Introduction: Mini Farm Windmill - Soldered Brass
My name is Dylan and I am 13 years old. I decided to make this windmill as I'm interested in creating miniatures and enjoy soldering. The windmill itself took around 6 days to make (working on and off on it). It's mostly made from brass, balsa wood, wire and thin aluminium tubing.
Supplies
This is a list of the materials that I used:
1.6mm Brass rod
Aluminium tubing - 1.57mm
Aluminium tubing - 2.38mm
Piano wire for spokes
Balsa wood dowel - 5.85mm dia. (for hub and pump base)
Square balsa wood - 7mm (for gearbox housing)
Sheet balsa wood - 2.4mm thick (for platform)
Sheet balsa wood - 6.65mm thick (for base)
Brass sheet 0.127mm x 102mm x 254mm
Very thin copper wire - for latticework
Artificial grass from model shop
Tools used:
Masking tape
Compass
Scalpel and fresh blades
Soldering Iron and solder
2 sizes of circular forms to shape the brass rod (to create circular formwork for the blades)
Gas stovetop to heat the brass rod to make them more pliable
Pliers - I used a variety of plier types - flat nose, needle nose
Metal snips to cut brass rod
Sharp scissors to cut brass shim - don't tell mum
Tiny drill bits or piano wire
Drill
Fine tipped pens to mark on brass
Pencil and rulers - small measuring ruler and set square
Superglue
Sandpaper
Coloured pens and pastels (preferably paints)
Windmill drawing pdf
Step 1: Pdf Plan
⬇️ Download and print the pdf. This is a plan to assist you. ⬇️
Attachments
Step 2: Cutting and Soldering the Brass Rod
- First cut the brass rod to size. This will be in the pdf.
- Tin the ends of all of the shorter pieces and secure in place with masking tape. Place over the plan and solder together.
- Repeat this so that you have two ladder shaped pieces.
Step 3: Soldering the Frame for the Tower
- Cut two more of each size of the small pieces and then tape one of the ladder pieces to the plan. Make sure it is vertical by using the 90 degree angle on your set square.
- Solder the small pieces to the side of the ladder-shaped part
- Solder the second ladder piece to the small brass rods. Tip: try not to get the short brass rods too hot when soldering as it might unsolder what you have already done. :-)
- Next, solder the remaining small brass lengths to two ladder pieces to form the fourth side.
Step 4: Creating the Latticework
- First strip the varnish coating from the copper wire with a scalpel blade as the varnish makes it more challenging to solder
- Solder one end of the copper wire to the bottom of the tower and spiral your way up, soldering at each point. Note: skip the first rung.
- Make an X shape by doing the same thing, then do it on all four sides until compete.
Step 5: Creating and Forming the Two Brass Rings
- Cut two pieces of brass rod to length. This will be for the rings that will hold the blades in place.
- Using pliers, hold the rods over a flame for around a minute. This is to soften the metal to make it easier to bend. Tip: try not to get the ends of the rod in the flame. I found that if they got hot it would make it more challenging to solder to.
- Tin the ends of the both the rods and carefully wrap the wire around both forms. Here I'm using a wooden dowel and a plastic container.
- Now solder the ends together
- Now the two rings are complete
Step 6: Cutting and Bending the Blades
- Cut out the blade from the plan and transfer it onto a popsicle stick or a thin pice of wood
- Using a thin tipped pen, trace the blade shape onto the brass sheet. Tip: try to minimise the amount of space these take up by arranging them like I have done. Tip: I would recommend you cut a spare piece just in case.
- Using a pair of sharp scissors, cut out the blades (just keep in mind the scissors may get a bit blunt.)
- The blades may be a little bent after cutting so use pliers to compensate for this. Also using the pliers, bend the blades into a U shape like I have done in the photo.
Step 7: Making the Hub
- Tape the ring to the plan and make a mark with a thin tipped pen on each of the 18 lines. Do this for both rings.
- Place the balsa wood dowel in the drill chuck and with the drill running, sand it until it becomes around 4.5mm in diameter.
- Use a piece of 5mm sandpaper to make to make an indent into the dowel
- Cut off the excess from the ends.
- Colour in the hub with a red pen (preferably paint)
Step 8: Spokes for the Hub
- First use a thin tipped pen to evenly space six marks
- Use a piece of piano wire or a thin drill bit to make six holes under the marks and then one at the bottom in the centre.
- Cut six pieces of thin wire to 1cm. These will be the spokes.
- Now superglue the spokes into the hub, making sure they are on a slight angle like an umbrella.
Step 9: Attaching the Blades and the Rings
- Solder the spokes to the small ring. Tip: also ensure the soldered ring join is between two of the spokes so you do not unsolder the ring join.
- Tin the bottom of the blades. Make sure to tin to the convex side (the side sticking out) like I have done in the photo.
- Solder the blades to the ring, making them evenly spaced using the 18 marks. Note the orientation of the hub. Tip: prop up the small ring so it is in line with the blades as it makes it easier when soldering.
- Continue to solder on the blades. I attached my blades with a slight pitch so when I blow on the rotor it spins clockwise.
- Solder the large ring to the back of the blades. Try to get as centred as you can.
- Now the rotor is complete
Step 10: Making the Platform
- Cut out a 2cm by 2cm square from the thin balsa wood sheet
- Cut a 1cm by 1cm square in the centre of the sheet. Note: do this carefully as not to split the balsa wood.
- Place 4 drops of superglue in the corners of the inner square and lower onto the tower until all 4 corners touch the brass rod
Step 11: Making the Gearbox Housing
- Use the square balsa wood, round the bottom two corners and cut an angle on the right side according to the plan.
- Colour in the bottom half red and the top silver. If possible use paints.
- Cut a slot in the bottom right. This is where the 1.57mm diameter tubing will go to allow the rotor to spin freely.
Step 12: Making the Rotor Spin
- Cut two 2mm long pieces of 1.57mm aluminium tubing. Cut two 1cm long pieces, one from 1.57mm and one from 1.38mm aluminium tubing. Cut one 1.5cm long piece of piano wire.
- Glue the thin tubing into the slot we made earlier
- Drill a hole into the bottom of the gearbox housing and superglue the 1.38mm tube into it
- Glue the piano wire into the hole in the bottom of the hub. Allow 8mm sticking out.
- Now slide one of the 2mm x 1.57mm aluminium tubing over it.
Step 13: Tailbone and Wind Vain
- Orientate the gearbox housing so that the 1.57mm aluminium tube is on the left hand side. Drill two 1.6 diameter holes 4mm apart from each other. The holes are aligned vertically.
- Cut two 2.5cm pieces of brass rod and then make one 3mm shorter than the other
- Superglue the rod into the two holes. Place the longer one in the bottom hole.
- Cut out the wind vain from the plan and trace it onto the brass sheet. Again try to minimise the space it takes up.
- Cut out the wind vain and trim the bottom two corners like I have done in the photo
- Lay the two brass rods over the wind vain. The top one is perpendicular to the back edge of the wind vain. The other rod will form a slight angle.
- When you are happy with this, tape the tailbone and wind vain down then solder them together.
- A small optional detail you can do is: cut a piece of brass rod to 5mm and glue it to the gearbox housing and tailbone. This part is called the vain spring.
Step 14: Attaching the Shaft to the Gear Box Housing
- Slide the piece of piano wire coming out from the hub into the 1.57mm aluminium tube
- Slide the other piece of 1.57mm aluminium tubing that was cut to 2mm over the and glue it in place. Tip: when the glue is drying spin the rotor so it does not get glued in place.
Step 15: Pump Mechanism
- Cut a length of brass rod to 15.3cm
- Drop it in between the 4 pieces of brass until it reaches the base
- Solder in place
- Drill a 1.6mm diameter hole in the balsa dowel
- With a blob of superglue slide the dowel over the brass 15.3mm brass rod. Make sure the bottom dowel is in line with the bottom of the rod.
Step 16: Base (Optional)
- Use a compass to make a 7cm diameter circle on the 6.65mm balsa wood sheet then cut it out. Tip: I attached the circle to the end of a drill and sanded it while spinning.
- Cut out a 7cm diameter circle from the fake grass, again using the compass to mark it.
- Glue the fake grass onto the balsa wood base
- Use pastels or brown paint to colour the balsa dowel, the platform and also around the circumference of the base.
- Slide the gearbox housing over the 15.3cm long brass rod
- Finally superglue everything onto the base and now the windmill is completed
Step 17:
I hope you have enjoyed this instuctable as much as I have enjoyed making and writing about my windmill project.
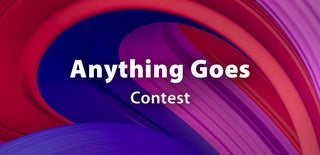
Runner Up in the
Anything Goes Contest