Introduction: 12V Lithium-Ion-18650 55ah Portable Battery
Dear Instructablers
A few weeks ago I brought a Narrowboat, A boat designed for the inland waterway systems of the UK. The craft is however in a state of neglect and would be classed as a project.
This Instructable will look at documenting the building of a portable 12v power supply.
The aim was to build a portable battery that could be used to run a selection of medium powered devices (10w - 60w) while on the boat. These include charging power-tools, my laptop & phone, and most importantly keeping the Bluetooth speaker topped up.
The battery was meant to able to be portable but also hold sufficient capacity to supply the power for the above-mentioned equipment for the time onboard.
This Introduces one of the first principles of battery design: the concept of the watt-hour.
A Watt Hour is a unit of measurement for power over a period of time (an hour), or in our case, a way of measuring capacity. One Watt hour is equal to one Watt of average power flow over an hour. One Watt over four hours would be four Watt Hours of power.
Example Equipment power x the amount of time estimated in use for an average period on the boat!
Tools Charger _ 60W x 3 hours = 180Wh
Laptop Charger _ 60W x 3 hours = 180Wh
Phone Charger _ 20W x 6 hours = 120Wh
Speaker Charger _ 10W x 2 hours = 20Wh
Light _ 30W x 5 hours = 150Wh
Summation of the Equipment Wh's = 650Wh
This meant I'd be looking at building a battery with a capacity 650Wh
Note, these times were based on the estimated consumption of power for working on the boat for a day then recharging the battery at work the next day.
Step 1: Understanding the Battery Options
A key concept in battery building is matching the user's requirements to different cell technologies to deliver the best final product.
The following are seen as key considerations when matching a battery technology to its user.
1/Specific Energy: The gravimetric energy storage density of a battery, expressed in Watt-hours per kilogram (Wh/kg). 2/Specific Power: The specific power for a battery is the gravimetric power density expressed in Watts per kilogram (W/kg). 3/Cost: 4/Performance: 5/Safety: 6/Life Span.
Li-ion (Lithium Nickel Manganese Cobalt Oxide (LiNiMnCoO2) — NMC
I selected the Panasonic NRC18650PF cells.
NMC packaged as the 18650 cells provided an excellent combination of properties when looking for a portable battery due to high specific energy and power, with a satisfactory level of performance, safety, and life span.
One issue was the cost of the cells; however, 18650 cells are widely available on the second-hand market.
It should be noted that this is a risk because of the cycle life of such components and the detrimental effect one weak link can have on the battery pack. As a result, when selecting a cell we will run a pre-pack test individually before its selection in an attempt to negate this issue.
I found https://batteryuniversity.com as an excellent resource
Step 2: 18650 Li-ion (LiNiMnCoO2) — Nominal Voltage, Capacity and C Rates
Understanding The Concept of Cell Voltages.
Nominal Cell Voltage is the average voltage a cell outputs when charged. The nominal voltage of a battery depends on the chemical reaction behind it.
A lead-acid cell will output 2V. A lithium-Ion cell will output 3.6V.
The keyword here is "nominal", the actual measured voltage on a battery will decrease as it discharges. A fully charged lithium-ion NMC battery will produce about 4.1V, while when discharged its voltage may be closer to 3.0V.
If you open the battery specification PDF you should find a graph that shows how the cell voltage drops as its capacity is reduced. This relationship becomes important when we look to understand a number of metrics of the battery,
another important figure is the C-rate
Charge and discharge rates of cells are governed by C-rates. The capacity of a battery is commonly rated at 1C, meaning that a fully charged battery rated at 1Ah should provide 1A for one hour. The same battery discharging at 0.5C should provide 500mA for two hours, and at 2C it delivers 2A for 30 minutes
Attachments
Step 3: Understanding the Battery
Once a cell technology is identified you can begin to calculate how individual cells can be combined to match the battery bank to the electrical systems you'll be using!
What's important to understand is the principle of electrical connection among cells.
First, we will consider connecting cells in series for greater voltage:
We know that the current is equal at all points in a series circuit, so whatever amount of current there is in any one of the series-connected batteries must be the same for all the others as well. For this reason, each battery must have the same amp-hour rating, or else some of the batteries will become depleted sooner than others, compromising the capacity of the whole bank. Please note that the total amp-hour capacity of this series battery bank is not affected by the number of batteries.
Next, we will consider connecting cells in parallel for greater current capacity (lower internal resistance), or greater amp-hour capacity:
We know that the voltage is equal across all branches of a parallel circuit, so we must be sure that these batteries are of equal voltage. If not, we will have relatively large currents circulating from one battery through another, the higher-voltage batteries overpowering the lower-voltage batteries. This is not good.
The 18650 cells have a Max Voltage of 4.2V, Nominal Voltage of 3.6V, and Min Voltage of 3.0V
The narrowboats electrical system runs a 12V system. We can attempt to match this by connecting the 18650 cells in series.
Connecting 3 cells in series will give us a Nominal Voltage of 10.8
Connecting 4 cells in series will give us a Nominal Voltage of 14.4
As you can see both arrays find it difficult to match with a 12V nominal system but there is a selection of systems that can help us produce the required output. However, they may come at an efficiency drop.
Panasonic NMC18650PF cell capacity
New Cells = 2900mAh
Used 90 => 100% Cells = 2610 => mAh
We can use the relationship between Watt, Volts, and Amps to work out how many cells are needed to be connected in parallel to reach the required battery bank capacity.
We can use the Wh estimation of 650Wh and divide this by are desired nominal system voltage of 12V
650Wh / 12 = 54000mAh
We can then divide the overall 54000 mAh required capacity by the capacity of the individual cells 2610mAh
54000 / 2610 = 20.5
This means we will need 20 or 21 cells connected in parallel to attain a bank with the necessary capacity.
Attachments
Step 4: Understanding a System Voltage & Inverter Selection
Very similar to nominal voltage is system voltage. This refers to the nominal voltage of the system as a whole. Since batteries are in many ways the heart of a battery-based system,
We call the battery bank’s voltage the system voltage.
Almost all narrowboat systems will use one of these three voltages: 12V, 24V, 48V. The system voltage of any given installation is usually, though not always, determined by the battery bank required by the application being served;
The inverter, if one is used, will influence this decision as well.
The primary function of an inverter is to convert Direct Current (DC) power into standard, Alternating Current (AC). This is because, whereas AC is the power supplied to industry and homes by the main power grid or public utility, the batteries of alternating power systems store only DC power. Moreover, virtually all household appliances and other electrical fixtures and equipment depend solely on AC power to perform.
It should be noted that most 12V volt systems are designed around the Lead Acid Battery technology. Which has a tighter voltage range than the 18650 cells.
This means it is important to review the appliances being served to make sure they can handle the voltage range of the 18650 cells of (12V - 16.4V).
The victron inverter is able to accept an input voltage between 9,2V - 17V.
Also from the Victon Data Sheet above, you can see the efficiency of the inverter and zero load power requirements including its ECO mode.
Step 5: Electrical Schematic & Inverter Selection
With all the Information we can draw out a schematic of the system.
To create the 650Wh battery we will combine four packs of cells in series to create a 12 - 16.4V (12v) battery voltage.
Each pack of batteries will contain 20 18650 cells to give a capacity of 55Ah. This means we will use 80 cells in total.
The battery pack will then be connected to either the Inverter, giving a 240V power supply. or the Charger to replenish the battery.
One of the most important aspects of the battery is the Battery Management System (BMS). This is detailed below.
Attachments
Step 6: Battery Management System
A Battery Management System (BMS) is an intelligent component of a battery pack responsible for advanced monitoring and management. It is the brain behind the battery and plays a critical role in its levels of safety, performance, charge rates, and longevity.
You will permanently damage your battery if it is Over Charger or Over Discharged as a result the inclusion of a BMS is essential.
However there as a few variables to consider when selecting a BMS.
- Matching the BMS to your series connections to the P-value of your pack. This is because the BMS will require voltage information from each of the 4 sub-packs to help keep the battery pack balanced.
- Matching the BMS to your cell chemistry, NMC 16.4v cut-off
- The amp Output rating. This is what the BMS will allow the MAX amp draw from the pack. It can be seen as a fail-safe.
- Output/Input Connection, combined charge, and discharge or separate connectors
We have an Inverter rated at 250 watts
Watts = Volts x Amps
Amps = Watts / Volts
250w / 12V = 20A
With this calculation, we can see that the BMS is able to allow the system to pull the needed amps being rated at 40 Amps.
Step 7: Shopping List
- 100 x Used Lithium-Ion 18650 (Panasonic NCR18650PF)_Price £89.00
- 1 x Battery Management System (BMS) 12v_4s_40A _Price £28.99
- 1 x XT90-S XT90 Anti-Spark Male Female Connector Plug_Price £2.99
- 1m x 8 AWG Gauge Flexible Silicone Wire Copper Black Red RC Cable_Price £10.99
- 1 x 4S 14.8V (16.8v) Battery Capacity Indicator Blue LCD Display_Price £9.99
- 1m x 7mm 0.2mm-30A-Pure Nickel Strip Strap Belt For Spot Welding battery_Price £9.99
- 1 x Victron Phoenix Inverter 12v/250v 250w_Price £88.90
- 7 x Cell Plastic Spacer Holder Case 18650 Battery Cylindrical Cell Bracket_Price £8.99
Step 8: Testing, Cataloguing and Using the Re-pack Software.
Before we start welding the pack together its important to give the cells a screening to find any faults.
- Start be recording each cell via an excel spread sheet, make a grid reference for each cell.
- One by one remove a cell and check its voltage, It should be 3.3 (remove if 3.2 or less)
- 3.3 volts is what the company discharges the cells to before shipping. If any cells have dropped below that voltage it maybe damaged.
- After the voltage check the remaining capacity rating on the cell against its reference location.
- Place back in the grid reference location.
After we've recorded our cells we can select the 80 largest capacity rated cells and run them through a box packing mathematics problem algorithm; the website below is a great tool to achieve this.
Run the cell inputs section and select your variables (4s/20p). You will end up with the cell capacities required in each of the 4p packs.
Step 9: Locating, Configuring and Fixings the Battery Pack
In this step, we will locate, refurbish, and build the battery's core structure ready for spot welding.
- Use your excel spreadsheet to locate each of the 4p cells from the repacker output. Enter the cell capacity you are looking for in the Find add on and it'll retrieve the grid location reference as well.
Once you have the 20 cells belonging to a pack:
- Gently grind off any nibs from the surface of the contact's + and - ends.
- It doesn't have to be perfect but some nickel from past welding can affect the quality of the new weld.
- Now it's time to use your glue gun to stick the cells into the 20 cell spacers.
- Remember to complete these tasks on a clean clutter-free table to avoid shorts, Use Kapton tape to cover areas for protection.
- Do the 20 cells one by one until all are done and glued together, double-check the orientation of the cell packs making sure the + and - terminals are orientated correctly.
- Add Kapton tape to protect against shorts while working on the pack
Step 10: Spot Welding
Firstly you'll need a battery spot welder.
I'd recommend the Arduino; You can find it at the link.https://malectrics.eu/product/diy-arduino-battery-...
In this step, we will create the connections between the cells.
- First, start by testing your spot welder on some spare nickel. You're looking to create a weld that is difficult to pull apart but not be putting a hole through the sample.
- You'll notice the welder will have a number of settings so read the manual and figure out which settings work best for the application at hand
- The settings will differ with regard to the quality of the nickel being used and the thickness of the strips.
- The thickness and width of Nickel strips will also be dependant on the amount of current you will be expecting to draw from the cells
- Once you've found a good setting for the welder, Cut a section of the strip to length for the area your working on. Check if it fits then create a simple cutting jig so you can quickly cut the required lengths.
- Now once again clean your working area and uncover the area of connections you'll be working on.
- remember to keep the other sections covered to avoid an accidental short!
- Complete the connections using the spot welder, making at least 2 welds and 4 spots. 3 and 6 spots are even better.
- once you've completed that section cover with Kapton tape and begin on the next section of connections.
- Make your way through the sections until completed.
- Test with a voltmeter from the positive and negative terminals.
- Voltmeter should read 3.3 x 4 = 13.2
Step 11: Anti-Spark XT90 Connector - (Female)
I personally really struggle with connecting the XT90 connectors.
You'll need to be connecting these to 8 AWG gauge wire to satisfy the current demands.
I guess the key is a good powerful soldering Iron and some flux to help transfer heat.
But the main aim of the step is to complete the connector before it's connected to the battery as this would negate the issue of completing the connection with a live current.
Once done we can put this aside and begin to connect the BMS.
Step 12: Attaching the BMS
We discussed the importance of the BMS in a previous step.
Now we must wire in the device.
- First, start by hot gluing the BMS to the battery pack in an area where you can trace the balance wires to their connections and the B- can reach the negative terminal.
- To relieve current stress on the B- wire I connect the wire along the terminal by extending it with a splice and tinning it along its lengh. Then solder it inbetween the nickel spot welds along the negative terminal
- next step is to cut, strip and solder the 5 balance wires into place. The black wire goes to the negative terminal and others then go between the series connections.
- Secure all wires with kapton tape
Step 13: Splicing and Soldering the XT90 Connector to the Pack
In the final stage of the pack build, we will connect the wires running from the XT90 connector we created in Step 11.
- Splice the P- wires together and then shrink wrap.
- Solder the main positive wire to the pack's positive terminal, like with the B- wire of the BMS
- Note that I stripped more wire than the picture shows.
- Finally, cover with Kapton tape and test the XT90 connector with a voltmeter.
Step 14: Padding & Wrapping the Battery
The step is for protection against the environment and impact.
I used an old foam yoga matt and cut it to size then shrink wrapped the pack a couple of time in different orientations
Step 15: Charger
I use the charger listed below:
HTRC C150 150W 10A AC/DC Balance Charger Discharger for 1-6S LiPo Battery,
https://www.banggood.com/HTRC-C150-150W-10A-AC-or-...
- It can charge at 10A
- So if your battery was flat it would take 6 hours to charge
Step 16: Finished
I added a capacity monitor by wiring it into the inverter input + and -
Thanks for viewing my build. I hope to upload a few more projects from the boat in due course.
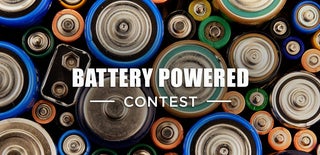
Participated in the
Battery Powered Contest