Introduction: Engraved Stone Rune Set and Decorated Storage Box
INTRODUCTION
The object of this “Instructables” project is to make a set of stone runes, (stones engraved with rune glyphs), and a wooden display/storage box decorated with ancient Norse and Celtic designs to store and display the runes. While this project employs techniques to create a specific end result, you'll see that many, many variations in materials and techniques are possible. I'll describe it in terms of what I did to produce it. You can decide if that way works for you or if you can accomplish these steps in a better or more convenient way for your situation and the tools you have. I will provide links for information on where to get the parts I used. Above are some pictures of the finished product.
DISCLAIMER: Throughout the following instructions I provide web links to where information and parts to make this project can be obtained. Some of these parts and information need to be purchased. I include these links only to provide the reader with a way to obtain the parts and information as I did. These parts and information may be available at other websites or stores or mail order businesses. I do not receive any benefit, financial or otherwise, from the purchase of any parts or information described in these instructions, with one exception. When I made this rune set and display box, I made only one. While I, or anyone following these instructions, could make additional ones, or variations of this one, I have not chosen to do so at this time. While I may decide to make more of them in the future, this one is for sale today, 10/13/18, at my Vintage Imaging website. You can visit, and maybe purchase, it at Rune Set and Display Chest.
Step 1: Background
First a little background on runes, what they are and why anyone would want to make a set of engraved runes. The sources of this information include: “runes” on Wikipedia at http://en.wikipedia.org/wiki/Runes, www.sunnyway.com/runes/, and information from an e-book by Mr. Bob Oswald, AKA The Runemaker.
"Runes . . .are the letters in a set of related alphabets known as runic alphabets, which were used to write various Germanic languages before the adoption of the Latin alphabet and for specialized purposes thereafter. They were used throughout northern Europe, Scandinavia, the British Isles, and Iceland from about 100 B.C.E. to 1600 C.E. Runic inscriptions of great age have even been found in North America, supporting stories that the Vikings arrived in the Americas long before Columbus. Runes have been used in Britain since the Dark Ages. When the Romans abandoned Britain around 450AD, waves of immigrants from Europe came and settled there. The Friesians from the Netherlands, the Angles and Saxons from Germany, then the Jutes and Norsemen (Vikings) from Scandinavia. They brought with them their set of ancient symbols known as the runes.
Originally, the Scandinavian variants had 24 runes. They are collectively known as "the Elder Futhark". The name is derived from the first six letters of the alphabet (F, U, Þ, A, R, and K). Other variants of runic alphabets evolved later.
Since ancient times people have used runes for writing messages, inscriptions and epitaphs; as amulets and charms; as well as an oracle for use in divination; and for rituals, magic and spells. The word "rune" actually means mystery, secret or whisper. Each rune has esoteric meanings and properties associated with it, beyond its mundane meaning and phonetic value.
The runes all have names that were significant to the ancient Germanic tribes, Norsemen and Anglo-Saxon pagans who used them. Each translates into a word or a phrase signifying concepts important to these early peoples, representing the forces of nature and mind.
Each rune has a story attached to it, a relationship to a Norse god. Some were named for gods, like Ing and Tiw; some for animals and plants such as the Ox or a Birch twig; some for natural features - a lake, or hail; some for everyday objects that they used like a carriage and an archer's bow; and some for timeless concepts such as joy, a gift, and humanity. The rune meanings are augmented by further interpretations for their orientation when viewed at a given moment such as upright as written like a letter, reverse (upside down) and converse (face down) presentation. The runes are also each traditionally associated with gemstones or crystals, trees, plants or herbs, colors, and the elements.
Runes are sometimes used as an oracle from which one seeks advice. This “runic divination” or "rune casting" is not "fortunetelling" in the sense that one actually sees the future. Instead, runes give one a means of analyzing the path that one is on and a likely outcome.
For more information on runes, rune casting and a lot of other runic stuff, visit these websites:
http://en.wikipedia.org/wiki/Runes
www.sunnyway.com/runes/ and information from an e-book by Mr. Bob Oswald, AKA The Runemaker.
This project creates a set of runes, engraved on stones, from the Elder FUTHARK. The picture above shows what the runes, or glyphs, look like and their names. You'll notice that although there are 24 letters, or runes, in the Elder Futharc there is a 25th space shown, the “Blank”. Some people consider this a 25th rune but more traditional runeologists consider it only a spare in case one of the other runes is lost. I include it here more because it seemed easier to make a 5 x 5 container than a 6 x 4, or other spaced box.
Step 2: Acquire the Stones and Prepare the Rune Glyphs
The stones I selected to have the rune glyphs engraved on are jet black, highly polished, stones 2 to 2.5 inches across. These are absolutely gorgeous pieces of stone. They were purchased at the website:
http://www.stonedecorative.com, and look like the first picture above.
The website describes these stones as: STONES FOR ENGRAVERS, a unique collection of polished, smooth natural stones. Beautiful in any color, these hand-selected stones are available in various sizes. Their almost uniform shape and non-porous texture will enhance any artwork … an engraver’s dream canvas! Ideal for laser engraving, sand-blasting, calligraphy, and even printing. They are sold in 22-lb bags.
While the website does not state what specific type of stone these are, I believe they are some form of basalt. This is because they are black, fine grained, and have a hardness in the range of basalt based on the Mohs scale of mineral hardness. They are available at this website in 3 different sizes. The stones used in this project are the middle size which is called “small”.
The Rune Images (Glyphs)
All the graphic layout for this project, the rune glyphs, the box decorations, and divider design is done using CorelDraw and CorelPaint X5 graphics software. Other graphics programs will work as well as long as you can output to a printer. The rune images, or glyphs, themselves are created from one of several rune fonts obtainable from web stores on the internet. Simply install the downloaded rune font purchased from a website and then install it to Corel and create a text entity in Corel with the mapped letters. Of course, as an alternative you can draw each rune glyph with the graphics tools in the software but I found it easier to buy the font set.
The second picture above is of the rune glyphs as they will be engraved, each one on an individual stone. You may notice the rune images shown in this picture are not in the order of the FUTHARK but instead in order of our western alphabet, a, b c, etc. This is just for convenience while laying them out to ensure I didn't overlook any. They will each be engraved to a separate stone and re-ordered in the storage box.
Step 3: Engrave the Rune Glyphs on the Stones
Laser engraving, such as with an Epilog Laser Engraver, Sandblasting, (or sandcarving as some people call it), or hand carving with a Dremel type rotary tool are all usable techniques to do the rune image engraving on the stones. Since hand carving can be error prone and very difficult to achieve a professional look and because I do not have a laser engraver, I selected sandblasting. The pictures above show my sandblaster including the compressor, blast cabinet, and dust vacuum.
While the details of how to sandblast are beyond the scope of this Instructable Project, discussion of a few points will be helpful. I use the dry masking system called RapidMask from IKONICS Imaging. See https://ikonicsimaging.com/films/rapidmask-sheets.html.
As the website states, it is the only dry processing, self adhesive, photoresist film on the market today that requires no washout. There are two types of RapidMask, RapidMask High Detail and RapidMask High Tack. These two versions of the RapidMask product have different thicknesses and are used for different types of sandblasting. With fine detail halftone making ability and strong blast resistance, the combination of RapidMask High Detail and RapidMask High Tack provide an effortless sandblasting experience. For this project I used the RapidMask High Tack product. As I will discuss later, after engraving the rune image, the engraving is color filled to enhance the contrast and perception of the rune. The masking system provides another advantage in that before the post-blast remaining mask is removed, it acts as an ideal mask for the color filling.
Laser engraving the rune images on the stones could also produce a great look without the tedium of managing a masking system. The graphics would be laid out with the same software and engraved directly on the stone. A possible color fill masking strategy in this approach would be to use another product from IKONICS Imaging called Laser Tape. While intended to combine the convenience of a laser engraver with the look of sandcarving by using a laser engraver to make blasting masks, IKONICS Imaging Laser Tape can be used to cutout a color fill mask before laser engraving the rune image on the stone.
Step 4: Color Fill the Engraved Rune Glyphs
After the rune image is sandcarved on its stone, but before removing the remaining blast mask the rune is color filled. The RapidMask makes an ideal mask for the color filling. With a fine model paint brush apply a coat of brass colored Model Master Acryl model paint to the blasted area of the stone. The paint should be available in hobby stores. Obviously, any color paint can be used but the brass color shows very nicely against the black stone.
Let the paint dry for about an hour to an hour and a half and then carefully remove the blast mask. This timing is important because if the mask is removed too soon the paint may drip or smear. If the paint is allowed to dry too long the mask may pull the layer of paint off the stone when it is removed. After the blast mask is removed, let the paint dry thoroughly. Depending on how the paint covers, a second coat or touch-up may be necessary after the mask is removed and the color fill has dried. After doing any necessary second coats or touch-ups of the color fill paint, let the paint thoroughly dry. I let it dry over night. Any additional paint outside the sandcarved area of the stone can be carefully removed with a razor blade paint scraper. Above are several pictures of some of the runes after being blasted and color filled prior to the removal of the blast masks.
Step 5: Acquire the Display Box
The wooden display box was purchased, unfinished, from DesignCraft Industries at: www.designcraftindustries.com/. As you can see on this website, they have many unfinished box designs with various dimensions, lid, hinge, and latch arrangements. They are available in Oak, Maple, Cherry, and Poplar.
Because of the size and number of compartments I wanted for the individual rune stones, I needed a box that had outside dimensions of 13 x 13 x 3 and inside dimensions of 12.25 x 12 .25 x 2.25 (with the lid on). This is not one of the standard sizes made by DesignCraft. So I ordered a custom box with the dimensions that were needed. To order a custom size box you'll need to use the “Contact Us” link to ask for a quote for a box with custom dimensions. The folks at DesignCraft were very responsive and helpful. I selected oak for the material and a recessed lift off lid with no hinges or latches. This design would also work fine with hinges and/or latches if preferred but with a lift off lid ask for the interlocking lip between the box and the lid to be 1/2" so the lid stays on more securely. If you plan on putting on your own hinges ask for the interlocking lip between the box and the lid to be 1/4".
DesignCraft does not sell compartment dividers for the boxes so I'll describe how to make them later. The box will be finished with an acrylic spray after the decorations are applied.
Step 6: Select and Prepare Decorations for the Display Box
Decorating the box provides the opportunity to really get creative with its appearance. While many variations are possible, I chose to use ancient Norse and Celtic patterns as well as my own designs which were laid out in CorelDraw. The ancient Norse and Celtic patterns were obtained from Dover Publications, Inc., of Mineola, New York. Dover produces many electronic clipart books with accompanying CD-ROMs containing the clipart images. I used “Celtic and Norse Designs” which contains 221 royalty-free designs, 48 of them in color. Dover states that they were “...meticulously adapted from artwork that once decorated ancient rune stones, furniture, sword hilts, and other Celtic and Old Norse artifacts...”. Dover can be located at www.doverpublications.com.
I chose to decorate the exterior and interior of the lid. I also placed a label on the exterior of the bottom of the box identifying myself as the maker.
(NOTE TO READER: If the pictures in this step show only partial views of the images referred to, just click on each picture to see it fully displayed or to cycle through all the pictures of this step in sequence.)
The center of the lid interior is dominated with the image in picture #1 which is not from the Dover source but is an image I created with the rune fonts and the CorelDraw graphics software. In addition to being colorful, it is intended to be informative in that it is a key to the position and names of the various runes in the box. The color of each rune in this image is the color associated with that rune.
Picture #2 above is image number 037 from the “Celtic and Norse” Designs Book/CD-ROM from Dover. Four (4) copies of it are used, one at each corner of the interior of the lid.
Picture #3 above is image number 040 from the “Celtic and Norse” Designs Book/CD-ROM from Dover. The perimeter of the interior of the lid uses 4 copies of this image.
So the decorated interior of the lid is shown in Pictures #4, #5, and #6.
Picture #7 above shows the basis for the image that dominates the center of the exterior of the lid. It is image number 209 from the “Celtic and Norse” Designs Book/CD-ROM from Dover, which I colored using the CorelDraw software to look like Picture #8. In addition to the central image on the outside of the lid, 4 smaller copies of the image in Picture #8 are positioned one at each corner of the exterior of the lid.
The perimeter of the outside of the lid is made up of 4 copies of the image in Picture #9. It is built-up from several images including number 155 from the “Celtic and Norse” Designs Book/CD-ROM from Dover, shown here in Picture #10, and the cropped off outer edges of image number 040 from the “Celtic and Norse” Designs Book/CD-ROM, and then all are colored purple, with a black pen outline, using the CorelDraw software.
The last piece of design on the exterior of the lid is actually based on a wrought iron type design that is included with Corel, what Corel calls Content. The file name is CGS12660 and it looks like Picture #11. The color is changed in Corel to red. The pattern is Corel “traced” and a non-zero edge pen weight is applied with the color black giving it the final look seen in Picture #12. Four copies of this are placed at the corners of the large central figure on the exterior of the lid. The decorated exterior of the lid is shown in Picture #13.
Finally, the. label on the exterior of the bottom of the box, identifying myself as the maker, was created using CorelDraw and includes my contact information and a graphic symbolizing my Sandcarving hobby. It is shown in Picture #14 and as applied to the box in Picture #15.
Step 7: Apply the Decorative Images to the Box
All the decorative images we just discussed are applied to the box using WATER-SLIDE DECALS. These are sold as blank decal sheets at places like https://www.amazon.com/Blinggasm-Waterslide-8-5X11-Inch-Inkjet-Printer/dp/B00ZLVF6AC on Amazon. Images you want to apply are imported to your computer (or imported and modified as I did with the images from Dover) and then printed to this blank decal paper. Alternatively, you can create your own designs from scratch using a graphics program like Corel and then print them to the blank decal paper. I did this with the large central image on the inside of the lid and on the makers identification label on the bottom.
There are 2 different types of blank decal paper. One for inkjet and another for laser printers and they are available in clear or white. Although I used the clear laser printer type the process for inkjet paper is very similar with certain differences. Read the instructions and limitations on the DecalPaper website for the type of blank decal paper you plan to use. Below is a paraphrased excerpt from the website on how to use the decal paper for laser printers.
“Create your own decals with this high quality, inexpensive water-slide decal paper for laser printers. This paper can be used with most laser printers, ALPS printers and color copiers. It is recommended to test a couple of sheets with your printer or copier to ensure compatibility prior to producing multiple copies.
The main use of this paper is for creating transfers decals for various uses such as: model trains, planes, cars, soap, candles, wood, furniture, plaques, plastic objects, computer frames, cardboard, ceramic, glass, enamel, metal plus other surfaces.
Copy any pre-printed design or create your own artwork with ink and paper or a computer drawing onto the blank, water-slide decal paper using an office copier, laser printer or ALPS printer.
How to print:
1. Begin by printing your image(s) from your computer onto your laser printer, color copier or ALPS printer with the use of BEL INC blank laser printer (decal paper).
2. Print on the glossy side of the blank paper. If you have purchased soap paper or candle decal paper, your paper will have a plastic film to protect the sheets. Remove this film before placing it into the printer. The blank decal paper I used had a protective, tissue paper, sheet that had to be removed before printing. Note: You should feed your printer one sheet at a time to avoid jamming the printer since this paper is thicker than regular paper. If you take it to a copy center, instruct the operator to feed the sheets one by one to the copy machine.
3. Allow the ink to dry and set into the paper for at least five minutes and it should be ready for application.
4. Cut out the image(s) as close as possible to the actual design and place them in lukewarm water for approximately 30 seconds. Hold the decal carefully to avoid tearing. You will begin to feel the printed image start to slide off the white backing paper. This means it is ready to apply onto your surface to decorate.
5. Gently slide the decal into place. Use a clean damp cloth or paper towel to gently wipe off excess water and remove any air bubbles that may appear. Allow setting time of about 3 hours. Your decorated object is ready! Note: You can speed up drying time by placing your decorated object under/near a fan.
6. If you wish to protect your decorated item from surface scratches, moisture, or fading then spray your dried decorated surface with an acrylic varnish such as Krylon Crystal Clear Acrylic finishing spray. This is available at various hardware stores. I recommend applying the Krylon Acrylic spray to the entire box in addition to the areas with decals. This will give the box a great finished look.
7. You can choose any of the following software for your custom decal creations: Adobe Illustrator, Macromedia Freehand, Deneba Canvas, or CorelDRAW. There are some simpler drawing programs that pack fewer widgets at a lower cost. Some of these come pre-installed in Apple iMacs and many other consumer-oriented PCs. “
LASER ENGRAVING DIRECTLY ON THE WOOD
While not done in this project, because I did not have a laser engraver, an alternative to the decal decorations is to laser engrave directly on to the wooden box. Graphics would be created the same way with Corel or some other graphics software and engraved on to the wooden box. One difference to consider is that while laser engraving can apply more highly detailed designs it cannot apply colors.
Step 8: Final Touches on the Outside of the Box
Apply padded feet to the 4 corners of the bottom of the box to protect the box as well as the surfaces on which the box will rest. Various types of padded feet with adhesive backing are available at hardware stores. Here is a picture of what I used.
Step 9: Make and Assemble the Dividers
Picture #1 above shows the dividers in their final assembly.
The second picture is a line drawing of the layout for the divider design and is done in Corel. (If it is partially hidden directly under the main picture above, click on it to see it). Matching the inside dimensions of the box, this second picture is a 12.25” x 12.25” grid of the center lines of the dividers to make the 25 equal sized compartments in the display box.
The third picture is another line drawing made in Corel and is the outline of one of the eight divider pieces needed to sub-divide the interior of the box into 25 compartments. (If it is partially hidden directly under the main picture above, click on it to see it). Each of these is 12.25” x 1.5” x .25” with equally spaced, .25” wide, notches. The notch width is to accommodate the crossing .25” divider piece.
Fortunately, Home Depot sells pieces of red oak trim, 48” x 1.5” x .25” so all we have to do is cut this trim in 12.25” lengths and put the notches in them. Make the length cuts so you get a full 12.25 piece so it will fit snugly into the box without requiring glue or fastners to hold it in place. Test the lengths of the divider pieces for fit in the box frequently while cutting to ensure a snug fit. Fine tuning of the length may be necessary.
While I do not have a laser engraver/cutter, I do have limited access to one where I work. To ease marking and cutting the divider pieces I cut the outline in the third picture (second line drawing, partially hidden, directly under the main picture above), full size, in a piece of laserable plastic on a Xenetech laser engraver. This plastic pattern is shown in Picture number 4.
As shown in the rest of the pictures, I then laid the plastic template on the wood strips from Home Depot and marked where to cut them. I made the cuts with a hand-held jigsaw or saber saw using care to make the cuts as straight as possible. Use a .25” wood chisel to cut out the top of the notch. As with the length of each divider, test the notches of the divider pieces frequently while cutting to ensure a snug fit between mating divider pieces. Fine tuning of the notch widths may be necessary using sandpaper.
Finish the divider pieces by lightly sanding any rough edges and applying several coats of Krylon Crystal Clear Acrylic Spray. I used Satin but a Gloss version is also available. Try to avoid spraying in the notches as this may prevent easy assembly of the divider pieces. The divider pieces can now be assembled by mating 4 pieces with the notch facing up with 4 pieces with the notch facing down at a set of upward facing notches. Push them together until they fit fully together. The total height of the assembly should be about 1.5”. Once all 8 pieces are together in the grid pattern shown in the second picture above, test the fit of the entire grid in the box, fine tuning the fit if necessary. If the divider grid fits snugly, no permanent attachment will be necessary. If the grid is loose, some glue may be necessary later during final installation. They should look like the last picture:
Do not attach the dividers permanently in the box at this time because we will be adding felt to the bottom of the box first.
Step 10: Construct and Install a Felt Liner
To prevent the rune stones from rattling around in each compartment, a felt liner will be applied to the interior bottom of the box. I selected sandy colored felt pieces from Michael's Craft Store. Since I could not get a single piece 12.25” x 12. 25”, I used 12 “ x 9 “ pieces and cut them so the seams fall under the edge of a divider piece. The first picture here is a Corel layout of the felt cuts based on the divider center-line layout.
NOTE: Do not glue the felt pieces down until the box decorations are complete and the entire box has been finish sprayed with several coats of Krylon Crystal Clear Acrylic Spray. This will avoid having to mask the felt when the box is sprayed.
After cutting the felt to the sizes shown above, apply a little spray adhesive, available at Michael's Craft Store, or Home Depot, to the underside of the felt pieces. Carefully apply the felt pieces to the interior bottom of the box following the pattern in the first picture. Be careful that the edges of the felt pieces come together completely without overlapping so they will be hidden under the edge of a divider piece.
After the felt liner is installed, you can get the grid of dividers in place in the box. The last picture shows the installed felt and dividers with the felt seams hidden.
Now the sandcarved rune stones can be placed into the box in the compartments corresponding to the positions on the large decal on the inside of the lid.
Step 11: Conclusion
Now that your rune set, and the display/storage box, is complete you can display your runes as a craft or artwork
You can get more information about runes at: http://en.wikipedia.org/wiki/Runes
Good luck if you decide to make yourself a rune set and display box and thank you for reading these instructions. - Richard M. Eslinger, Farmington Hills, MI.

Participated in the
Craft Contest
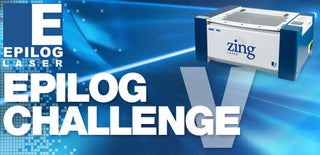
Participated in the
Epilog Challenge V