Introduction: Transforming Bumblebee Costume
Every year for halloween, I try to make the most inventive, elaborate costumes I can, though this is the first one I've made an instructable for. When I was thinking about what I should do this year, I decided I wanted something different than your average latex mask and bodysuit, I wanted something unique, that people can't help but be amazed by. After some thinking, I realized that I wanted to make a transformers costume for many reasons. There are only a few of these costumes on the internet, so I didn't have a whole lot of help, but I still kept going on. In fact, I originally wanted my costume to be the first realistic transforming costume that actually drives via electric skateboard, but the cost proved high and time was low (only had like a month). This can be a fantastic project for anyone who is up to a little hard work (it pays off with the stares and amazement), and has a lower budget (around 50 bucks). Please vote for me in the halloween costume contest!
Step 1: Planning and Research
The amount of good transforming costumes on the internet you could count on one hand, so I only had a few sources of information, but, as with every project, you need to have a plan and know what you're doing before you start. After many google searches, the costumes that inspired me most were:
There were others to, but these seemed pretty great in terms of style and, on the second one, transforming action.
After cementing my transformation idea inspired by the video, I looked at images of Camaros and of bumblebee himself to get the design down. I drew sketches and made miniature models to make everything worked like I thought it would. After I was convinced I knew exactly what I would do, I started.
Step 2: A Note on Artistic Research
In the process of creating something as detailed and in-depth as a transforming costume, you need to experiment and create many prototypes and different versions to get exactly where you want. Artistic research is trying different things and messing up in the process in order to finally get it right. Pictured above is the first version of my costume (no research). Made out of PVC and foam board, it was so huge and ugly that I scrapped it fairly fast. Although it wasted my time and made me have to rethink my whole idea, I am glad that i made that PVC model because it helped me to understand what it was that I wanted and how I could accomplish it. When you are designing any sort of costume, or even trying to make something similar to mine, I suggest that you keep in mind that there will be multiple versions that you won't like, and that you may have to start over. For creators, mistakes and failures only make us better.
Step 3: Humble Beginnings
Before you start building the costume itself, you will have to go through a whole set of preliminary measurements and sketches to determine exactly how the costume will fit. To do this, you will need a large sheet of cardboard or paper (I used cardboard) that is big enough to crouch sideways against it (the position that your body will be in when in car mode), then crouch and have someone trace your outline onto it. The reason you do this is to be able to draw out the car profile exactly to the right size of your crouching body. You have to do a few smaller sketches on paper to cement your idea before you actually draw against the outline.
Some things to think about when drawing out the preliminary pattern:
1. The height of the top of the back can be a problem proportionately, but try to make it look like a real car as best as you can. You may have to lengthen the hood or raise the wheels to obtain the correct proportions.
2. It is helpful to be looking at a photo of the car you are modeling (I used a Camaro), in order to understand the design elements.
3. Remember that you don't have to get it right on the first time; if you are using pencil you can sketch over it and erase if it looks bad.
4. Think about and incorporate your transforming elements into the drawing (picture 2 and 3 show my sketch of the different parts I will need to cut in order for it to transform properly), if you don't think about it now, you could have a great looking car that transforms horribly.
5. Before you star to cut, look at your sketch and determine how it will look 3 dimensionally, if you don't like it, change the design now.
Step 4: The Dome: Measuring, Cutting, Assembling
The first piece that we will create will be the dome, which contains the windows and windshield in addition to the roof. This is the piece that will be resting against the back and tailbone when on (see pic 13). This piece is very important, as it is the hardest piece to get the proportion correct.
Materials for this step:
1. Cardboard (multiple large sheets)
2. 3/8" dowels
3. X-acto blade and cutting mat
4. Hot glue and gun
5. Ruler, yardstick, tape measure, whatever measuring device you prefer
6. Your full size profile drawing from previous step
The first thing to do will be measuring the width of your shoulders (1' 5" for me), and using that for the width of the top of the dome. Cut out the piece that is the top of the dome (shoulder width by drawing length), by using the drawing for length reference. For me, this first piece was 1' 5" by 1' 1". The second piece that we will cut will be the front piece containing the car's windshield. In the photos, piece #2 (front windshield) and 3 (back window) are rectangular, while they are supposed to be trapezoidal. The reason for this little mess up is that I didn't take into account the fact that cars have an angle change at the windows, so if you are confused, just follow the writing. The front piece will be 1' 5" at the top, 1' 7" at the bottom, and 8" long (8" tall with trapezoidal sides that slope from 1' 5" to 1' 7"). The third piece will be the rear window. Similarly to the 2nd piece, this one will be trapezoidal despite the pictures. The dimensions for the sides of the rear window are the same as the windshield (1' 5" sloping to 1' 7"), with the height being the only difference at 10.25". The final part of the dome are the side pieces which contain the tops of the doors and the side windows of the car. For the dimensions of these pieces, the top side will be the length of your top piece (1' 1" for me), and the sides of the trapezoid will be the lengths of your front and back pieces (8" and 10.25"). The bottom side of the side pieces depends on the angle at which you want the windshield and rear window to be in relation to the roof. Refer to your original sketch when deciding the angles of the front and back and keep in mind that the height of the whole dome depends on these pieces (you need the dome to go over your whole back while down). After you have all of your pieces cut and have put them up against each other to test, you are ready to begin assembling them.
The assemblage is fairly self-explanatory. We already know where they will be in relationship to each other, so all that is left is to glue. Every time an edge touches another edge, we glue a dowel that is the length of the edge on to strengthen every connection. Keep in mind that some dowels must be slightly shorter at corners or points at which dowels meet to prevent over lap. The top piece must be extra strong as it is where the car's weight is all focused, so we have to make support dowels strengthen the inside face (pic #9). When doing this, make one dowel that cuts the whole diagonal, and two half diagonal lengths so there is no overlap. After everything is glued together, make sure to test it on your back in order insure that it is the right shape and size before moving on (it should go over your entire back in a crouched position).
Step 5: The Hood: Cutting, Assembling, Moving Parts
The second and most important element of the transformer costume is the hood and doors. The reason that this part is so important is that the hood and doors make up the main and most crucial transformation elements. When creating this part, make sure that all transformation action is sound before moving on (test multiple times).
Materials for this step:
1. Cardboard (obviously)
2. X-acto blade and cutting mat
3. Measuring device
4. Duct tape
5. Dowels
6. Hot glue
Everything in this step is directly related to your original sketch. When creating the sides especially, the whole thing is based off of your design, so make sure that you like how every thing looks. The first sides that I drew and cut looked fine at first (pic #2), but when I put them up to the dome to check, they looked horribly short and ugly, so I had to redo the whole step and switch to a longer, more angular hood (pic #3 compares these sides). The side pieces contain the doors, front wheel wells, sides of hood, and a curved back end which will connect to the rear fender in the next step (see pic #4 for visual reference). After you have cemented the side piece design (make sure that it extends fairly far past the dome bottom it will be against, in order to make a realistic hood length), draw it out onto cardboard and cut out two. Place them against the bottom of the dome to see if you like how they look (if they look bad, redesign and cut now, so you don't end up like I did).
After finishing the side pieces, the next thing to do is the hood. The length of the hood will be however far out your side pieces extend past the dome, and the width will be the width of the bottom of the dome (1' 7" on mine). To add more realism and style, I angled the front of the hood into a point, which will aid in molding later. On the other, non-point side of the hood, there is a hole through which your head will rise during transformation. Measure and cut this hole exactly centered in a rectangle slightly larger than your head (8.5" by 11.25" for me). Save the cutout, as it will be the part against your head, providing an exact fit with the rest of the hood. You are now ready to attach everything to the dome and complete the main moving part.
After you have glued the hood onto the side pieces (same deal, dowels and hot glue), you can attach the cutout from the hole in the hood to the dome's front so that it is sticking straight out if the dome is flat against the ground. The way that I accomplished this was with dowels and a lot of hot glue (see pic #11 and 13). After you have attached the cutout to the dome, you have to attach the hood and side piece to the dome as well, but tape, not glue (do not attach the cutout to the hood). Duct tape on both sides with multiple strips to insure a secure bond. After both sides are taped up solidly, you can test and practice the transforming action by lightly pressing out the side pieces from the inside and lowering the hood with your head coming through the hole pivoting on the duct tape. There are many good photos of both positions (transformed and non transformed) included.
Step 6: The Tail End: Drawing, Cutting, Assembling, Moving Part
This is the smallest element of the costume, yet it is important as it contains another moving part and seals you inside the costume. I am sorry for the lack of cutting and assemblage photos in this step, but it should be fairly straightforward.
Materials needed for this step:
1. Cardboard
2. Duct tape
3. Dowels
4. Hot glue
5. X-acto blade and cutting mat
This piece is the tail end of the car which includes the rear wheel well, the trunk and the back of the car. For this piece, there weren't any set dimensions other than the width (1' 7", just like rest of car), so the profile is cut to the shape of your original drawing. The first part will be the side pieces, which are cut from the design of your profile drawing, making sure that the wheel well/ fender portion aligns perfectly with the back of the door piece. After the side pieces are cut, you have to make a rectangular top piece that is the length of the tail end by the width of the rest of the costume (1' 7"). Glue to top piece to the sides, flush of both ends, the same way with dowels and hot glue. In order to support the thin sections of the side pieces, you will have to glue dowels cut to small size directly to the curve (pic #3). Once you are sure that the thinness of the side pieces won't be an issue, take a rectangle the height of the back of the tail end (where the trunk and tail lights are) by the width of it (1' 7"), and glue it on securely. On my costume, the very back had a curve, so I didn't use dowels; I just bent the cardboard and glued it right on (dowels aren't really necessary for this as there is not much stress on this panel). If all the connections are solid and the whole piece is not flimsy at any point, you are ready to attach it to the dome, creating the second moving part.
The attachment of the tail end piece to the back of the dome is fairly easy and self explanatory. All you have to do is duct tape the meeting point of both pieces when assembled (see pic #5-8). To insure a secure and tight connection, line up the pieces perfectly and tape with multiple strips on the underside and top of the seam. To test and practice your transformation action at this point, you will have to get inside the costume in car form, push lightly out the doors, slide the hood down (as before), and stand up so that the tail piece can pivot back to allow standing mobility.
Step 7: Magnets
This is a tiny part of the costume, yet it is extremely important as it is the part that keeps the entire costume solid when in car form. The only things that you need for this step are small neodymium (or other powerful magnets) magnets and hot glue. I cut each magnet in half (only using 2), then glued them next to each other where the tail piece's wheel well aligns with the door (pics #1-3). This connection point makes it so that when the costume is in car form, the door can't slide up and the tail can't pivot back, keeping the costume rigid until you detach the magnets. When testing and practicing transformation at this point, if you find it hard to push out the doors, you can push out or kick the back of the tail end with your foot to detach the magnets.
Step 8: Detail Work and Molding
At this point in the process, your costume's basic form and transformation action is completely finished (yay!), but you still have to make the heart and soul of the costume: the exterior look. This step will include creating the grille, hood, fenders, and roof. For this step, I cannot really give any measurements, as everything I did was based on visual appeal as I was going.
Materials you will need for this step:
1. Cardboard
2. Hot glue and gun
3. X-acto blade and cutting mat
4. Multiple sheets of "Foamular", a rigid insulation material for carving details. I got mine at Home Depot.
http://www.homedepot.com/p/Project-Panels-2-ft-x-2...
5. Tools for cutting and shaping foamular. I originally used an electric knife to do the carving, but I actually found it much easier to use a steak knife for cutting out of shapes and a chef's knife for shaping.
6. Electric sander for smoothing the foamular. I guess you could use sandpaper, but it would be really, really hard, and take forever if you could even do it.
7. Spray glue for foamular. I used this: http://www.homedepot.com/p/3M-Super-77-16-75-fl-oz…
The first detail that I worked on was the grille. I had not yet put a piece on the grille area, so cut I cut two identical rectangular pieces and glued them to form the same angled point as the front of the hood about an inch back from the front of hood. Then I cut a bunch of inch wide strips the length of the sides of the the point and glued them on to make a look like a Camaro grille (if you are confused with my description, see pic #5). A car does not have a grille just sticking out by itself in the front, so you will have to cut another two smaller rectangles to form the point under the grille (confused? see pic #6). In order to complete the cardboard aspect of the grille, you have to glue small squares on top of the strips on either side for the head lights (pic #7). If you are happy with how your grille looks, you can now move on to the foamular, if you are unhappy, you could add extra details that I didn't do (remember that the foamular is the main detail material, so even if it looks bad now, it will still probably look good with foamular).
Now that you are satisfied that your costume needs no more cardboard (you won't be able to add any more later), you can start working with the foamular. This material is fantastic for this type of thing as it is easy to cut, and rigid enough to provide good form. I am not sure of the dangers of foamular dust, so when sanding, wear a mask or respirator (better safe than sorry). After you have familiarized yourself with the material (practice cuts, sanding, hitting with a rock), you will be ready to begin creating pieces. The first foamular piece that I created was the hood. To do this, you have to draw out the exact shape of the hood onto the foamular, then cut it out with something like a steak knife. Put the cut out piece on top of the hood to see if it lines up well (if it doesn't, you can trim it), then draw out the exact shape and position of the hood cutout which your head comes through onto the foamular (DON'T CUT IT YET). Now the fun part begins. To shape the raised center of the hood, mark out 2 parallel lines equidistant from the point where you want the edges of the raised part to be. Cut a groove into the lines that you just drew with a chef's knife (only as deep as you want the raised part to be). You then have to remove the material out flat from outside of the groove using the chef knife on both sides. Put it on top of the hood again to see if it looks symmetrical. If you like it you can take out your sander and smooth out all the flat parts, until it looks nice and even. I also used the sander to make the front taper down to a point for realism. Now you can cut out the cutout where your head will come through, making sure that your cuts are straight and accurate as you won't be able to trim it because it needs an exact fit. Once you are completely satisfied with the looks of the hood and have seen if the transformation works with the foamular cutout on the cardboard, you can glue. Spray a good amount on both the foamular pieces and the cardboard, then immediately line them up perfectly and hold it for about a minute. The glue should be workably set in about 5-10 minutes.
The next foamular part is the area below the grille. This area is much easier as you will not need to shape or sand the pieces. All you need to do is simply cut out pieces to cover the area below the grill, keeping a small rectangle at bottom, and glue them on the same way (pic #11 for reference).
The last pieces are the front sides, roof, and fenders, and I unfortunately did not have a camera while I was doing them, so you'll have to look at the picture of the finished project. The front fenders are pretty easy, being just a semi circle carved and sanded down for a smooth transition (I feel that by looking, you'll understand and can carve and glue yourself). The rear fenders on mine are larger than the front and have are shape of the whole profile of the tail end. This part will require a lot of carving and sanding to get a desired look, so be prepared. As in all gluing of pieces, make sure everything lines up. The next pieces are the front sides. These were something I just added because I thought it would look better if the headlights were framed by a layer of foamular. They are just rectangles the height of which is the same as the side of the front and the length of which is however long you want, as long as it is short enough to not overlap the front fenders. All you need to do is taper the whole thing lengthwise on only one side to a point for a smooth transition, then glue up against the grille and front area. The final foamular piece I did was the roof. This is optional as the roof probably looks ok flat, but I wanted to round it for realism. To do this, just cut a piece the size of the top of the dome and taper to a point on both sides, round everything with the sander. After you have all of your detail parts glued on, all that remains is painting!
Step 9: Painting
Sorry that I don't have any painting photos, but you should be able to understand, as it is all fairly easy spray painting. First, you need to cover the entire costume in a white primer coat, then all yellow once the primer is dry. I taped off the areas where I wanted racing stripes and painted it black. For the windows, tape off about an inch on every side then paint grey (taping off an inch is so that you have the yellow lines on the edges of the dome). For the grille and front area, tape off and paint the grille black, the lights gray, and the bottom part black. Once the gray paint is dry on the headlights, use a small brush and white paint to carefully draw the circle of the light itself. The tail lights I painted with a brush and red and black paint (you can do these however you want).
Step 10: Extra Pieces/parts/props
At this point, you are almost completely finished! all that you need to do is make the wheels and optional leg pieces. First we will make the wheels. All it is is a foamular circle (10 inch diameter for me) painted yellow with spokes painted on. For the rear wheels (pics #1-5), secure a thin strip of cardboard across the gap, then tape the wheel to it from the inside. That easy! The front wheels you will be holding, so all you need to do is take a short segment of PVC pipe and secure it to the back for a handle. To do this, hold the PVC near the edge (it will make it easier when you are in car form), and twist and press to make a shallow hole that you can fill with hot glue to secure the handle in place. Now, if you want to have leg pieces like mine (not necessary, just add some pizzaz), just take a rectangle of painted yellow cardboard, and wrap it around your leg. To secure the leg piece in place, one would think that some sort of tying up thing would work, but I found that securing with a strip of duct tape worked just fine for me.
Step 11: Finished!
Go wow everyone and win money in contests, as you are done!
If you have trouble understanding the transforming mechanics, or just want to see the costume in action, watch these videos! I drop a wheel in the second one.
Attachments
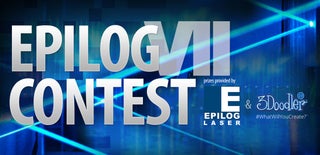
Participated in the
Epilog Contest VII
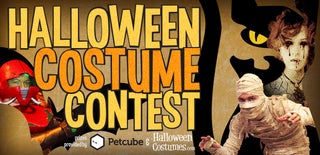
Participated in the
Halloween Costume Contest 2015