Introduction: Welding Plastic W/ Soldering Iron
First off, this was an experiment that ended with effective but unattractive results. I continue to try to experiment and improve the results. Also, please share your results if you try this.
Why: You can glue ABS with ABS/acetone glue , but what do you do for PLA? I had an idea to use a soldering as a welder while looking at a multi part mask print on Thingiverse. Ultimately, a strong weld could be much stronger than the rest of the print due to the larger area of solid plastic. I feel that this will work better than using other gluing methods depending on the requirements of the project.
I printed a case for my Smoothieboard last night that had warped a bit and figured this would be a great opportunity to test this process.
Step 1: Setup and Tools
Tools: Soldering iron with adjustable temperature.
Temperature: I started at 210 because that is what I usually use to extrude PLA. If you go to high, you risk burning the plastic. I ended up going up to 230 to get more heat into the plastic and did not burn it. I haven't tested the upper limit.
Work area: I used my helping hand to hold the project in place but other things could work.
Step 2: Weld Away
The goal of this process is to melt both pieces to be joined and the extra filament all at the same time to fill the gap and create a single piece of plastic.
The initial heat of 210 was not effective. I upped the temperature to 230 with slightly better results. I may test again with a higher temperature. Possibly using a temperature that can burn the plastic but moving fast enough to avoid the burning would work best.
Technique:
- 1.75mm filament: I first tried a short piece of filament. The filament was to thick to melt quickly enough. It worked alright when I melted it on to, not into, the seam and then went back and added more heat to the weld area to get a strong weld.
- Brim filament: I had a piece of filament from the single layer brim nearby so I tried that also. this was a very thin piece and melted very well. However, it was so thin that it was hard to hold straight and took a long length to add enough material to the joint.
- Ideal? I may try extruding a length from my .80 nozzle the next time i try this to see if that is a better size.
- 3mm filament. I didn't try but the 1.75 was way to thick so I wouldn't bother unless you have a different iron that can put more heat into the joint or find a better technique.
Results: The part is plenty strong. The welds are a bit ugly. I couldn't get the plastic to flow like with a traditional welder so the joints are a bit ragged.
Step 3: Possible Improvements
I have a few ideas for improvements.
Heated work area: Working with a heat gun or something to apply heat to the weld area would keep the weld from cooling to fast and may allow the plastic to flow for longer.
Preheat: Same Idea as above but preheating the joint with a heat gun and than keeping it warm.
Hotter Iron: I may try a higher temperature that could burn the plastic but keep it moving along quickly to get a better bead.
Larger Iron or different shape head: I have a cheap soldering iron/wood burning kit with several different shapes of heads. One with a flat triangular or teardrop head might work better to apply heat to a wider area. Unfortunately, I don't have a temperature control for that one but I'll see what I can figure out.
If I eventually find a good solution tho this I will make a better Instructible with more definitive guidance. for now this is still experimental.
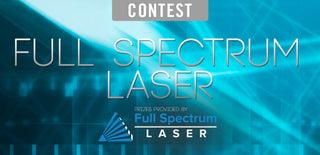
Participated in the
Full Spectrum Laser Contest 2016
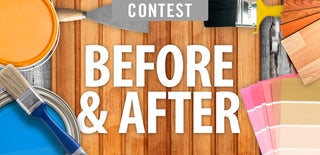
Participated in the
Before and After Contest 2016