Introduction: 3D Printed Electric Guitar
For my second custom guitar (see my first one here), I was inspired to use rapid prototyping technology rather than materials processing equipment by my students taking courses in my makerspace. This guitar was designed using the Onshape CAD program and 3D printed using LulzBot TAZ 6 printers equipped with the MOARStruder print head.
I am no professional guitar builder by any means, instead just a DIY maker enthusiast and Technology, Engineering, and Design teacher from New Jersey. I've put together this instructable with a beginner's take on the important do's and don't for guitar building, as well as a chance to share my failures and mistakes for you to learn from.
I hope you enjoy, happy making!
Step 1: The Design
Unlike my last guitar which was inspired by the Fender Stratocaster, this one is inspired by the Gibson Les Paul. Initially, I really wasn't too sure where I wanted the design to go, but I knew I was constrained by my printer's build volume and that I wanted to emphasize the 3D printing technology.
To achieve this, I created a hollow appearance by designing the guitar to be mostly open and see-through. The only exception to this are the large areas where the neck, bridge, and electronics attach. I also did not want any wires or knobs to be seen from the front, so they are all hidden in a pocketed panel on the back of the guitar. I also knew I would have to print this guitar in multiple sections to fit on my build plate, but that the neck's mounting point should not be split and printed more solid that anything else from a structural and tuning perspective.
I purchased these plans for the Gibson Les Paul and followed the dimensions loosely, mainly focusing on the neck length and distance from the bridge in order for the guitar to be tunable when finished. I also worked to make the neck angle correct for setting the action, this was something I messed up on my first guitar and had to shim the neck to get the strings at the right height.
Attachments
Step 2: The Components
There are endless levels of components you can choose for making a guitar. The choice between brands and quality vary extensively, and I am no expert on choosing them. I always figured that my cheap DIY guitars would do just fine with cheap and reasonably reviewed components.
- Neck - I used the same neck from my first guitar, great price and quality with a beautify appearance
- Pickups - I chose these cheap hum buckers to match the traditional Les Paul style
- Tuning Pegs - I went for well reviewed and chrome to match all the hardware
- Tune-O-Matic Bridge - Huge fan of the Tune-O-Matic wrap around style bridge for DIY projects, its only one piece instead of a two piece string holder and bridge. This makes install easy and its extremely adjustable for intonation.
- Harness and Components - I wanted a simple a vintage sound, this harness is like a classic LP Jr
- Neck Plate - I wanted to laser engrave this part so I went for a black anodized plate rather than chrome
- Strap Locks - I went for well reviewed and chrome to match all the hardware
- Strings - Personal preference really
- Glue - Depends on filament choice, I used gorilla glue for T-Glase
- Filament - Personal preference, I used T-glase but would recommend PETg
Step 3: 3D Printing
All the parts are cut to fit onto a print bed that is 280mm x 280 mm in X and Y. I chose to use Taulman T-Glase filament because I wanted the guitar to light up and change color based on music being played. The concept was cool, and a track for the LED light strip runs along the back outside of the guitar, however the filament choice was a mistake.
T-glase is a cool product, but its expensive, prints slow, and when you print at a high fill density, isn't very transparent. Looking back, I would have used natural PETg or even PLA. Working with the t-glase proved to be troublesome when trying to glue it all together and the lights don't shine all the way to the front of the guitar as desired.
Choosing the MOARStruder was also a mistake. It did cut the print time down by 60%, but also forced me to print at a layer height of 0.6 which proved to make the meeting points of the different parts riddled with gaps. Looking back, printing with PETg slowly at 0.25 would have been worth the time.
Step 4: Bonding the Sections
Before bonding the sections together, I inserted the bridge nuts so I could use them as an alignment point. I inserted bolts into the nuts and a bar across to hold them in the correct position.
For other sections, I used Irwin quick grip clamps to hold the guitar in position. For the glue, I chose to use standard, clear, expanding gorilla glue because of the large gaps between sections. If I had chose to use PETg that was closer, a loctite superglue would have been cleaner and easier to work with.
In some places, I actually melted and boding the plastic in a sort of plastic welding method using a soldering iron. This worked well for filling large gaps but didn't look too great with T-Glase, again I would recommend a different filament choice.
Step 5: Neck Install
Installing the neck is pretty straight forward if you have your measurements right and take your time. I drilled pilot holes into the body through the mounting plate, then clamped the neck in place while inserting screws.
Same idea for the tuning pegs. Position each peg in place and tighten using the mounting nuts on the top of the headstock. Then drill pilot holes and insert screws through the mounting holes on the back of the headstock.
Further adjustments to the neck angle may be needed once you get the strings on and check action height.
Step 6: Electronics
I installed the pickups into the pick guard, then installed that on the body of the guitar through the front. I then installed all the harness components into the back plate and soldered the wires to the pickups, as well as a ground wire to one of the bridge mounting posts.
Step 7: Strings and Tuning
Now the fun part! Here's where you can see your hard work pay off, or fall apart. String up the tune-o-matic bridge and strings through the tuning pegs. Before tuning, get the string height set because that will change all of your tuning that you do. Rotate the large bridge posts up and down to raise and lower the bridge to a desired action height. If needed, you can unbolt the neck and shim it to increase its angle.
Get the guitar in tune open strum, then move down to the 12th fret. The same note should be played in a different octave. If its sharp or flat, you can adjust the little slides under each string with a screw driver to get the note just right. If all of the strings are off, you can position the entire bridge closer or farther from the neck. This is a tricky process to get just right and its even harder on a plastic guitar.
Check out this video for guidance on setting the action and intonation. Once your strings are set, you can also adjust the height and position of the pickups for optimal sound. I raised mine by almost an inch to get them nice and close to the strings.
Step 8: Finishing Touches
For finishing, I sanded parts of the guitar where I glued and welded the pieces together. I then installed the strap buttons and enjoyed this DIY project.
It sits proudly in my classroom next to my first guitar and serves as an inspiration to my students in our maker space. Overall, I am pretty pleased with this project and already planning for Guitar #3.
Thanks for reading!
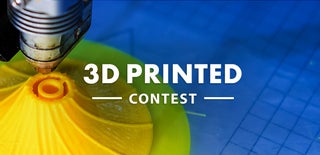
Second Prize in the
3D Printed Contest