Introduction: Wooden LED Synced Headphones From Scratch
Why do they blink? Well I wanted there to be a unique effect that would make them stand out, and not just be wooden headphones. I've had people stare at me while I'm in the library, with faces saying "Wait a second, is it blinking to the music? Sweet I want a pair!"
I just want to say that I made everything from scrap pieces of wood, leather, acrylic, plastic, and foam with the exception of the electronics of coarse. I had no directions, just countless prototypes out of packing material and some rough measurements of Bose acoustic headphones. Making these headphones has been a wonderful experience for me and is one of my more successful pieces of art I have made and thats why I want to share them with all of you. Special thanks to my mother, father and Garry Cerrone for all contributing knowledge of their trades.
Step 1: Everything You'll Need and More!
- body: Any hard wood (Cherry) - 1" thick, at least 3x 8.5'' to accommodate two pieces.
- top ring: More hard wood (Oak) - 1.5'' think, at least 3x 8.5'' to accommodate two pieces.
- Plug:
- Even more wood (mahogany) - .25'' thick,
- Acrylic 1/4 thick or two .1/8" pieces glued together.
- Squishy donut:
- High density foam, can be purchased at fabric stores -1" inch thick, but go bigger because it is easier to cut down to have a little extra, plus it compresses
- Very thin soft leather or suede, I believe mine is 1/32" (I got a scrap from saddle maker at my moms store) you can purchase the color of your choice: Here
- A spool of upholster or ultra strength thread with extra wax coats.
- Headband
- Heat molding plastic sheets(ortho plastic) search amazon for "moldable plastic sheets"
- (1/4'' to 1/2'' BrassChicago screws) depends on thickness of plastic
- black 1/16'' cut of black leather
- spandex fabric for padded sleeve
- foam for padding
- use wax coated thread for leather stitching
-
Plug: 2x (blue) LEDs - 5mm, 3.7volt
- Electrical wire
- TIp 31c transistor
- alligator clips
- speaker wire
- thick stereo headphone wire
- 2x Stereo jacks
- Headphone splitter
- 3v battery
- Sewing machine
- stove top
- pan
- Jig saw
- miter box
- x-acto knife
- hand saw
- dremel
- chisels
- hammar
- needle nose pliers
- wire cutters
- flat pliers
- soldering iron
- at least 5 clamps
- wood rasps
- vice grips
-
Sanders
- barrel sander
- normal belt or electric hand sander
-
paper
- 120 g
- 200 g
- 300 g wet dry
- 400 g wet dry
- 600 g wet dry
- Gorilla wood glue
- 2 part epoxy
- Danish oil
- solder rosen core FOR AUDIO VERY IMPORTANT
- electrical tape
- masking tape
Step 2: Planing and Designing
- Measure size with ruler mark with the grid lines
- then use the marque tool to snap to the grid measurement
- use fill tool to color selection
- deselect and drag circle to gauge size of plug
- print to appropriate scale
- Use card stock or some kind of thick paper to cut out
main template: 3" x 4"
Plug diameter 1.75"
Step 3: Trace the Templates to the Wood
Draw templates on 1" inch thick hardwood, make sure the grain runs with the longer dimension. I drew it the wrong way first, but fixed it afterwards.
Step 4: Carving the Ear Cups
Step 5: Cutting and Drilling the Cups
Cut the Pieces out on the scroll saw. Try to keep the blade on the line to minimalize sanding.
Drill the hole
Find the center, mark it with an awl, then drill through with a small bit.
I used a 1.5" hole saw bit to remove about a 1.75" hole with it clamped in the drill press
Step 6: Oak Rings
- Use the red template to trace on the 3/4"oak
- Drill out a hole for the scroll saw blade to come through.
- Thread the blade and remove the center. Make this as smooth as possible for the inside will be hard to sand.
- Once everything is cleared out, move to the outside and cut.
Step 7: Attach Oak Rings to Cup
You can take a file to the outside of the ovals to true everything up. Move the ovals around until they fit best then dampen, glue and clamp.
Step 8: Rounding and Shaping Ear Cups
- Before you start rounding mark a fall off line that's the same height all around the cup.
- Try to blend the the rounding right before the line.
- I started rounding with some big toothed wraps and files. This takes a very long time so using a dremel is a possibility too.
Step 9: Plug Design
- Mark acrylic and cut out squares
- Frost both sides of each piece, I sandblasted them, if thats not a possibility, sand with 320+ grit paper.
- glue with epoxy and clamp to wood
- mark with circle template and mark the center on the wood
- sand to size on barrel and belt sanders
- drill out center based on the size and depth of LED. It should be flush with the bottom of the led, but not so deep that it punches through.
Step 10: Cut Heat Sink of the Transistor
The transistor at the original size doesn't fit well so the heat sink needs to come off. I don't think this effects anything because the circuit still works, and the transistor never gets that hot.
Clamp the transistor tight and saw back and forth with small hacksaw or serrated cutting blade make sure to cut all of the way through or it will snap.
Step 11: Wiring the Transistor
Both ears are slightly different, what I'm calling the left ear, has the jack receiver where the music plugs in. The right channel then goes over the top of the band and down to the right cup powering that circuit.
Step 12: Complete Circuit
Bend the wires around the 3v battery so it stays and makes a good connection. You can purchase little slides that hold the batteries that have solder ports. I never thought to use one until recently, and I ordered some off Ebay. i'll show updated pictures when they get in.
Step 13: Wire New Leads and Extract Speakers
- Take the headphones apart until you get down to the speaker where you can see the ports. Be sure not to take apart the protective fence around the speaker for you can easily break them for being careless.
- snip the red and the copper wires.
- Get a fresh strand of speaker wire from the spool. Make it a little longer than you think you need split , strip and twist it. Making sure that all 7 internal wires are intact before proceeding for this will diminish the quality of your music.
- Scrape any old solder off the speaker contacts with the soldering iron. Re solder making sure to use rosin core AUDIO solder for it needs that higher conductivity rate to transmit music well.
- Heat the wire and the contact plate then melt the solder by touching it to the wire and plate. Don't try to force solder on with the iron tip let the solder flow to the heat.
Step 14: Fit Circuit in Plug
push the led into place and rotate the speaker until the wire coils and press it lightly down. Cut a notch for the wire to pass through. feel free to cut foam and fabric to diffuse and insulate speaker.
Step 15: Construct Headphone Cord
I wanted to make one because more often than not these cords are flimsy and break easily. I got two stereo audio jacks from radio shack for pretty cheap and soldered them to a thick cord my physics teacher gave me. Its very simple to do, when you solder these make it quick and try to minimize heating of the soldering ports for they could come loose.
- Pass the wire through the hole of the correct ports (See pictures)
- Solder
- Snip excess
Step 16: Sewing the Donut
- cut a rectangular slice to set thickness
- trace the red template with a sharpie
- Cut out with scissors or knife
- cut a bevel on all edges to round the foam completely
This was much more difficult than I originally thought it would be and took a couple tries.
- Cut a rectangle to 3.5"x 6"
- Sew ends together leaving smooth side out (img.8)
- Wrap around donut
- Put a stitch on the top bottom and middle of both sides to hold the leather in place
- Work around connecting the sections and pull leather tight around foam but not too tight because it will deform the donut shape.
- you man need to trim the leather down a little bit as you go.
Step 17: Finishing and Treating the Wood
There are countless ways of finishing wood, depending on what you want. I thought about going for the the lacquered finish, but I don't like how artificial it feels afterwards. I wanted to preserve the wood, yet leave it somewhat open to feel and build a patina of its own. This is what I've done so far.
First things first is to sand these things till they glow. The trick to getting insanely smooth wood is not just using high grits it all starts with the lower grits. After this things are shaped go over them with some finer files to achieve perfect roundness, i.e. no bumps, or lumps. next get some 100 or 120 grit and a powered sander and go at it working in circular motions around the ovals. Do this until all traceable scratches, divots, and imperfections are removed. In between grits wipe with a rag to remove clinging dust. Keep working up the grits making sure that each one is properly addressed. The more care you give the better your final result will be. Once you reach the 400s and 600s its good to touch up by hand. Try to minimize strokes against grain for they will fog wood. Stop and wipe clean with dry cloth when reached desired smoothness.
I used tung and linseed oil, danish oil works well too, this strengthens and brings out natural color in wood. I think I used 4 to 5 coats. Instructions are different for each.
I have yet to put anything else on mine yet, but I plan on putting several coats of wax on a later date. I will upload pictures when I do.
Step 18: Headband Design and Bending Template
- The template needs to be bent smaller than a head, so measure a diameter of 6 inches with ruler then set a compass to 3 and draw a little farther past halfway on each side.
- cut out on a scroll or band saw
- sand lightly
Step 19: Bending and Constructing the Top Band
Plan out your top band and forks all in one mine was 2" wide on the band, 18'' long, forks were 4" wide and tapered to band. the top band cuts down to about 6''.
- Make a paper template for the forks, and cut it out. This way it's the same on both sides and looks the way you want.
- Now for the cutting and bending of the plastic. Get a cookie or brownie sheet and lay the non stick plastic down with a pretty high water line and heat it. The plastic should start melting around 150f.
- Draw directly on the plastic with a sharpie and heat the plastic so its soft and cuttable with a scissor.
- Get the template we made in the previous step and have it ready for when you heat (Sorry I don't have bending pictures of the band on the template). Once you have the strip cut to size and smoothed the way you like, take it out of the water and immediately wrap it around the template so that the forks hang even on both sides. Hold it to fit for a few seconds and then plunge it in ice water to quench the hot plastic and hold its current shape. When most things get cold they contract so the plastic should cling pretty tight to the template, making for good flex in the headband.
- Take the plastic off and make sure the flex and curvature is ideal.If not you can sometimes cut a second smaller piece of plastic to adhere and strengthen the curve.
- If everything is good mark where to cut the forks off, reheat and snip them. It's good to leave a little extra room on the forks, the top doesn't need to be as long as you think.
- Have your wooden pieces ready so you can use them as bending templates.
- before you bend the forks themselves get a scrap wide enough to accommodate the width of the forks. Make a S shaped bend to mold the forks to.
- heat and mold to the template you made in step 2. once its fully hardened move on.
- heat only the legs of the fork not where they come together to preserve structural integrity. It helps to run or dip cold water in the areas you don't want to change. Once you have selectively heated the legs drape the fork over the cup and lightly squeeze and hold in place making sure both sides are symmetrical. Dunk in ice water when reached desired shape.
- If your plastic gets banged up it helps to smooth with a wet spoon while hot.
Step 20: Attaching the Headband to the Ear Cups
Before you drill its best to attach the forks to the cups and make sure they are the same on both sides. I found some small brass screws with a smooth section towards the top so they can swing and move around. put a mark in the middle of both sides where the plastic meets the wood. Make sure the fork is far enough back so it doesn't stick above the edge. Pre drill the plastic and wood separately and screw in halfway to make sure it fits.
Tape drilled the forks to the band and make sure everything is the way you want it. Once its perfect mark where the holes will be. Select a bit according to the size of your hardware. Rest over a section of wood when drilling to get a clean hole. Remove tape and cups when done to paint.
DON'T PAINT THE UPPER BAND IT WILL BE 100% COVERED WITH LEATHER.
Plastics usually do best when sprayed, I happened to have some gloss black that works with plastic. WARNING this stuff takes at least 5 days for the extreme tackiness to subside. Don't be like me, I was in a rush to finish a portfolio for school. Have patience for it to dry fully or you will have to do lots of touch ups and it could get on the wood.
Step 21: Upholster and Finish the Headband
Its the home stretch, wrapping this thing. When leather is this thick and sewed this tight it is near impossible to turn inside out, so I sewed it on the outside. Measure the EXACT width of the band and make sure you have more than enough extra length to cover both forks at the end. You can use your average sewing machine but be sure to increase the stitch distance, and use a thicker needle.
IMPORTANT: Before you slide the leather on remember to pass the speaker wire though the leather sleeve so it will be on the other side to power the right ear cup.
Step 22: Attaching the Donut
Use some double stick tape nothing too permeant. I had these double stick dots that attached to wood pretty well, and pulled the donuts down tight. You could probably glue it with some epoxy and carefully clamp the leather.
Step 23: Finish
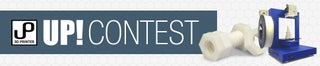
Grand Prize in the
UP! Contest