Introduction: 3D Printing Concrete Molds
Welcome to this guide on how to use 3D printing to create concrete molds. In this guide, I’ll try to cover some simple techniques that might help you get started.
I recently started my own journey, learning how to do this, so if you have any ideas, feedback or questions, please leave them in the comments, so we can improve together!
In the guide, I’ll cover how one can utilize 3D printing to create molds, how to avoid typical pitfalls, some simple coloring techniques, and my experiences so far with surface treatment.
Supplies
- Hobby Concrete
- Color suited for concrete (Optional)
- Surface coating (Optional)
- 3D printer (and filament)
- Tape or rubberbands
- Box cutter and sand paper
- CAD software
Step 1: Creating the Molds
The reason 3D printing is so convenient for creating molds, is that it is quick to 3D model (assuming you have simple CAD skills), and is therefore also quick to print. On top of this, 3D printing gives a lot of geometrical freedom when creating molds, as the print is built layer upon layer.
I made all of my 3D models in SolidWorks and my printer is a Prusa MINI with a print nozzle of 0.4 mm. The prints are made in PETG as that is more water-resistant than PLA and therefore better for long-term use. ABS would however also work just fine.
When creating a mold you need to have four things in mind; how to get your object out of the mold, how to keep the mold together, split lines and draft angles.
I started off by creating a simple mold for a tealight candle holder in four parts: The bottom part and three identical sides (see CAD drawing) . As long as you have a round geometry you should be good with doing the mold in four parts. For joining the mold I decided to do a simple mortise and tenon-inspired joint in the shape of a triangle for joining both the bottom and the sides. The type of joint really doesn't matter all that much. The only tip I have for you here is to make the joints as large as possible, as this will be easier for the printer to make snug.
Split lines are the visible lines that show on your object where the mold itself joins together. It can be beneficial to think about where you want your split lines to be, as these can be hard to remove completely. Therefore hiding them in some places you know people won’t notice them is to be preferred.
When creating a mold it’s important that you can get your object out of the mold when it’s finished hardening. For this reason, you want a slight tilt on the angle of the mold, as shown below. If your sides of the mold are completely straight, you’ll find that it’s impossible to get it out of the mold without breaking the mold completely. As a rule of thumb, you should aim to have an angle of about 10-15 degrees to make sure it slips the mold when hardened as illustrated below. (see illustration Source: https://www.cewheelsinc.com/engineering-guideline...
When all of this is taken care of, the only thing left is for you to print your mold!
To try out making something bigger I also made a mold for a bowl. For this mold I used the exact same techniques as described above. The only difference is the shape, size, and color.
If you just need an easy way out to start trying you can use the molds I've worked on so far
Step 2: Preparing the Molds
Before adding the concrete, it’s necessary to clean up the molds. Grab a box cutter and remove any excess material that is decreasing the tightness of the joints. Then, I recommend sanding the centerpiece. The centerpiece needs to be pulled out like a plug, so make sure you make it easier for yourself, especially if you are thinking of reusing the mold.
Before putting the mold together, I would grab some lubricant (vaseline-based or even food oil will do) and coat the inside surfaces of the mold. This will greatly reduce the chance of the figure breaking when you remove the mold(See picture 2 where I forgot to sand and lube). I’ve also seen people cover the centerpiece with a balloon (see references), but I’ve yet to try that for myself.
With everything looking nice and lubed, it’s time to put the molds together. You can use tape, rubber bands, etc. It’s really not that important. The important part is that it is tight! The tighter the mold, the smaller the corrections are afterward.
If you made it this far, you are ready to mix some cement!
Step 3: Molding
For concrete, I recommend listening to smarter people than me (that’s what I did). I just went to the hardware store and asked what they deemed to be the best fitting type. I came home with a bucket of fine-grained hobby cement (0-0.1 mm stones) and so far that has worked just fine and it wasn’t that expensive either. If you are not in a position to get advice, I’d say that it generally seems like the fine is better when it comes to these smaller projects (seems logical). Concerning grey or white, I’d recommend white if you are looking to color the concrete. But if it’s not too expensive I think a bleeding mix of the two could look really cool as well. Mixing the concrete I recommend following the instructions on the box (bag or bucket). Generally, you rather go a little too thin to ensure it gets into all the corners of the mold.
For coloring, I’m using a liquid color concentrate that I got for a resin project long ago, but you don’t have to go with this specific solution. You can color concrete with many different types of paint, color powder, or concentrate. I’ve added a link in the reference list where you can see a clear overview of how to color concrete using different techniques.
For the color molding techniques, I’ve experimented with layering full colors and bleeding colors, and I’m especially happy about the bleeding effect. The layering was done by mixing two separate batches of concrete with two different colors and then adding one after the other. The bleeding was done by adding the color, giving it a few turns without mixing it fully, and then adding it to the mold.
With the concrete being ready to be poured into the mold, the last step is to remove air bubbles. You can use many different methods to do this. I put the mold on a piece of plywood and knocked the plywood with a hammer to shake out the bubbles. I’ve seen other people use homemade multi-tool-whisks or just knock directly on the side of the mold.
Step 4: Finishing Touches
When your molded object is hardened and you get it out of the mold (hopefully in one piece), it’s time to sand the surface with sanding paper. I use 220 grit sanding paper, but if you only have sandpaper that is more rough or more fine that will work fine as well. For this part you need to make sure that all of your surfaces are smooth and the split lines have been sanded down. When you are done sanding, make sure you remove all the excess cement dust with for example a damp cloth. Now you are ready to give your object a surface treatment. As far as I know there are two good ways of doing this. One is treating it with varnish, the same as you would for wood. The method I used was using a concrete sealer. This stuff can be bought in most hardware stores. Apply the concrete sealer in good amounts, and wipe off any excess when applied. Let it dry for a couple of hours and apply another layer. This will make sure the surface is more repellent.
Step 5: Future Work and References
Thank you for reading my guide! In the future, I'm going to be trying some more surface treatments, so if you have some good ideas on this subject, please leave them in the comments. Additionally, I hope you enjoyed this guide and that you feel optimistic about starting out with some concrete molding. I think it's really cool and I hope you have the same experience!
References:
Guide to the basics of making a mold:
https://concretecountertopinstitute.com/free-train...
Article on draft angles:
https://www.cewheelsinc.com/engineering-guideline...
Guide to coloring:
https://www.cewheelsinc.com/engineering-guideline...
Guides to 3D print molding:
https://www.cewheelsinc.com/engineering-guideline...
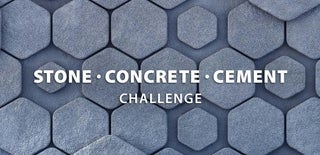
Participated in the
Stone, Concrete, Cement Challenge