Introduction: 2x4 Wave Coffee Table
I have always been amazed by those ridiculously cool parametric tables that are built out of hundreds of slices of wood. It is pretty awesome to think how a flat board can morph into such an organic and fluid-looking shape. I have also been dying to push the boundaries of my new miter saw. Enter the wave table.
In tackling the first iteration of this project, I opted to stick to things that I know and things that I can get easily. 2x4s are some of the most common and low-cost materials out there; a perfect candidate for my wild experiments. My most powerful tool though is the knowledge of trigonometry. That's right, trigonometry. Please, stay with me here! It's not going to be that bad...
What I have set out to produce here is a project that not only looks neat, but is relatively low-tech, low-cost, and attainable by even the most basic woodworker. I also hope that going through the steps outlined here will leave you, your students, children, friends, or whoever else with a new found appreciation for what a little bit of math can do. I know I would have paid a lot closer attention in class had I seen this!
I have been dreaming up this project for some time now, and with the New Year has come a sense of urgency to finally bring it to fruition. I have also not published an Instructable for some time, so I needed to change that as well. I hope that you enjoy. Let's get going, we've got a long math lesson ahead.
Step 1: Some Disclaimers
Before we dive in I want to be clear about a few things...
- SHOP SAFETY IS EXTREMELY IMPORTANT. Know how to use your tools safely because that miter saw will own you. Wear protective equipment at all times. It will be hard to see your finished product when something gets lodged in your eye.
- I AM NOT A PROFESSIONAL WOODWORKER. My means and methods may be lacking at times. I make lots of mistakes. Please tell me if you know a better way to do something or if you see a way I can improve.
- 2x4s ARE NOT HIGH QUALITY MATERIALS. They are made for framing houses and doing other rough jobs. They have knots, gashes, are soft, don't finish well, etc. There are better materials for furniture projects such as this, but I am trying to keep costs down here.
- THERE ARE BETTER TOOLS FOR THE JOB. Namely, a drill press, jointer, and planer. My shop is small and my budget is limited.
- TRIGONOMETRY IS AWESOME. The sooner you start believing this, the smoother this is all going to go. Embrace it. You have no choice...
With that off my chest, it's time for some math. Better start believing...
Step 2: Here's Your Sine
Before we get started, you need to understand how all of this works exactly. As I have mentioned several times already, the answer lies somewhere in that class you slept through back in high school. I'm talking trigonometry!
The main principal behind trigonometry is that, in a right triangle, the lengths of each side of the triangle occur in ratios proportional to the other, acute angles. Recall that the interior angles of a triangle always add up to 180-degrees, and you are off to the races with trig.
To review, the three main trigonometric functions are:
SINE: sin(angle) = length of opposite side / length of hypotenuse
COSINE: cos(angle) = length of adjacent side / length of hypotenuse
TANGENT: tan(angle) = length of opposite side / length of adjacent side
There are 3 other functions as well (COSECANT, SECANT, and COTANGENT), but they are basically just rearranged versions (inverses, to be specific) of the main three and are therefore unnecessary. This is why you typically don't find them on calculators...
With any trig application, there are multiple ways of looking at a problem, but for our purposes we will look at it relative to the bottom of the boards and the floor (see diagram above). This scenario can be expressed as:
sin(90 - miter angle) = height of table / length of board
In building our table, we will set both the table height and the angle, which allows us to solve for the length of the board. Nifty, huh? Let's try it out.
PRO-TIP: You could also use COSINE if that makes more sense to you. Here's how it would look:
cos(miter angle) = height of table / length of board
Step 3: Calculation Station
So, now that we're all trigonometry experts, let's apply what we know to our table. A typical coffee table is around 18" tall, so we will start with that.
My miter saw will adjust up to 50-degrees, so we will set that as the maximum angle. Minimum angle will be 0-degrees on the saw, equivalent to a straight 90-degree cut. To create our wave we will reduce our miter angles in 10 degree increments between our maximum and minimum angles.
PRO-TIP: A smaller increment will result in a smoother looking wave.
Applying the math we learned in the last step, our 40-deg miter board would look like this:
sin(90-40) = 18" / length of board --> length of board = 18" / sin (50) = 23.497"
To make things a bit more organized as we go, we will apply part numbers to each different miter angle. I used A1-A6. So...
A1 --- 50-deg miter --- 18" / sin(90-50) = 28.003" --> 28"
A2 --- 40-deg miter --- 18" / sin(90-40) = 23.497" --> 23-1/2"
A3 --- 30-deg miter --- 18" / sin(90-30) = 20.785" --> 20-25/32"
A4 --- 20-deg miter --- 18" / sin(90-20) =19.155" --> 19-5/32"
A5 --- 10-deg miter --- 18" / sin(90-10) = 18.278" --> 18-9/32"
A6 --- 0-deg miter --- 18" / sin(90-0) = 18.000" --> 18"
See, that wasn't so bad...
Step 4: Material Math Miscellany
So, we've got our board lengths figured out, but more math still remains. We need to know some quantities before we head to the hardware store. Let's get to it.
For the sake of balance we will complete 1.5 cycles of the wave, resulting in sort of an S-shape.Therefore, our pattern looks like this (dropped the "A" to fit on the page :/ ):
1-2-3-4-5-6-5-4-3-2-1-2-3-4-5-6-5-4-3-2-1-2-3-4-5-6-5-4-3-2-1
Tallying this all up, there are 31 total pieces. The actual thickness of of a 2x4 board is around 1.5", so 31 multiplied by 1.5 means our pieces of allthread need to be at least 4 ft long (give it a little slack).
Breaking things down even further, these are the quantities of each board:
A1 - 4
A2, A3, A4 & A5 - 6
A6 - 3
Multiplying these quantities by the lengths calculated in the last step results in an overall length of approximately 55 ft. We will round this up to 60 ft to be conservative.
We can use some more trig functions to solve for the width of our table as well. Using sine and tangent, I calculated about 27" wide. Therefore, our glass top will need to be at least 27" W x 46" L.
And with that you have a near complete materials list for the project. Isn't math so very useful?
Step 5: Tools
You'll need a few tools to pull this off.
Tools (required):
- Miter Saw - with at least 10-degree increments, max angle of 50-degrees
- Drill
- 3/8" drill bit - step up to 7/16" if you want some slack in your holes
- Punch or nail - really, anything pointed will work
- Hacksaw
- Square
- Yardstick - Needs to display at least 32nds of an inch
- Crescent Wrench
- Pencil
- Protractor
- Compass
- Cardstock or any thick paper
- Exacto Knife or any small tipped blade
- Calculator (PRO-TIP: turn the calculator on your phone sideways for trig functions)
- Oscillating sander or sanding block
- Paintbrush
Obviously, this can get much easier if you have some better tools. Here's what I would recommend based on some of the challenges I ran into during my build:
- Drill press
- Planer
- Jointer
- Framing square
- Measuring tools with 64ths of an inch marks
- Access to CNC machine or Laser cutter
Step 6: Building Materials
The following materials will allow you to build it just like me. Obviously if you choose to add more layers or adjust any heights (totally OK, and very easy to do now ;) ) you will need to adjust. Based on our calculations from earlier, we will need the following materials:
- 2x4s --- 60ft --- I used six 10ft pieces
- 3/8" Allthread --- 2 pieces > 48" long. I could only find 72" so I'll have some leftovers :/
- 3/8" Nuts --- 4
- 3/8" x 1" Washers --- 4
- 3/8" Lock Washers --- 4
- Screw-in Non Slip Rubber Pads - 7
- Sandpaper - I used 80 & 150 grit --- your call based on your desired finish
- Paint - more on this later
- 1/4" thick sheet of glass, probably around 30" x 54"
Optional:
- Felt pads - if you have wood floors ;)
And that's about it. With the exception of the glass, I found all of this at my local hardware store for under $100. Depending on the quality of materials you buy and where you are located, your costs could vary significantly.
Step 7: What's the Miter?
Enough math and planning...time to play with tools! Break out your miter saw and set the miter angle at 50-degrees.
Clip one end off of a board to get started. Then make your marks using the yardstick and pencil and cut out your pieces. I recommend cutting the large ones first.
Repeat this for each angle until you have cut out all the pieces listed on your material sheet.
PRO-TIP: If you start by cutting all the longest pieces (A1, 50-deg miter), work your way down incrementally, and buy the 10ft sticks I suggested earlier I can almost guarantee that you will have just enough material (negating any mistakes or unusable spots of wood). I was left with about 4 feet of the last 2x4, nearly matching my 55ft calculation perfectly.
Step 8: Dance a Jig
Two pieces of allthread will hold the piece together. By running them both through the center we also reduce the number of penetrations we have to make in the piece, which adds some aesthetic value.
In order to prevent twisting, both pieces will need to be offset from the center of the board, as I learned the hard way. I honestly knew better, but I had another idea and went for it. Mistake. Luckily it was nothing some spare dowel and wood filler couldn’t fix ;)
The fastest and easiest way to mark these holes is using a jig. We could certainly go through and measure/mark all our pieces out one by one, but “ain’t nobody got time for that.”
To create the jig you will need a nice thick sheet of cardstock or paper. Grab one of your 2x4 pieces and lay it over the top of the sheet. Press down on the 2x4 to hold the sheet in place and trace along the sides of the 2x4. Now, grab your protractor and draw a line perpendicular to one of the lines you just traced in the approximate center of the sheet. Find the midpoint of this line and mark it.
Placing the point of your compass on the center mark you just created, draw a 1” radius circle. This circle will ensure that all of the holes are offset the same distance from the center of each board. Cool huh? Geometry is fun.
Use your protractor to mark angles 90, 80, 70, 60, 50, and 40 degrees relative to the perpendicular line you drew through the center of the circle. Be sure to do this on both sides of the line for both the top and bottom holes. The intersection of the each angle line and the arc of the circle is where you will drill your holes. Neato.
Using the Exacto knife, cut three small windows along the line you drew perpendicular to the edges of the 2x4. One near the outside edge, and one in the center. These windows will help you align the jig on the pieces in the next step.
PRO-TIP: Label your angles as you go to make finding the right one easy later. 40-deg = A1 and 90-deg = A6. You fill in the rest.
Fold the cardboard along the lines you traced off of the 2x4 and the jig is ready for use. Alternatively you could tape or glue some guide rails flush with the same lines. It’s up to you. See that wasn’t so hard.
If this was a little too much for you to take in (or you are just feeling lazy) don’t worry. I am a bit confused myself, but I have you covered. Refer to the drawing above or download the attached SVG file if you get stuck. For all you high-speed CNC and laser cutting people, with a little doctoring you should be able to convert it over to G-code and cut these out. I totally would have done it, but I wanted to demonstrate how it’s done sans CNC for those of us working on a budget.
Attachments
Step 9: Make a Mark
Now we will mark our hole locations using the jig we just made. First, we need to find the center of the board. An easy way to do so is to draw diagonal lines connecting each of the corners. The point where they intersect is the center of the board. See, isn't this geometry stuff awesome?!?!?!
Once you have found the center point, pull out your square and draw a line through the middle of it and running perpendicular to the length of the board. Place the jig by aligning the lines on the template with the lines drawn on your board. This is where the little windows we cut earlier come into play.
Using your punch or nail, mark the top and bottom holes for the board. This hole will help prevent your drill bit from walking when it first bites into the material. Pay close attention to the orientation of your holes. To simplify this as best I can, the line running through them needs to be perpendicular to the top surface of the table.
With everything marked, remove the template. It’s time to drill.
Step 10: Drill Baby, Drill
Using a drill or drill press, drill a 3/8” hole through each of the marks you just made. Be careful to keep the bit straight as you penetrate the board. This will save you some time later by preventing twists and binds.
I have an admission to make... Apparently I totally suck at drilling straight holes. Embarrassing. If you are terrible like me it's OK, there's still hope. You may have work a bit harder than your fancy friends with their fancy drill presses, but this will still all work. As mentioned in the tools section, stepping up to a larger bit will give you some slack to work with if your holes aren't quite perfect.
Step 11: Testing...Testing 1, 2
As confident as you may feel, a test fit is imperative at this point. It will help ensure that all of your holes are big enough, are in the right location, and will point out any other issues you may have developed thus far. As mentioned before, it revealed plenty in mine.
To test it out, simply screw a nut and washer onto the end of each piece of allthread and start stacking pieces in the sequence we devised earlier. It works best to do this vertically. Gravity is your friend. Physics is almost as cool as trigonometry!
Number your pieces as you add them so that after you make adjustments later, they each find their way back to the same places. If you encounter pieces that are hard to slide on, do not align, or generally look off, make a note of it. I simply wrote what was wrong on the piece to make it easy to track.
Due to my poor drilling I had several tight pieces and minor alignment issues, so I was very glad I took the time to check before I got too far ahead. Small holes can be enlarged by reaming them out with a drill bit and any length issues can be marked and handled back out on the miter saw.
Make the necessary adjustments and repeat this step until you are completely satisfied with how your piece goes together. This is why I used allthread. You can assemble/disassemble as much as you want.
Step 12: Scuff It Up
Once you are happy with how your piece is taking shape, go ahead and trim off the excess allthread using the hacksaw. Take your time to ensure a straight cut and not to damage the threads on the ends.
Now, remove all of your pieces from the allthread (again? I know...), and start prepping for paint, i.e. sanding. This will ensure a smooth finish when we paint, and will also remove any of the stamps, etc. you typically find on 2x4 lumber. I hit mine with some 80-grit sandpaper first, then finished it off with some 150-grit.
Keep in mind that these are still 2x4s. They are not fine pieces of wood, and will likely not be perfectly smooth either. This is where that planer would have came in sooooo handy.
Step 13: Fifty Shades of Green
Painting is an extremely open-ended topic, but I wanted to describe my method because I think it turned out pretty cool. Basically, I wanted the color of each piece to fade from A1 = light to A6 = dark. Right off the bat, this probably sounds really difficult to pull off, but it is actually surprisingly easy.
This method is easy because the paint companies do all the work for you. They typically do an excellent job of grouping similar colors to aid in your selection of the perfect shade for your home. These groups are, more or less, color families, which go nicely together because of some uniting feature.
What we also have working in our favor is the is that we don’t have that much to paint, and paint companies like to hand out small samples for indecisive homeowners to debate the merits of Robin’s Egg Blue vs. Shimmering Sapphire vs. Utah Sky vs. Shimmering Mist vs. [Insert Obscure Paint Name Here]. You get the point. These samples typically come in 8oz cans, which should be more than enough for this project. They typically aren’t free either, but are significantly cheaper than buying a full can.
So, now that the secret is out, go to your local paint store and navigate over to the shelf full of paint swatches. Find a paint swatch that you like with at least six colors on it --- your choice. Ask for a sample of each color for a series of 6 colors on the swatch and BOOM! Sick fade, bro!
Step 14: A Fresh Coat
With all of your paint ready to roll (no pun intended), apply it to your boards using whatever method you prefer (i.e. brush, spray, don’t paint at all, etc.).
I chose to brush mine because it was cold out and I was forced to paint inside the house. Spray painting inside the house without ventilation is not a great idea.
Apply a couple coats and let your pieces dry per the paint manufacturer’s guidelines.
PRO-TIP: Don’t get too carried away on the area between the holes, or anywhere where the pieces overlap. Focusing only on what’s visible can save you a lot of time and paint!
Step 15: All Together Now
Once your paint has dried we can go ahead and reassemble the piece. Ensure you have installed a nut, a washer, and a lock washer on one end of the allthread (should already be there from earier) and slide the pieces on in the same order you used in the test fit. Adjust the boards as needed so they are level on top/bottom and there are no gaps between them.
Once all of the pieces are on, install a nut, washer, and lock washer on the opposite side of the allthread and snug it up to the last board. With the help of a friend (to hold the opposite end), tighten the nuts using a 9/16" wrench or a crescent wrench. No need to torque it down super tight, but make sure it’s not going anywhere and that you have closed any gaps between the boards.
Step 16: Smooth As Glass
What we have so far looks pretty sweet, but it’s no table yet. To finish it off we will top it with a piece of glass. You are welcome to use any other flat sheet of material as well, but I think that glass does a good job of showing off the pattern below.
Per our calcs from earlier, our sheet needs to be at least 27”W x 46”L. I went with a 30’ x 60 sheet that I had been using to protect a desk (isn't it great when things just work out like that!)
The glass can probably just sit on top of the boards, but I opted to install some small rubber pads to prevent sliding. I installed these on each of the A1 and A6 boards.
PRO-TIP: If your table top did not come out perfectly level, use some shims underneath the rubber pads to dial it in.
Step 17: Netflix and Chill
Transport your finished table to its final destination, preferably between the TV and a cozy couch. Break it in by binge-watching a whole season of something on Netflix. Crack open a couple cold...sodas, or pour a tall glass of...lemonade, and revel in your new creation.
But seriously, enjoy your work and put it somewhere where you can show off. I was literally mesmerized by this thing for hours just assembling it and hopefully you are too.
Way to go! You are awesome and are well on your way to becoming a regular trigonometry wiz...there, got it in one last time!!!
Step 18: School of Hard Knocks
Hopefully you knocked it out and the only problem you had is that you couldn't complete the last step because you are already caught up on all the latest shows. Unfortunately, for me, I had a few missteps that I would like to point out here. Maybe you are in the same boat. Let's reflect.
My drilling was terrible. I need a drill press next time.
I need a more precise yardstick. I think I may have been off slightly on some of my measurements.
I underestimated how low quality 2x4s generally are. No amount of sanding I did helped much and I ended up with plenty of dents/scars/etc. due to the softness of the wood.
A planer and jointer would do wonders for consistency and improving finish.
My fade didn't turn out quite like I planned. I think this may be due to the fact that the angles and lighting already produce sort of a natural fade with the shadows. The jump between A2 and A3 seems more dramatic than it did on the swatch.
I didn't trust my gut and ended up drilling a bunch of extra holes. Thankfully, they are hidden below everything, but it would have been nice to get it right the first time.
And other than that things went great! Hopefully you can learn from these, improve upon them, and knock this thing out much better than I did.
Step 19: Thank You!
Thank you so much for taking the time to read this Instructable. I had a lot of fun putting it together and hope that you enjoyed it.
I put a lot of time and effort into this project, and the only thing that makes it worthwhile is your continued support and feedback. Please hit me up, send some love, or follow me on any of my channels if you would like to stay posted on what I'm up to.
Time to go kick it on the couch and put my feet up on the new coffee table. Later!
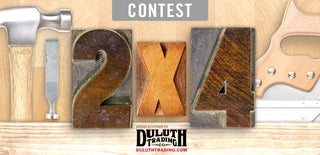
First Prize in the
2x4 Contest
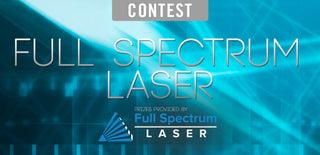
Participated in the
Full Spectrum Laser Contest 2016