Introduction: Convert a Lawn Mower Engine to Steam or Air
This is an instructable on how to change the camshaft timing so that you can run a push mower engine on steam/compressed air you can usually pick up these engines really cheap or free
I am entering this instructable in the hack it! challenge and the mad science fair so so would love the vote's if you like it
Step 1: Tools
wrench or socket set
hacksaw
screw driver set
welder ( if you give the camshaft to a friend with a welder or someone who takes shop in school they should be able to do it with ease)
hammer (optional helps with stubborn things that get stuck)
Step 2: Strip the Engine
first strip the engine of all unneeded parts such as the carborator the muffler magneto etc. you need the spark plug left in.
Step 3: Draining Oil
first you need to drain all of the oil out of the crankcase.
Step 4: Crankcase Cover
now that the oil is drained its time to take the cover off
Step 5: Camshaft Removal
now that you have the cover off you should see the inside of your engines crankcase look for the big gear off of the shaft
Step 6: Modifying the Camshaft
now that you have removed the camshaft you need to modify it so that it will run on compressed air or steam do do this you need to modify the timing lobes the lobes on the gas engine allow the engine a intake compression and exhaust cycle what you want to do is to modify the timing so that it only has a power and exhaust stroke look at the existing lobe and weld on a lobe to the opposite side then take it to your bench grinder and grind at the weld until it is smooth and looks like the the original side ( do not grind off the original lobe you want both of them)
Step 7: Testing
for this step you need to remove the engines head so go ahead and do that now that you can see the valves and the piston you can o the testing the testing is done by putting the modified camshaft into the crankcase and turning the engine while looking at the valves and checking to see if the timing is appropriate to the piston movement one valve should open as the piston goes down and the other should open right as the piston goes up (you cannot have both valves open at the same time it will lower the efficiency temendously and the engine will stall
Step 8: Put It Back Together
after you have completed the testing you need to reassemble the engine so put the crankcase back together with the modified camshaft and put the head back on now for testing you want to use commpressed air so either tap the intake or the ehaust ( if you put the air into the exhaust it will run backwards) or you can make a fitting from a peice of metal and a gasket. now put the engine in a vice to hold it and and apply the air ( dont put to much pressure about 30-45psi) now take a scewdriverand turn the fly wheel until the engine starts turning if it stalls then the timing is off and the two valves are open at the same time. so tear it apart and grind some more if it does not stall then you are done!!!!!
Step 9: Going All Out
if you want to go the final step then you can put on a new flywheel and make a boiler and run the engine on steam also if anyone make a buggy or boat would love some pics
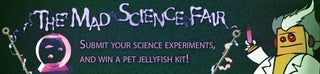
Participated in the
The Mad Science Fair
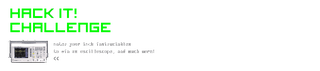
Participated in the
Hack It! Challenge