Introduction: Titanium Snow Saw
Here is a complete set of instructions on manufacturing a snow saw out of titanium. Before we start building anything, we need to start out with a list of tools and supplies used to complete this project. A water-jet or other CNC is required for cutting titanium. For this, I used a local waterjet service.
Step 1: Materials and Tools
Materials List:
Some sort of 2-Dimensional software that can read/write AutoCAD DXF files
A piece of metal, either sheet or flat bar, 36” long and 3” wide – I used titanium because I had access to it, and it has ideal properties for the final saw, but any 5000, 6000, or 7000 series aluminum between .080 and .125 inches thick will work pretty well too.
Scrap wood – 1/4-inch thick for the handle, you will need enough to fabricate the type of hand you want.
Some sort of fastener for holding the handle to the blade – I used two (2), 3/8-inch diameter by 1/2-inch long aluminum binding posts
Plasti-Dip – or some other sort of coating that will give a good grip through your gloves in cold, wet weather.
Tools List:
Sander – I used an angle grinder to sand both the wood on the handle, and add a finish to the titanium
Drill and bits for drilling holes for attaching the handle
Screwdriver –For attaching the handle
Wood Saw – I used a band saw, but any saw that can cut wood it fine
A few clamps
1 cheap disposable paintbrush
Now that we have a list of materials, we can start the build process of the saw.
Step 2: The Blade
The fabrication process of the blade is fairly simple. Start out with a design that you like in CAD, and send it to a water-jet or machine shop that can cut it out. I have attached my blade pattern to this page it is in AutoCad .dxf format. If you do not have AutoCad, there are several free viewers available such as Draft-Sight to view and edit my cad drawing.
Once you have your CAD drawing, you need to find the material to cut the blade out. I made mine out of some scrap 1/8th inch thick titanium left over from another project. Titanium is a very good metal to use for this saw, because it is lightweight, strong, and does not corrode. I built my prototype for this out of aluminum, and it worked well until I hit ice, then it bent. Steel is nice and strong, but it is heavy, and it rusts. If you do not know where to get metals like titanium, you can go to onlinemetals.com.
Once you have your metal and CAD file, it is time to send your saw out to be cut. I found a local shop with a waterjet, because I knew it would be the least expensive option with the best edge quality. I used West Coast Waterjet in Seattle, WA. They were very helpful, and I am very happy with the final blade.
My DXF file is attached to use.
Attachments
Step 3: Finishing the Blade
I used to my angle grinder and sanding disks to finish the blade. I just used 60-grit disks for all the blade work (polishing and sharpening).
On the pointed end, I used the 60-grit to bevel the edges to about 45 degrees, to put a decent edge on it (perfection is not required).
I then drilled the holes to 3/8” to fit my binding post fasteners. This took forever as titanium is very hard to drill. This is where I realized I should have modeled in the correct size holes for the posts for the waterjet to cut. This would have saved me time.
I then cleaned up the holes with the angle grinder by sanding off the burrs left from drilling.
Step 4: The Handle
Layout the two halves that will become the saw handle. The handle halves should be long enough to fit your hand (with winter gloves on), and about 1/8th of an inch wider than the width of your blade on the handle end.
Cut the two handle halves from 1/4-inch thick stock (plywood in this case) on your saw from.
Center them over the two handle holes on the blade, and drill the fastener holes through the handle halves.
Align the two handle halves together, and temporarily bolt them together with the binding posts (do not have the saw blade in the middle at this point).
With the handle temporarily assembled, sand the handle to even up the front and back edges (the other edges are sanded later).
Unfasten the paddles.
Step 5: Final Assembly
Using your binding posts, attach the handle halves to the blade. Because you oversized the paddles they should overhang between 1/16th and 1/18th of an inch over the width and the end of the blade.
Take your angle grinder or other sander, and sand the handles to be even with the saw blade on the top and bottom edge of the blade, and on the back edge.
Make sure that the handle fits the way you want it to at this point, if it does not go back, and sand it until it is good enough for you. It does not have to be perfectly smooth, as it will be covered in plastic.
Open up the can of Plasti-Dip and using a piece of scrap wood, stir the plastic.
Slowly dip your handle end of the blade into the can of Plasti-Dip.
Slowly pull the blade out of the can of Plasti-Dip.
Use your paintbrush to cover the rest of the wood that isn’t already covered with the plastic.
Coat the wood part of the handle with Plasti-Dip one or two more times per directions on the can, waiting 30-60 minutes between coatings.
Let your saw hang to dry for one or two days.
Go find some snow and build an Igloo!
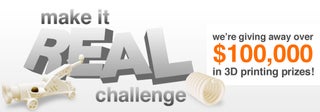
Participated in the
Make It Real Challenge
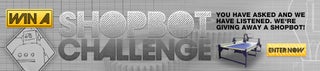
Participated in the
ShopBot Challenge