Introduction: A Flat Pack Rocking Cat!
Hello Instructables! It's been a while since I've done a how-to.
My good friend and college roommate just recently became a father, so I decided to make a gift for his child. I ultimately decided to make a rocking horse. To make it a bit more unique, I decided to make it a cat instead of a horse (since there were inside jokes among my friend and I involving cats). And, given that it had to ship cross country from Pennsylvania to Washington state, I chose to make a flat pack design so I could reduce the shipping costs. It also uses mostly standard hardware found in knock-down furniture designs.
I took inspiration from a few different rocking horse designs I had seen around the internet (definitely Scandinavian influenced). I took dimensions from a rocking horse plan in a woodworking book I have and this design from Canadian Home Workshop to develop the general size and shape of my rocking cat. I also received some input an industrial designer friend on the overall shaping of the cat body.
Feel free to take this design and modify it as much as you want. It could certainly be made with more traditional joinery, and doesn't have to be made entirely of plywood. Have fun!
Step 1: Materials and Tools
Here's a list of materials and tools needed to complete this project:
Materials:
- Half sheet (4'x4') of 1" thick furniture-grade plywood (it's more than you need but will provide some extra in case you mess up). I used birch plywood from ApplePly. Alternatively, you could use a full sheet of 1/2" thick plywood (4'x8'), cut it in half width-wise, then glue the two pieces together to create the necessary 1" thick piece.
- 1" diameter oak dowel (at least 16" long)
- 16 flat head cap screws, 1/4-20 thread, 2 1/4" length (McMaster-Carr part # 91263A567)
- 12 barrel nuts, 10mm OD, 16mm length, 1/4-20 internal thread (McMaster-Carr part # 90835A210)
- 4 hex drive steel threaded inserts for wood, 1/4-20 internal thread (McMaster-Carr part # 90192A124)
- 5 minute epoxy
- Spray adhesive (for attaching templates)
- Paint (bold primary colors such as yellow, red, and blue)
- Clear coat (I recommend a water-based polyurethane)
Tools: (the minimum required to make this)
- Jigsaw
- Handheld power sander (orbital, belt, or sheet sander) with coarse to fine grit paper
- Drill
- Self-centering doweling jig
- 10 mm drill bit
- 1/4", 5/16", and 3/8" drill bits
- Countersink bit
- Combination square
- Straightedge
- Center punch
- Mallet
Additionally recommended Tools: (this will make the whole job a lot easier)
- Band saw
- Drill press
- Table saw
- Router
- Belt/disc sander
- Oscillating spindle sander
- 1/8" and 1/4" roundover router bit
- 10mm forstner bit
- Transfer punch set
Step 2: Drawings, Patterns, and CAD
Attached are various pdf drawings, patterns, and CAD models. If there's a particular format you need, let me know and I'll see if I can get it to you. Some of the drawings can be printed to scale and used as patterns, I've indicated the paper size in the file name.
Step 3: Cutting the Runners
Print out a copy of the runner pattern. Cut and tape together using the aligning marks.
I cut my piece of plywood in half, creating two 2'x4' pieces, to make things a bit more manageable. Adhere the pattern to the wood using spray adhesive (I like using 3M Repositionable 75). Spray the pattern only, and make sure it dries completely before sticking it to the wood, otherwise you will be left with lots of paper stuck to the wood when you eventually remove the pattern.
If you're just using a jigsaw, go ahead and cut out the runner. Otherwise, trim the board down on the table saw for handling, then complete the rough cuts on the bandsaw.
If I were smart, I would have cut out a second strip of wood and screwed it to my piece with the pattern on it so would only have to do the cutting and shaping operations once, and the pieces would match up perfectly. Live and learn.
Step 4: Finishing the Runners
After making your rough cuts, it's time to do the fine shaping. Before you do that, however, go ahead and use a center punch to mark the holes while the pattern is still attached (It may come loose during sanding). Then, drill the through holes using a 1/4" bit (drill press recommended)
Using a sander, begin sanding the wood right up to the lines on the pattern. This process can take a little while, depending on how particular you are. Once completed, you can peel off the paper pattern.
After the fine shaping, it's time to round over the edges. You can do this with a sander, however, I used a trim router and a 1/8" roundover bit for a more uniform appearance.
Finally, I used a countersink bit on one side of each runner, on each hole, to allow the flathead screws to sit flush when the rocking cat is assembled.
Step 5: Cutting the Foot Runners
Start by cutting some plywood down to the proper size for the foot runners (11" x 2 1/2"). A jigsaw and a straightedge can accomplish this task, though it is much easier with a table saw.
After cutting to size, layout and center mark all of the holes.
Step 6: Drilling Holes in the Foot Runners
First, drill the two 1/4" through holes that are in the center of the runner, then countersink (make sure you countersink the proper side!)
Next, drill the 10mm holes for the barrel nuts. I made them flat-bottomed for appearance, but they can be through holes too. If drilling flat-bottomed holes, make sure you're drilling on the right side, and use a 10mm forstener bit. I neglected to take a picture during this step, FYI.
Finally, drill the cross holes on the ends of the foot runners. Initially, I had tried to do this on a drill press, but the holes ended up being out of alignment. The solution ended up being to buy a self-centering doweling jig. I bought a cheap one from Harbor Freight, which I ended up having to completely disassemble so I could calibrate it (it was not centering!).
Once i got it straightened out, I attached it and used a transfer punch to gently mark the wood. I then pulled out the punch and peered down the jig hole with a flashlight to see if the mark i just made matched the hole position i had marked earlier. If it didn't, I nudged the clamp a little in the desired direction and checked alignment again.
Once positioned properly, I set the desired depth on the drill bit. Finally, I inserted the drill bushing into the jig and drilled the hole.
Step 7: Test-fitting the Base
Now's the time to check if you drilled the hole straight and in the right locations. To do this, try to assemble the base together from the runners and the foot runners.
I had a several that were out of alignment. I ended up having to drill out some of the holes from 1/4" to 5/16", as well as drilling some of the 10mm holes a bit deeper and/or slotting them out a bit so things would line up.
Step 8: Cutting the Rocking Cat Body
Print out the pattern for the rocking cat. It's pretty large, so unless you have plotter you'll have to take it out somewhere to get printed. I went to my local print shop, and even though they don't have a large format printer, they were able to put together a 1:1 scale print for me from a few smaller printouts. The whole thing cost me a whopping $2.
Apply spray adhesive to the back of the pattern (make sure to let it dry!) then attach to plywood. Rough cut using a jigsaw or band saw, then do the final shaping with a sander. This is a bit time-consuming given the amount of details and smaller radii present here compared to other parts.
Step 9: Drilling More Holes
Use similar procedures used in the prior steps to drill the holes in the rocking cat body. Start with the flat bottomed 10mm holes (again, you can make these through holes if you want), followed by the corresponding 1/4" through holes for the screws (using the doweling jig). Finally, drill the 3/8" holes using the doweling jig.
Note that one of the pictures shows extra holes drilled for the seat mounting. Initially, I had made the design with three screws to attach the seat. However, their position made it tough to attach the doweling jig properly, and they ended up being way out of alignment. I changed the design to use just two screws in a position where the jig could attach securely.
Step 10: Finishing the Cat Body
After the holes are drilled, peel off the pattern, then round the edges by sanding or using a 1/8" roundover bit. After that, attach the body to the base to check hole positions and fit. I had to drill the 1/4" holes out to 5/16" like before and adjust some of the 10mm holes.
Step 11: Making the Seat
Print out and attach seat pattern to a roughly-size piece of plywood (note: my images show three holes on the pattern, which have since changed to two holes on the final design). Rough cut on the band saw then shape with a sander. Test fit the seat on the cat body. The two notches will probably require some fine tuning to fit properly (a chisel or file helps for this). You want the fit to be a tiny bit loose.
Step 12: Drilling Holes and Finishing the Seat
Since I changed the mounting design of the seat mid-construction, I had to come up with an easy way to mark the holes (this method also works if your holes are out of alignment). To do this, I installed the two threaded inserts, leaving the top of each protruding above the surface a little bit. I then put the seat in place and struck it firmly with a rubber mallet. The force of the mallet strike creates indentations in the wood which can be used to center mark the holes to be drilled.
Drill and countersink the holes, remove the pattern, and round the edges. I used a 1/4" roundover bit here to create a softer edge.
Step 13: Making the Handle/footrest
The handle and the footrest are identical pieces.
Cut two 8" pieces from your dowel rod. To cut the dado in the center, I took a piece of scrap wood with square edges and brad nailed it to the dowel. This gave me a means to hold the dowel still and square when cutting the dado. I used a band saw to cut it, but you could probably do it with a table saw and the right jigging or a chisel and hand saw.
Drill and countersink the hole in the center of the dowel. Use a sander to round the ends of the dowels.
Step 14: Permanently Installing Threaded Inserts
The four threaded inserts called out in the materials list are used for attaching the seat and foot rest. Thread each insert into the hole to the proper depth. For the seat, the top of the insert should be flush with the edge of the plywood. For the holes for the handle and footrest, the insert should be threaded in as far as it will go. The purpose of doing this is to cut the threads in the wood before the inserts are glued into place
Now, remove all the inserts. Lay a bead of epoxy in each hole, then re-install the inserts (remember, seat position - flush with surface, handle/footrest position - all the way to the bottom of the hole). It helps to use epoxy that has a mixing tip; it makes it easier to lay the epoxy bead in the hole.
Once the epoxy has cured (I waited 24 hours), use a 1/4-20 tap to clean the internal threads of the inserts, which likely got epoxy in them when they were inserted.
Step 15: Finish Sanding
The end is nigh! Time to do final sanding of all of the plywood pieces. I used a random orbit sander starting with 120 grit pads, then did a second pass with 220 git pads. Finally, I raised the grain, then did a final hand finishing using 220 grit paper.
Step 16: Painting and Clear Coating
I painted the foot runners, handles, and seat. They got a few light coats of primer, followed by a top coat of either red, blue, or yellow paint. I used spray paint for an even finish, but brushing paint on would work fine as well.
Finally, every piece (painted or not) got 4 coats of polyurethane. I used a water-based formula to make cleanup easier.
Step 17: Final Assembly
Here's a series of images from the instruction manual I sent to my friend so he could put his together. I attached a pdf of the manual as well if you're curious.
That's it! This was a fun project to work on, and will perhaps become a family heirloom.
I did the majority of the woodwork in the wood shop of my employer, the National Robotics Engineering Center.
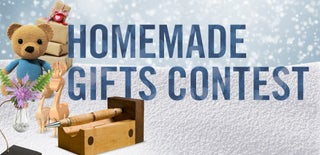
Participated in the
Homemade Gifts Contest
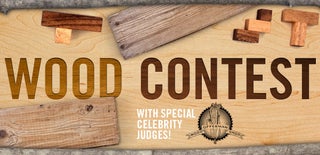
Participated in the
Wood Contest