Introduction: 2x4 Electric Violin
"You were so preoccupied with whether or not you could that you didn't stop to think if you should."
That is the 2x4 electric violin in a nutshell. An affront to both 2x4s and violins alike, but not without its charm.
This project actually turned out better than I had expected - I'm fairly pleased with how it looks, feels, and plays. Is it the best violin I've ever played? Not by a long shot. But it was very fun to put this thing together from a piece of scrap lumber in my garage.
I'm so proud to be the Grand Prize Winner of the Instructables 2x4 contest! Thank you all who viewed and voted! I encourage anyone with the interest and the tools to try their hand at making an electric violin - it's surprisingly easy. I've also just listed it on etsy if anyone would like to purchase one: https://www.etsy.com/listing/266861772/electric-violin
-Aaron
Step 1: Materials
Tools used:
- Band saw
- Belt sander
- Wood carving knife (I used a pocket knife)
- Coping saw
- File + rasp
- Power drill
- Clamps
- Sand paper (60 grit and up)
Materials:
- One 2x4
- Violin fingerboard (with nut attached)
- Violin Chinrest
- Violin bridge w/ pickup
- Violin strings
- Violin shoulder rest
- Wood glue
- Paint, clear finish
To play it, you will also need a bow, which is beyond the scope of this instructable. You will also need an amplifier and a pre-amp (because the signal from the pickup is too weak for a normal amp), although if you play this violin in a quiet room you will still be able to hear it - just like an electric guitar without an amp.
Step 2: Design
*WARNING: My sketches are not to scale - they are visual guides only*
The first thing you must do is decide on the design. Fortunately, due to the dimensions of the wood, you don't have a whole lot of choice in the matter. My own design is based on some rather minimal electric violin designs I've seen around the web. There's no shoulder bout and no faux-violin body simply because there was no room on the board for it. If you want more options for your instrument shape, I would suggest making the base of the instrument like I have here and then crafting the other shapes out of another piece of wood and gluing them on.
Electric violins, by their nature, don't need to be as meticulously crafted as traditional violins because the sound wave propagation is not determined by the shape/density of the body of the instrument but by the small pick-up on or in the bridge. This allows for great flexibility in how you design the shape of your violin.
There are still a few dimensions to keep in mind for optimal setup.
- The distance from the bridge to the nut is approximately 13in
- The bridge will have to sit lower than the fingerboard (notice that on traditional violins the neck is attached at an angle - this is not necessary for an electric violin, but you must account for the height of the bridge when designing your violin)
- The G-string should be 5mm above the fingerboard and the E-string should be 3mm above the fingerboard. Some luthiers mave vary these dimensions slightly.
- Also, remember that the tension of the strings will put the instrument under considerable stress. At the very least, there should be a straight mass of wood all the way from the head to the tuners to prevent warping of the body. Aside from that, shape it how you want - you can carve a likeness of Steve Urkel and glue it to the shoulder bout and it would be OK (and, frankly, pretty awesome)
A few more things to keep in mind:
- Carefully mark your center line - it will make lining up the finger board much easier once you've started shaping the body.
- While it is certainly possible to make a fingerboard, for this project I did not want to get into that. I know a luthier and she let me dig through some of her discarded fingerboards for one that I could use. They can also be purchased for about $10 on Amazon or Ebay.
- Trace the fingerboard on the 2x4 and mark where the top and bottom of the nut are. Also mark where the bridge goes.
- If you want your pegs/tuners to be on the head of the instrument, unlike my design, you will probably want a tailpiece. This can also be purchased from a number of online sellers.
Step 3: Shaping the Body
Body
Once you've finished your design, transfer it to the top of your board. Because I do not have a planer and I consider the flatness of the neck to be one of the most significant parts of the instrument, I drew my design so that the flat surface of the neck (which is later glued to the fingerboard) is the face of the 2x4. I then angled the body slightly to make up for this.
Using a band saw and/or coping saw, carefully carve out the shape of the instrument. Leave a little extra room on each side of the fingerboard - we will later sand the neck to size with the fingerboard attached.
Then flip the workpiece on its side and draw the profile of the instrument. Cut it out with the saw. (Keep in mind the radius of your bandsaw - I knocked the blade off track at least 2 times while trying to make a tight curve. Later I just used the coping saw to clean that bit up.)
Now is also the time to drill the holes for the strings/pegs. For my design, I drilled 4 holes in the head to hold the ball-end of the strings (note that this is reverse of how a traditional violin is strung). I also cut a small channel on the bottom of the head so the balls don't protrude. Change drill bits and drill holes for the tuning pegs behind the bridge.
Neck
To make the shape and contour of the neck, I turned to my knife. If I had a dedicated wood carving knife, I would have used that, but all I had on hand was my trusty opinel pocket knife. Overall it worked pretty well, although that thing does have a thin blade which made some of the shaping a little more difficult. Careful with splintering - I don't do much carving so I don't know if this is a normal thing, but several times I was whittling an edge and seemed to catch a splinter that just got bigger and bigger until it took out a chunk of wood exactly where I didn't want to.
After the knife, I used a file/rasp to tidy things up a bit.
In order to finish the shaping of the neck, we need to attach the fingerboard temporarily. Using a small amount of glue (we will be removing the fingerboard in a minute, so don't go nuts) attach the fingerboard to the neck and clamp it. Let it set for a bit then use your sander to trim down the edges of the neck until it is flush with the fingerboard. Remove the fingerboard and don't forget to sand down the glue left on the underside. Remove the fingerboard once you've made the sides of the neck flush (I used a chisel and carefully wedged it).
Drilling
Two things must be drilled - holes for the strings at the top of the neck, and holes for the geared tuners near the chinrest. I don't have a drill press, so things weren't perfectly aligned, but it's not so far off that it really bothers me.
For the small string holes, I used the smallest bit I had.
For the tuner holes, I ended up using a 9.5mm brad point bit, which was just slightly too small. I was able to eventually (and with great effort) get the tuners to fit through the holes, but it would have been much better to use a 10 or 11mm bit. When drilling, try as much as possible to make the holes at a 90 degree angle to that part of the work piece. You want the gear box to sit flush beneath the wood.
Sanding
You know what to do. Start low and work your way up. I started at 60 and for most of the instrument didn't go higher than 150. I mean, it's only a 2x4.
For the neck, I went up to 600. Your hand spends a lot of time moving around the neck so it only makes sense to make this part as comfortable as possible.
Finish
I decided to use a traditional clear finish on the neck and paint for everything else with black spray paint.
Step 4: Assembly
Tuners
This was kind of a bear because my drill bit was just barely too small and I was too lazy to get back in the car and make another trip to the depot. It worked out in the end - I just used pliers to help get everything in place. Don't forget to put the washer over the top of the tuner before screwing in the bushing. Since I basically had to jam, twist, and bribe my tuners to get into position, I didn't bother with the small screws that attach the tuner to the "headstock". If you followed my directions and used a larger drill bit, you will want to screw the tuner in place to keep it from moving and buzzing.
Fingerboard
We'll need to use a little more glue this time. I laid two thin strands of glue running the length of the neck (be mindful of where the body stops being in contact with the fingerboard). Clamp it down, clean away the squeezed out glue, and let it set for a bit. I took of the clamps after about 45 min. It would be wise to wait to string the violin (at least not at full tension) until 24 hours after you applied the glue.
Bridge
The bridge blank I ordered needed to be shaped before I could use it. I marked the area I wanted to eliminate and then set to work with the belt sander. Use the belt sander for the top curve and the contour of the profile, but not for the feet. For the feet, I used an old luthiers' trick: attach a piece of sandpaper with double sided tape on the place the bridge will sit. Then move the bridge back and forth along the sandpaper until the feet have the same contour as the body.
Using a file, make four notches along the top ridge of the bridge for the strings. If in doubt, check pictures of violin bridges online to see how it should look.
When you position the bridge, you may want to remeasure it's position - at this point you won't have any of your original pencil markings to help you and bridge distance is one of the few dimensions we need to be mindful of (~13 inches from nut to bridge).
Step 5: Closing Remarks
I wanted to record a video so you can hear the results, but I broke one of the strings when I was putting it on. I thought it was an e string, but it's possible that it was a thin a string. That's what happens when you try to use old unidentified leftover strings. I'll get a new set of strings and make a video - it really does sound good.
The next step is to get a pre-amp. I'm planning to use an arduino to make a combination pre-amp and effects processor, but you could just as easily buy one and install it.
I also intend to mount an old shoulder rest to the bottom so it's a little easier to play.
I hope you enjoyed reading my instructable! If you build one, I'd love to see pictures!
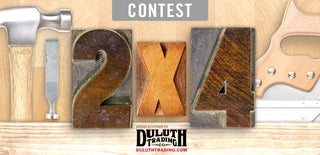
Grand Prize in the
2x4 Contest