Introduction: Tricopter Frame Build
Introduction
I finally bit the bullet and made a start on building my tricopter. This instructable is for the build of the frame only, which is all that I have completed so far. As I get to the rest of it, more will follow.
I've never built anything like this before, but I've hoovered up all sorts of information from the web and made a start. I plan to use motors and other stuff used by other people who have made machines of a similar size and weight, that way there's a reasonable chance that it will fly - whether I can actually fly it is another story.
If you are planning to copy all or part of this build, please note that I have an impressive stock of spare screws and materials in my workshop, which means that so far this has cost me almost nothing for materials - you may not be as lucky. I also have a number of machines in the workshop that you may not have, especially the lathe and the milling machine. If you don't have access to machines like these, you may want to re-design bits of the frame to suit the materials and the equipment that you do have.
Step 1: Step 1 Design
Step 1 Design
Many of the designs for multicopters on the web are based on bits of wood and lots of zip ties and gaffer tape. While these undoubtedly work, it seems to me that it would be best to build it with as much precision as possible so that the machine is well balanced and the control computer doesn't have to work too hard to keep the thing straight and level. I decided to build the main three arms from some 10mm square alloy tube that I had lying around, and the plan is to run all the wires inside these tubes to keep the whole thing tidy. The length of the arms was determined by the material that I had, I ended up with the front two at around 350mm long and the rear one around 310mm.
I also decided that the landing feet would be best positioned at the ends of the arms to give less chance of tipping over on landing than a helicopter style skid arrangement. However, with all the weight of the batteries in the centre, a hard landing would put a lot of force on the three arms, so I included a bracing rod underneath each arm to make the whole thing more rigid.
Low weight is important, obviously, so all of the materials (apart from fasteners) are all aluminium and fibreglass sheet. The last thing you want is for anything to come undone in mid air, so most of the screws have nyloc nuts to stop them from vibrating loose, and those that screw in to a tapped hole are secured with lock washers and/or thread locking compound.
The part of a tricopter that seems to cause builders the most problems is the tail rotor swivel - there's probably a proper term for this, but the rear motor needs to be able to pitch left and right in order to steer the thing and keep it pointing where you want it to go. Its important to have no slack in this mechanism because it needs to respond instantly when the flight controller decides that its time for a change, and any slack will cause a delay - I've never flown one of these beasts, but I would guess that slack will cause the whole thing to over-correct and cause a potentially fatal oscillation. There are various ingenious ways that others have used to build this part, I used a spare chunk of alloy bored out to take a pair of miniature ball bearings, and the servo to tilt the motor mount is mounted underneath in between the landing feet.
Step 2: Step 2 Tail Rotor Swivel
Step 2 Tail rotor swivel
The first part is the tail rotor swivel, since the size of this determines a number of other dimensions.
The plate that the motor itself will mount on is made from 3mm alloy sheet, hacksawed and filed to shape, and then the two ears hammered down to make a flat U shape. I set this up on the milling machine and machined the inside and outside of the ears flat and cleaned up the top and bottom faces with a fly cutter to make sure all was flat and square. I cut a piece of 12mm square alloy bar to fit in between the ears and drilled and tapped the ends of it for a couple of M4 screws, then drilled a 5mm hole across exactly in the centre of the face that points towards the bearings.
The bearings are held in a piece of alloy rod around 19mm diameter out of my junk box. I machined flats on either side of it to give flat faces to mount it and bored it out to 8mm diameter to suit the miniature ball bearings. A M5 cap screw through the bearings, with a brass sleeve in between to stop the bearings getting crushed, then a brass washer under the head of the screw, and another pair of these between the bearing housing and the motor mount plate, stops the bearings from being pulled out of the housing. Assemble the motor plate on to the cap screw, and tighten up the nyloc nut to clamp the screw firmly to the plate and free to swivel in the bearings. For those of you as paranoid as me about things coming apart in flight, a few tiny drops of super glue or bearing lock on the outside of each bearing will hold them in the housing, but note that these bearings are very small and too much enthusiasm with the glue will give you a swivel that doesn't, and which can only be dismantled with a large hammer.
The swivel assembly is held between the two parts of the landing foot. This is made from fibreglass sheet, the two parts clamped together and machined on the mill to give a neat finish. I cut openings in the feet to reduce weight a bit, easy with the mill but more difficult if you don't have one. Two M3 screws each side hold the bearing carrier to the fibreglass, and two more M3 screws with lock nuts hold it to the end of the tubular arm.
If you want to run the cables inside the tube, you will need to machine a slot at each end so that the wires can enter and exit in a neat way and avoid the possibility of a screw or two cutting into a live wire. If you don't want to be bothered with this, the wires can be simply strapped underneath the arms with small zip ties.
The steering swivel is moved by means of a servo. My plan is to mount this vertically between the fibreglass landing feet, and pushing/pulling the motor plate by means of two ball ended rods. I don't yet have the servo, but I know which on I'm going to use, and have all the dimensions needed. The servo will need to be screwed in place, so I have cut a nylon block at the top which is screwed to the fibreglass feet with M3 screws, and which is tapped ready for the M3 screws which will mount the servo. Once I have the servo, I will add a similar block at the bottom.
The mounts for the ball ended rods are screwed to small right angle brackets fixed to the motor plate, and they will screw directly into a bellcrank lever on the servo. The rods came from an earlier adventure into scratch built radio controlled cars, and are adjustable for length.
Step 3: Step 3 Centre Platform
Step 3 Centre platform
This is pretty easy. It can be any shape you like as long as it has enough room for the radio receiver, the flight controller and the battery, as well as space for all the many wires that will make a fine nest there. Mine is made from 2mm thick fibreglass sheet, the only materials I have bought so far :-)
I chose to make the design so that the arms are all at 120 degrees to each other. To make sure that they are accurately positioned, I clamped the top and bottom fibreglass plates together with screws and machined to overall shape on the mill. Then mounted the plates on to my rotary table and drilled the mounting holes at exactly the right angles.
The flight controller that I plan to use has a small display screen and a number of buttons to change the various settings on the top, so my original plan to mount in in between the two plates would only work if I cut a sizeable hole in the top plate. I decided instead to mount it on top of the upper plate and fit some kind of canopy or roll bar to protect in case of an inverted landing. The receiver, power distribution and other wiring arrangements will live between the plates, so I also machined a couple of slots in the top plate to run the wires from the controller down into this space.
I plan to hang the battery underneath the platform for easy access for charging, not sure yet how to do this but it may involve zip ties and/or velcro
Step 4: Step 4 Crash Braces
Step 4 Crash braces
I'm expecting some pretty heavy landings, and don't want the inertia of the heavy battery to damage the arms, so there are crash braces underneath each arm to provide some additional strength. These are made from 4mm diameter alloy rod and the weight is negligible, and because the forces on impact will tend to pull the brace rod I'm hoping that these will be man enough for the job. Depends on how hard the crash is, I guess..
There are brackets made from 15mm alloy channel screwed underneath the centre platform using the same screws that hold the arms in place. Each bracket has a short alloy rod mounted across the channel and fixed with a M4 screw either side, and a 4mm hole drilled across the rod provided a mounting for the brace rod. The rod is locked in place with nuts on either side of the rod.
The same arrangement is used at the outboard ends of the arms where the brace rod is fitted to the highest point of the fibreglass landing feet to give the best angle.
Step 5: Step 5 Motor Mount Plates
Step 5 Motor mount plates
Each of the remaining two arms needs a plate to mount the motors to, these are made the same as the steering motor plate from 3mm alloy beaten into shape with a hammer, the inside and outside of the ears machined on the mill as before to ensure a snug fit. The ears are drilled and the plate bolted to the end of the arm with one screw going across, and another vertically, nyloc nuts on both of these.
After mounting the plates to the arms, I set them up in the mill and fly cut both top and bottom surfaces to ensure that the motors will sit exactly at right angles to the arms. The motor mounting holes will need to be drilled exactly the same distance from the centre of the plane on each arm, so I plan to do this after final assemble and when I have the motors.
Step 6: Step 6 Final Assembly
Step 6 Final assembly
The last step before assembly is to cut the arms exactly to length, and drill the mounting holes in the alloy tubes using the fibreglass plates as a template.
I used some plastic spacers from the junk box to maximise the room in between the two plates, as I'm guessing that there will be a mess of wires in there and the more room the better. Also, the lower the bottom plate sits, the better the angle of the crash braces.
I weighed the whole thing on the kitchen scales and as built it comes in at 460g. Tricopters this size seem to average around 750 - 800g in ready to fly condition, so I have around 300g available for the battery and motors - everything else weighs almost nothing.
Step 7: Step 7 What Next?
Step 7 What next?
The next step is to order the motors, propellers, steering servo, speed controllers (these will be mounted at the outer end of each arm to minimise the wiring) and the flight controller. This will let me complete the drilling of the holes for the motors and run all the wiring, and mount the controller on top with some anti-vibration mountings - apparently the vibration of the propellers can confuse the gyros
Then I just need a radio and some kind of roll bar to protect the electronics and we're off!!
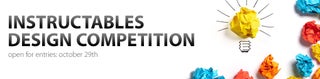
Participated in the
Instructables Design Competition