Introduction: Stitch and Glue Boat Construction
The "Stitch and Glue" method of boat construction is one of the most popular methods of plywood boat construction today. It allows for easy test fits, fast assembly, and simple fixes. I recently modified the Mini-Cup Sailboat plans, normally calling for assembly with wooden stringers, to stitch and glue.
I apologize for the lack of some crucial photos, as once the process is started and the gloves are on, the epoxy usually gets everywhere so I try to limit my camera's exposure to it.
Step 1: Tools and Materials
Epoxy brush
Sharp scissors
Saw
Drill
Drillbits
Latex gloves
Plastic scraper
Materials:
Epoxy resin (marine-grade)
Zip/cable/wire-ties
Fiberglass tape (11.1 Oz best for structural, bi-directional not necessary)
Most of these materials can be purchased at a marine supply store.
Step 2: Cut It Out
First you need to have your parts to be stitched and glued cut out. For my boat's 1/4 inch plywood hull, I used a Jigsaw to cut out the pieces I had lofted from the plans.
If your pieces are joined at odd angles, you can choose to cut the pieces out at an angle, or just use a file to shape it later.
Step 3: Drill Some Holes
Depending on the amount of curve in the pieces you're stitching, drill holes that will accommodate your Zip-ties anywhere from 3" apart to 6" apart, about 1/4" to 1/2" in from one of the piece's edges to be joined. This definitely does not have to be exact.
Now mock up the two edges to be joined, the one with holes in it and the one without. Try to clamp it as best you can for at least a few feet, especially if it's curved. Then, drill holes in the untouched piece that line up with the holes in the other piece. Again, this really does not have to be exact.
Step 4: Tie It Up
Now start loosely attaching Zip ties through every set of holes. Start tightening them evenly from the middle outwards, until you have it exactly how you'd like it to stay, forever.
You should consider which side of the joint the locking part will be on. If you can access both sides when everything's in place, make the locks on the part that will not be taped, so you can take them off later.
Note about alternate "stitch" methods:
Though traditionally the stitch in stitch and glue has been copper wire, I find cable ties to be better for a few reasons. Mainly, they are easier to tighten and remove (in some instances), and they have a safety feature integrated into them in the sense that they usually break before the wood breaks in the event of over-tightening. However, it should be noted that the advantages of copper wire are that it can be completely removed from epoxy if already covered in it by simply heating it up and pulling it out, and also wire is stronger and normally skinnier than cable ties, which allows for a closer bond, which is especially helpful in tight curves, and a smaller hole drilled into the hull. Copper wire has to usually be cut to length as well, whereas cable ties are pre-cut, and have to be tightened either painfully by hand or with a pliers which can be cumbersome.
Step 5: Joint Specific Instructions
There are a few things you need to worry about if you're gluing an "inside" edge, where the tape will be folded inwards. In order to have a strong bond, you need to create a rounded epoxy fillet to fill the corner. Thicken some epoxy to the consistency of peanut butter, and apply the rounded fillet using a popsicle stick evenly throughout the joint. You can leave the ties in, as long as the locking part is on the outside, where it can be removed later.
If you have to glue on the same side that the locking part of the tie is on, then apply "welds" of rounded, thickended epoxy in between the ties, let it dry, remove the ties, and then fill in the gaps with rounded fillets. Be sure to sand the epoxy before you apply the tape if it has dried.
If you're working on an "outside" edge, and you have access to the inside, then go through with the same rounded fillet of epoxy on the inside, and just go over the ties. Once it's dry, you can remove the bulky locking portions on the outside, and continue.
If you're working on an outside edge and do not have access to the inside, then you're in a sticky situation. Your best bet is to space the edges using 1/4 or 1/8 inch dowel inside the loops of cable tie, so that you can then apply thickened epoxy inside of the joint as "welds" in between the ties. Once it dries, remove the ties, fill in the rest of the joint with thickened epoxy, and continue.
Note that before thickened epoxy is ever applied, you should first "wet out" the surface with epoxy by coating the area in unthickened epoxy. Use your epoxy brush to evenly coat the surface, and don't worry about getting it on the cable-ties.
Step 6: Start Taping
After you've got your joint somewhat solidified with a weld of thickened epoxy, you can remove the cable ties. you may need to cut them, but just get out what you can, and don't tape over the locking part. Sand the area smooth (and rounded if an outside edge) so that it's ready for epoxy.
If your joint required you to "weld" it together so that you could take out the cable ties (especially the locking part), make sure to sand the area roughly before you start to apply the tape. Epoxy generally does not stick to itself very well. Remember to wet out the surface once again if you've had to wait for the first coat to dry.
If the joint is all ready and set, cut a length of fiberglass tape to fit the joint. You can leave about a quarter inch of extra on each side if you want, but for inside joints especially it's best to cut it exactly. Roughly pat down the tape to the wet epoxy surface, and then starting at one end with a fresh batch of unthickened epoxy, brush on epoxy until the tape becomes relatively clear. You may need to finesse the bubbles out with a finger, but generally fiberglass tape is pretty easy to get right.
Use a plastic scraper to help you get out any bubbles and to spread the epoxy along evenly. Generally I'll wet out around a 1 foot section with a brush first, and then get another foot out of it using the plastic scraper. You just want the fiberglass tape to be impregnated in epoxy, not necessarily coated. A thin layer of epoxy is flexible, and the fiberglass gives it the tensile strength it needs, whereas a thick layer of epoxy is more likely to crack.
If you're going around curves, you may need to "kerf" the tape around the edge by making a few 1' cuts into the tape along the inside and outside radius of the curve. The tape stretches pretty well though, and try pulling on the ends of the tape before you make any cuts, which decrease the strength of the joint.
Step 7: Drying and Finishing
Follow the epoxy's instructions on drying time and curing (generally 6-12 hours to touch). Try to keep dust and insects off of it in the meantime.
If you're okay with the slightly raised and bumpy texture of the fiberglass tape, you can cover the seam in a polypropylene drop cloth, which doesn't stick to the epoxy and will create a nice and smooth surface.
If you want it to be smoother, then suit up in a jumper or long sleeves and pants (with legs and arms taped) and sand it out. Fiberglass gets everywhere, so to avoid itching for weeks, do everything you can to keep dust from flying around.
If your joint needs to be super strong, then do a few more seams of tape overlapping the original seam. This is common on large boats (20 ft+).
Step 8: Epilogue: Mini-Cup Mods and Suggestions
I made a few modifications to the original plans. For one, Instead of having stringers and screws fastening each piece of plywood, I use the stitch-and-glue method outlined here. I also rotated the original cockpit dimensions so that the rounded end was towards the stern. Additionally, I placed deckplates in the cockpit for access to the five watertight compartments. In the two foreward compartments I added two non-watertight bulkheads at the fore end of the daggerboard box to stop any cargo in those compartments from sliding around too much. I also added an additional support beam at the top of the stern between the rear bulkhead and transom. I coated the entire hull, inside and out, in epoxy for longevity.
In terms of the rigging, I kept the general rig dimensions, but added outhaul, downhaul, and traveller lines feeding into clam cleats at the cockpit. The spars are 1.25 in aluminum T6 tubing and the mast is a 2.25 in alumunim T6 pipe. I made the sail with a sail-making neighbor of mine, and it is based of off the given dimensions with the shape "eyeballed". The The mainsheet goes through a swiveling fairlead and cam cleat located directly aft the daggerboard, with an accompanying block directly above on the boom. I may try and make a higher performance sloop rig; I'm not sure the lateen rig does it justice.
On deck, I added a cleat and set of chocks at the bow and an additional cleat as a handle on the daggerboard. I put an adjustable hiking strap in the center of the cockpit at the floor, which certainly sees use. The hull's nearly flat-bottomed design means that in the water, the Mini-Cup likes to be sailed flat, and tends to turn into the wind with even small angles of heel.
Attachments
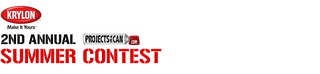
Participated in the
2nd Annual Krylon Summer Contest
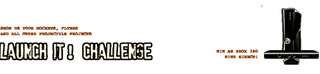
Participated in the
Launch It! Challenge
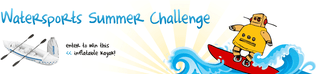
Participated in the
Watersports Summer Challenge