Introduction: The Lazy Worker's Safety Equipments
Being a Do It Yourself guy, I am passionate about getting my hands dirty building different stuff. The feeling is so satisfying when that thing or projects ultimately works in front of you. Some time things get messy and you need to work a lot and things might get tiring.
Well well well !!!! not any more ...... As in this instructable we are going to modify some of the safety equipments that are laying around my workspace for quiet a while and add some useful features to them so that we can squeeze a lot more juice out of them instead of just having safety around the workspace....
The basic idea is to put features that will help the workers or DIYers to be more productive at the job site and providing them a bit more comfort with putting the following feature in safety helmet and Air muffs.
Features
- Headlight
- Retractable safety glasses/smartphone holder
- Air cooling
- Sound proof head sets
- Mobile charging port
- Dual set of drinks
- Rechargeable Battery
- Popcorn/Chips flask
So guys its time to show some action...... Lets get building....
Step 1: Required Materials and Stuff
The material required for this project is easily available at any hardware depot having a bunch of basic safety equipments and some of the old computer hardware.
The parts that i have used in this project are listed below:
- Safety helmet
- Air muffs
- Road traffic safety cone
- A pair of drinks
- A 12v PC fan
- A pair of speakers(small ones will do the job)
- A pair of antenas from old radios.
- A 12v LED light
- A 12v charging circuit used in automobiles
- Lithium pollymer cells
- Standard 5mm male/female charging jacks
- Black spray paints
- Safety Jacket
- Mobile charging chord
- 3.5mm audio chord
- 5mm thick plexi glass sheet
- Some electrical wire
- 2.5inch UPVC pipe
- A 50ml syringe
Step 2: List of Tools
This is a simple project in which tasks can be performed by using various tools. The tools that i am listing below are the ones that I have used but its not necessary to use the same tools but whats important is to get the job done....
The list of the tools used are:
- A cordless drill machine
- A bunch of drilling bits
- Multiple pliers
- Soldering Iron
- Hot glue gun
- Round shaped file
- A miter saw
- A set of hole saw
- etc
Step 3: Cooling Fan
No more sweating on the job site. Well keeping that in my mind i have mounted a 12v DC fan that is used in our personal computers.
The mounting process is straight forward. First i have cut down a circular piece using a hole saw. The edges are then sanded and then the fan is mounted using four cut screws.
Step 4: Drink Holder
I have decided to put a pair of holders at the rear side of the helmet. These holders are designed to hold a pair of soft drink cans but they can also be used to put up anything near to that size as the holders are flexible enough to adjust as per requirement.
These holders are made out of 2.5inch UPVC pipe cut down to 2inch in length. Since the diameter of the pipe is smaller that that of the cans, so it helps to grips the cans tightly. Both the holders are dry fitted and then spray painted. A pair of holes are drilled which acts as the mounting using 3mm nut bolts. As the paint dried both the holders are then mounted using nut bolts.
Each bolt is cut down so that there is good head room left inside the helmet.
Step 5: USB Charging Circuit
On top of the helmet I have added a USB charging port so that I can charge up anything (5v devices) using a USB cord.
For this purpose I have used an old 12v auxiliary car mobile charger. The reason behind this is that the battery pack that is going to be used is of 12v which is necessary to drive the cooling fan.The circuit is first disassembled, and i have removed the old input connectors, replacing them with a pair of wires which will go directly to the battery pack now and can be operated using a simple switch. Afterwards, the circle is enclosed again and mounted on the helmet by drilling a hole in the front. The circuit is then mounted in place using a cut screw.
Step 6: Head Light
I have used a 12v LED light to serve as a headlight for illuminating the workspace if needed. I have decided to mount everything such that it is easily replaceable in case of failure. Since there is no way that i can mount this light on the helmet without damaging the light . I have attached a custom made adapter for this purpose.
This adapter is made using a 50ml syringe. The rear side is cut down,painted and then glued to the light using hot glue. A pair of holes are drilled on this mounting and helmet which serves to mount the head light on the front of the helmet.
Step 7: Battery Pack
To power all the utilities, a 12v battery pack is made out of an old out of order cordless tool battery pack. The cells are lithium pollymer and thus offers a very good power to weight ratio. Each of this cell is rated at 2200mAh which mean that the battery pack when configured in series will be capable of supplying 12v at 2200 mAh for one hour.
After soldering all three cells in series a pair of wires are soldered to positive and negative leads.The terminals are covered with two strips of black tape and later the battery pack is covered using a heat shrinking film. The battery pack is then glued to the rear side of the helmet using hot glue.
This means that it can run the whole setup i.e headlight, cooling fan and the mobile charger for 2 to 3 hours on a single charge. The battery pack can be charged using a 3s lipo charger in less than 30 minutes.
Step 8: Wiring Thing Up
The wiring of the whole setup is straight forward. First, I have drilled three small holes just above the headlight to mount toggle switches and just below them is a bit bigger hole to mount the charging port to charge the battery pack.
The three toggle switched are used for switching of charging circuit, headlight and the cooling fan. The negative battery terminal is soldered to the centre of each of these switches. The other terminal on the switch is soldered individually to all three units(i.e charging circuit, headlight and the cooling fan).The positive leads of battery is directly soldered to all three positive leads of the units.
Both positive and negative battery terminals are now connected to the charging jack. Note that the middle connection is these charging jack is supposed to be the positive terminal white the side connection serves as the negative terminal.
Step 9: Headphones
The stock ear muffs are modified to not only serve as noise reduction equipment but you can also use them to listen to music using a 3.5mm audio jack.
I have used a pair of old speakers that i have got from some old computer scrap. Both of the are in good condition. Each one of these sparkers are then mounted in ear muffs. The mounting base is made out of 3mm plywood sheet. This allows me to neatly mount the speaker using four screws inside each muff.
Now both the speakers are wired using an audio cable. The wiring is quiet simple. An audio cable has three wires. Black one for the ground which is common connection for both speakers. the rest of the two serves as the audio signal for right and left speakers respectively.
I am not using any kind of amplifier because these speakers are sufficient enough for use in headphones while being powered up directly from a 3.5mm jack.
The sound quality is flawless and they are quiet loud at maximum volume. Well I have made some good quality headphones as cheap as dirt!!!
Step 10: The Safety Glasses/Smartphone Holder
The safety Glasses are totally custom made. The reason behind this is to not only serve as safety glasses on job site but when you are having some rest these glasses can serve as a smartphone holder. Since you need a minimum distance of 25cm (Human eye minimum focal length) to view anything clearly which is made possible using the legs made out of old radio antennas so that glasses are extendable.
The front plate is made using 5mm thick plexi glass sheets. A pair of holes are drilled at the top corners in which antenna legs are glued. The other end is mounted on the helmet using 3mm nut bolts on each side. A small bracket is glued to each side to act as smartphone holder.
The best part about these safety glasses is that they are not only extendable but they can also retract above the head of the helmet. So the final foot print is quiet confined.
Step 11: The Popcorn Bucket
The road safety cone that is lying in my workshop for quiet a while is now being used as a snacks holder for my lazy breaks.
Step 12: Time to Show Some Laziness!!! (End Results)
Finally the project is over and the end results are quiet good..... much better than what I have expected.... all the feature worked out nicely specially the retractable safety glasses/smartphone holder.
On a single battery charge I am able to use all the available features for up to 2.5 to 3 hours.
Now its time to lose up and have some snacks.
If you like this project then don't forget to vote it in the LAZY LIFE contest.
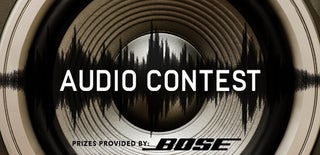
Participated in the
Audio Contest 2017
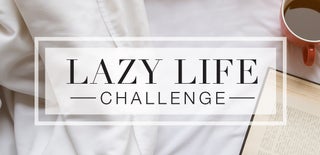
Participated in the
Lazy Life Challenge