Introduction: 1932 De Soto Hood Ornament Replica
My Father-in-Law is a big classic car guy and one of the cars that he as restored is a 1932 De Soto. Unfortunately the Mascot (Hood Ornament) was missing and getting an original is nearly impossible and a replica was very expensive. When we were at the 2012 Back to the fifties weekend car show in Saint Paul,t MN I said "you know Les, I could probably make one, it won't be perfect, but from 20 feet away you wouldn't be able to tell."
I've never made anything like this before but that's never stopped me in the past. With a basic understanding of the investment casting process I started to stumble along the steps you'll see laid out in this instructable.
Step 1: Materials & Tools
Materials
Images or reference measurements of what you're trying to replicate.
Some wood to make a base and casting box.
Stiff wire to make a skeleton
Modeling clay
Liquid Latex or silicone
Spray foam
Investment casting wax
Tools
Dental / Sculpting tools
Fine detail files
Misc woodworking tools
Double boiler
Soldering iron / solder
Metal Casting equipment (or access to)
Step 2: Getting Ready
Fortunately since I was at a car show I should be able to find other examples to take pictures and take measurements. Unfortunately the 1932 De Soto is a rare car so the only thing close was a 1933 De Soto. The mascot is very similar in design, but she's swept forward more than a 1932 mascot. The internet filled in the rest of the information I needed along with the dimension from where she will be mounted.
Step 3: Sculpting
---*** Disclaimer ***---
I AM NOT AN ARTIST
I drew the outline of the base on a wooden plank.
Lining up the outline with the pictures and references I created I drilled a hole that I used to mound the support structure.
I did my best using some 12 gauge copper electrical wire to make a basic support structure match the shape of the mascot. Using a soldering torch I locked everything together so the support structure would not move around while sculpting.
After the support structure was in place I started adding modeling clay. Nothing special used, just a tub crayola clay from wal-mart.
From this point on it's just adding more details shaping it with the dental picks / sculpting tools. The majority of the sculpting was done while the clay was still wet. When everything was dry I did some additional scraping and filing to bring out as much detail as my limited artistic ability allowed.
Step 4: Preparing the Master Mold
I'm going to say up front that there is probably a better way to do this, but again, I've never done this before.
I stopped by my local hobby lobby and picked up some latex. I started by brushing on two coats allowing them to fully dry in between coats. The third coat I embedded some gauze to give the latex some reinforcement and ended with a 4th and final coat.
Now the tricky part.
Find the sharpest scalpel or exact o knife you can find to cut the latex off of the clay model.
Plan the cut line using a few simple guidelines
Cut lines should be made to let the clay / wax model come out as directly as possible.
Cut lines should be made in areas where the seam can be hidden or easily smoothed away
After the Clay master is removed and the latex mold is cleaned some simple tape is used to help keep its shape and seams lined up. The latex is relatively firm but there is still some flexibility.
The next step was to create a support or "Sabot" for the latex mold so that it retains it shape when the wax is poured in. I started by creating a box and then carving out wood spacer blocks to fill in the air gaps. To fill the gap between the wood blocks and the latex mold I used some expanding polyurethane foam. To prevent the latex mold from collapsing I put the clay master back into the mold after recreating the wings that broke off. (looking back I should have waited to cut the mold until after this step)
The clay master was removed for the last time. The latex mold was cleaned and the casting box was assembled.
Step 5: Creating the Wax Models
Using a double boiler I melted the wax on the stove top.
Carefully pour the wax into the mold a little over since there will be some leakage and shrinkage.
As you can see the 1st couple didn't come out very well. Having a consistent quick and uniform pour will help prevent some of the removal problems that came up. Preparing the mold with a release agent would help, I'm not sure what that would be tho, maybe a silicone spray would do the job. Make sure the wax is completely cooled before attempting to remove or else it might bend or break.
Get those sculpting tools back out because there may be a bunch of touch-up work.
Now is the time to get things right, use a pencil soldering iron or sculpting tools with a hear source to help melt and shape the wax to the final look.
Step 6: Lost Wax Casting (Investment Casting)
These next few steps you'll have to have a really good buddy with a foundry, or source this part out. It ended up costing me a bottle of Captain Morgan and a $50 True Value gift card to cover supplies.
The 1st step is to attach wax pathways and funnel to allow the molten metal to enter the mold and the gasses inside the mold to escape.
The next few steps are building up alternating layers of ceramic slurry and silica sand. With the 1st layer of slurry a little extra care is taken to brush the slurry into every nook and cranny.
The mold is next placed into a kiln where the wax is melted out and the ceramic shell is hardened.
The mold is cooled and tested with water to make sure there are no leaks cracks or holes.
When ready to pour the mold is re-heated so there will be no thermal shock when the hot metal is poured in. This also helps the metal flow into every nook and cranny because the metal won't cool as quickly.
Once the metal has cooled the ceramic shell is chipped away and the feeder gates and vents are cut off.
I received two successful metal castings from the original four wax models. One ceramic mold cracked in the kiln and the other failed the pour because it solidified too early using a brass alloy. The two good ones were a zinc alloy.
Step 7: Finishing and Polishing
The 1st four pictures are what I received from the foundry. The rest of the work is smoothing detailing and polishing.
Hand files are used to smooth out the surface and files were used to deepen some of the details.
A bench grinder with buffing wheels and polishing compound was used to polish the surface. A dremel was also used for some of the harder to reach areas.
Sorry I don't have a picture of it on the car, but from 20' away you can't tell that an engineer with no artistic ability made it. (with a little help from his friends)
I hope you enjoy.
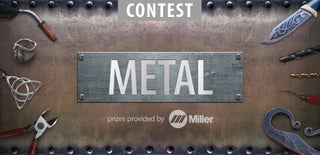
Participated in the
Metal Contest 2016