Introduction: AMAZING! Brilliant Ideas & DIY
Watch the video
Angle grinder is a great tool for improvement. Its design is well suited for connecting various accessories that completely change the functionality of the angle grinder. Many of these nozzles can be made by hand. An example of this is a detachable reciprocating wood saw powered by a grinder.
Supplies
Materials:
- wood saw;
- bearing with an inner diameter of 22 mm;
- 2 enlarged washers M14;
- nut M14;
- bolt M8;
- steel pipe d 40 mm;
- 5 bolts M6;
- 11 nuts M6;
- sheet steel 2 mm.
Step 1:
Nozzle manufacturing
Unscrew the hacksaw handle.
In order for the saw to make translational movements, it is necessary to make an eccentric. To do this, a washer, bearing, washer and M14 nut are put on the grinder spindle. To shift the center of the structure, it is necessary to insert a piece of M8 bolt into the gap between the spindle and the bearing. It needs to be cut to match the height of the bearing. The resulting design is tightly clamped with a nut, due to which the eccentric will rotate without friction on the spindle thread.
Step 2:
To mount the saw, a similar design will be used as on the standard protective casing of the angle grinder. A piece of pipe is taken with a length equal to the distance between the beginning of the gearbox and the middle of the eccentric bearing. Then it is partially cut into 2 rings. The cut should be more than half. The notch line runs opposite the edge of the seat for attaching the casing.
Step 3:
It is welded to the edges of the cut along the M6 nut. With their help, the ring will be pulled together like a clamp when the bolt is tightened.
Step 4:
A hole is drilled in the hacksaw blade 1 mm larger than the outer diameter of the bearing. It is slightly flared at the top and bottom. Given the quality of the hacksaw steel, the work will take time.
Step 5:
From sheet steel, 2 identical rectangular plates of arbitrary size are cut. A 40 mm hole is drilled in their center.
Step 6:
One plate is welded with a clamp tube.
Step 7:
At the corners of both rectangles, a 6 mm hole is drilled. They should be opposite each other.
Step 8:
Holes are marked on the hacksaw blade, as on plates. They are drilled, after which they are bored with a file to enable the blade to move. You need to sharpen in both directions in a horizontal direction from the centers of the holes.
Step 9:
For aesthetics, you can paint with spray paint from a spray can.
Step 10:
To use the nozzle, you need to lubricate the contact surfaces of the web and pressure plates with grease.
Step 11:
Details are pulled together by bolts and nuts. You need to pull tight. Locknuts are placed on top so that the canvas does not unscrew and is not clamped.
Step 12:
An eccentric is assembled on the grinder, and the nozzle is placed instead of the protective cover. All reciprocating saw can be used. After use, the tooling can be removed and the angle grinder used as usual.
And let's get to work on cutting.
Step 13:
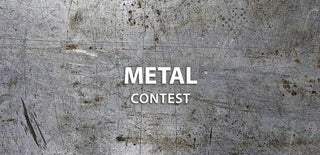
Participated in the
Metal Contest