Introduction: Super Flexible Double Curvature Surface - Laser Cut Plywood
Carl Friedrich Gauss distinguishes between three types of curved surfaces, single curved - neutral (cylindrical), and double curved - negative (hyperboloid) and positive (spherical).
Curved surfaces are very attractive, especially negative double curved surfaces, but also very complicated to perform. What’s interesting about them in constructive terms is the increase in stiffness and load capacity as the surface is bent in one and two directions.
In a small book DIGITAL Gehry Material Resistance Digital Construction (Bruce Lindsey, Bitkhäuser 2001) writes that if flat piece cost one dollar, single curvature piece cost two dollars, double curvature piece cost ten dollars. This is true for all materials wood, metal, plastic, glass, concrete ...
It is immediately clear why some engineers are crazy about double curved surfaces and are constantly trying to find a method that can simplify and cheapen the process.
From time to time I search the Internet on that matter. One day I stumbled upon the wooden book covers that can be done on a laser cutter, with interesting technical solution of the spine; wooden board is slit in such a way that can be bend like rubber.
I immediately turned my machine on and started playing with this surface. The feeling of holding that piece of wood in my hands was incredible, something that just seconds earlier, was a stiff piece of plywood was now flexible like paper. But only in one direction, in the other was still stiff. Then I decided to cut the surface to enable it to bend in both directions, so that I could achieve double Gaussian curvature, positive and negative. After a couple of failed attempts that were based on a variety of perforations, I realized that what I was doing didn’t make any sense. I've studied the way in which the first surface was cut. In order to be bent it was turned into a series of slender elements that are easily twisted, which are interconnected on fixed points. The greater the distance between the fixed points, and the slimmer the elements, the more flexible the surfaces is. Although an element can twist for only a few degrees (before it breaks) when multiplied many times, the flexibility is incredible. I realized I should apply the same theory in both directions – so I turned the line elements into a rectangular spiral, whose segments twist in both directions, and in that way I connected the fixed point with very long slender elements. The result was even more fascinating.
When you first hold plywood cut in such a way it completely surprises you, you are not sure what exactly is in your hand, you cannot believe that it’s wood, because the lack of rigidity gives you a totally different feeling.
But, what to do with this piece of flexible plywood? I have some ideas, but I would also like to hear more suggestions ...
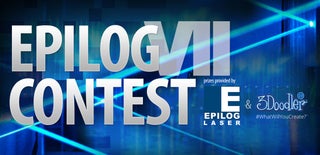
First Prize in the
Epilog Contest VII