop up the short end. This closes the gap created by the wedge I cut out, and now it's ready to weld.
Step 4: Time to Weld!
No action shots of welding (sorry! I got a tripod AFTER this build).
I used Lincoln 180HD GMAW welder. SMAW and GTAW will work too. Use what you can get your hands on!
Table Legs and Bench Legs:
Weld up the Horizontal cross members to the Vertical legs to form a rectangle as shown in the pictures. Once you have a rectangle, weld the 22" length for the table, and 12" length for the bench, perpendicularly to the center of the top horizontal cross member. (The third photo shows one bench leg and one table leg.)
Chair Legs:
Weld together the cuts made in the previous step on the rear legs to give the back of the chair a slight angle.
Weld end caps to the tops and bottoms of all rear legs, and the bottoms of the front legs
Weld on the 2"x1" tabs perpendicularly to the 2 sides of the front legs, and perpendicularly to the 2 sides of the rear legs. Since the front legs are 16" tall, the tabs on the rear legs go 16" from the bottom. I skipped ahead a bit and included an assembled photo of these tabs. Refer to the last photo in this step.
Adjustable Table / Chair / Bench Feet:
(not shown) Weld a 1/2" nut to the inside of the 2"x2" end caps that were cut out and drilled through earlier. These will hold the table and chair feet in place.
Tack weld a 1/2" washer to a 1/2" carriage bolt as shown in photos 5 and 6. These feet will be screwed into the end caps later.
Weld the 2" end caps to the bottoms of all chair and table legs.
Finishing:
After all welds were made, I went back through all of the pieces with an angle grinder and flap disc to smooth out any sharp edges and corners. I also gave the tubing a final sanding, cleaned it with alcohol, went over it again with a tack cloth, and applied a few coats of flat black spray paint.
Step 5: And Now Back to the Lumber
I purchased 17 - 2"x4"x8' pieces of pine and ended up using 16.
To begin with, I ran all of the pieces through my table saw, taking 1/4" from the short sides of each board, leaving me with 3" wide boards. This was done to remove any surface imperfections, straighten the boards out, and remove the rounded edges.
Next, I used a pocket hole jig and wood glue to attach the full length boards to each other. The screws went in about every 6" or so. Having since learned more about the actual strength of wood glue on a long grain, I would not do so many screws. In future projects, I plan on using glue only with either dowels or biscuits for alignment.
I started with 2 sets of 2 boards each, and 3 sets of 3 boards each. The idea was to leave them under 12.5" wide so they would fit in my thickness planer.
After allowing the glue to set overnight, I ran all of the new boards through my thickness planer to get the tops nice and smooth. Using the same gluing and pocket hole screw method, I attached one set of 2 boards to a set of 3 boards for the bench and chair back, and 3+3+3+2 for the table top and chair bottoms. Photos 3 and 4 show the underside of the completed table top.
Remember, everything is still in 8 foot lengths.
Step 6: Cut It Down to Size
After all of that gluing and screwing together, what I have is 1 board that measures 8ft x 15in and another that measures 8ft x 33in.
Table Top and Chair Bottoms:
Cut down the table top from 8' to 6'. The 6'x33" piece will be the final table top size.
Take the remaining 2' section and cut it down to two 18"x18" squares. Then, cut out two 2"x2" squares from the two rear corners. These cut outs will accommodate the rear table legs.
Bench Top and Chair Backs:
Cut down the bench top from 8' to 5.5'. This will be the final dimension for the bench top.
Take the 2.5' cut off piece and cut out two pieces measuring 14"x6". These will be the chair backs.
(Pictured in this step are the seat bottoms and seat backs.)
Step 7: Assembly Time
Table Top / Bench Top:
I began by laying the table top on the floor upside down and centering the 2 sets of legs on top of it.
After making sure that the legs were evenly spaced from the edges, I drilled 5 holes into the center truss only and drove in 3" long screws.
I repeated the process for the bench, but used 4 holes instead of 5.
Feet:
Be sure to screw in those sixteen 1/2" feet to their end caps before turning the table over (photo 5)!
Chair:
I placed the chair bottom on top of the table (once I flipped the table right side up) and used 1" screws to attach two front legs directly to the underside of the chair bottom.
I then placed the rear legs into their cut outs and screwed them in as well.
(not shown) I drilled 4 pockets holes pointing outwards on each corner of the chair back and used self tapping sheet metal screws to attach the chair backs to the rear legs.
Step 8: Finishing
I applied several coats of butcher block oil to all wood surfaces, waiting 6-8 hours between coats, allowed them to cure, and set my table.
Step 9: Questions / Comments
Thank you for reading through my first ever Instructable!
Any questions or comments to make future ones even better are much appreciated!
Check me out!
http://mothlightcopperworks.com/
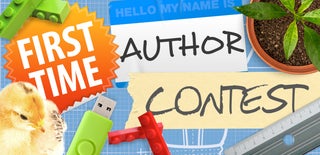
Runner Up in the
First Time Author Contest