Introduction: Wire Clamping Tool ( DIY )
As requested by r-philp, here's a write up of how I made my wire clamping tool. This is simply a loose copy of the Clamp Tite brand tool. It is not to scale and absolutely not my idea/design in any way. I built both copies from a photo in the Garret Wade catalog.
Step 1: Tools and Materials
Tools: ( Not pictured )
Files- standard set and jeweler's set
Drill press with vice ( I used a cordless drill in some of my steps but the steps can be done on the drill press )
Clamps
Dremmel with cut-off wheels
Hacksaw
Sandpaper- coarse and fine
Drill bits- 7/64" & 13/64"
Countersink bit
1/4-20 tap
Calipers and ruler/tape measurer
Small hammer
Marking tools
Materials:
1/4" I.D. aluminum tubing
1/8" ss rod
An old center punch ( I used a piece of 3/8" ss rod and turned my own nose piece )
1/4-20 ss all-thread ( Not pictured )
1/4-20 wing nut ( I turned my own from a large brass punch )
1/4" UHMW washer ( Not pictured. A regular steel washers might destroy your tool over time and regular plastic washers are too soft to hold up to the pressure of pulling the wire )
Step 2: The Hard Part- Drilling Holes in Round Rod
Don't cut anything to size yet, you can minimize waste.
To align the chuck on the press to the vice you"ll 1st have to chuck the rod to be drilled on the press. Once done, Bring the vice to the rod and close it onto the chucked rod without moving the rod. Finally, clamp the vice down carefully so it doesn't move on you. You'll have to repeat this step for every piece to ensure that you're drilling centered.
Using the 7/64" drill bit, set up and drill a hole about a 1/4" from the end of the all thread piece. It might help to file a small flat where the hole will start on the all thread. Reset the clamp, and using the same bit, drill about an inch from the end of the center punch or the 3/8" rod. Start drilling very slowly and watch the bit when it touches the workpiece, make sure the bit doesn't move to either side.
If you decide to make your own wing nut, drill a 13/64" hole an inch from the end of the rod in the same way as the other two pieces.
Step 3: Making the Body
This is a fairly straight forward step. First, score parallel marks on the aluminum tube with the calipers. Next, starting 3/4" from the end of the tube, with a Dremmel, cut slots on both sides to 2 1/2" long. Then, starting with an assortment of jeweler's files and working your way up to small standard files, open the slots to 1/8" and clean them up as much as possible without going overboard. Use the 1/8" rod as a gauge, sliding it up and down both slots together until you have a nice, easy glide with minimal play. The aluminum works easily, so this won't take long.
Once the slot is finished, cut the other end to 1/2" from the end of the slot and clean and de-burr all of the edges.
Step 4: Making the Nose Piece
*** Please note that using a drill in this manner could result in serious injury. I am simply telling you how I did it. I take no responsibility if you choose to use this method. ***
To make the nose piece, I chucked the rod on the drill and filed a shoulder where the taper ends. Using a file and some elbow grease, I turned the shoulder down so that it was about 3/100s of a mm larger than the opening on the body of the tool. I constantly checked my work and made sure it was parallel across at least a half inch off the shoulder. Once I was close to the desired measurement, I finished the shoulder with some sandpaper to get a smooth finish.
Once happy with the shape, I moved the piece into the chuck so that 9/16" of the shoulder was exposed. I then used a hacksaw against the chuck with the drill at low speed and cut the nose piece off cleanly so that I ended up with a half inch shoulder. To make assembly a little easier, I slightly chamfered the end on the shoulder and filed the tip left from cutting.
I used a file and sandpaper to shape the tapered end of my nose piece before making the shoulder, but it took allot of work which is why I suggest using an old center punch. For my original tool, I used an old 1/2" pin I found in a scrap pile. It ended up dictating the size of the tool which i thought to be too big for my needs.
I used the same method to shape the brass wing nut. If you're not interested in looks or want something easier, try your local hardware store for a regular wing nut. They're inexpensive and easy to find.
Step 5: Assembling and Finishing
On a vice, press the nose onto the body at the 3/4" side making sure to keep the hole and slot aligned. Be sure to go slowly to keep everything straight and stop as soon as the end of shoulder meets the tool body. It'll take surprisingly little pressure on the vise to bend the tool body at the slots and ruin it.
Next, sand down 4" of the 1/8" rod to 2.9mm and cut two 2" pieces. Starting with the all thread, drive your pin into the hole through the slot as shown in the picture until both side are even. The assembly should slide freely all the way through the slot. If not. pull the all thread all the way up to the top of the slot and gradually rework the it until you get a clean glide. Install the nose piece pin. If the pins are a little loose, use a little super glue on both sides of the pin.
On the tip of the nose, you need a small notch for the wire to cradle in while you're pulling it tight. A small triangle file makes short work of this. Just keep the notch parallel with your pins and centered on the tip. I made mine about 1/8" deep.
Finally, install the washer and the wing nut, bottom out the tool and cut the all thread to 1/2" above the wing nut.
Done! Go make some wire clamps. For instructions on how to use the tool, check out GeeDeeKay's instructable, https://www.instructables.com/id/Hose-Clamp-Magic/?ALLSTEPS. It was the inspiration for my instructable.
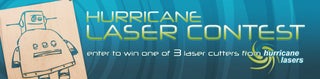
Participated in the
Hurricane Lasers Contest