Introduction: Apple G4 Cube Case Mod Rubik Style Hackintosh
The original G4 cube held a 450Mhz PowerPC processor and max 1.5gb RAM. Apple manufactured the G4 cube from 2000 to 2001 at a price around US$1600. It ran Mac OS 9.04 to OS X 10.4 (PowerPC, not Intel). It is approximately 7.5 x 7.5 x 10 inches, with all ports on the bottom, not the back. An original Rubik's cube was approximately 2.25 inches cubed, or roughly the size of one square on this case mod.
https://apple-history.com/g4cube
Lets get real with a Hackintosh build in a cube case and make it look like Rubik's Cube!
Over the last numerous years I have acquired 6 G4 cubes. I sold a house, moved everything to storage, bought a house, moved stuff out of storage, and am finally getting settled. So some of the projects are years old, not so fresh, but still case mods.
This will be a long post with lots of pics (over 50). Some sequences can be done in any order, some rely on others, they are presented here in what I believe to be a reasonable order. Some pics are from another build, just to show you multiple ways to do something. Not everything is complete yet, but soon...
Here are the tools I used for this build:
- Drill Drill bits Tap M3 and 6-32 (to make threaded holes for screws)
- Tin snips
- Wire stripper
- Soldering Iron
- Solder
- Shrink wrap or electrical tape
- Hacksaw (hand cuts)
- Jigsaw (power cuts)
- Vise (to hold things when sawing or soldering)
- Rotary tool with cutoff wheels (strange cuts)
- Pliers
- 3D printer
- Screwdrivers: Philips, Standard, and Torx
- Ruler or tape measure
- Caliper (for accuracy)
- Thermal paste (attach heatsinks)
- LEDs, wire, misc small electronic components (touch sensor, voltage regulator, molex connectors, resistors, and capacitors)
- Art cutting board
- X-acto knife
- Colored Vinyl sheets
- Spray paint
- Comb
- Misc screws, washers, metal offsets, rivets
- Double stick tape
- Hot glue gun
- Creativity
There are many phases to a build. Aesthetics, functionality, hardware, and software to name a few. I usually start my build by acquiring raw materials and computer components. Hardware: I then test on the bench with my assembled computer components to make sure they operate as anticipated (with Windows). Software: I then Hackintosh it, and make sure all kexts and components work as anticipated. Part of Functionality is deciding what components match the functionality of the original and whether to include them in the build or leave them out, as well as additional features not present in the original design. These include original parts like Optical drive, Wi-Fi, Bluetooth, speakers, touch power; and then adding additional features like IR remote and determining if there is physical space to add a discreet GPU or internal power supply. The final part of Aesthetics is how you want your cube to look: Original or modded.
This cube build components are:
- Apple G4 Cube case
- Gigabyte H97N-wifi motherboard
- Intel Xeon E3-1241 v3, 3.5GHz (4 core, 8 thread)
- 16Gb DDR3 1600MHz RAM
- GTX 750 TI 2Gb video card (need GPU because Xeon has no onboard graphics)
- Apple Slot Load DVD-RW
- Dell 1510 half-height Wi-Fi card
- MacBook Bluetooth card (3.3v)
- MacBook IR sensor (5v)
- Apple original white remote
- 128Gb Samsung SATA III 6.0Gb/s SSD
- Super low profile CPU cooler
- 320W Flex Power Supply
Some things I love about the G4 cube is that it is silent, fanless, and has a quick latch to release the innards. One thing I hate is the external power supply with a wonky 4-pin power plug. With higher power components, the noiseless/fanless feature is not an option. With smaller power supplies, everything can fit inside the cube without an external brick.
Step 1: Salvage
Disassemble on old G4 Cube. Not so tricky, but don't throw anything away yet, you may need it later, especially the screws. When you have completed the build, sell the G4 guts on eBay.
Physical limitation of the cube is approximately 6.75 inches in three directions. A mini-ITX motherboard is legally 6.7 x 6.7 inches. You have to leave a little room for play, and some of the connectors on the motherboard can spill over slightly. If you want to use the original touch sensor, you may need additional room. The original top grill also supports some of the weight of the cube, and unless you can mill it down or cut it off, it protrudes into the interior of the cube (more on this later).
Step 2: Heatsink Modification
To fit a power supply and video card inside, we have to remove as much wasted space as possible. The giant heatsink that makes up the locking mechanism can be trimmed down significantly. I have seen it done many ways, and I have done it a couple different ways as well (pics attached). I have a CNC engraver but not a mill, so I powered through it with hand tools. This is my preferred result.
- Strip everything down, including the external side rails. - On the back side raised portion that faced the CPU, make two cuts perpendicular to the fins about 1/4 to 1/2 inch from the edge, but don't cut below the raised area too far, just enough to see through. Use whatever tool you like, I prefer a hand powered hacksaw.
- While still on the back side, cut two slots closest to the locking mechanism in line with the heat sink fins. I prefer to use a power jigsaw, but the blade won't fit through unless you put a couple pilot holes first.
- Now the fun part... you have to cut through the fins along the back plate, deep enough to reach your first two cuts. Once you cut both sides, the center should just fall out.
- File down all the rough spots with a hand file and deburr any pokey stuff you could cut yourself on. Re-attach the side rails. - An easier way that does not retain the original spacing and rigidity is to just cut straight through along the locking mechanism so you end up with 3 parts, discard the center and then fasten the two remaining back together with another piece of metal.
- Later we will attach the power supply and a hard drive to this open area.
Step 3: Motherboard Mount
Since we just finished the heatsink mod, let’s look at where to mount the motherboard. The original was mounted directly to this heatsink, but a Mini-ITX motherboard holes do not line up with the G4 motherboard holes. Simply flip the heatsink over and make 4 new threaded holes that line up with a mini-ITX motherboard. The motherboard will essentially take the entire space of the locking mechanism, so do your best to center it.
I have used 2 inch offsets, but lately I have been using 1-7/8 inch instead. Gives me a little more room in the corners of the bottom cube plate.
Step 4: Bottom Faceplate
We mounted the motherboard, so now align the face plate and make some measurements to notch out the face plate to accept the mini-ITX I/O plate. I usually have to cut off the left-hand side of the I/O plate to get it to fit. You will also have to remove the two pins that hold the cube corner supports in place.
And fitting the video card is next, as well as the hole for the power plug from the power supply (yeah, it's ugly).
Step 5: Video Card
The stock GTX 750 TI was almost one inch too long. That was the heat sink and fans, the board itself was short enough. I removed the original fan cage and pushed the fans to the left and screwed them directly to the heat sink. For future reference, a single fan 1050, 1060 or 1080 mini will fit by cutting down the fan shroud. An R9 Nano fits without modification.
Remove the heat sink. I used a comb to keep the fins somewhat aligned while I cut them off with a rotary tool and cutting wheel.
Reassemble the GPU, and now it is short enough.
Step 6: GPU Riser
A video card simply will not fit in the motherboard slot as the locking mechanism is 2 inches away (I used 1-7/8 inch offsets to mount the motherboard). The only way to move the video card is to extend the PCIE slot with a riser. I have tried many risers in the past with no luck (right angle solid, ribbon cable, ribbon cable wrapped in aluminum). The ones that did work for me are the crypto coin mining type. A small dongle with USB3 connector and a separate board with full-length PCIE slot and another USB3 connector.
Here lies the problem: The USB port is almost always vertical, and will protrude out the side of the case. So I tried notching the locking mechanism to accommodate. I also had to notch the top internal cover as my riser card went to the edge.
Until I found a new riser that had a horizontal dongle! But alas, there is one more problem we have to deal with: The riser card extends to near our 6.7-inch limit, and the two connectors will get covered. I soldered a new vertical USB3 connector and optional power connector to alleviate the problem. Again failure, as the USB3 port with cable installed will protrude directly into the video card.
The final solution is to hard wire the riser card to the dongle by soldering in a piece of USB3 wire (9 wires).
Step 7: Power Supply
! ! ! E L E C T R I C A L - W A R N I N G ! ! !
- We are modifying a power supply, and putting the 115v mains inside the case. Make sure you do not have power applied when making any connections or soldering.
I did testing with a different power supply (and done online calculations, CPU TDP 70W), and idle produced only 33 Watts, while intense CPU or graphics were still under 250 Watts. That means the 320W power supply should be sufficient.
With the center fins removed, a FLEX power supply almost fits in there perfectly. A FLEX power supply is just a little too long to fit between the locking handle indent and the top grill, so we have to shorten it.
The FLEX is a little too long, so I remove the fan, and relocate the power plug to the cube bottom face-plate next to the video card.
The cube is small compared to other form factors, so we can shorten all wires on the power supply. Most of the cable length should be cut off and re-soldered to the power supply motherboard. Here are the wires cut off, De-soldered, and the empty holes.
Since I live in the USA and tend to only use 115v power, I don't need the option to go 220v. I removed the switch and connected the jumper directly to the power supply motherboard between A115V and B115V.
There is a little unused space in the power supply for the primary wires to exit the case. Since I won't be using the original cover, I can reclaim that wasted space. Here is the completed power supply next to the original, and the full length of the wires is 4-6 inches shorter.
Final step is mounting it to the locking mechanism where the heat sink used to be. Note that some wires are actually routed between the gap of the power supply and the former heat sink.
Step 8: Optical Drive
Why not? I know they are not in use much anymore, but I still need to burn the occasional media platter. And most drivers for new hardware come on a dvd. To maintain the original functionality and AWESOME toaster popup optical media, I have included a DVD-RW. I have a slot load slim drive, which is much thinner than the original optical drive, so I 3D printed (white) some adapter brackets to mound the drive. A few attempts and several adjustments later, and I had the perfect fit (red).
My SSD is large enough for my primary OS and applications, but user data and media storage needs a little more space. So I mounted my SSD outside the optical drive with a piece of the original drive cage that I cut off. I also mounted a 500Gb spinner to the opposite side of the power supply on the locking mechanism (heat sink).
Attached are my 3D STL files for your 3D printing, the file names end in 50, meaning 5.0 inches is the maximum dimension.
Step 9: Wi-Fi and Bluetooth
Originally, I had a modern Apple brand BCM94360CD 802.11ac Wi-Fi/BT 4.0 dongle on a mini-PCIE adapter, but the slot on the motherboard is vertical. The full-length card is 2 inches itself plus the socket on the motherboard which means it would hit the locking mechanism.
Not wanting to notch the locking mech again, I opted for the half-height 802.11a/g/n Wi-Fi only Dell 1510 card.
I then added a MacBook Pro Bluetooth card (2005, 12Mbps, limited range) with antenna. Since the Apple card needs 3.3v, I could tap into the power supply, or pull 5v down to 3.3 from an internal USB port. Since the IR Sensor needs the internal USB port as well, I decided to put these two components together on one internal dual port. I ordered a few L78L00 3.3v voltage regulators in TO-92 package to solder between the USB port and the Apple card to reduce 5v to 3.3v. After connecting, nothing showed up, so swapped the D- and D+ lines of the USB, then Bluetooth showed up fine.
Antenna placement could be an issue being that the entire cube case is metal making it a Faraday cage. There are minor exceptions: a plastic plug on both sides of the external case are for the original Wi-Fi antennas. Since the wifi card will have an external facing antenna port off the motherboard, I need to put the BT antenna near one of these plastic plugs.
I 3D printed a replacement plug to fit on the bracket and insert my BT antenna. Attached is my 3D STL file for your 3D printing, the file name end in 125, meaning 1.25 inches is the maximum dimension.
Attachments
Step 10: IR Sensor
A MacBook internal IR sensor (2007) runs on 5v, so directly connecting it to an internal USB port will power it fine as well as provide IR data to the computer from the remote control. The sensor should face the front, but the cube case design does not allow for such things unless you drill a hole in the front of the case. Instead, I opted to mount the sensor downward facing, near the front of the cube, and put a little piece of reflective material at a 45 degree angle to allow front IR signals to bounce up into it.
Both the IR sensor and the BT card are soldered onto a USB header and ready for installation. The 3.3v regulator and capacitor are inline.
And they both show up and work fine!
Step 11: Aesthetics
Yes, the original case design is cool. I like a little more flair to let guests know it has been modified. For this build, I had a case I had already painted flat black. I wanted more flair, so I decided on a Rubik style imitation. I started with 2 inch squares but it didn't look right, so I went down to 1-3/4 inch squares. Vinyl purchased at Michael's craft store as well as a corner rounder (doing the corners by hand was ugly).
To make it more visually pleasing, I added fake highlights and shadows with silver (couldn't find gray), brown and beige (darker than white). I also had to spend some time cutting each ventilation hole out of the rear grid. Not perfect, but looks good at a quick glance.
Step 12: Misc Items
There are some rare threads about using the orginal touch power button (capacitive/proximity) but I have not had success with that. I opted for a touch sensor that outputs a LOW TTL signal when activated (most output HIGH). I needed the LOW to sink the open circuit on the motherboard power switch. This is the model I chose: https://www.itead.cc/electronic-brick-touch-senso...
Attached is my 3D STL file for your 3D printing, the file names end in 20, meaning 2.0 inches is the maximum dimension.
Speakers:
Of the six cube cases I have, I have not a single set of Apple speakers. For this reason, I will forgoe any attempt to include an internal power speaker system. The motherboard will support audio out via the headphone jack, and the Video Card HDMI will support audio directly to an HDMI monitor.
Software:
That is another story for another time. Hackintosh build guides are plentiful out there.
Attachments
Step 13: Final Assembly
Once all components have been modified, final assembly begins.
- The last solder joint is connecting the main 115v leads from the power supply to the power connector on the face plate.
- Then add a couple of SATA cables for drives behind the power supply.
- Lower in the locking mechanism (heat sink).
- Attach the power supply main board to the back plate
- Install the riser on the video card
- Install the optical drive holder
- Connect appropriate power and data cables
- Install the top plate and connect the touch sensor
Here are 6 photos of the sides of the completed cube.
Photos of a look inside the top with the grill open and closed.
The optical drive working!
Step 14: Benchmarks
Here are a couple of camera shots of the screen (forgive the moire). macOS High Sierra 10.13.6 and Geekbench 4.2.3 CPU score of 4491 sincle-core and 14913 muli-core. OpenCL computation with CPU and GPU is 45990.
Cinebench R15 results as well.
Unigine Heaven Benchmark 4.0 average 51.6 FPS at 1080p over HDMI, so not extreme, but suitable for light gaming.
I have an ISeek thermal camera, so I ran a session of HandBrake to convert a movie. See the Intel Power Gadget and the heat generated. TDP on the CPU is 70-80W, hitting around 135F outside the case. I will re-run the tests when the cube is fully assembled.
Step 15: The Future
I have five left to build... How about a cube with 18 cores / 36 threads and a R9 Nano?
I appreciate your feedback, comments, and suggestions.
Happy Modding!
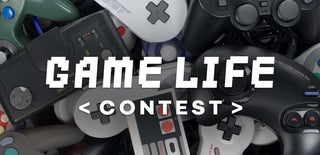
Participated in the
Game Life Contest