Introduction: Build a Through-Dovetail Jig With 3D Printed Templates for Less Than $100
In this instructable I'll show you how to use Fusion 360 and a 3D printer to make a jig for cutting variably-spaced, through-dovetails with a router. My jig is made for use with an 11/16" cutting diameter, 8 degree dovetail bit, but you can follow my instructions to make your own jig for dovetail bits with different angles and cutting diameters. I already had the router bits and guide bushing, and was able to use plywood that I already had in my shop, so my project only cost me about $30 for the t-track and miscellaneous hardware. If you have to purchase everything needed to make your own jig, including the router bits and guide bushing you should still be able to build this for less that $100 US.
The jig consists of 3D-printed templates mounted to a 3/4" t-track. This allows you to vary the spacing of your dovetails by sliding them along the track. The t-track is mounted to a 1" thick backbone via small sections of track, which allows you to move the track in and out to fine-tune the fit of the dovetail by making the pin wider or narrower. The jig has 3/4" particle board backing boards on both sides of the backbone to provide a waste board that protects the body of the jig and helps minimize tearout. The top 1 1/4" section of the backing board is removable, so that it's easily replaced to provide a fresh surface for each joint setup. The 3D-printed templates are double ended, with a tapered end that matches the angle of your dovetail bit and guides the router bit to cut the pin, and a fork end with a slot that guides the dovetail bit for cutting dovetails slots. For both cuts, a guide bushing mounted in the router base follows the template to make the cut. I also mounted my jig in a base that clamps to my bench and makes it easy to clamp the stock in place when using the jig.
To build the jig, you'll need a 3D printer capable of producing clean prints (I'm assuming your already know how to operate your printer), and tools for cutting the track and wooden parts of the jig, as well as a drill or drill press for putting everything together. If you plan to use the same dovetail bit for which I made my jig, you can skip the Fusion 360 section and just print the templates and the t-nuts from my design (.stl) files. But if you need to make templates for a different dovetail bit, you'll also need Fusion 360 or a similar 3D modeling application to create a 3D model for your template. I'm a novice with Fusion 360, and it took me less than an hour to learn the basics of the program and make my first model. Each template takes about three hours to print on my printer (a Voxelab Aquila) and I made two test templates before I was happy with the result. Since I rarely make dovetails on cabinets deeper tham about 16", I sized my jig accordingly and printed a total of 10 templates - eight full templates for the main dovetails and 2 mirror image half templates for cutting half pins on the ends of the dovetail joint. It took me several days of printing to print all of the templates. I also designed a 3D printed, drop-in nut to work with the t-track because I wanted to be able to use 8-32 screws to secure the templates to the track and also to be able to add and remove templates from my jig without sliding everything off the end of the track.
Background
Through-dovetails are my preferred method for joining the corners of bookcases and small cabinets. In addition to adding a nice detail at the corners, dovetails provide a very strong joint due to the fact that they interlock and provide a large glue surface. For the past ten or fifteen years, I've been cutting through-dovetails using a router and a home-made jig similar to the one I describe in this Instructable. Making the jig was a bit involved, however because I had to figure out how to machine the pile of plastic templates with the accuracy required to produce good-fitting dovetails, and I ended up scrapping some of the templates due to poor fit. However, I managed to produce enough accurate templates to make a complete jig and the result has worked well for me over the years. I've used it to turn out rooms full of bookcases, storage boxes and small cabinets for myself and my daughters.
In recent months I've started to realize the benefits of owning a 3D printer and have used it to print replacement parts for sewing machines, vintage electronics, espresso machines, and my benchtop CNC router. As I've grown accustomed to using Tinkercad to design a part I need, I started thinking about more things I could do with a 3D printer. Then, while cleaning up after a recent woodworking project, I realized that the plastic templates needed for my dovetail template could be easily modeled and then accurately printed with my 3D printer. However, I opted to move from Tinkercad to Fusion 360 because I wanted to learn to use it and this seemed like a good project to do so. It turned out to be a very good decision, because I learned that Fusion 360 makes many things that I wanted to do much easier. I especially liked being able to draw my shape in 2D and then extrude it and refine it with just a few clicks or keystrokes.
Supplies
I used the following to build the basic through dovetail router jig.
- Fusion 360 (a free-for-hobbiests 3D modeling application) to create the 3D model of the pin-tail template.
- 3D printer, properly set up to print PLA prints.
- tablesaw to cut the wood parts of the jig and to cut the aluminum track to length
- drill press to drill mounting holes in the wood and aluminum parts
- digital calipers to measure parts for adjusting the fit
- combination square to layout parts and to assist in adjusting the fit of the dovetails
- cordless drill/driver for assembly
I used to following supplies in my project to build a jig capable of cutting 16" wide dovetail joints
- PLA filament
- a 24" length of 3/4" wide by 3/8" deep aluminum t-track, cut into one 17 1/2" length and two 1" lengths. I bought a pair of 36" length tracks for $26 from Amazon, but you can also get a pair of 24" lengths for $19
- (10) 8-32 x 1/2" long screws to fasten the templates to the t-track.
- (2) 8-32 x 3/8" long screws for mounting track to jig
- (12) 8-32 nuts
- (6) 1" long flathead wood screws
- (10) 1 1/2" long flathead wood screws
- 2 pieces of 3 5/16" wide x 17 1/2" long 1/2" (12mm) thick plywood (I used baltic birch), glued face-to-face to form the 1" thick backbone for the jig, or a similarly-sized piece of harwood planed flat
- 2 pieces of 2 1/4" wide by 17 1/2" long 3/4" thick particle board for the lower (fixed) backing boards on either side of the jig
- 2 pieces of 1-1/4" wide by 17 1/2" long 3/4" thick particle board for the upper (removable) waste backing boards on either side of the jig
I also used the following supplies to build a base for the jig, which makes it much easier to use if you're not using it with a router table.
- bottom board - 3 1/2" wide x 24" long x 1/2" thick plywood
- rear clamping bar - 2 1/2" wide x 1" thick x 20 1/2" long
- clamping bar - 2" wide x 1" thick x 20 1/2" long hardwood
- 2 clamp screws - 8" long 3/8-16 carriage head bolts, t-knobs, and washers
And here are the additional things you'll need to use your jig to cut through dovetails.
- Router with 1/2" collet and a baseplate that accepts Porter-Cable style guide bushings
- 8 degree x 11/16" diameter dovetail bit ($17)
- 1/2" straight bit ($18)
- 5/8" guide bushing with nut ($10)
Step 1: Design Your Template - Critical Dimensions
You can use Fusion 360 or an equivalent 3D modeling application to design the part, but the drawing process will go easier if you first establish the critical dimensions of your template so you can use these dimensions when creating your 3D model.
To arrive at the dimensions for your template, you should understand how the template is used to cut the tails and pins for the dovetail joint. The tails are cut using a dovetail bit, and the fingers or "slot" end of the dovetail template guides the bushing while the router bit cuts the dovetail-shaped slot in your workpiece. The pins are cut with the wedge-shaped end of the template using a straight bit guided by the same bushing. The slot part of the template is sized to just fit the guide bushing, so the tail is cut to the larger diameter of the dovetail bit. This means that the pin needs to be cut so that the widest part of the pin (the part on the inside of the joint) is the same dimension as the widest part of the tail opening - in this case the cutting diameter of the dovetail bit. When making a cut, the bushing rides against the template, and since the bit is a smaller diameter than the bushing, the template must be narrower than the pin you intend to cut by the difference between the bushing and the router bit. When drawing the template by hand, you have to do a bit of trignometry to figure this out precisely, but with Fusion 360, you simply first draw the pin template to the width of the stock, and then use the "Press Pull" tool to shrink the template by 1/16" on each side of just the pin.
The attached videos in the next step take you through the process of creating the printable 3D model for your template using Fusion 360, but before your start modeling, you need to gather some information that determines the dimensions of your template. Your dimensions will be specific to the dovetail bit and guide bushing that you plan to use and the maximum thickness of stock that you plan to cut with your jig. My template is designed for use with an 8 degree dovetail bit with a large cutting diameter of 11/16". That means that the narrowest dovetail I can cut is 11/16" at the base of the cut. So I need the pin-cutting end of the template (the wedge-shaped part) to have an 8 degree taper and to be sized to cut a pin that's 11/16" wide at the base of the pin. Since the base of the pin is on the inside face of your stock, this dimension is measured on the outside face of your backing board, against which the stock rests when cutting the pins.
You also need to know how long the slot and the pin templates need to be, and this is determined by your maximum stock thickness and the diameter of the guide bushing. To make a complete cut, the guide bushing must be able to follow your template to both the inner and outer faces of your stock. If it is stopped short of the inside face of your stock, you'll be left with a little curve, and if the template stops too short on the outside face of your stock, you'll cut into your stock face and ruin it. So the template needs to extend past the outside face of the stock by at least half the diameter of the guide bushing plus 1/8". The extra 1/8" is required because that's the amount that you can move the whole template either in or out in order to adjust the fit of your dovetails. I add a 1/16" to this just to ensure that I have room for error. In the same way, the inner shoulders of the template need to be located the same amount inside the inner face of your stock (the outer face of the backer board). I sketched all of these considerations out using the Note app on my iPad before I started making my 3D model so that I could simply enter the resulting dimensions of the template in order to create my model. Here's a summary of my calculations and the resulting dimensions that you can use to derive your template dimensions.
Inputs (these may vary depending on the router bit for which you are making your template)
- Router bit diameter = 11/16"
- Bushing diameter = 5/8"
- Maximum stock thickness = 13/16"
Fixed dimensions for the jig
- Jig backbone thickness = 1"
- Backer board total thickness = 1 1/2" (2 x 3/4")
- Adjustability factor = 3/8" (1/8" in and out +1/16" extra allowance - this is the amount the template can be moved off center in order to adjust the fit of the joint)
Distance from center of the template to each shoulder
- (thickness of backbone /2) + backer board thickness - (adjustability factor + bushing diameter)/2
- 1/2" + 3/4" - 7/16" = 13/16", but I adjusted this to 3/4" to give the router bit 1/16" more travel towards the center of the jig just to be sure.
Length of tail slot and pin template
- adjustability factor + bushing diameter + stock thickness
- 3/8" + 5/8" + 13/16" = 1 13/16"
Overall length of each template
- 2x distance from center + 2x length of tail slot and pin template
- 2 x 3/4" + 2 x 1 13/16" = 5 1/8"
Width of each template
- width of the "finger" + bushing diameter + width of "finger" (I chose 1/2" for each finger to allow for enough strength of the finger but still allow fairly close spacing of the templates if needed).
- 1/2" + 5/8" + 1/2" = 1-5/8"
Step 2: Create Your Template in Fusion 360
If you're going to build a template for the same dovetail bit that I used, you can simply print the template included here, and adjust the fit in Fusion 360 by opening the .stl file and editing it as I describe later. But if you need to create a template for a different dovetail bit, you can follow the video to understand how I created the template and to replicate that process for your own template.
Here is the basic process I followed:
- Create a 2D sketch to be used for all three template shapes.
- Save three copies of the sketch to be used for the 3D shapes for each of the three templates (main, right end and left end)
- Extrude the 3D shapes from each of the sketches and add details to the 3D model (shrink the pin template to allow for the guide bushing, add the screw recess and t-track slot, and add some filets to make a nice pretty print).
- Generate the .stl for each 3D design and send it to Cura for slicing and then printing.
A couple of caveats about my use of Fusion 360 are in order. First, I am very much a novice in Fusion 360, so I'm sure there are better or easier ways of doing some of the things I did to get the end result. I have used Tinkercad pretty extensively to make 3D designs for things that I print, but this was really my first time using Fusion 360. Having noted that, here are the basic steps that I cover in the video:
Create a sketch (2D) of your template using the dimensions from the previous step in this Instructable.
I started by creating a two-dimensional sketch on the x-axis plane that serves as the foundation for creating the 3D designs for all three template types that I wanted for my jig: the main template and a pair of mirror image left and right-end templates for creating half pins on the ends of the dovetail joint.
- Draw a centered rectangle on the origin, drawn to the overall dimensions of your template. Centering it on the origin is important because it makes it easy to draw the other elements you need. Make sure you orient this drawing so that the template length is drawn along the x-axis and the width is drawn along the y-axis.
- Delete the two construction (dotted) lines that are created for this rectangle, as they will get in your way later and you have no need for them.
- Draw a second rectangle centered on the origin to indicate the shoulders of the template. Make the width (x-axis dimension) 2x your distance from the center to the shoulder and make it the same height (y-axis dimension) as the first rectangle). For a 1" backbone and a 5/8" guide bushing, this ended up being 2 x 3/4", or 1 1/2" for my jig.
- Change your line type to "construction" and draw a third rectangle that's centered on the origin to indicate the outer faces of the backer boards. The x-dimension for this is 2 1/2" and the y-dimension is the same as the first rectangle.
- Now, still using a construction line, draw a centered circle on the leftmost line of your template rectangle to indicate the size of the slot to guide the bushing for your dovetail cut. Place the center of the circle at the intersection of the x-axis and the leftmost line on the template rectangle, and make the diameter the size of your guide bushing + .005 inches to provide a little clearance. Fusion 360 is so easy to use in this respect, you can actually just type "5/8 + .005" in the dimension input box and it does the math! In my testing this results in a slt that fits the bushing with no play but still allows the bushing to move easily.
- Draw another centered circle on the right-hand backing board line to indicate the width of the pin template where the stock rests against the backing board (this is where the size of the pin should match the cutting diameter of your dovetail bit. The final template will still have to be made narrower here to compensate for the difference between the router bit diameter and the bushing diameter, but that's best done on the 3D model using Fusion 360's Press Pull tool.
- Draw two angled lines between the intersection of the circle and the backer board line and extend them a bit beyond the rightmost line on the template rectangle. Use the angle for your dovetail bit (mine is 8 degrees). Note that after starting your line and extending it to the length you want, you can just hit the "Tab" key on your keyboard and the angle input will be highlighted so you can just enter "8" there.
- Use the Extend tool to extend each of these lines from the circle-backing board intersection to the shoulder line.
- Draw two horizontal lines from each of the intersections between the bushing circle and the leftmost edge of the template, extending both to the leftmost shoulder line.
- Finally, draw a centered .18" diameter circle on the origin. This is the hole for the 8-32 screw that will hold your template on the t-track.
- If you want to make your sketch pretty, you can use the Trim tool to remove the 2 angled lines that extend beyond the right side of the template, but it's not necessary to do so.
- Complete the sketch before proceeding to the next section.
Make three copies of your sketch, then extrude each of the three different templates and add the remaining details
I created the sketch in a way that allows me to make the three different templates (main, right and left) from the same basic sketch. So I used the "File > Save As" command to save a main, left and right template design, and then opened all of them from the data panel to finish each of the designs. After you do that, the process for each template is roughly the same. You use the Extrude tool to create the basic template shape by selecting the appropriate regions from your sketch and extruding to 1/2" thick, alter the width of the pin template to reflect the difference between the router bit and the guide bushing, add 1/4" radius filets (rouded corners) to the inside corners ot your template, add a round recess on the top for your screw and slot to fit your t-track on the bottom, and finally add a .04" filet to the edges of your template to make a nice print. As you go through this process, I think you'll start to gain an appreciation for the benefit of using Fusion 360. Here are the steps in more detail (but again, it's best to follow along with the videos).
- Extrude the template shape to 1/2" thick by activating the Extrude tool and then selecting the regions for the part you're making, as follows:
- Main: select both forks, the center section, and the center of the pin template
- Left: select the upper fork, the center section, and the center and lower portion of the pin template
- Right: select the lower fork, then center section, and the center and upper section of the pin template.
- After selecting all of the sections, enter "1/2" in the extrusion distance box to create a 1/2" thick body from your selected shapes.
- As I mentioned earlier, you need to reduce the width of the pin template to reflect the difference between the guide bushing diameter and the straight bit that you will use to cut the pins. Do this by activating the Press Pull tool, selecting the angled faces (or single face for the left and right templates) on the side of the pin template, and then entering the difference between your guide bushing radius and router bit radius as a negative number This will press each face in by that amount.
- Add a 1/4" filet to the inside corners of your template by activating the Filet tool and selecting the line representing each of the inside corners. Not that Fusion 360 lets you select lines that are hidden by the model, so you don't even need to rotate the model to see each of the corners.
- Add a recess for the 8-32 screw. Enable the Sketch tool and select the top surface of your template to start a sketch on it, then draw a .4" or 13/32" diameter circle and complete the sketch. With the Press Pull tool, press the circle 1/8" into the template (again, you can simply enter "-1/8" in the box for the press distance).
- Add a slot to the bottom of the template for the t-track. To do this, select the bottom of the template and start a sketch on it. Then draw a centered rectangle whose length matches the template width, and that is .745" wide (this is what worked best for my 3/4" t-track from Powertec, which measures at .744" on my diigital calipers). If your track measures differently, alter your dimension accordingly and err on the side of smaller since you can correct too snug a fit with a little filing, but you don't want a loose fit. Complete the sketch and press the rectangle into the template by 3/16" to make the slot (enter "-3/16").
- The finishing touch is to add a .04" filet to all of the exposed edges of the template. Do this by activating the Filet tool and selecting the top face, the side faces, and the two bottom faces and then entering ".04" for the filet size. Fusion 360 adds the filet (rounded corner) along the edge of the face, including the perimeter of the screw recess.
You now have the 3D designs from which you can print your set of templates. At this point, you can either export your design as an .stl file and then import it into your preferred slicer, or you can go to the Utility menu in Fusion 360 and send it to your slicer directly.
Step 3: Print the T-Nuts and Templates
You're now ready for the 3D printing part of the project. I'm assuming that you know how to make 3D prints, and if not, you can find plenty of good tutorials elsewhere on Instructables or on YouTube. I printed my drop-in t-nuts and templates with PLA, and used a slightly higher-than normal bed temp along with an enclosure to help minimize warping on the bottom of my prints.
Print the t-nuts
Start by printing a set of t-nuts, so that you're able to attach your templates once you have them printed. There's nothing for you to draw here since the t-nuts I designed are pretty generic, but if your track differs from the Powertec track that I used, you can open the .stl files in Fusion 360 and adjust them as needed. Note that there are 2 different t-nut designs. The slide-in nuts are for attaching the template track to the short lengths of t-track on the jig body, and the longer drop-in nuts are for attaching the templates to the template track. I made these drop-in so that I could easily add or remove any of the main templates without having to slide either of the end templates off the track. This was probably design overkill, but I like how they work so I stuck with them. You'll note that each type of nut is printed in batches of 4. I tried printing more at a time but I tend to get bad warping when printing more than 4. After printing them, you'll need to clean the edges up with a small file and make sure they fit the t-track properly. The 8-32 nuts just press into place, but you could also add a drop of CA glue round the edges of the nut to help secure it.
Print your templates
Before slicing your template, make sure you keep the t-track slot facing down, so the best printed surface is on the top of the jig. In your print settings, you'll need to enable support for the slot, and as I noted above, I increased the bed temperature from a recommended 60 C to 64 C to minimize warping. The enclosure was a big help against warping, and I put mine together from a $7 car windshied sun shade and 2 feet of 4-foot wide 11 mill clear plastic, supported by a cardboard top and some wooden dowels. You can check out the picture for reference.
After you've printed your first template, remove the supports and run a file around the edges of the slot to clean up any excess plastic, then test the fit of the slot on your t-track. You should have a solid fit with no play and your template should slide on the t-track with slight resistance. If the fit is too tight, measure the slot and the t-track with your digital calipers and adjust the slot width in your drawing by using the Press Pull tool to increase the width of the slot as needed. Remember to adjust each side of the slot by half the total adjustment, so you keep the slot centered on the template. After adjusting your design for fit, re-export your design, re-slice it, and print another template. Then test and adjust again as needed until the fit off the printer is perfect. At this point you can proceed to print your remaining templates.
Attach the t-nuts to the templates
At this point you can attach the t-nuts to the templates using the 8-32 screws. I found that 1/2" truss head screws are just a little too long, while 3/8" screws are much too short. I could have made the screw recess deeper to make it work with 3/8" screws, but I instead opted to use 1/2" and just grind them down enough so the don't bottom out in the t-track when the templates are mounted and the screws are fully tightened. I used a small grinder to take about 1/32" off each screw.
NOTE: If you're printing templates from your own design, you might want to confirm that you have everything right before printing the whole batch. To do that, you'll want to skip to the next section after print your first two templates and making a couple of test cuts.
Attachments
Step 4: Build the Jig Body
You'll have plenty of time to build the jig while your templates are printing, and I recommend getting started on it while your first template is printing so that you can test things out after printing a few templates to confirm that your template design is correct (this is especially important if you've created your own 3D designs rather than using my 3D models).
The jig body is simple. The length of t-track is mounted along the top of the 1" thick by 3 1/2" wide backbone using short pieces of t-track. This allows you to change the position of the t-track to adjust the width of the dovetail pins to create a tighter or looser fitting joint. The lower backer boards are screwed to both faces of the backbone and they hold the upper backboard firmly against the bottom of the pin and tail templates. This makes it possible to easily replace the part of the backing board that is cut away when you rout your dovetails.
Cut your t-track to length
The length of your t-track depends on the width of stock on which you want to be able to cut dovetails. Assuming you always want your dovetail joints to have about a half pin on each end, your t-track should be 1 1/2" longer than the widest stock you plan to cut. Once you've figured this out cut your t-track to length. One thing you might want to think about in cutting your track is where the pre-drilled holes fall on your track. I wanted to use the pre-drilled holes to mount my track, so I cut mine so that they were equistant from the ends of the track. After cutting your track, remove any burrs with a small file or sandpaper.
If you follow my approach for mounting your track to the backbone, you'll also need to cut a couple of 1" lengths of t-track from your remaining track. If you're using a tablesaw to cut your track, use caution cutting short lengths of track because it's easy for them to catch the saw blade and become projectiles. I prefer to cut small lengths with a jig saw and a good metal-cutting blade.
Make a backbone and attach the t-track
I made my backbone from two 1/2" thick pieces of good quality plywood glued face-to-face, but you could also use a piece of hardwood. You'll want to make sure the the board is flat and the edges are straight and square to the faces of the board. Cut the backbone to the same length that you intend your t-track to be.
Since I mounted my track to the backbone with small 1" lengths of t-track, my next step was to cut two 3/4" wide x 3/8" deep dados in the top of the backbone. I positioned these so they are perfectly aligned beneath the outermost pre-drilled holes in my t-track. After cutting the dados, I drilled a single hole in the center of the 1" tracks and countersunk these using a 23/64" drill bit (you can also use a 3/8" bit but this will cut slightly into the edges of the track slot). I mounted the 1" t-tracks to the backbone with a couple of flat-head wood screws.
Make the backing boards and attach to the backbone
The backing boards are made from 3/4" particle board or MDF, and are mounted to either side of the jig backbone. When you cut your dovetail joints, the bit has to travel beyond the inner face of your stock to complete the cut, which means it will cut into whatever surface your stock is clamped to - that's why you need a backing board. And each time you cut a different dovetail layout, you'll end up cutting away different parts of the backing board, so it will need to be replaced pretty frequently. Rather than replacing the whole board, I used a 1 1/4" piece of backing board at the top of the jig, and a 2 1/4" board at the bottom. The bottom board is permanently mounted to the jig with a couple of 1 1/4" long flathead wood screws (make sure they are at least an inch in from the ends). The top is only friction-fit and prevented from sliding side-to-side by a couple of screw points extending about 1/16" from the face of the backbone.
Add end stops for aligning the pin and tail stock to the template
To make it really easy to get properly aligned joints, I added an end stop to the end of the jig against which the stock is aligned. When you make your cuts, you need to reference both the pin and the tail boards against the same end of the template, so the stops for both cuts are installed on the same end of the jig. When the pin side of the template is facing you, the end stop is positioned at the right end of the jig, and when you flip the jig around so the tail side of the template is facing you, the stop is at the left end of the jig.
The easiest way to position the stop is to use a combination square and measure from the end of the jig, and install your stops aligned to the mark. I used two 1" lengths of 1/4" steel pin for my end stops.
Step 5: Add a Jig Base (optional)
It's much easier to use the jig if you mount it in a base that includes a built-in clamping bar. That way you only have to mount your stock in the jig, clamp it, and cut the pins or tails. You can skip this entirely if you plan to use the jig upside down with a table-mounted router.
I made my base from a piece of 3/4" plywood and a pair of clamping bars made from 1 1/2" hardwood. The back bar should be about 2 1/2" tall and should be about 3" longer than your jig's backbone so it extends at least 1 1/2" on either end. The front bar should be the same length as the back, but only needs to be 1 1/2" tall. The plywood bottom should be about 4" longer than the clamping bars, so you have 2" free at either end for clamping to your bench. Make it 3 3/4" wide so that when the jig is mounted, it overhangs the plywood slightly.
Before attaching the rear clamping bar to the bottom board, you'll want to drill holes for the clamping bolts. Start by drilling the recess for the bolt head, using a bit that's the same diameter as the wrench you use to turn the bolt. Position this hole so the bolts clear either end of the jig by about 1/8", and so the top of the front clamping bar will be aligned with the top of the rear clamping bar. After drilling the recess hole for the bolt, drill the hole fro the bolt through the center of that, and then clamp the top bar to the rear bar and use the hole drilled in the rear bar as a guide to drill a mating hole in the front bar.
You can now attach the rear bar to the base board with some flathead wood screws. You'll also need to drill a hole in the rear clamp bar to accomodate the end stop so the jig body can rest flush against the clamping bar. The location will be obvious as soon as you try to put the jig in the base.
Finally install the bolts and use a hammer to drive the bolt head into the undersized hole in the rear clamping bar.
Step 6: Make a Test Joint and Adjust the Fit
Before you make your first dovetail joint for a project, you'll need to adjust the fit of your dovetails by making a test joint. For this you'll need a couple of pieces of stock - one on which you can cut a set of tails and another one to cut pins. The process is as follows: set the template position for the widest possible pin size, cut the tails (the width of those doesn't vary) using your dovetail-cutting bit, then switch to a straight cutting bit to cut the pins. Once both sides are cut, test the fit, adjust the position of the template backward (i.e., make the pins narrower), and cut and test again, repeating this until you have a good-fitting joint.
Set the template for a test joint
Clamp your jig base to your bench before setting up your template for a test cut. When setting the spacing of your templates, position them to allow access to the screws that hold the template t-track to the jig body so you can loosen them and move the t-track to adjust the size of the pins. See the photo for reference.
For the first pin cut, you will want to start cutting the pins too wide and then work up to the right fit so you don't have to keep cutting off the end of the pin board. So start with the template t-track positioned at the front of the jig.
Cut the tails
Attach the guide bushing to your router base before mounting your dovetail bit to your router (the dovetail bit has to be insert through the guide bushing because the cutting diameter is larger than the bushing). Clamp your tail test piece in the jig with one edge aligned against the end stop. Then place a piece of stock the same thickness as your test stock on top of the template, place the router on top of this stock, and adjust the cutting depth on your router so the bit hits the top of the test stock clamped in the jig. This will set your depth of cut to the stock thickness. Cut your dovetails by following the template slots with the guide bushing until you reach the shoulder of the template for each slot. Make sure you don't lift the router up while the bit is under the template, or you will ruin the template.
Cut the pins and adjust as needed for a good fit
After you've cut the tails, flip the jig end for end in the base so the pin templates are facing you. Then remove the dovetail bit and install the straight bit in your router. Set the depth of cut the same way you did for the tails, then proceed to cut the pins. They should be too big at this point. Use a combination square to move both ends of the track in by 1/32" and cut the pins again. repeat this process until the pins just slide into the dovetails without needing to pound them in. If you go for a tighter fit, you run the risk of starving the joints of glue wich will produce a weak results.
You should not have to perform this fitting process for each project unless you're careless with your jig and let the templates knock against things and possibly move the t-track.
Step 7: Make Some Boxes!
Making boxes with your through dovtail jig is pretty easy. After you've cut your pieces to length, arrange your pieces as you plan to assemble them and mark the outside of each piece as either "pins" or "tails". Mark the outside only as this will help you remember to keep the outside of the piece facing you as you cut each end.
Since the jig allows you to vary the template spacing, you'll need to set that up next. I start by placing the outside templates so I get a little more than a half pin on each end of the joint, and I use my combination square to ensure that these are set the same distance in from the edge of the board for symmetry. I then space the remaining dovetails evenly or sometime I arrange them into multiple groups of closely-spaced dovetails with a larger space between each group. The important thing to remember is to make your spacing equal fo a good-looking result.
After setting up your template, equip your router with the dovetail bit, set the depth of cut to equal the thickness of your stock (or maybe a paper's thickness more), and cut the tails first. After each cut remember to spin the board to cut the other end, keeping the outside face of the stock facing you. Do NOT flip the board end for end. You should be able to read your "tails" label on the face of the board.
Once you've cut all of the tails on all of your boards. flip the jig in the jig base so the pin templates are closest to you, and change your router bit over to the stright cutting bit. Once again, set the depth of cut to equal the thickness of your stock and cut the pins. When cutting pins, I usually take the first pass following the template from left to right, thereby removing the outer surface of the stock with a "climb" cut, which helps avoid tearout. I then complete each pin by following the template with progressively deeper cuts until I reach the shoulder of the template with the guide bushing.
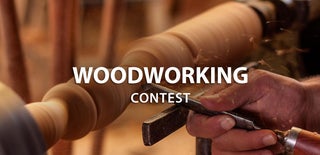
Participated in the
Woodworking Contest