Introduction: Resin Cast Coasters
There is a war being waged in your home. Drinkware and condensation have conspired in a brazen and brutal attack on your furniture, and the casualties are mounting. The stakes are high and the time for action is fleeting.
But there is hope. A growing resistance rises against this awful tyranny. They call themselves: coasters.
While their bravery is unrivaled, not all coasters are comprised of the same fiber. The cardboard ones suffer the greatest casualties. Cheap and inexpensive, they arrive in great waves, but soon wither amidst the moist volleys of their enemy. Those built of stone and wood fight bravely, but are slow to reach to the battlefield and demand the highest wages and rations. What your furniture desperately needs is a lightning fast, resilient, and capable weapon. Fortunately, a band of top scientists, hidden away in a secret lab in remote Texas, is engineering such a solution.
Advances in machining, mold-making, and resin casting have allowed us to turn the tide in this conflict. High-quality, battle-ready coasters are now being produced in record time. Adaptive camouflage is enabling them to blend into any surroundings, advanced polymers keep them strong and nimble, and a unique sense of value and purpose helps them make a bold statement on any battlefield.
So, brothers, sisters, humans, fine furniture owners, heed this call to action. Help put an end to the great oppression. Invest in coaster bonds today and let’s make some resin cast coasters!!!
Check out the PROJECT VIDEO!!!
Step 1: Tell Me Why?
While the situation is not nearly as dire as I made out in the last step, the qualities listed really are the true reasons that I came up with this idea. These coasters are durable, quick to produce, cheap (at scale), available in an almost endless number of color combos, and they just look fun and cool.
I first came up with the idea when I became frustrated at the time and effort CNC machining coasters was taking. Back in college I had the opportunity to try my hand at some casting, and was amazed by the detail it was able to consistently produce in a short time. No solution is ever quite perfect, but this seemed like too good of an idea not to try.
Step 2: Tools & Materials
Materials:
- Lexan Polycarbonate, acrylic, or machinable wax - 1/4" thick, around 4"W x 4"L
- Alumilite Amazing Mold Rubber
- Alumilite RC-3 Casting Resin OR Amazing Casting Resin (have had good results w/ both)
- Stencil-making material - 2 sheets
- Hot glue sticks - I prefer low temp
- Sandpaper - 80 & 220 grit
- Dosing cups - should come in the resin packs above
- Popsicle sticks
Tools:
- CNC router (I realize not everyone has one of these around...find a friend or a local maker space!)
- Hot glue gun
- Scissors
- Oven - preferably a craft oven, but an old toaster oven works too
- Orbital Sander
Software:
- Inkscape or Illustrator - any vector graphics software
Step 3: Mind for Design
Coming up with a design is obviously a very open-ended item. At the time these were made, I had a huge crush on that "long shadow" effect, so that's what I went for. However, I've also done some mazes and window pane looking stuff. Get creative and find something that suits you, but keep these general guidelines in mind. These should apply to anything produced using this technique:
- Design should be saved as an SVG file. Most CAM software requires this anyway.
- Overall dimensions should be approximately 88mm x 88mm. There is no standard coaster size, per se, but this has worked generally well for me.
- Inlays should be a minimum of 1/8” wide, i.e. the width of your milling bit. Just good CNC practice here. Also, the resin will flow and cure better in a large area (the chemical reaction that allows resin to cure works fastest in the largest areas).
- No open-ended inlays, meaning all should be completely contained within the main body of the coaster. Think of the inlay voids as little above-ground swimming pools…rip a side off and all the water comes out. Resin works the same way.
- Any text needs to be converted to paths. More basic CNC/CAM design. Also, let me reiterate that inlays must be at least as wide as the bit. Big, bold, block fonts work the best. I like to use one called Aharoni.
Once your design is complete, group all of your inlay paths as a single object. This will make life much easier in the next step, especially if you have a very complex design.
And that should get you going. Have fun with this step, get creative, and really try and visualize how the inlays and main body will work together.
Step 4: Wham, Bam, Thank You CAM
Import your completed design SVG file(s) into your CAM software (Here I am using Easel by Inventables). Adjust your work area and material settings to match the properties of your material. My settings were as follows:
Bit Diameter: 0.0625 in = 1/8"
Feed Rate: 25 in/min
Plunge Rate: 9 in/min
Depth per Pass: 0.02 in
Select your inlay(s) and set them to a fill pattern with a depth of 0.05 inches or 1 mm. This depth will give us enough volume for our inlay to cast properly but also avoid creating a deep void that is difficult to de-mold.
Select the main body of the coaster and setup an outside cut pattern to the full depth of the material. I do not use tabs so I do not have to cut/sand them later, but I will leave that up to you.
Once everything is set properly, go ahead and generate your G-code.
Step 5: Walk the Blank
Secure your piece of Lexan on the wasteboard and prepare your CNC machine to cut. Once all systems are go, start your machine and execute the G-code program to cut out your coaster.
Once the program is complete, power down the CNC machine and remove your coaster. Inspect its sides and the inlays for any burrs or dust, and remove them using as best as you can. It is import to leave the surface of the blank as pristine as possible, as the molding/casting process will pick up even the faintest details. Pay particular attention to the top surface. Burrs or rough edges in the bottom of the inlays are not that big of a deal since they will be cast over later.
What's great about these blanks is you can use them again, and again, and again... As long as you take care of them they will be around to make many molds.
Step 6: Think Inside the Box
A mold box is basically what it sounds like. It seals off the volume surrounding the mold blank, allowing the mold rubber to cure around it. Recall my crude swimming pool analogy? Same concept. You’re catching on fast.
Begin by securing the mold blank with the INLAYS FACING UP to one sheet of the stencil sheet using double-sided tape. Place the blank at least 1” from the edge of the sheet. I repeat, inlays go up!!! This will allow the mold rubber to flow into them and create a mold negative.
With a scissors and ruler, cut the second stencil sheet into ~1.25” wide strips. These will serve as our box’s side panels. Use the strips to form a “fence” surrounding the entire mold blank and offset by at least ½”. I recommend doing any bending and forming before gluing.
"Weld" your fence to the base sheet using the hot glue gun. Envision that you are constructing a water-tight tank. EVERY EDGE MUST BE COMPLETELY SEALED, including the vertical edges where you join separate panels. Be very liberal with the glue. A leak will not be fun to deal with later.
Be careful to avoid getting glue on the blank as this will compromise the finish you worked so hard to perfect earlier. The easiest way to do this is to glue from the outside as much as possible and not pass the glue gun (and the inevitable hot glue strings) over the center of the box.
Step 7: Make the Mold
Now that our box is formed, it's time to make a mold. Bust out the Alumilite Mold rubber, the catalyst, and a sturdy popsicle stick.
The mold rubber is formed by the chemical reaction that occurs when you mix the base and the catalyst together. As any good chemist knows, producing the desired result requires balancing both sides of the chemical equation that represents this reaction. This is a long-winded way of saying that, for the rubber to cure properly, you must mix it in the proper ratios.
For the Alumilite Mold Rubber this means a ratio of 12:1 (12 parts base to every 1 part of catalyst). You could try and calculate the exact amount needed and mix accordingly, but I prefer not to...here's why:
PRO-TIP: The easiest way to nail the mix ratio every time is to use the whole kit at once. An easy way to do this is to create multiple molds at a time. So, cut a blank for that second concept you’ve been dreaming up, cut a backup of your first, or find something else to mold (because casting is fun!).
Pour the catalyst into the base and mix well. Be sure to scrape all of the edges and the bottom of the container and do not stop until you have a completely homogenous mixture with no streaks. For the Alumilite Mold Rubber the final mix will be a light pink color.
Slowly pour the mold rubber into the mold boxes starting at the lowest point and letting the rubber gradually fill the box. Fill each box to around 1” depth.
Now kick back, relax, and let it cure. According to the product specs this takes around 2 hours.
Step 8: Break the Mold
After your two hours is up, check to see if your rubber is fully cured and is not tacky to the touch. If everything is firm and smooth, then carefully begin removing the side panels of your mold boxes.
Once the panels are off, carefully pry the mold blank (with mold) from the bottom sheet. You can remove the mold here as well, but I find it easier to work with it detached from the main sheet (the mold blank is usually the most intricate and difficult piece to remove).
Slowly and very carefully remove the mold blank from the mold. It works best to start in one corner and work your way in. Use caution on the inlays as they are thin and could tear if you are too aggressive. Applying tension along the length of them works the best.
As intimidating as this all may seem, the mold rubber is very pliable and forgiving (which is why I prefer it over others). After a couple attempts, you will quickly get a feel for which surfaces of your blank demold the easiest, where it hangs, and the best angle of approach.
And with that you have made a mold! Way to go! The hardest part is over.
Step 9: Get Warmed Up
In order to achieve the best possible finish, the mold needs to be heated prior to casting. What this does is help prevent air bubbles from getting trapped in the bottom of the mold. To generalize greatly, the hot mold surface cooks the air out of the resin.
To pre-heat safely and effectively use a craft oven or an old toaster oven with temperature control. Set the heat on 140-deg and heat for at least 1 minute per lb of rubber.
Step 10: Master Caster
Finally, the moment you’ve all been waiting for. Much like the mold rubber, the casting resin must be mixed in certain ratios to cure properly. However, this ratio is 1:1 (equal volume of each), making this step significantly easier. Possibly the most difficult part is estimating the total volume of your mold.
A pour of around 6-8 drams in each dosing cup usually does the trick for me. Generally, the full 8 (16 drams total, mixed) is enough to pour one base coaster body and fill the inlays (coming up shortly) in another. Again, keep another mold on standby to handle any excess until you have your quantities dialed in.
Based on your volume calculation, pour the required amount of Part A in one dosing cup, and an equal amount of Part B in a second one. DO NOT MIX THEM YET.
Prepare for the cast by gathering your mixing cup, popsicle stick, and dye (optional) and arranging them so they are easy to access as you need them.
Retrieve the pre-heated mold from the oven and lay it flat on the table.
Step 11: Pour Some Resin on Me
Before you do anything, be aware that most of these resins have a short working time (around 1.5 minutes for RC-3). This means that you will need to execute the steps below quickly and deliberately. Doing smaller pours makes working within this timeframe very manageable.
Combine the two parts of resin plus any dye (just a couple drops) in the mixing cup and stir vigorously using the popsicle stick. Stir until the mixture is a uniform color. Remove the popsicle stick from the cup and set it aside.
Slowly pour the mixture into the mold cavity starting in the lowest point and allowing the resin to slowly fill to the top. Fill the cavity as fully as you can and stop pouring once you reach the top edge. Some overflow is likely, especially during your first attempts, and it can be sanded off later. Of course, this wastes resin so try to be as precise as possible with your pours.
PRO-TIP: After the pour, return the popsicle stick to the mixing cup and angle it so that it is immersed in any leftover resin in the cup. This will make cleanup much easier later as you can use the stick to pry the wasted resin out of the bottom of the cup (thus, saving your cup for another mix).
Now sit back and watch the magic unfold.
Step 12: The Cure
After the ~1.5 min work time is up you will notice a strange phenomenon taking place. Usually, starting along the sides or in the deepest part of the mold, the resin will begin changing from a transparent liquid to an opaque solid. It’s pretty mesmerizing to watch! This is the chemical reaction taking place, and you need to leave it alone and admire from afar.
The opaque blob will appear rapidly and then slowly spread through the entire casting. Give it at least 5-10 minutes to do its thing, as per Alumilite’s cure time guidelines.
Step 13: The Big Reveal
Once it has had plenty of time to cure, you can remove your casting from the mold. The reaction is exothermic (gives off heat) and recall the mold was pre-heated, so it will be warm to the touch. Remove it just as you removed the casting blank earlier, slowly and carefully.
Inspect the inlays for any irregularities. Sometimes a stray air bubble or two will get caught and leave small bulbs in the corners. These really won’t affect anything since we are about to cover them anyway, but you can remove them with a small pin or exacto knife. You’ve completed your fist casting! Congrats!
Step 14: Inlays Potato Chips
Pouring the inlays works just the same as the main cast, just on a much smaller scale. As such, we will need to pre-heat the casting before our next pour. Pop it in the oven for a couple minutes.
PRO-TIP: If you are moving fast and have just removed a warm casting from the mold then it may already be fairly warm, saving you some precious time and heating energy.
Prep your resin, mixing cup, dye (of a different color, optional), and stirring stick just as you did before. The only difference will be your mix volume, which will be significantly less in this case. If you were paying attention earlier, you may remember that it's handy to combo pours with subsequent coasters, i.e. say you poured a blue coaster base...Make your next blend a sharp yellow and use it for the inlays (for some good contrast) and as the base color for a new coaster.
Adhering to the same timeline, retrieve the casting, mix the resin and dye, and carefully pour the mix into the voids of the inlays. In this case I would actually recommend slightly overfilling the inlay voids. This will help ensure a nice uniform finish in the next step ;).
Once everything is filled then sit back and watch the magic unfold yet again. Almost done!
Step 15: On a Plane
Although it may not look like it, we’re on the final stretch! Right now you probably have a lop-sided, lumpy blob that doesn’t look very stable. That will change very soon.
Break out the orbital sander with an 80-grit sanding pad. We will use the rough grit to knock down any over-pours (inlays, and possibly the coaster base) on the coaster. I like to start on the main body and finish with the inlays.
Rough sanding is complete when all excess material is removed and the edges of all of your inlays are sharp and crisp. At this point the coaster should also be level (top and bottom). For aesthetics, I make sure to sand the entire surface, buffing out any glossy areas of resin. Sanding the edges is optional, but I generally prefer not to.
Finally, smooth everything out to a glass finish with some 220-grit sandpaper. Remove any dust using compressed air and/or a damp cloth.
Your coaster is finished!!!
Step 16: The Battle Is Over
I hope you had fun, learned a lot, and are super proud of your coaster(s). We’ve covered a lot, so you certainly deserve it!
Experimentation with different colors and/or multiple pours can be a lot of fun, and is highly encouraged. Above is a showcase of some of my favorites.
I think that these are very unique and, with the addition of your own designs, make for a nice conversation piece or gift for a friend. Not to mention, they really do work and hold up well. I have had some of the original concepts for well over two years and they still look and function great!
Step 17: Thanks!
I hope you have enjoyed this Instructable as much as I enjoyed making these coasters. Thank you for taking the time to read it! I hope that many of you will be inspired to try your own designs, and that I'll see some of those awesome "I made it" badges in the comments below.
If you'd be interested in a set of these without all the hassle of resin casting, please let me know. I have a small stash stored away that I would consider parting with to a good home. Plus, with all these molds ready to roll, a fresh new batch is only a few pours away.
So, brothers, sisters, fellow humans, table owners, we can do it! Together we can turn the tide in this war against those tyrannical glasses and their condensation allies. Get out and get making now! The future depends on it.
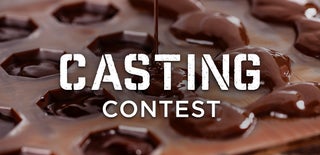
Participated in the
Casting Contest