Introduction: Cross Cut Saw Track
Here's something you probably don't know about me ... I don't have a sliding miter saw. Here are some other things you probably already guessed ... I do have a regular miter saw; I don't really have the space for a sliding miter saw, let alone a second miter saw; I rarely have the need for a sliding miter saw, and I sure the hell don't want to pay for a sliding miter saw.
Looks like it's time to make a solution ... and then fix the fence on my large table saw sled.
Step 1: The Parts and Layout
You've probably seen a track saw, and they are awesome ... awesome at being expensive. You've probably also seen a saw board. In fact, I was making a conventional 4' one when I thought to myself, "Self, You need to make me a sandwich. But after that, you need to modify this design so we can cut up that sweet 12" wide board that the miter saw can't handle."
Sorry, I got distracted. We'll focus on the modification. 1/2" plywood which I cut down to 10 1/4" x 18". A strip of 3/16" hardboard cut to 1 3/4" wide (left it long). and another piece of 1/2" ply that was 1" wide and around 10 1/2" long (left it long).
The offset to the left of my circular saw blade is 5" so I scored a shallow line at 5 1/8" on a table saw. I'd recommend going a little more then the offset for a cleaner first cut (I know I should've gone with 5 1/4"). This shallow line is an alignment line and a trick I found on youtube.
Step 2: Glue and Screw the Rail
Slap on some glue, line up your rail with the shallow cut, and throw a screw in one end. Now dial in the other end and make sure you use a square for verification. Drive some more screws. I used # 6 1/2" wood screws and I predrilled the hardboard with countersinks. I trimmed off the excess hardboard at this time.
Step 3: Cut the Edge and Attach the Stop
The next step was to run the saw down the board against the rail. I didn't get a picture because I needed both hands. This makes the edge of the board parallel with the rail and custom fit to your saw (like any saw track).
Now the modification. We want to attach a stop to the bottom of this board and we want it to be square. Turns out my framing square ... wasn't so square, so it failed at its only job in life. I used a speed square, which actually did its job, but you could use a combination square or a framing square that doesn't suck.
I lucked out and this end was already square so I used my table saw fence to help me keep it all flush while I slapped on some glue, fired a few pin nails and then secured it all with a few wood screws. I trimmed off the excess on the tablesaw at this time.
Step 4: Brand It
You've probably noticed that I stencil my name on all my shop made jigs and that is because I want to (and my friends are thieves) ... simple. I don't do it to my tools because I never know when I might want/need to sell them and I don't use them on job sites. Anyway .. stencil, black spray paint, quick shot of lacquer on top so the boiled linseed oil doesn't pull the paint out (because it does).
Step 5: Ready to Cut
You're done and ready to cut that board baby!! This one is pretty accurate, but it's more for breaking boards down to more manageable sizes anyway.
What makes it better than the plastic version I could buy for $13? I can throw a clamp on this and the weight of the saw is supported the entire length of the cut, so Ican run the saw with my left hand while supporting the off cut with my right hand, which eliminates pinching/kickback risk I'd normally encounter. Also, since the offset to the blade is already calculated into the track, I don't have to measure my saw shoe every time (because I forget the offset) and add to my measurement, etc. Just mark my desired cut position and put the track there. It also didn't cost me $13.
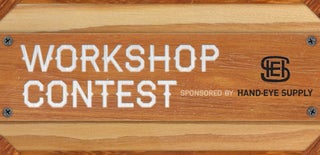
Participated in the
Workshop Contest