Introduction: How to Make a Remote Controlled Robotic Hand With Arduino
This is my school project for the 5th year of high school (I'm Italian, we have 5 years of high school).
It consists in an artificial hand controlled by a glove with flex sensors. The artificial hand reproduces the movements of the hand with the control glove, wirelessly. The hand and the glove works both with Arduino.
I just wanted to share my work for everyone interested :)
This guide is still in development, sorry if some parts are not clear, I'll put some 3D images in future.
I'm sharing something about my project on my facebook page: https://www.facebook.com/Gabry295
Step 1: Materials Needed
I bought almost everything from https://www.sparkfun.com/, they have fair prices (I don't mean to advertise!)
Total cost: ABOUT 160$
Materials for the control glove:
• an elastic glove;
• LilyPad Arduino board (there are different versions, which usually only have 4 analog inputs, so pay attention and buy the one in the image): it works exactly like the classic Arduino UNO, so you can use even an Arduino Nano, but pay attention to the voltage needed;
• XBee module: for the radio communication;
• Shield to connect the Xbee module;
• 5 Flex sensors;
• 5 resistors: 47 KΩ;
• battery pack with 3x1.5 V batteries (Lilypad can be powered from 2.7 to 5.5 V, so 4.5 V it's ok);
• LilyPad FTDI adapter: to connect the LilyPad board to the PC and load programs with the Arduino IDE (quite optional, because you can use also the Arduino UNO board removing the ATmega chip, but it's tricky to make this kind of connection every time).
-
Materials for the robotic hand:
• a steel structure for the palm of the hand and wood for the fingers;
• Arduino UNO board;
• XBee module;
• 5 servomotors 5V powered (I used TowerPro SG90);
• a servomotor shield for Arduino UNO: to connect the servomotors I used the Robot_Shield from FuturaElettronica, which has also a switching regulator to power the entire circuit, but you can use any shield made for controlling servomotors. Link: https://store.open-electronics.org/index.php?_rou... ;
• Shield to connect the XBee module (I made an horrible one, but it's economic and I needed to make one small because of the size of the Robot_Shield);
• fishing wires;
• (optional) fihing sinkers, to secure the fishing wire, can be done also simply making a knot;
• 9 V Battery.
-
Tools needed:
• angle grinder (mainly to cut wood and steel);
• axial grinder;
• welding machine (with electrodes);
• drill;
• soldering station and solder;
• electrician's scissors;
• pliers;
• heat shrink tubing.
Step 2: Making the Glove
To make the control glove I suggest first to choose the right position of the different components, then connect everything with the proper length of wire.
To make an analog read with Arduino LilyPad you need to make a voltage divider, since that flex sensors don't work like potentiometers (they have only 2 contacts).
So following the scheme, first solder the 5 resistor on the LilyPad board, one side to the 5 different Analog pins, the other in common to the ground. Then solder the flex sensors, one side to the 5 different Analog pins and the other in common to the positive.
Then connect the XBee Shield: two wires for the power, the oter two for the signal. Solder the Tx pin to the Rx and vice versa.
Now you need the battery pack, and the glove it's done.
BE CAREFUL: don't power the Arduino LilyPad over 5.5 V and don't power it conversely (even if sometimes I did it by mistake... And it still works!)
Step 3: Making the Robotic Hand
This is the most complicated part, because you have to choose the proper materials to make the hand, but it can be also easy if you have the possibility to 3D print the hand (there are many different 3D projects on the web for printing hand parts).
I started making the fingers with cork, to find the proper structure for the movements, then I made it with a branch.
So make three wooden cylinder per finger, two of them with 1 cm over the normal lenght of your phalanx, needed to fit one piece into another.
Then with an angle grinder make the grooves to make the pieces fit together (see the images, you'll understand better).
You'll need some sandpaper to make the pieces curved, so that they can rotate.
Use a drill to make the holes for the hinge, then you have to make other two holes for the fishing wire, vertically, one towards the inside of the hand and one outwards. So when the wires are set at the top of the finger, when you pull the one inwardsthe finger will close, and when you pull the one outwards the finger will open.
The palm was problematic, beacuse I made it initially with wood and the thinner parts always broke. So I decided to make it of steel and I've had no problems.
Cut it and do some protrusions similar to those made for the fingers to fix them to the palm (see the images as a reference). Then use the drill to make the other holes for the fishing wire, the thumb will be tricky because it's not vertical as the ther fingers.
Afer making the hand, you need to make a support for the five servomotors and a support for the Arduino UNO boards. Be sure to choose the right position of the servos, so they don't touch each other while rotating.
The last part consists in connecting the fingers to the servomotors: fix the fishing wires at the top of the finger and make them pass through the holes; then, when the wires are at the bottom of the hand, turn the rotor (manually, without powering it) at his maximum rotation (180°) so that it's in a vertical position, then set the wire that closes the finger to the lowest hole of the rotor, for example making a knot; turn again the rotor at 0° (it's again vertical and the knot made before is at the top) then set the other wire (wich opens the finger) to the lowest hole of the rotor. Follow the last image in this step to understand better.
So, when the motor is at 0° (vertical) the finger is opened and when the rotor is at 180° (vertical again) the finger is closed.
Step 4: Circuit of the Robotic Hand
For the circuit, you can choose to use a servomotor shield for Arduino UNO (search on eBay or Amazon) with a XBee shield, or make a custom shield (I'll make one as soon as possible) with the XBee Module and the pins for the servomotors, and power the Arduino UNO by its jack port.
The DIY XBee Shield I made uses a 12 KOhm resistor and a 22 KOhm resistor, you can see the wiring in the pictures.
So I used what I had already bought before, but you can use everything that let you control the servomotors and the XBee.
The servomotors have 3 wires:
- yellow: signal (connect to a digital pin);
- red: power (+5 V);
- brown: ground (GND).
So now you won't make mistakes :)
I used the simplest type of servomotor, working at 5 V, with a rotary angle of 180 degrees (that's the perfect angle, we don't need more).
The USB ports of a computer can't give anough power to control 5 servomotors, so I suggest to use a 12V power supply to test everything and then use the 9V battery (Alkaline are preferred).
Step 5: The Programs
The program of the hand and the glove, with all description, are in links below.
REMEMBER: to load the program you have to remove everything connected to the TX and RX pins of the Arduino (in this case the XBee module), else the program won't load. Remember also to set the correct kind of Arduino in the IDE (LilyPad or Arduino UNO).
Links for the two codes:
https://codebender.cc/sketch:59559
https://codebender.cc/sketch:55013
Try this code to test the flex sensors on the glove: https://codebender.cc/sketch:56264
and this to test the connection between the Lilypad and Arduino Uno: https://codebender.cc/sketch:55014
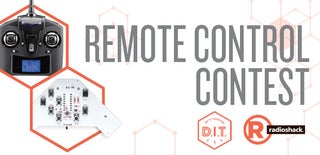
Second Prize in the
Remote Control Contest
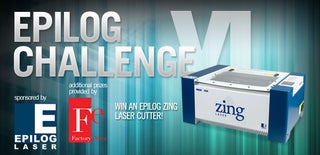
Participated in the
Epilog Challenge VI
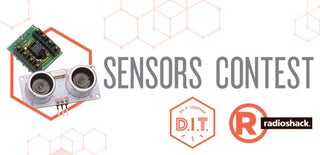
Participated in the
Sensors Contest
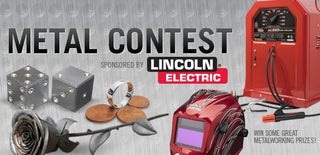
Participated in the
Metal Contest
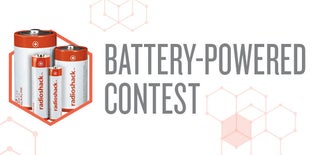
Participated in the
Battery Powered Contest