Introduction: BACKBOX ONE - More Than Just a Heavy Duty (tool) Carrier
'Never stop training' is one of my favorite quotes.
'Making errors is fun - you'll do it much better next time' is also one of my favorite quotes.
'When the going gets tough, the tough get going' is ... also, yes.
But my ultimate favorite is 'Never say no to a beer'.
Whatever, all that to say that since I'm (trying to be) a professional handyman I never bothered about parking my car faaaar from the worksites
- because I'm too lazy to keep on searching a decent parking spot for hours
- because I'm too maso - or stupid - and I don't care about carrying my heavy toolboxes
- because I'm too evil to give my occasional collegue the pleasure by accepting easy jobs 'learn it to do the hard way, it'll be a lot easier later'
So I do a lot of jobs crossing the city walking - 'Never stop training' you know...
But. All that time of walking workout a great part of my anatomy was left unexploited. Well, no, not thàt part ;), but my bàck - a virgin field that bagged for fertile seeds. My hands were full, but why should someone who carries a nice North Face backpack during mountain treks should need to carry stuff in his hands in his working time?
So I tried several classic backpacks. Last time I did I had a fresh sharpened chisel in my pack and guess what happened when I unloaded my back... Right, that thing perforated the fabric and ripped my arm.
Making errors is fun, I said once. Forget what I said. It's not.
That was the last time I did that backpack thing the stupid way. Things had to change. I looked on the net, found what I looked for, checked the next day because I thought there was an comma-error on the page - which wasn't, checked my counts, got insanely drunk once again and in a beer-ised mood I decided to build my own.
A lot of artists take good decisions being influenced by smokeable, drinkable or insertable stuff. Really. So why shouldn't I?
So here's a way to build a nicely portable, relatively cheap, heavy duty yak-proof toolbox that's also workbench, angle-cut rig, electric strip, moon lander and, why not, just a backpack you can use to carry fragile stuff like optical gear.
Enjoy!
Step 1: Prototype Design
This must be the first time I went through a protype design before starting to build.
I just wanted to know what the scetches I made would look like for real, and so I made a version in cardboard & styrofoam.
Generally I was quite pleased with the concept, but one thing that made me laugh in the first place & worry in the second was that it looked terribly like a coffin. Or even worse, a small coffin.
No-one would like to walk the streets with a mini coffin on its back. A full size one might be funny, but this was everything but full sized.
So my design needed to be 'uncoffinized', and also I decided to give it a bit more height.
I decided to build it almost entirely with alubond - a composite material I already used in previous I'bles. It's not cheap - some 150$ per square meter (I got the chance to have some leftovers for free). But it's relatively light, cutable with the miter saw and easy to rivet.
Step 2: Inner Structure
I decided to make a solid inner structure, since I'm used to use my toolboxes as a handy step (that's how I crushed the toolbox of a collegue, once). Too bad he had hidden his sandwich in that box, too.
Could have been worse after all. He's the proud owner of a chihuahau.
Plywood (16mm thick) looked okay to me (a bit less would haven been okay also), so after the shape of the ground plate I started to shape the three panels of the skeleton.
Note the angled edges. A miter saw is really a must. Set the right angles and rock those cuts.
Screwglue them together and screw the skeleton to the ground plate. Inox screws. High performance pistol glue.
If you want a nice finish you can cut some alubond panels and glue them to the inside of the box. Needless luxury maybe, and more weight to carry. That's why I did it.
Note the extra's at the top of the verticals. Those'll serve to insert magnets later.
Step 3: Outer Plating - Fixed Parts
Put your work upside down on a piece of solid plywood and mark the four corners to create the plywood cover.
Cut it out with a miter saw and respect the angles of the sides!
Screwglue it in place.
Then measure carefully the four corners, cut the four triangles and screw them to the inner structure.
Countersink the screws.
Use aluminium tubes to rivet those triangles to the ground plate.
Step 4: Outer Plating - Movable Parts
Time to make the doors.
Again: measuring & cutting.
A nice way to make hinges is to use inner tubes.
Glue them them to the ground plate and door panels with double sided tape and use alu strips to rivet the whole.
Cut the excess of the panels and use magnets to keep the doors in closed.
Step 5: Hammering the Cover
This alu cover has two functions: as slip-proof step and a closure to keep the four doors closed when the yak is on the move.
To cut this cover right you should make a copy of the wooden cover, and place it on a piece of antislip alu sheet. This piece will serve as mold when you start smashing the sides.
You can use the original piece, also. But hammering implicates impacts, and unless you want to destroy your box it's better to use a copy of the plywood cover...
Mark the four corners and cut the four triangles where the sides will meet. A bit of calculation, I agree. Or do it 'at sight and good luck' like me...
Clamp sheet & plywood and start hammering the sides.
Cut the excess at the end and smooth those sharp edges.
Did you know you can easily cut this stuff with a jigsaw? Well, now you do.
Use ear protection, it's a kinda loud operation.
Step 6: Finishing
I used a few pieces of riveted kydex (or similar) to have a nice finish on the rather uggly corner panels.
Call it 'the cool factor'.
Needless luxury, again. So do it anyway.
Step 7: Carrying Gear & Stabilizers
Now the 'box-part' is ready we're gonna make it a backpack.
For that we need lanyards & a back protection.
Use some nice belt stuff and transform it. Instructions in the pics.
Note the 'stabilisers'. The rubber dots hold the box stable when put on the ground. The lower are fixed, the upper are removable. There's only one on the pic, two will make it more stable.
Step 8: Extra 1: Electric Strip
It happens often when I'm on a worksite that I need an electric extension or a strip. So why not integrate this in the box?
Another reason: no-one could steal this object anymore!
Step 9: Extra 2: Drill Storage
How a simple hole can make the difference between carrying your drill with you, or not.
Step 10: Extra 3: Angle Saw Rig
Another habit of mine: using my toolbox as support to cut angles on wooden, alu or plastic profiles.
Instead of carrying a miter saw or a classic U-shaped wooden rig I made this cool piece to ease my worklife.
Concept: fix a removable 'saw-guide' in the cover of the box and combine this with another piece of plywood fixed temporarly to the cover.
Set the right angle, screw the guide, slide the profile and cut.
Remove & store after use.
Step 11: Painting
Yes, this needed a lot more creativity...
I should ask one of our local graffity artits to pimp this up!
Step 12: Storing
This box is definitely large enough to carry my essentials: drill, saws, a lot of hand tools, silicone or glue pistol and some small hardware - enough to do half of what clients ask me to do.
Don't forget: I still have both hands free to carry other gear.
Wanna use it as a classic backpack? Easy, even a telescope & binoculars can go inside and be transported in all safety!
I'm sure there are plenty more possibilities for this device. It can be a portable kitchen, gamers box or boozebox - got to try this ;)
Suggestions? I like to know!
Hope you like it as much as I do. If you have any questions, comment below!
Step 13: Evaluation
There's a lot of good to say about this prototype, but it wouldn't be correct not to talk about its inconvenients.
First of all: it could have been less heavy. It's okay to me, even filled with gear, but when my wife tried it, all she said was 'you're nuts'.
So if you want to keep it a bit lighter I can suggest:
- to use plywood of 10mm instead of 16
- to drill a few holes in the inner structure with a clock drill - it will withstand someone standing on the box anyway
- not to glue extra plates on the inside of the plywood (step 2)
- to use less rivets & screws, maybe
Second, it's not yet watertight. So I suggest or to add rubber joints at the inside of the doors, or to use a backpack poncho when it's raining.
Third: the magnets to hold the doors closed aren't sufficient, so I added an additional groove&slot-system to avoid that the intestines come out of the belly every time I'm removing the cover.
Fourth: yet to discover. Check the updates!
Step 14: Training Day
27 march 2014 - First Trial
Weight Backbox One: 24 Kgs - 52 Lbs
Weight bellybag: 9 Kgs - 20 Lbs
Let's call this 'full capacity'...
Distance to worksite: 3km - 2 miles
One word: it was awesome and even more comfortable than I thought.
I'm sure this device is gonna give me a lot of pleasure the coming years!
Yak-proof, definitely!
The only inconvenient of the day: I wish I had integrated a toilet...
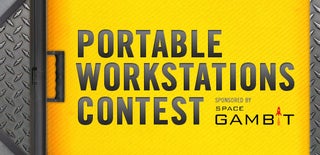
Third Prize in the
Portable Workstations Contest
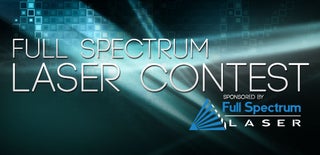
Participated in the
Full Spectrum Laser Contest