Introduction: The Bicycle Bubble Machine
Finally, be the star of commuter traffic! Make all the kids in the neighbourhood happy! Or just jealous! Engage in inspiring discussions with chemtrail believers! With the wind-driven Bicycle Bubble Machine drawing a dense stream of soap bubbles behind you, you too can bring peace and happiness back to the streets! Believe me: it's really great fun to go biking with this machine on a beautiful summer day -- most people are startled at first, as this thing really doesn't just make bubbles, but large clouds of bubbles, but soon everybody will smile at you, some people applaude, children will chase after you, or rather after the bubbles! And even if some people might think I am making a fool of myself -- an adult man on a bike producing a stream of soap bubbles everywhere! -- I still have a great time with this: after all, it's never too late to have a beautiful childhood :)
The Bicycle Bubble Machine is a bubble machine attached to the luggage rack of your bike. I actually found bicycle-mounted bubble machines on the net, but they all run on batteries. The Bicycle Bubble Machine only uses the relative wind created by riding your bicycle: a wind wheel will turn a wheel with bubble wands, which are blown directly by the relative wind. It works surprisingly well at a comfortable range of speeds, and with the jet-engine-like look the machines have, when one is attached to every side of your bike, it's an eyecatcher.
For this project you'll need 3D-printed parts which I published on Thingiverse (http://www.thingiverse.com/thing:950452). If you don't own a 3D printer, there are a lot of online print services to choose from. For the tank part your printer should be reliable enough to do a print of 7-10 hours, and its bridging capabilities should be at least somewhat okay.
The Bicycle Bubble Machine isn't hard to build, once you printed all parts.
Step 1: How It Works, and What Didn't
Most bubble machines work by turning a wheel of bubble wands so they periodically dip into a tank of bubble liquid. The Bicycle Bubble Machine uses the same principle, but the wheel of bubble wands is not driven by a motor, but by the relative wind created by riding your bicycle; and, unlike most bubble machines, the bubbles are not blown by a fan, but also by the relative wind.
My first attempt at building something like this was to combine the wind wheel and the bubble wand wheel in one printed part (see 2nd photo). While this looks charmingly simple, it has obvious shortcomings: the wind wheel will have less surface, and thus create less torque; the bubble wheels have to be shorter, limiting the tank size; and a small tank will result in more bubble fluid being spilled. As 3D printing enables you to just try out any crazy idea, I did just this and noticed, that this actually works, but you have to drive very fast to make the wheel overcome the friction of the bubble fluid, and the results are even at high speeds not satisfying.
So the idea was to make separate wind and bubble wheels and connect them with a belt, using a mechanical advantage to make the bubble wheel turn easily. This worked very well, and it's what this instructable describes.
Step 2: What You'll Need
First of all: you''ll need
- a 3D printer, or access to a 3D printer or online 3D printing service; my printer has a printbed diameter of 170mm and the largest part, the tank, nearly fills this, so it will work on most, but not on really small printers
There are some non-printed parts you will need:
- for the axles of the wheels I used 2mm welding wire, one that comes in rods rather than as a roll, which worked fine; you can take any reasonably stiff and straight axle with a diameter of roughly 2mm, as you'll probably drill out the axle holes anyhow. I also used tooth picks, which actually do work, but not for long :)
- a roughly about 5cm x 80cm board to mount one machine on each side, which will then be put onto your luggage rack; I used a spare one of 10cm x 70cm (the wind wheel mount protruding a little over the edge of the wood, because 70cm was too short); you should take less than 10cm width, however, as this makes some bubbles that move down less likely to pop; I painted the board to match the plastic I used for the printed parts
- small self-tapping screws (so your plastic doesn't break)
- small wood screws
- elastic ribbon (the stuff that makes your knickers hold, I used 8mm wide black)
- sewing stuff: needle and thread, fixing pins
- a small drill (like 2.5mm) to drill open the holes for the axles, as many 3D printers will not make the holes dimensionally correct
- screwdriver and the like
Step 3: Print the Parts
You will find the parts here in the downloads section. Printing this will take some time, mainly due to the tank.
Print one of every part, two of each clip. Print either two 3mm spacers or one 6mm. If you want to have the bubble machine the way I have it (one left, one right, "jet engine look"), you'll have to print everything twice.
As for the slicer settings:
it is very likely that you'll need a raft to print at least the wind wheel; on my (probably badly calibrated) printer I also needed a raft to print the tank. Any reasonable infill will do. See below for more considerations regarding the tank.
I printed this in PLA. After letting the Bubble Machine stand in the sun for some hours (yes, stupid me), the bubble wheels deformed, which actually is a specific PLA problem -- I replaced them with ABS printed ones, where this does not happen, and which also makes them more robust. If you have ABS, you should also think about printing the clips in ABS; this will last longer.
Please: try to print all the parts in the orientation they have in my STL files -- the tank will not be fun to print otherwise and the clips are oriented to be more robust due to layer orientation.
Printing the tank
The tank should be as solid as possible so it doesn't leak bubble fluid. My first tank with 20 % infill, two perimeters and two top/bottom layers leaked -- it didn't render it unusable, but it got soapy on the outside and if you left the tank full at evening, there wasn't much fluid left the next morning. I then did three perimeters and four top/bottom layers, which made it better. Besides a slightly higher extrusion factor, a very slow perimeter speed (up to 30mm/s) will help to make this more water-tight -- but as it takes 7 hours to print even with good speed, you might also just consider coating the tank, like with an epoxy or some other water resistant glue. A higher infill might also help getting things waterproof.
For the tank, you should enable support "from printbed only", not elsewhere! This is because, inside the tank, there are bulkhead walls to prevent sloshing effects, which act as support also, but having additional support inside the tank will make it store less fluid, keep fluid in dead places and will be a mess to remove; but you will need support for the mount, so enable "support from printbed"
The tank will need bridging (mostly about 10mm) in the slanted area that begins at a Z-height of about 40mm; give this good layer cooling, if you can, but it should work even without.
Other parts
Remove supports; for the support from printbed that it generated inside the tank above the refilling hole you best take a needle-nose plier. Take care to remove as much support as possible from the part of the tank where the wheel will be mounted - it should move freely.
Step 4: Mount the Wind Wheel
Start with mounting the wind wheel on its mount (that part with the long hole at the bottom for adjustment). you can ignore the small ring you can still see on the photo, as wheel and pulley will be fixed using the self-tapping screws.
You will mount parts in this order: small pulley, optional washer, wind wheel mount, optional washer, wind wheel (see photo). Cut your axle of choice to a length so that it doesn't protrude too much to either side. Now check that the axle will move freely in the hole in the wind wheel mount -- if it doesn't, drill open the hole with a small drill (for my axles of 2mm diameter I used a 2.5mm drill). Now press the pulley onto the axle (if it won't fit, use the drill too), then if you want (may make movements better) a washer, then the mount so that the foot is on the pulley side, optional washer, then the wind wheel (again, if it won't fit, use the drill).
Now, the pulley and the wheel are supposed to be fixed on the axle so they will always rotate together. Screw in the self-tapping screws through the small holes on the side of pulley and wheel shaft until they press on the axle just enough to fix things. If your printer was precise enough so small nuts will fit into the corresponding pockets, you can also use M2 or M3 screws through captive nuts here, but it really isn't necessary.
The wind wheel is supposed to be mounted on the end of the board. Use two wood screws to screw it to the board. Don't screw them too tight, as you might want to do a small adjustment later for correct belt tensioning.
Step 5: Mount the Tank and the Clips
Now that the wind wheel is mounted, you can attach the tank and the clips. The reason you mounted the wind wheel first is because you'll want to attach the tank to the board as much to the outer edge as possible (where there is a better wind), but not so near it will collide with the wind wheel. Attach the tank with two to 4 screws to the board, so that it still has a few millimeters distance to the wind wheel.
The clips (they're designed for luggage racks from 10mm diameter tubes, very common in my country, tell me your diameter if you want a different one) should be positioned on the bike so that you can later mount the machine centered on your luggage rack as far behind as possible. Mount the clips with wood screws so that you will later first clip in the clips from the side (see photo), then push down the other side until it clips in. See the beginning of my video to understand what I mean.
Step 6: Mount the Bubble Wheel
Now mount the bubble wheel, similarly to the way you mounted the wind wheel, fixing the large pulley and the bubble wheel with self-tapping screws to the axle. Correct order is: large pulley, optional washer, outer axle hole of the tank, two 3mm or one 6mm printed spacer, bubble wheel (with the shaft facing away from the pulley), inner axle hole of the tank (see photo).
Again, check that the axle rotates freely, but the bubble wheel and the pulley are fixed so they always rotate together.
Step 7: Mount the Belt
You're nearly done!
While originally I wanted to use tooth belts for this machine, I found that elastic ribbons also work -- they're much more readily available, and they're much easier to connect to a loop of a custom diameter. The pulleys can be used with a GT2 tooth belt, if you want to go for that; I kept them when switching to elastic ribbon, as the teeth of the pulleys provide good friction.
Before cutting the ribbon, wrap it around both pulleys to estimate how much you'll need; add some centimeters to it before cutting.
Now take the ribbon and form a loop around both pulleys, temporarily fixing it with two fixing pins. You will have to find out the right belt tensioning: if tension is too high, the axles will be skewed, leading to a much too high friction, and nothing will move; if tension is too low, the power will not be transmitted over the pulleys. The correct tension will be much looser than you would think at first: just try around with the fixing pins, until moving the wind wheel with the fingers will move the bubble wheel without noticing too much friction.
When you've found the right tension, use needle and thread and sew the loop together; then shorten any overlapping piece of ribbon. Mount the belt; probably it will not have exactly the same tension you aimed at while pinning it -- just adjust by moving the wind wheel until tension is right and only then tighten the screws in the wind wheel's long hole. Test a last time if everything moves freely.
Step 8: Fill It and Have Fun!
Fill the tanks with bubble fluid -- there are differences in quality and I like to use good fluid; you can also mix it up yourself and experiment with different recipes. Close the tank using the printed cap.
Now is the time to test your Bicycle Bubble Machine. It will take some meters at a comfortable, not too slow speed until everything rotates freely. If it doesn't work, chances are that belt tensioning is the problem and you should get back to the last step. Also, check that both wind and bubble wheel are rotating freely and wheel and pulley are both fixed so they always rotate together.
As you can see in my video, the amount of bubbles may vary, but this machine does make really a lot of bubbles at the right speed. So, when you're fast, bubble fluid may be empty sooner than you think; I like to fill half a litre of bubble fluid into a water bottle and keep it in the water bottle holder of my bike.
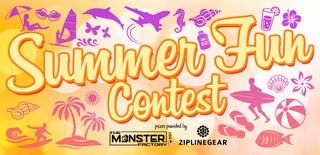
First Prize in the
Summer Fun Contest
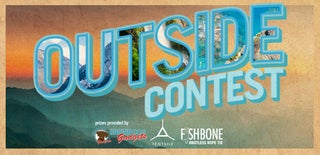
Participated in the
Outside Contest