Introduction: Swing Light: a Bicycle Powered Glowing Swing
If you follow these steps you can produce a glowing swing for a swingset that generates its power using a bicycle dynamo. The swing motion is not impeded by the setup, and you can run at least 3.5 meters of 12V LEDs off of it, as well as charge 12V batteries you may wish to include in the setup (or can be further used for charging small devices - like phones and mp3 players). Why? because it is a fun way to add light and energy-harvesting capabilities to a common piece of playground equipment we don't always consider illuminating. so why not??
also, you can re-use the same circuit, dynamo, and LED strip to power LEDs on your bike (or other devices requiring lesser or equal input) in the same way.
Please vote for us in the 2015 Make Energy Contest! You can vote in the upper right corner of the instructable :)
The back story: in 2011 I began the Purple Swing Project in Atlanta, GA as a street art project. Some swings lasted there for almost 2 years. While hitch hiking in Europe I continued the project, developing the techniques along the way and it evolved as I placed over 20 swings in 15 cities. I have also placed a tire swing in Cusco, Peru. While traveling, I was always trying to think of a novel way to produce energy from these swings, and thus the idea was born. With an original deadline of October 2014 for a mini maker-faire, the project hit quite a few snags as I learned with the project and continued to develop it. Thus, some of the steps below will show the way it was originally done and a better method, juxtaposed. ...this instructable has been several months in the making. You can learn with this project, too. It doesn't take a genius or special skills to make this.
Unlike another somewhat similar project I learned of while making this (oh the frustration after 2 years of working towards this goal!), this does not require effort to swing and does not limit your swing motion - you can swing as high as you want, and the resistance from the wheel is small - so even a kid can power it without an adult pushing them.
you can be a novice at all of the required skills as long as you have:
- access to tools (check your local hacker space, neighbors, etc) and assistance (some steps are really best with 2 people, even if you know what you're doing!)
- basic soldering. you will only be doing a few solders https://www.instructables.com/id/How-To-Soldering/
- basic bicycle maintenance. not necessary, but helpful https://www.instructables.com/id/Bicycle-Maintenanc...
- comfort with tools: hacksaw, drill, wrenches (anyone have a good instructable to suggest?)
Have fun!
Step 1: & All That Good Stuff
the materials list for this project really depends on what you already have. I will divide it into sections.
Bicycle pieces
-an old rear wheel. It needs to be somewhat tru, but it can be damaged.
-the wheel needs a tire, and it works better if the tire also has a tube. The tire can be old, but it needs to be firm enough for the dynamo (hang on, we're getting to that)
-either: an old frame you can cut in half... -or- 2 old dropouts (the pieces on the rear triangle that hold the rear wheel) -or- make your own axle holder by drilling appropriate sized holes in wood. This is needed to hold the wheel.
-a chain that fits the gears of the rear wheel you selected. It doesn't have to be a full chain. But you probably need 18" (.5m)
-a 12V, ~5W dynamo. Mine came free from the university bike co-op, on an old bike. Some dynamos are 6V instead, so make sure you get the right kind!
tools: potentially a pump, a wrench to fit the axle (unless it is quick release), and definitely wrenches that fit your dynamo (hint: although they used to do it with who knows what tools back in the day when these things were more popular, a socket wrench will do wonders)
bicycle wheel base
if you are using an old frame: you will be needing to grind the frame and then attach it with bolts to a wooden base. so you will need scrap wood wide enough to take the frame and weight it down. if it is only a 2x4 that won't be as good of a base as a wider piece. You -could- use a premade bicycle trainer or build something similar to it... I will cover some examples when we get to that.
if you are using dropouts to build your own rear wheel stand: you will have to build up 2 sides of wood (or another material...you could use bamboo and create a model of a rear triangle) to the correct height for the wheel to attach the dropouts to. you will also need a base.
if you are using your own special setup for holes: you could follow the same idea as for the dropouts except you will need to drill holes for the axle (same function as dropouts) instead
so, basically:
-wood for the base
-possibly wood for a pseudo rear triangle (don't worry if you don't know what that means yet! it basically is the back half of the bike - only the part that looks like a triangle shape on each side)
-bolts, to mount the bike frame to the base -or- the arms/special setup you will be making to the base
tools: drill, wrenches for bolts, possibly angle grinder if you are using a frame, dremel or another tool for a metal frame
Electronics
-rectifier: You need this to convert the AC output from the bike dynamo to DC, which the LEDs need.
-capacitor: I used one: 4700 uF from radioshack
-LED strip: I purchased a 5 meter (~16ft) $15 strip off Amazon. The important part is it takes 12V. You could use another type of LED strip. This one came with a controller and remote, but you could definitely modify this project to run off your own, potentially Arduino-powered, LED strip (but those weren't in the budget). I bought a weather-proof one. If you buy RGBW instead of RGB you will have problems finding a y-splitter for it, unless you want to make your own (RGBW is 5 pins, RGB is 4).
-old or cheap 12V/650mA+ wall charger (or 12 -to- whatever the range of your LED strip is - mine took 12 to 24 V. I just plugged the charger in directly to the control box first to make sure it worked. your strip might need higher current than 650mA, it depends, mine would run off anything under 2000mA). Quite a few devices you might not need anymore could have these, like this one. Check your cable box!
-cables and alligator clips (we used alligator clips throughout testing)
-breadboard (you could do this without one, but it would be a lot neater and less likely to short out if you get one!)
- y-splitter to connect 2 strands of the LED (one for each chain side of the swing - you will be cutting the LED strip) to the control box
-1 or 2 4-pin pieces to convert the female ends to male ends. If you are doing RGBW you will need 5 pin ones or to make your own using these. The pins come with the y-splitter (as in link above).
-extension cable for the power (5-12V DC plug extension, probably 12ft, can find on amazon, 2.1mm x 5.5mm). not pictured.
-velcro for the cables
-electrical tape
-tupperware or other container to house the completed circuit and battery
if you are going to do the battery addition:
-switch (we used a SPDT - single pole, double throw switch like this one)
-diode to protect the 12V battery (FR202 "fast recovery" diode with 2A forward, 100V backwards works - some diodes with lower forward voltages might be better at charging the battery)
-RC/hobby 11.1V (12.6V fully charged) LiPo battery with pins for attachment (usually comes as a set from hobby stores)
tools: soldering iron, solder, wire cutter (one that can remove insulation), voltmeter, scissors to cut LED strip
The swing deal
-a swing. You can make one out of wood. I did an entire project around northern and eastern Europe using only scrap wood I found in cities to make swings. If you have a tight budget, you can find a piece of a 2x4. If you go this route, you will need sand paper and a drill bit. A firm swing is better than the floppy kind you find on kid's playgrounds, although it won't really matter once you're sitting on it.
-possibly: sand paper
-if it doesn't have holes already: a drill bit. I almost always go with 18mm.
-chain (or if you can weld, solid steel pipes to attach the swing with). rope could work, but be careful to use non-stretchy rope. it also won't work as well in un-weighted tests as chain or a solid rope (it needs to be at least 10mm). At least this, although we got a stronger chain
-2x U-bolts (unless your swing has another attachment mechanism). You will want to drill the holes after deciding on the size (you need fairly sturdy ones!)
-8x nuts and at least 4 (if not 8 instead) washers for U-bolts
-a swingset or sturdy structure that the swing can hang from (if you are doing this from a structure that doesn't have pre-drilled definite weight bearing hooks, you will need hooks and a drill, or something strong like webbing or stronger rope than paracord that can hold weight and take abrasion, which you can attach to)
-carabiners, clips and/or quick-links that can support at least 200lbs (since you have 2 sides to the swing you should technically be ok with this as long as you keep relatively equal distribution). How many you need also depends on your setup. If you don't have anything, I would purchase (4). (top and bottom of both sides of the chain) to start with - but you might also need one above the chain arm from your eyebolt, depending on your anchor points.
-we used 200lb weight tested velcro straps with carabiners for our setup to make it portable. You can use climbing-strength webbing instead for the same effect, cheaper, and tie a hitch knot or anchor with a tied loop of webbing using a wrap 3 pull 2 technique. 100lb (for chain arm) and 200lb (2 of these for the main swing support)
tools: sand paper or sander, drill bit and drill, wrench to tighten u-bolts, bolt cutter (unless you want to leave it longer to adjust size)
The arm
-pipe. We were going to use free bamboo we had lying around but settled on 1.25" PVC pipe. you could definitely repeat this project instead with bamboo.
-paracord, or another thin and relatively strong cord (it won't be taking all of your weight, but it will be taking some force!) - but something less stretchy than paracord would be ideal, as this made getting the final chain tension correct a bit tricky
-eyebolt with 2 washers and nuts
-pvc glue
tools: pipe cutter or hacksaw, drill and drillbit for the holes for the paracord, lighter for end of paracord, scissors/knife to cut cord
other details
-container for the circuit
-zip-ties: great for testing
-outer wrap/pipe for the LEDs, to protect them from the swing. we used clear vinyl pipe from home depot, but it was expensive (1.25" outer diameter, clear tubing, 10ft, $18) and a pain! if this is going to be limited use, you could use plastic tape
Step 2: Circuit Step 1: Rectifier
Note that out circuit diagram above does not include a protective diode, which we add in the full circuit later. Right now we are just looking at everything to the left of the switch and battery - that is just a rectifier and capacitor. From that you just add output cables, and that is all you truly need unless you want to add the potential for a battery (if you do, you can take this circuit with you anywhere and attach the dynamo to a bike wheel and run LEDs off your bike using combined battery and dynamo power as you ride! so it adds versatility. Additionally, the battery can let you take photos in the field while no one is on a swing, etc, and be recharged through use)
The first thing you need to add is the rectifier. Here we used a bridge rectifier. This converts the AC signal from the bicycle dynamo to DC.
It has a specific polarization you need to keep in mind. This should be marked on the rectifier, probably with a + sign. The negative pole is directly opposite it. The other 2 leads are for AC input. they are -not- polarized. You can check the polarization with a voltmeter. If the positive lead is on the positive terminal of the rectifier, it will register positive (on most voltmeters this will be a 1.0). If the positive lead of the voltmeter is on the negative terminal of the rectifier, it will register negative.
Solder the rectifier to the breadboard when you achieve the orientation you desire (you will be adding a fairly large capacitor, so keep that in mind! leave enough space!)
After the other components are added you will want to add shrink tubing to and cut one of the 2 AC leads shorter than the other - so that they cannot short each other out. you will end up trimming any excess from the + and - leads as well so they can't short anything out. keep this in mind as you are adding the capacitor and DC output cable!
Step 3: Circuit Step 2: Attach the Output Cables
Before you complete this step, make sure you have access to another appropriate (likely 12V) adapter to test and program the LEDs.
You need to cut and strip a 12V adapter that you do not plan on using again. the main reason you need an adapter in a certain range is if you are using a controller box (that sometimes come with the LEDs), as these only accept input cables with a certain diameter head. The diameter of a cable's head is dependent on its output voltage.
Keep the legs long enough that you have a comfortable distance from the circuit to the controller box (or whatever you are attaching to program your LEDs/the power input for your LEDs, depending on your setup).
Once you only have the head and two legs from the cable (you won't need the outlet adapter anymore) you can strip away some of the insulation. Strip away at least 2". Twist the copper wire that you now see so you can stick them easily through the breadboard holes.
You need to identify which leg is negative and which is positive. Usually one arm leg will be dashed/striped/have a white line. For most adapters (but not all!) this is positive and carries the current. The other, unmarked line should be the negative, ground side.
This is important because you need to solder this to the corresponding + and - sides of the rectifier (not the AC input sides. we identified the sides of the rectifier in the last step.). The + side is likely marked, and the negative side is directly opposite it. Stick the copper wires from each side (you probably want to twist them more as it might be tricky to keep them together), probably in a different hole on the breadboard than the rectifier wires, or more precisely if you want to keep a neat circuit layout. Solder the copper to the breadboard, and to the respective corresponding + or - legs of the rectifier. You can either bend the rectifier legs (better idea), use wire, or temporarily use a lot of solder to bridge the two.
You should now have the output cables and rectifier on the non-conductive side of the breadboard, and the legs and solder on the conductive side.
Step 4: Circuit Step 3: Add Capacitor
I used a 4700uF capacitor from radioShack.
This definitely has polarity as well. Usually they have a negative marking, or arrows pointing to the negative side. You will be attaching and soldering these legs to the same points you attached the output cable in the last step to. These attachment points will each have the correct leg of the rectifier, the correct leg of the output cable and the correct leg of the capacitor. You will likely need to bend the legs of the capacitor to attach them horizontally on a small board.
Solder the capacitor legs to the rectifier and output once you have checked that they are correctly oriented as described above).
Step 5: Adding a Battery and Switch to the Circuit (optional)
This step is entirely optional! If it is beyond your scope and soldering skills, don't worry! the circuit will work with just a capacitor and a rectifier. All you need to do is trim the + and - ends of the rectifier, and then add shrink tubing to the AC input leads of the rectifier and cut one shorter than the other so that they won't interfere. you can see in the photo of the underside of the circuit above the AC leads before we cut one of them shorter and added the tubing (just insulation so nothing would short out). At that point, you can have a fully functioning swing light circuit, already!
now, if you want to add a battery, so that you can have the option of powering the strip without motion or maybe charging devices (you might want to modify it further for that):
In the end we ended up reconfiguring the circuit, according to the diagram (minus one switch - you only need one as the LED strip is controlled by a remote)...the switch labeled "on/off" is optional.
We learned that we had put the capacitor in inefficiently - it could take up less of the board a different way.
We added a switch, 2 jumpers (small insulated wire pieces), pins for the battery connection, a 100V reverse voltage and 1.2V forward voltage at 2A FR202 diode to prevent charge from flowing back into and damaging the circuit and dynamo and to allow charging when the battery is not in use, and a 11.1V (11.1-12.6, fully charged) LiPo battery from a RC hobby supplier. The diode is a change from the circuit in the first step.
The diode does not protect from overcharging the battery, just from backflow and discharge of the battery when not in use. The battery we used is 1000mAh.
Keeping the original setup (but moving the output cables a little) the battery (cable to attach the battery to/header pins) is attached in parallel with the capacitor, with the diode in series with the + end of both. A SPDT: single pole double throw switch is added, where both sides of the switch turn on (the up position powers the circuit only via the battery and diode, the down position allows the light strip to be powered directly from the rectifier circuit.) The battery charges off excess voltage- when the voltage exceeds the forward voltage of the diode (1.2V) and the current voltage of the battery. To not use the battery, disconnect it or use an on-off-on switch (the SPDT switch here does have a center position where it is not connected to either side and can only charge the battery, though - and is effective).
You can see the completed circuit in the photos.
Step 6: Making the Swing: Step 1
Being a street artist who used swings as my main medium - I could write a full length instructable on it! If you want to make a swing from wood, you first...need to select the proper piece of wood. Not rotten, preferably somewhat smooth and level, and at least the dimensions of a 2x4. Those aren't as comfortable. I have made them out of sections of 4x4s before, too. The thinnest swings are 1" thick. You will be sanding later, so they can be in rough shape. It depends on how much work you want to put in...
Step 7: Making the Swing: Step 2
You will be drilling the wood next. In this case, the holes need to match the placement of u-bolts (or another similar attachment mechanism). You could alternatively use eye-bolts. Even with rope, I like to have 2 holes on each side. Usually, I need a 17mm drill bit for 10mm rope. We used a pre-made swing from my former projects for the u-bolt, and the 17mm holes were slightly wide, but worked. Not everyone has quite so large wood-working drill bits on hand!
Test the u-bolt sizing with the drilled holes and mark where you want to drill. I bought what I think was 2 3/4" u-bolts, but the next size up is probably even better.
whatever you do, do not consider nailing! I used those once with a swing, never again! they are dangerous, especially when a piece of wood is subjected to weight. Use bolts, and if anything is pulled upwards, make sure it is pulled upwards against the bottom of the swing, securing it in place.
Step 8: Making the Swing: Step 3
Sanding and painting needs to be done to protect your swing users and the swing itself. What coarseness of sandpaper you use depends on how rough your wood is. You also need to sand the holes a little bit, but it won't be as much of an issue for this project.
I usually spray paint my swings. I have a standard color I always use (Montana Gold: Sweet Dreams - the best purple!) but, any spray paint will do - cheaper brands might need a second coat. I rarely needed to do a second coat, and my swings have lasted up to 2 years outside in harsh city environments. Make sure you use proper facial gear if spray painting (which is highly recommended as it dries much faster. I have waited a day or more for canned paint to dry). You probably want a somewhat wide-coverage nozzle for ease of use, which may not come standard with the kit - you can find these at art stores. Protect whatever surface you are spraying under and follow all instructions - make sure it is in a ventilated area (outside...).
Step 9: Making the Swing: Step 4
Once your swing is dry from painting, attach your u-bolts.
You will want at least 1 washer and 2 nuts -per hole- so that would be 4 washers and 8 nuts total.
but, it would be better if there were 2 washers. The 2 nuts need to be placed so that the bottom rotates opposite to the one above it, locking it in place against the washer and the metal plate.
You could put a 2nd washer on the top of the swing. it would cover the hole. But that is up to you.
Your swing is complete!
(I usually write something on mine with a paint marker, like a positive phrase. You can do as you wish!)
note: in the pictures we don't have a 2nd locking nut on the bottom - but you should put one there.
Additionally, you can and should file/cut/etc extra lengths of the u-bolts down so as to not cause injury.
Step 10: Cutting the Swing Chain
Our chain was 10ft long, and we decided we would need 2x 5ft pieces. This is about a good length for a swing for smaller playground sets that you can almost reach without a ladder... but a bit long for small kids' playground sets. It won't be long enough for tall industrial playgrounds.
Use bolt cutters or a similar tool to cut the metal.
Step 11: Building a Base
This is one area I am leaving open for interpretation and not going to provide very good guidance on. I apologize ahead of time:
our base was built using a piece of scrap wood and an old bicycle frame, that was angle grinded to just a rear triangle with a seat tube (take all components off - including brakes!) I did not do the angle griding, but was fortunate to know folks who have access and knowledge to do this.
Holes can be made in the frame using a drill press or a drill with a bit that can cut steel. Make sure to keep the drill bit lubricated/cool, it takes time. also, don't forget eye protection!!
We added bolts and washers to attach the frame at the seat tube to the base.
You can find a broken bike frame local to you either at a bicycle cooperative (or small, neighborhood bike shop) or in online classifieds.
Instead you could make your own base with holes that would hold the axle. Or use dropouts, the piece that holds the axle on the frame itself, on your own base. Those methods would not require an angle grinder or an old frame.
here is an idea: https://www.instructables.com/id/No-welding-pedal-g...
or use a bike trainer like they do here: https://www.instructables.com/id/How-to-Build-a-Bic...
One more option is to use a full bicycle and suspend the rear wheel slightly off the ground. This could be possible by taking the front wheel off and bolting the fork onto something sturdy... Or perhaps bolting the frame to something at a tilted angle, so the rear wheel is in the air? I have not tried this method, but it certainly would be portable! If you do this you will need to leave the rear brakes un-hooked and disconnect your current chain
For instance, if you are going to bolt the fork onto something, look at how they do that in this project: https://www.instructables.com/id/DIY-Bike-Generator/
Added note: the reason we build a base and don't attach the swing further up is for stability and portability, for use with other swingsets. If you want to attach the wheel further up to a swingset frame, you could, but you would need a way of securing it on the sides with bolts. If you choose to do this you won't need a base, just clamps or bolts, and a single structure/swingset frame to attach to. Keep in mind that you still need it below the chain arm enough that the dipping arm motion keeps the correct tension and that a person trying to "reach the sky" on the swing won't cause the chain arm to rotate into the wheel.
Step 12: The Bike Wheel
We used a 700c rear road bike wheel. You could use a 26 or 24" mountain bike wheel. Smaller wheels could also work, but, we haven't tried them. It needs to be a rear wheel with a cassette and freewheel. A fixie won't work the same way, as it won't keep the induced inertia from a swing user's forward inertia. This means, when the swing user gets to one maximum point, the chain is pulled in one direction. At the other point it is pulled the other direction. With a regular freewheel, the non-engaging direction does not have an effect on the wheel. On a fixie, it causes the wheel to rotate the other direction at this point.
You need to make sure your wheel is fairly tru, which means that it doesn't wobble a whole bunch. A little is ok.
https://www.instructables.com/id/Bicycle-Wheel-Trui...
Add a tube and tire so you have an inflated, firm tire.
here you can learn to change a road bike tire:
Step 13: Attaching the Dynamo
I would advise looking at an instructable like this if you are not familiar with bike dynamos:
https://www.instructables.com/id/How-to-install-a-d...
we placed ours' in an atypical way so that it rests on what is below the wheel when it is engaged. Dynamos usually have a lever that allows them to be engaged or disengaged from the wheel. Positioning it so it moves efficiently without causing extra friction can take a little bit of patience and practice. You will likely need something like a socket wrench to tighten the bolts next to the wheel as it is a tight space to work in with a full-sized wrench.
Step 14: Dynamo O-ring and Alligator Clips
We used an o-ring on the dynamo to reduce friction. You could use 2. it fits relatively tightly and allows the normally plastic dynamo wheel piece to run more smoothly against the tire and with less noise.
The alligator clips are the leads we are using from the dynamo to the circuit. a more permanent attachment could be made with wires wound in the same locations, but we needed something quick, on hand, and portable. Clip one to the top of the dynamo, where there is a little nut that can be loosened - it goes below this nut, touching the metal. This is your AC, although using our rectifier that won't matter. The other clip is ground. It needs to clip on another part of your dynamo or your frame, if it is steel. If your circuit isn't working, you might want to check that you have correct placement of these pieces and particularly the ground cable - that messed us up in the beginning!
Step 15: Measure and Cut PVC Pipe
The long PVC arm is fairly easy to measure. You want the swing chain to go through the pvc at approximately the width of the swing. it can be wider, but not narrower, and still be stable.
From one of the holes you want at least 2ft to the point of attachment with the chain arms. you can cut your pvc when you are sure you have a good length measured. Use a hacksaw or pipe cutter.
Measuring the length of the chain arms is slightly more difficult. Start with 2 pieces of PVC, 2ft or less. use a 3 ( T ) or 4 (+) way connector piece (in the end you will probably want the 4-way connector).
It would be good if you already had the holes for the swing chain drilled (see next step) so you could attach this to your swingset frame or hooks above. If not, you could use a helping hand to determine the location of the holes.
In our case, we went with about 6" on each side of the connector. The reason you need to examine this is that although a wider length between holes would be more efficient, it isn't necessarily going to keep the tension in your setup. If you are using only bicycle chain and not bike chain with cord, you might be able to keep the tension at longer widths.
When you test for the optimal placement you don't need to keep your dynamo engaged. Just make sure your wheel base is lined up properly with the PVC arms (the tough part)... and tie the cord onto both the PVC arms and the chain. This doesn't have to be a great, final knot - just enough to test and adjust. The structure you plan to set your swing up on could also be a factor in where you choose to drill these holes.
Once you have decided on a width or range of widths, cut these smaller arms to size.
Step 16: Drilling Holes
You will need to drill the holes for the swing chain in a slit shape. The angle of ours' formed almost an "X" if you were to look from above as the width of the PVC accommodated slightly more than one link, and they are offset from each other. As these slits will likely still be a little loose around the swing chain, you will need to secure the chain to the swing arm (this has nothing to do with weight bearing). We used zip-ties for this.
We used a drill and a dremel for this process (and a hacksaw, but let's not talk about that, you shouldn't try that). A file would also be good.
You also need to drill holes in the arms the bike chain or cord goes through, wide enough for the cord. Even if you are using all bike chain, you will probably need a tiny bit of cord at the top to secure it.
Step 17: Proper Chain Tension
The chain tension is difficult to get right. Once you have fixed the cord to the PVC side arms, make sure there is plenty of room to play with. You want to at least have the system taught enough that the chain hangs at the center of the axle bolt (as pictured) before attaching it. This might raise the platform off the ground a little, so make sure to have weights! I would recommend cinder blocks, although all we had was a heavy tool bag.
If you need help on shortening/lengthening a bicycle chain (as you need one chain that is not connected at either end) and finding the correct chain please see: https://www.instructables.com/id/Using-a-Bike-Chai... to help you on using the chain tool. Remember that some wheels take different chains depending on the number of speeds. Single speeds, fixies, and BMX bikes use a different chain than road bikes, which often use different chains than mountain bikes... It all depends on the number of teeth and thus diameter necessary.
or resort to:
http://sheldonbrown.com/chains.html
now, the chain tension we are using involves the use of a cord, unless you connect multiple lengths of chain so that your piece is entirely chain - but the same rules as you would use to find the correct chain tension a bicycle still apply!
Step 18: Tying Knots
you don't need to offer them a ring or anything. all you are going to do is tie the cord securely to the bike chain.
I used a barrel knot, which is kind of like 3 overhand knots joined together.
Test your chain length again, and leave some room for adjustment, especially if your final structure is going to be a different height or you plan on using this on different swings. We had a good 4ft of extra cord we tied up out of the way.
Here's a good collection of instructables on knots:
Step 19: Testing Your LEDs
This needs to happen with both your rectifier + capacitor circuit and your battery. If you choose to do the full circuit, simply flip the switch between testing and roll the wheel with your hands (or you can use the swing if you're lucky enough to be able to at this point and extra careful!). Make sure they function as you expect. Pictured is a 4-pin connector needed to plug the LEDs into their control box. your LED kit should come with this. Keep in mind you will need this for the cable routing!
Step 20: Cutting the LED Strip
There is a good tutorial here:
http://www.ecolocityled.com/category/soldering_led_strip_waterproof
Most pre-made strips have regular marks, RGB or RGBW, etc, that will designate the points at which you can cut the strip. You can usually just use scissors.
We cut 2x 5ft pieces (after making sure 5ft was the length we would use) off of the strip, one from each end, so that each piece had one adapter on it. Keep in mind that you will now have 2 pieces, one with a male adapter and one with a female adapter. To route the cables to a y-splitter later, you will need an extra 4-pin male adapter piece to make them both male.
Step 21: Cutting Outer Casing for the LEDs and Swing Chain
We bought 1.25" OD clear casing for the LEDs and chain to go through. Our section was 10ft, so we cut it approximately in the middle and then took a little extra off, to end up with 2x 4ft9 pieces. Carefully use a boxcutter or similar tool for this process. Thinner diameter tubes would work but would be more flexible and less protective and harder to pull the equipment through. Larger diameter tubes will be more expensive but make the next somewhat frustrating step easier!
Step 22: Pulling the LEDs and Swing Chain Through the Outer Casing
This step might be super frustrating for you if your tubing is bought in a coil with any sort of restrictive bundling- unless somehow you can stretch that out. If you don't buy it that way, you might be able to just use gravity or possibly just one lead cord (you can use paracord)
If you are unlucky like I was, you will likely end up resorting to tape and a lead cord... and something like 2 unbent clothes hangers...to pull the chain, which you will attach with tape (or weave through) to the LEDs and do a lot of very frustrating pulling, some of which might damage a few LEDs (we only damaged a few, so it ended up ok)
Step 23: Making a Circuit Container
I made a circuit container from an old tupperware box with lid (something more sturdy would be better, though!) This isn't completely waterproof, but it is protective. (note: make sure tupperware is dry!). I positioned the circuit and then cut holes with box cutters and scissors for the 2 AC leads and another for the power to the LEDs. the box was big enough to house the LiOn battery as well.
I used electrical tape afterwards (not pictured) to secure the AC leads and power adapter end to the box, and also added shrink tubing to the AC leads exiting the box (that attach to the dynamo).
You might want to use velcro on the bottom of the container to secure it to the wheel base or wherever you intend on placing it, but that is up to you!
Step 24: Cable Routing
you have a little bit of freedom here.
We decided to use an extension DC power adapter cable and keep the LED pieces on top of the swing arm. this meant using velcro with the control box. We bought a y-splitter that connected the 2 LED strips to the control box so that we could run 2 shorter strips, one down each swing chain, instead of a long 5 meter one. I have so far only found 4-pin LED splitters, meaning that you can only do this with RGB, not RGBW strips, unless you make a 5-pin splitter yourself (we might post an instructable on that later as we plan on doing this to use the better RGBW strip we have).
We used electrical tape to attach the y splitters to the LED strips more firmly (you have to do this, they are flimsy connections otherwise). If you cut this correctly, you should have 2 adapter ends, one from each end of the LED strip, available. One will be male and one female, so you will need one 4-pin adapter to make them both male, so they attach to the splitter. Keep in mind to line things up correctly. Usually the adapters have the ground cable socket marked. In ours' it was white, and lined up with the arrow on the y-splitter adapter side. Plug the pins in the correct way.
If your circuit isn't working, you may have plugged the pins in the wrong direction, flip them over so that ground is on the other side (if ground was on left, put it on the right side of the adapter it is plugging into). As I stated, usually this is marked.
From the LED control box, we drilled a hole in the swing arm and routed the DC extension plug from the control box to the circuit on the ground, via a 4-way PVC pipe connector and a 1ft arm extending beyond the wheel base below it. This allowed the extension cord to drop down where it wouldn't interfere with the wheel.
Step 25: PVC Glue
We only glued the main swing arm into the 4 way connector, as we wanted to possibly exchange the side arms later, but you could glue all pieces. make sure you line up your holes correctly!
included is another picture of PVC glue from a different project, for an idea.
Step 26: Straps and Eyebolts and Other Attachments
We drilled a hole for one eyebolt with 2 washers and 2 nuts to hold up the swing arm just before the 4-way connector. It attached to 200lb-weight tested velcro straps, which we ended up using for the swing support to make it transportable for our purposes. However, if you have other attachment plans, you should probably use them! The velcro isn't very permanent :/
Climbing-tested webbing or rope could also work and be just as strong for this purpose, but cheaper, if you can't drill into your structure and ensure you have strong bolts.
Make sure whatever you use is safety rated and strong enough for your purposes!!!!
Step 27: Placing Your Swing
When choosing a swingset, make sure your swingset is in a good location and stable - that it is anchored in the ground.
You will need to secure your wheel base to the ground. There are plenty of methods of driving stakes in that could work, or using heavy objects. I would use cinder blocks or cement, if you can't find a way to bolt it to the base of the swingset.
The wheel base needs to be again lined up with the chain arm, and the chain tension adjusted, particularly if you are using para cord and it has stretched.
Keep in mind that for a taller swingset you will likely need a ladder and more assistance to place this, unless you want to sit on someone's shoulders as I had to in order to hang the swing!
Step 28: You're Done!
Enjoy your glowing swing and amaze your friends!
https://www.youtube.com/watch?v=jqYIwhgLnIA
Step 29: Acknowledgements
Thanks to:
Bryan Stuck and Klaus Mewes for assistance and improvements with this project
Larry Nosewalker for the use of his apartment during the building process, Ralph Edge for the use of his geo-dome during the building process
early swing-making photos - Patrick Ahlstrand
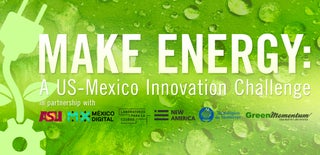
Participated in the
MAKE ENERGY: A US-Mexico Innovation Challenge
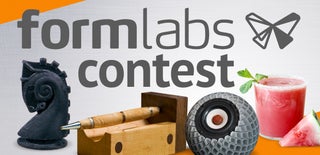
Participated in the
Formlabs Contest
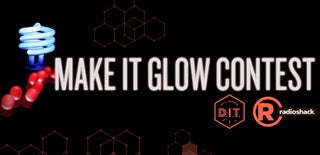
Participated in the
Make it Glow!