Introduction: TIG Weld a Broken Knife
A panicked scream came from the kitchen and thankfully there was no bloodshed. A kitchen knife had slipped and fallen on the tile floor.
Broken in two this would either be trash, a nice handled box cutter or a new TIG welding project.
I tried it as a box cutter and it was awesome, but I really wanted to practice TIG welding on stainless steel.
TIG is short for Tungsten Inert Gas. It is an electric welding process that heats an area of metal with an electric arc. The arc is shielded with an inert gas - in this case Argon. The gas shielding will protect the molten metal from becoming oxidized during the welding process. The power is adjustable and as you may guess, the bigger the spark, the deeper the weld. You can weld two parts together with capillary action pulling molten metal from both parts, or add a filler rod of suitable material.
I am quite new to TIG welding, so bear with me... this one is gonna be a bit rough.
Step 1: Set Up Welder
Set up welder according to the charts for the material. I set the welder to DC power and dialed it down to 60 amps.
Step 2: Clamp the Two Parts Together
I clamped the parts together and made sure the piece was grounded to the table.
Step 3: Tack Weld the Two Parts Together
A quick zap held these parts together so I could undo the clamp. No filler used in this step, but you can see how the metal has pulled in from the edge.
Step 4: Weld
My first pass wasn't that pretty so I did it twice. I learned that my power was fine for the thick part of the blade, but once I got to the thin stuff, it burned right up. Now I think of it as a battle wound.
This weld was given just a little bit of filler rod.
Step 5: Grind and Finish Sand
Grind off the lumps and finish sand. I used the rough and fine bench grinder and finished up on a belt sander.
As you can see, the discoloration gets sanded away in the process.
Step 6: Enjoy Your Knife
This knife has new life once again. It's a bit sharper now than it was before too!
There are still blemishes, but there is also a lesson learned and a skill practiced.
I did this project at the Tech Shop in San Carlos California.
http://techshop.ws
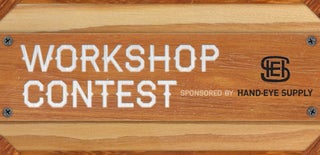
Finalist in the
Workshop Contest

Participated in the
Manly Crafts Contest