Introduction: Folding Kitchen Knife
I had an idea to see if I could make a small thing big. As I was making dinner I pondered what smaller objects could be remade into a larger version when it hit me; Why not make a folding knife large enough to cut up my vegetables?!
Continuing a trend of questionable ideas, here's how I turned a small folding knife into a big folding knife.
Ready? Let's make!
Step 1: Supplies
I used a folding blade with a linear lock as the template for my design. This knife is very simple and was designed as a kit, making it easy to disassemble.
I then looked for the largest kitchen knife I could find, which was a 14" chef's blade.
With these 2 components I could start designing the folding kitchen knife.
Step 2: Take Things Apart
The folding knife had a few torx machine screws holding the two halves of the handles together. With the knife completely disassembled I could determine how it worked and what needed to be done to make a larger version with the chef blade.
Step 3: Scan Folding Knife Body
To scale up the knife accurately I photocopied the knife halves and the blade, along with the chef blade.
This photocopier allows me to scan and digitize the file as a PDF.
Step 4: Computer Design
I imported the PDF scan into CAD and traced the folding knife outline, then traced the chef blade.
With the knife outlines traced at the correct size I could resize the folding knife to fit the chef blade. With the handles scaled up the chef blade was checked for clearances in the folding knife body. Minor adjustments were made to the chef blade to allow a clear swing path.
The outlines were then printed on standard printer paper and printed.
You can download my folding knife PDF below.
Attachments
Step 5: Print Template
Print the template on standard printer paper.
Step 6: Glue Template
Spray adhesive was used to glue the template printout to a piece of 1/4" plywood.
Step 7: Cut Plywood
Once the glue had dried completely the wood can be cut out by following the outline. A scroll saw or bandsaw will make quick work of this.
Step 8: Handle Openings
Before the lock channel is cut all the openings in the handles are drilled.
I started by drilling the opening at the end of the lock channel with a 1/2" drill bit. Then, the two halves were lined up and clamped together. Using a 1/8" bit I drilled the openings around the perimeter that would connect the two halves.
Step 9: Cut Lock Channel
After the openings were drilled the lock channel was cut. Cutting the opening at the end of the channel makes removing material in the channel much easier.
Step 10: Remove Paper Template
With all the openings and shapes cut out the paper template can be peeled off and removed. Sanding will remove any paper that remains stuck, so it's not important if there's any left stuck on.
Step 11: Steam Lock Channel
The lock channel on the small folding knife is a bent section of steel that acts like a spring and locks the blade in place when it passes the threshold in the fully open position. To mimic this action I steamed the lock channel into position.
The locking half of the handle is placed over a pot of boiling water and left to steam for a few minutes. Do not submerge wood. Next place a wedge of sacrificial wood into the lock channel to bend the wood, then continue steaming for a few more minutes. Remove wood from heat and let cool completely.
Once the wood is cool the sacrificial wedge can be removed, the channel should now stay bent allowing the lock to engage when the blade is inserted.
Step 12: Handle Standoffs
To allow space for the blade between the handles I used small strips of wood as standoffs. These standoffs were slightly thicker than the blade.
I rough cut some scrap wood to use as standoffs, making sure not the cover any of the drilled openings which would attach the two halves, and ensuring not to cover the blade path. I used regular wood glue to attach the standoffs.
The rough shape would be shaped and sanded when the handle assembly is complete.
Step 13: Mark Blade for Cutting
Using the paper templateI traced the cut lines onto the chef's blade with a marker.
To protect the blade, and myself, I covered the cutting edge of the blade with tape.
Step 14: Cut Blade
To make this chef blade fit into the profile of the folding knife the tang needed to be removed. I used a metal cutting bandsaw on a high speed to cut through the hardened steel blade, then cleaned up any burrs with emery cloth wheel and metal file.
Step 15: Drill Rotational Opening
The hardened steel knife blade is very strong, and only tough drill bits will be able to drill through. Using carbide tipped drill bits I started with a small pilot hole, then reamed the opening with larger bits until the opening was of the right diameter.
Even with heavy duty drill bits, I still ruined a couple of bits drilling through the blade.
Step 16: Assemble Pieces
The pieces can be assembled and a threaded rod is inserted as the rotational axle for the folding action.
The threaded rod bites into both the wood and the blade openings. It's not a perfect solution, but works well enough to hold the blade securely in between the wood handle halves.
Step 17: Dowel Attachments
Using wood glue on the standoffs, the two handle halves are pressed together. Wood dowels were hammered into the drilled openings to secure the two sides. Allow glue to dry completely.
Step 18: Refine Lock
After the glue was dried and I had a chance to test the locking action I noticed that some of the wood at the end of the locking channel was wearing away, making the locking sloppy. With the blade fully extended I made a small metal shim that was epoxy glued inside the end of the lock channel, this securely held the blade locked open when in use.
Step 19: Trim Attachment Dowels
Using a small hand saw I trimmed the excess length of wooden dowels holding the two halves together.
Step 20: Trim Folding Axle
Using an angle grinder the excess threaded rod was trimmed from either side of the handle.
Step 21: Sanding
Starting with a coarse grit sandpaper I removed any leftover pieces of the glued on paper template and rounded over the edges. Then switching to a finer grit sandpaper ensure a smooth and uniform finish over all surfaces of the knife.
Step 22: Wax Finish
Since this knife is for food use I went with a natural wax finish. Using a rag I rubbed the wax into the wood which gave it a nice finish.
Step 23: Flip Out and Chop!
You're all ready to bring a knife to a food fight!
This ridiculously large folding kitchen knife is ready to decimate your veggie ememies. Flick out the blade and start chopping.
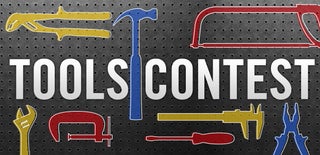
Participated in the
Tools Contest
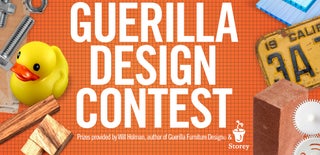
Participated in the
Guerilla Design Contest