Introduction: 3D Printing Puzzle Repair
If you own or have access to a 3D printer, then you'll no longer need to fear buying a used puzzle from a garage sale! Or, perhaps you already have a puzzle you'd like to save from from a fate of forever being incomplete.
Follow along with my simple instructions and there will never need to be another unfinished puzzle again!
Supplies
Any 3D printer
Paper + pencil/pen
Computer scanner
Vector software (Inkscape, Illustrator, Affinity Design)
Calipers
3D software (I used TinkerCAD)
Paint!
Step 1: Copying the Missing Pieces
I went pretty low tech with this technique and stuck with the tried and true pencil and paper to trace the outlines.
Tip: A mechanical pencil works best as the straight and thin graphite gets the closest and most accurate edge.
Just slide a standard size piece of paper under the missing piece gap. Using a standard sized paper allows you to double check your scale when it's pulled into software. I used the same piece of paper for all the different pieces and I just made sure not to overlap them. You can see that I messed up tracing a piece; I simply crossed it out, moved the paper over, and tried again.
Tip: Using a standard sized paper allows you to double check your scale when it's pulled into software
Pop that paper into a scanner and we'll pull that digital copy into our vector software for the next step!
There are other ways you could make this work without a scanner such as: taking a very accurate and level picture with a camera with some sort of measurement guide or scanning the cluster of puzzle pieces that surround the missing piece gap directly without the tracing step.
Step 2: Digitally Create Your Pieces!
After opening your scanned image into a vector software (Inkscape, Illustrator, Affinity Designer) you'll want to lock the layer of the image and then create a second top layer to trace your lines. I don't kill yourself with accuracy here, just eyeball it and follow the lines the best that you can. I tend to follow the outside of the line so you can see what you are doing and because you lose a little of the edge in the tracing process. My quick video should help explain my process the best. You could try to do an image trace/raster trace/bitmap trace but I find that makes the pieces a lot more lumpy. This process isn't flawless, but it always ends with the pieces fitting pretty well for me.
After tracing the individual pieces I bring them together into a much more uniform cluster. Turn the scanned image layer invisible, and export as an .SVG.
I use TinkerCAD because it is quick and easy, especially since it just needs to be extruded. There are many other CAD/ 3D printing softwares out there that can do the same.
No matter what I do, when I import my files into TinkerCAD they are never the right size. All of your pieces are now grouped together so if you highlight your full grouping in the vector software you should see the correct width and height. Manually correct these in TinkerCAD and you'll know your pieces will be the correct size.
Don't forget to measure the thickness of the puzzle for your new pieces! Calipers come in handy for this. Use that measurement to set the height of your extrusion. Now you can export your new 3D files as a .STL!
One last software, I promise....just load it up into your preferred 3D printing slicer.
I printed the pieces solid at 100% infill, PLA, normal .175 detail.
Step 3: 3d Print!
The satisfaction of a quick but useful print!
My technique is a little sloppy and can lead to some tiny gaps but it always fits well enough that it will only fit in the position and place it is supposed to.
Step 4: Paint!
Before you stress out about getting your new puzzle piece perfectly painted, know that professional restoration artists usually loosely block out any missing areas of paint so as to not detract from the original artists work. Enough to trick the eye and fill out the painting instead of trying to flawlessly replicate the original art. Even if your color is off or your pattern is a little sloppy, it'll still make the puzzle look more complete than a gaping hole. Strive for complete, not perfect!
I spend about 30-45min painting each piece. I enjoy the challenge of trying to match the colors and see how close I can get it. They look great at a distance and sometimes can completely disappear! Up close and under scrutiny its obvious which ones I've manufactured. So...don't give up if you don't feel artistic enough, it takes very little to fool the eye at a glance.
I use acrylic paint and that is a disadvantage as its a very flat paint compared to the glossy printed cardboard. Usually you can't tell unless the light hits it just right. I'm not sure if enamel paints or a clear coat would fix it. I don't bother because I'm not trying to completely trick anyone.
There will also be 3D printing texture, paint texture, and some color "glow" you won't be able to get with acrylic like you can with ink. So, while not flawless, I'm happy to be able to place the new pieces and call the puzzle complete.
Good luck salvaging your favorite puzzles from the misfortune of missing pieces!
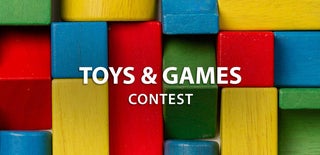
Participated in the
Toys and Games Contest