Introduction: Absolut Welding Cart
This Instructable is going to show you how I took a beverage display cart and turned it into an EXTREMELY useful work table with a light duty adjustable height welding surface.
I was lucky enough to acquire a steel cart that was used to display Absolut Vodka in liquor stores. I was told it was made to carry half a pallet of vodka, so I figured it would be fine for my lighter duty welding and construction activities.
I think this is something you could do to other types of carts. I hope it will at the least give other people ideas for their projects.
Step 1: Tools and Materials
HARDWARE
- Casters - 4 of 3-inch total locking casters from Woodcraft, call 800-225-1153 or web site is http://www.woodcraft.com, part# 141051.
- 16 of 5/16 inch bolts for attaching new casters to cart - home improvement store
- 16 of 5/16 inch lock washers - home improvement store
- 16 of 5/16 inch nuts - home improvement store
- 3-inch long deck screws
- 2 pieces of 3/4 inch diameter all-thread at 3 feet long each
TOOLS
The tools I used on the project were as follows:
- Cordless drill
- Drill press
- Hacksaw or cutoff saw
- Screwdrivers and wrenches
- Bolt Cutters
- Grinder
- Various clamps
WOOD
- 2x4 lumber as needed for the size of your cart
MISCELLANEOUS
-
Corian or other solid surface material
- Top piece is 24 inches by 36 inches
- Bottom piece is 28 inches by 41.75 inches
Metal Welding Surface
- This is a piece of steel 24 inches wide, 36 inches long, and 3/8-inches thick. I think it weighs about 95 pounds.
NOTE: If you plan on using any tool for a project please make sure you are familiar with the tool and all of the dangers associated with it. If you are not familiar with a tool then you should ask someone who is to show you the proper way to use it. A lot of communities have classes at local colleges on the proper use of tools and machinery. There are also local woodworking clubs that offer classes at very reasonable rates for beginners. I highly recommend using these resources for your safety and for the most efficient use of the tool.
SAFETY FIRST
Always wear eye and hearing protection.
Always work safe with the proper safety equipment and guards on your tools.
Step 2: Cutting an Opening for the Argon Tank
The first thing I did was cut a hole in the heavy wire mesh that makes up the cart top. I made it just big enough for the 80 cubic foot argon tank for my tig welder. Once I cut out the wire mesh I used a grinder to remove the sharp edges on the pieces I cut.
It's not too difficult to lower the argon tank into the opening. I don't use up the tank that fast so I am only replacing the tank every 6 to 8 months.
Step 3: Top Support
The top of the welding table is composed of two different materials. Half of the top is a 3\8 inch thick steel plate and the other side is a 1/2 inch thick piece of solid surface material. A lot of people generally call this corian, but that is just a brand name of solid surface material.
I decided to make the steel welding plate height adjustable so I could work on projects at different heights and also level the welding surfave when needed. To do this I created a frame out of 2X4's that would help distribute the weight on the cart and allow for 3/4 inch diameter all-thread to pass through the frame at the four corners of the steel plate. The all-thread can be adjusted individually to level the welding surface or all four corners can be raised up to one foot for an elevated welding surface. I'm sure I will receive a lot of comments about this being a bad idea with having wood in the support frame. This is a light duty welding and work table for mostly light duty tig welding so I'm not too concerned about sparks on the wood frame material.
The cart I started with had a thin piece of steel sheeting that formed a 2 inch lip around the top of the table. I used two 2x4's stacked flat on each other that rest on the heavy wire rack on the top of the cart. I placed another layer of 2x4's on the underside of the wire racking.
Next I drilled the 3/4 inch holes through the 2x4's making sure to center the holes on the openings in the heavy wire racking. Make sure your all-thread is loose in all four holes before connecting the bottom layer of 2x4's under the wire racking to the top two layers. I connected the top two layer of 2x4's with the bottom layer (under the rack) with the 3-inch deck screws. This holds the wood frame firmly in place.
I added two 2X3 wood cross pieces to help with the lateral stability of the frame. It also helps support the solid surface material. I did this by cutting the cross pieces to length, laying them on the two outside 2X4's that run the length of the cart, and then marking the outline of the cross pieces with a pencil. Next I took the marked pieces and cut out the notch for the cross pieces on the bandsaw. One screw through the end of each cross piece into the stacked 2X4's holds them firmly in place.
Make sure you pre-drill the frame pieces for the 3-inch deck screws so you don't accidentally split one of the 2X4's.
Step 4: Leveling Screws
The four leveling screws are placed at each corner of the welding surface. I started with two pieces of 3/4-inch all-thread material and then cut them in half so I have an 18 inch long piece of all-thread at each corner of the 3/8-inch thick welding surface. I used an abrasive cut-off saw to cut the all-thread to length. If I was to do it again I would just buy four of the 2-foot long pieces and not go through the cutting. It would cost a few dollars more, but would save a lot of time cutting and cleaning up the cut ends.
I was careful to drill the holes for the all-thread between the wire mesh in the top of the cart.
So the steel plate could be lowered to lie flat on the frame I recessed the all-thread nuts into the 2x4's. This also keeps them from spinning as you adjust the all-threads up and down.
Step 5: Solid Surface Top
I used solid surface material for half of the top work surface. I've had people tell me I was crazy for doing that since it can be so expensive, All I can say is that I got it as no cost from someone, so the price was right and it cleans up easy. As an added bonus, the solid surface material is 1/2-inch thick and the metal welding surface is 3/8-inch thick. By adjusting the all-thread I can make them match up with each other.
The top is 24 inches by 36 inches, which is the same size as the steel welding surface. I set the solid surface material on the wood frame and then marked the limits of the area cut out of the wire mesh for the argon tank. Then I made a radius between the two edges of the cut to match the outer radius of the argon tank. I did this with a compass, but you could just as easily mark this using the tank itself.
I cut out the area for the tank using a bandsaw. Then I used a spindle sander to smooth out the cut edges.
I used silicone caulking as an adhesive to hold the solid surface material in place. I put the bead of silicone on top of the 2x4's and then carefully lowered it into position using the welding surface as a guide. I set some weight on the solid surface top and left it in place for 24 hours so the silicone could set up properly.
Step 6: Solid Surface Bottom Shelf
The bottom shelf covers the entire bottom of the cart. I cut the solid surface material to the correct length and width. It was 28 inches wide by 41.75 inches long.
I cut notches out of the corner of the solid surface material that were 4 inches long and 1-1/4 inches wide to allow for the corner posts of the cart and the brackets for the cross braces.
When I want to move the cart I can easily put the welder foot pedal, hoses, and ground clamp on the bottom shelf. The bottom shelf already has the welder and the safety cap for the argon tank.
Step 7: Replace the Casters
The cart originally came with four swivel casters of which two had a swivel lock. The hard plastic wheels on the casters slipped a little on my concrete garage floor so I decided to replace the casters with some fully locking swivel casters I already had for another project. The casters I put on the cart have polyurethane wheels that really stay put on the concrete floor when in the locked position. They are each rated for 300 pounds so I have plenty of capacity for the things I work on.
The hole pattern on the replacement casters was different than the hole pattern on the original casters so I did need to drill 3 new holes in the plates on the bottom of the cart.
When unlocked the cart rolls freely around with little effort. They almost roll too easily. I have these same casters on another work table/cart. I moved it once while rearranging the garage and forgot to lock any of the casters. I hate to admit it, but It started rolling right out my garage. With the ball bearings in the casters and the wheel material I didn't even hear the thing rolling. I caught it about 20 feet down my driveway.
Step 8: Put All of Your Welding Supplies in Place and Get to Work
Now that the cart is complete you can put your welding supplies in place and get to work on the next project.
I can't tell you how nice it has been to work with this new welding carter compared to the setup I was using before. I can roll it wherever I need it in the garage, lock the casters, lever the top with the all-thread adjustment (if needed), and start welding.
You may not be able to find one of these beverage display carts, but you might find something similar that will work just as well for you.
I'd like to find out if anyone else has made a work table or welding table this way or similar. Please let me know or post some pictures. Better yet, make an Instructable for it.
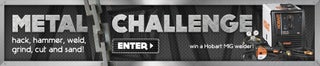
Participated in the
Metal Challenge
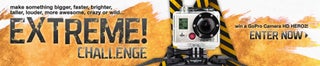
Participated in the
EXTREME! Challenge