Introduction: Strengthening a 3D Printed Part
As we all know, 3D printed parts produced by our ordinary home type printers are not so strong and when used in place of actual parts, they don't last long. I thought it would be great If it is possible to somehow strengthen the 3d printed parts and worked on the subject a bit.
Strengthening a 3d part may give us the ability to use those parts in place of actual working, load bearing parts. So instead of trying to find an original replacement part for a broken one of our gadgets, robots, vehicles, mechanical toys or in any mechanical tech project we develop, we can simply go with the 3d printed parts.
The need for me to develop this instructable arose in fact when i bought some bicycle accesories from ebay. Recently I've bought two cycling front pannier bags . One for my gf's bike and one for mine. The bag's support was suitable for 1" handlebar thickness and barely fitted to my gf's bike. And didn't fit to mine as my bike had a 31.5mm thick handlebar.
I planned to manufacture the parts with matching dimensions to my handlebar by 3d printing them.
Step 1: The Part Required
This is the disassembled part which I planned to produce by 3d printing.
To produce a 3d printed part, you need to have the 3d model files for it. So you need to either find and download them from the internet or get to work and model it yourself. Way 2 was the only choice I have, as 3d model for a specific part like this is impossible to find on the internet and I needed to modify it to fit my handlebar anyway.
But as very well known, 3d printed parts are not so famous with their strength. I've thought that an ordinary printed part willl not be strong enough to work properly at my bike, with heavy stuff in the bag, going on bouncy roads. So I thought that it will be necessary to strengthen the part somehow.
In my previous boatbuilding experience several years ago, I saw how much some layers of fiberglass and epoxy give extra strength to a thin plywood part, enabling it to withstand strong forces easily.
So I decided to use fiberglass and epoxy to do the job.
First plan was to model the part, do the necessary modifications on the dimensions and cover all around it with fiberglass fabric and epoxy. So I started modeling my first design for the part.
Step 2: The First Design
I ended up with a part like this. I've arranged necessary details with required dimensions, and overall enlarged other dimensions to make it a bit bulkier. I've enlarged the surfaces for them to be able to carry reinforcing fiberglass fabric.
I also made grooves on all sides for the epoxy resin to fill and give the part an extra strength. I've modeled holes that go through the part from one side to the other, to connect the sides together internally, provide a link with fiberglass and epoxy to support from the inside.
I've printed the part using an Up printer and tested whether it fits to other original parts.
I choose a lattice type fill while printing leaving quite emty space in the printed part. This normally should reduce the strength of the part considerably but it was done for a purpose. I've drilled several more holes on the printed part, between the 3d modeled ones for the epoxy resin to flow inside part, giving the part much greater strength.
Step 3: Applying Fiberglass and Epoxy to the First Design
This is the dirtiest part of the job. Epoxy and fiberglass is hard to work with. Sticks to everything and very difficult to clean.
First I took several fiberglass threads from the fabric and sew the parts from one side to the other to provide a glassfiber reinforced connection between the sides.
Then I laid the parts on a piece of nylon as epoxy fortunately doesn't stick to nylon well. Then applied epoxy resin to the surface, put the fiberglass fabric cut to required shape and size over the wet surface and applied more epoxy on top. Until the fiberglass fabric becomes transparent.
Repeated this for each side on all parts and left them to cure around a day after each application. Took a while for the parts to be glassed completely.
Step 4: More Epoxy for Added Strength at the Sides
I've poured some more epoxy to the side grooves of the part for sideways strength.
Step 5: The Second Design
While making the first design, the idea was to partially fill the inside of the part with epoxy thru the extra holes drilled strengthening it from the outside by covering it with epoxy soaked fiberglass. While printing the first part, this second thought came to my mind to 3d model the part as a bare shell only and build the inside structure with epoxy and fiberglass later on.
So I started modeling this while also still waiting for the layers of epoxy-fiber to cure over the first one. I wanted to manufacture both designs and compare them in strength and ease of production. I also used different approaches towards filling the part 1 and 2 of the second design( two parts were necessary for mounting the bag to the bike).
As seen, the second design is an empy shell with 1mm wall thickness. The round part is separated from the big part to make the filling process easier. It is possible to screw fit the round part back to the main part during the curing of the epoxy fill inside.
Step 6: Filling the Second Design With Epoxy and Fiberglass
First I shredded some amount of fiberglass and stuffed them into both of the parts until they are more than half full. Then started pouring small drops onto them and applying a bit of pressure to soak them.
Step 7: More Filling Into the Design#2 Part#1
Continued this until all fabric inside is wet and then added more fabric and epoxy step by step making the inside of the part is full. Then Screwed the round part on top of it. I continued filling the part, rising the level of epoxy-fiber mixture to the edge.
I did the same to the smaller part.
Step 8: Filling the Second Design's Part 2
For this part, I followed a little bit different approach, I didn't fill it to half full from the start. I've placed only one layer to the bottom of it, than a second layer covering both the bottom and also the sides. Wetted these two layers with epoxy until they are completely transparent and continued adding layers one by one and appying pressure to get them wet with epoxy. Added a bit more epoxy for every 2-3 layers.
With the previous mehod, the part was filled with more epoxy and a little bit less fiberglass fabric. With this method, the part is filled with a lot of fiberglass and less epoxy in between the layers.
Step 9: Left All the Parts to Cure.
I checked all the parts from time to time and filled the spaces which were formed due to epoxy flowing inside the gaps. Added more fiberglass fabric where necessary. Time for the parts to completely cure and harden is around a day. There are faster epoxies on the market or you can add the hardener more than necessary to speed up the process but I don't recommend as it gets even more difficult to work and disables the epoxy to flow inside and fill the empty spaces.
Step 10: Completed Parts and the Assembly
Well the completed parts turned out to be rather nice, especially with the second design. I assembled them along with the existing parts of the pannier. They matched perfectly. Ready to be mounted on the bicycle.
Step 11: Removing the Plastic Parts
This step was not intended to be done in fact. I was planning to use the 3d printed parts with the reinforcing inside them. But while I sanded one of them, the printed skin at the outside of one corner just broke off and the rest peeled off very easily. As it provided no extra strength to the part, I removed nearly all of it, converting the part into an epoxy-fiberglass composite part.
Step 12: Results
I've used the parts during a 20 days trip around Sweden, Poland, Germany and Denmark without problems. The front bag was absolutely full with food during the whole trip and there were a lot of bumpy roads in the path too. The parts worked great and they are still rock solid. I've listed some results from this study below.
1-Interestingly, epoxy doesn't stick to 3d printed ABS plastic well. So extra holes and negative details that provide holding points for the cured epoxy is mandatory.
2- Covering a 3d printed part is much difficult than simply filling an empty part. It takes a lot of time. In the end this produces a lighter part. And there is certainly a great strength improvement over a 3d printed part without reinforcement. It is easy to see this, comparing a reinforced and non reinforced parts by simply trying to twist them by hand. The reinforced part is absolutely rock solid while the other is not.
3- The second method of reinforcing is much easier and produces a much neater result. There is nearly no need for cleaning after curing. And the produced part is like granite. :)
4- I've tried two approaches with different amounts of fiberglass, when handled, they both give the same feeling for strength and solidity. But the one with more fiberglass should be able to bear more weight before breaking I strongly guess.
5- The second design produces a heavier part, as it is completely full with epoxy and fiberglass. Removing the abs plastic parts surrounding the epoxy reduced some weight. But it also changes dimensions of the completed part. So dimensions must be adjusted during design, taking into the change the lack of abs plastic will bring.
6-Grooves and empty spaces can also be put into the design of the second part to prevent epoxy to fill into them, thus creating a lighter part.
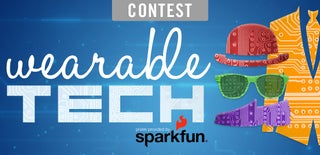
Participated in the
Wearable Tech Contest
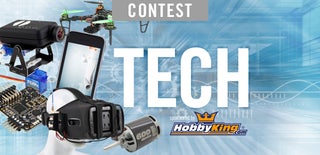
Participated in the
Tech Contest
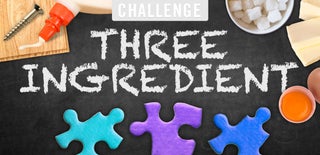
Participated in the
Three Ingredient Challenge
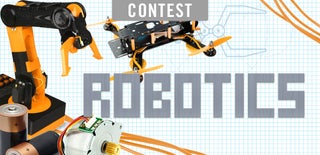
Participated in the
Robotics Contest