Introduction: The Sewingmachine Scrollsaw
This project aims to design and build a scrollsaw based on a sewing machine.
For months I had an old sewing machine standing in the corner of my workshop, not really knowing what to do with it. It had been thrown out by the previous owner because it didn't really work anymore. The most important components, however, still functioned. I hoped I would be able to fix it.
But, whilst taking a closer look at it the other day, I figured out two issues about it:
- I couldn't find the sources of its many problems.
- I actually don't need a sewing machine.
A scrollsaw, on the other hand, was something I could find use in.
All materials used in this project are extracted from the sewing machine or is scrap wood.
I don't suppose you do have the exact same sewing machine, so I'll be a bit more general with the instructions: no measurements or dimensions. Not that there ever were any..
This project takes about a weekend.
Watch me explain it:
Step 1: What We've Got
Let's start out with disassembling the machine. I'll remove all components, I wouldn't need.
It is important not to destroy any of the components, since they might come in handy later on. So put away you saws and hammers, and get on about this with screwdrivers and time.
I was surprised about the inside. This thing is like a clockwork! And build to survive an atomic attack.
Everything is shiny stainless steel or molded aluminium - rarely plastic. Thanks to the rather modular design of the machine, it will be rather easy to disassemble the parts not needed, which is like 90% and quite allot.
The mechanism for the needle will stay, as well as the drive shaft and the motor. The presser foot and its lifting mechanism will later be used for the other end of the cutting blade.
Step 2: Fixing Problems
This sewing machine was able to do quite some fancy tricks and many sewing-patterns. I do, however, just want to cut my wood in straight lines (A zig-zag cut might be interesting though).
The head, which holds the needle mechanism, is tiltable, so the needle can stitch in the mentioned patterns. As you can see on the first picture, the tilting is controlled by the arm, coming from the top-right and mounted to the head in the center of the picture. I replaced this arm by a little metal plate so the head is fixed. You might run into similar problems with other sewing machines as well. I was lucky that there was a threaded hole nearby, and that I found a fitting piece of metal elsewhere in the machine.
Step 3: The First Steps Towards a Scrollsaw
The mounting for the needle turned out to be quite useful. I could actually mount the blade with it.
It wasn't, however, much of a use where it was. I had to put it to the top of the machine in order for things to work as I wanted them to. But that was rather simple: A single screw held it in place, and I could as well mount it on the other end of the rod.
The rods position is adjustable, so i could lift it slightly in order to get it to run freely.
Next off, I had to build the frame the table would rest on. The solid aluminium frame was perfect for drilling the required holes. It didn't take long 'till everything was in place. It is not important to work super precise here, but if you can, do it. The most important thing is, that it is level.
Extra support might be needed, as was it in my case. A vertical bar was added underneath the frame.
Step 4: The Table
A piece of 30mm scrap wood would serve as a table. A router was used in order to make space for the mechanism underneath the table. I wanted to get the mount for the blade to move as close as possible to the surface of the table, resulting in enough working area above it. Also I rounded the edges, just for esthetic reasons.
You don't have to use a router. A big drill works just as well for removing material where needed.
Next off, I added two hinges to the frame. These two pieces are the only parts I had to buy. 50c/piece in a local hardware store. They will serve for the tilting mechanism. It is important to mount them as much as possible on a line with the mounting of the blade.
Step 5: The Tilting Mechanism
A hinged arm used in the sewing machine would do well for the tilting mechanism. I had to drill a hole into one end, so I could mount it to the table with a single screw.
A block of hardwood has been added right underneath the frame. Subsequently, a slot has been cut into it using a saw. The arm from the table will fit right into it.
Next off, I took a knob from the sewing machine and fitted a short piece of 8mm threaded rod to it. Using a 7.5mm drill I could drill a hole into the guiding block, which would allow a thread for the 8mm rod to be cut by the rod itself. This allows the knob to adjust the pressure on the arm, fixing the tables position.
Step 6: The Arm
In order to fit a arm, I had to cut a slot into the table so it could fit in underneath it. If I would have known this before, I would have left more room in the frame underneath the table, so the arm could fit without having to get out the router again. It is important that the arm is stable and mounted well to the rest. Use both screws and glue here!
Next off I did cut out the rest of the arm from a 40mm piece of English oak. I did, however realise that there was a natural crack in it. I filled it up with glue and added screws in order to support the material here.
In order to find the right height for the arm, you'll have to do a bit math. How long is the blade, how much stroke is there?
Step 7: The Receiving Mechanism
The mechanism on the arm is rather simple. A spring will hold the blade on tension. Initially, I wanted to use the spring from the presser foot, but it was too hard, so a softer one came in use. The rod from the presser-foot did, however, stay.
After having figured out how this all will work, I had to drill a hole for the rod. This hole has to be precisely above the lower mount for the blade, as well as perfectly straight. Also, it has to be exactly the same diameter of the rod. In my case it turned out to be 7.8mm in diameter. A 7.9mm drill was all I had around, but it did the job just well.
A little metal arm was then mounted to the rod. This will be useful for avoiding the rod to rotate around its own axis.
A 3mm rod, as well from the sewing machine, serves as guide. In order to make it mount well to the arm, the rod itself served as a drill for the hole. Just roughen one end of it and mount it to your power drill. Now 'drill' it into the wood and unmount it as soon as it is deep enough. Rock solid!
Give the mechanism a bit oil so it moves nice and smoothly.
I was lucky that the presser foots rod was flattened in one end and that a threaded hole had already been drilled into it there. A simple screw with a little washer will mount the blade just nicely.
Step 8: Finish It Up
The motor of the sewing machine was, luckily a 230V motor with 60W. Although the power led to a concern, I've chosen to give it a chance, which turned out to be a good idea later on. The electronics of the original machine were surprisingly simple. I didn't have the pedal of the sewing machine, but it turned out that maximum power was just right. And the light bulb from the sewing machine wasn't needed either, since it wouldn't be able to stand the vibrations the scrollsaw would make.
So, I just connected the motor directly to a cable with a power plug.
As one of the last steps I had to mount the blade.
Well... yea..
Although I made sure that I could mount the blade before I build the frame, I didn't think about this during the build. So it was essentially impossible to access the mounting mechanism underneath the table.
A chisel was utilised in order to carve a path for the screwdriver which would fasten the mounting screw. Now it works just fine, but I should have thought of this before.
Now that everything is as it should be, it was time to turn it on. You'll have to adjust the tension of the spring for the blade before it runs optimal.
But now I discovered a new problem: the arm is vibrating allot. And by that I mean allot. The entire construction was jumping around on my workbench like a kangaroo on speed.
The issue was the arms natural frequency which fitted to the frequency the blade runs with.
In order to solve that issue I've chosen to change this natural frequency by adding weight to the arm. Two kilos, to be precise. It is by far not the most beautiful solution, but it works just fine. And gives people something to wonder about.
Step 9: Final Words
So, well, it works!
It actually cuts very nicely, and even some of the thicker woods. It takes a while 'till you stop breaking blades all the time, but it isn't more difficult to use than most of the commercially available ones.
Next time I would have to build one of these, I would, however, use a different construction for the arm. Maybe even make it out of metal. I think that would solve some of the issues with it.
Apart from that, I'm rather pleased with it!
Feel free to ask any kind of question, I'll gladly answer them!
Also, if you liked this instructable, vote for it!
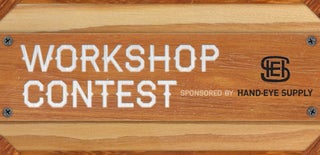
First Prize in the
Workshop Contest
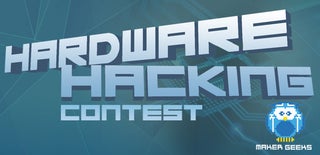
Participated in the
Hardware Hacking

Participated in the
Manly Crafts Contest